- お役立ち記事
- The difference between Make-to-order Production and Assembly Production
The difference between Make-to-order Production and Assembly Production
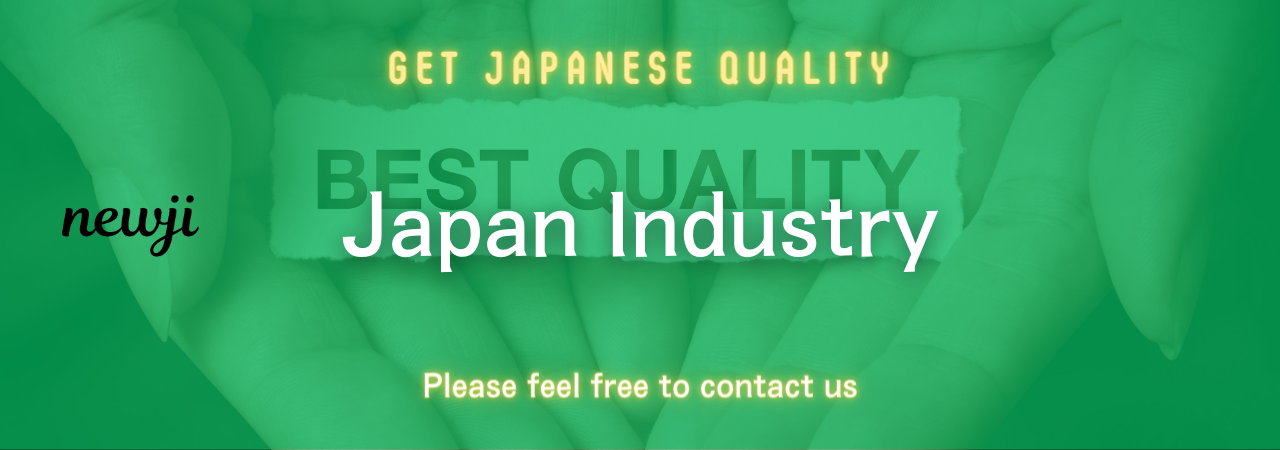
In the world of manufacturing, understanding different production methods can help businesses achieve greater efficiency and meet customer needs more effectively.
Two commonly used methods are make-to-order production and assembly production.
While they might sound similar, they actually have distinct processes and advantages.
In this article, we’ll explore these differences to help you understand which method might be best suited for your business.
目次
What is Make-to-Order Production?
Make-to-order (MTO) production, also known as built-to-order, is a manufacturing process where products are made once a customer places an order.
This means the production doesn’t start until there is a confirmed demand.
MTO is particularly useful for companies that produce highly customized products.
It’s often used in industries like aerospace, construction, and custom electronics.
Advantages of Make-to-Order Production
One of the main advantages of MTO production is the ability to offer customized products.
Since each item is made per customer specifications, businesses can cater to specialized needs and preferences.
This can result in higher customer satisfaction and loyalty.
MTO also reduces the risk of overproduction.
Since manufacturing only begins after an order is received, there’s little to no excess inventory.
This can save the company storage costs and minimize waste.
Another benefit is better resource allocation.
With MTO, manufacturers can plan their resources based on specific orders, optimizing the use of materials and labor.
This can lead to cost savings and more efficient operation.
Challenges of Make-to-Order Production
Despite its advantages, MTO production does have some challenges.
One of the biggest issues is lead time.
Since production starts after an order is received, it can take longer for the customer to receive the product.
This might not be suitable for customers who need immediate delivery.
Additionally, MTO requires a robust process for handling and managing orders.
Companies need efficient communication channels between sales teams and production units to ensure that special requirements are clearly understood and met.
What is Assembly Production?
Assembly production, also known as make-to-stock (MTS) or build-to-stock, is a manufacturing method where products are produced and assembled in anticipation of future demand.
Unlike MTO, production starts before any customer order is received.
This method is typically used for standardized products that have a consistent market demand.
Industries like consumer electronics, automotive, and household appliances often use assembly production.
Advantages of Assembly Production
One of the key benefits of assembly production is shorter lead times for delivery.
Since products are pre-made and stored in inventory, customers can receive their orders almost immediately.
This can be crucial for meeting customer expectations in competitive markets.
Another advantage is economies of scale.
By producing large quantities of standardized products, companies can lower their per-unit production costs.
Bulk purchasing of raw materials also tends to be cheaper, further reducing overall costs.
Assembly production can also provide a buffer against fluctuations in demand.
With inventory on hand, companies can quickly respond to increases in customer orders without ramping up production schedules.
Challenges of Assembly Production
However, assembly production comes with its own set of challenges.
One of the main drawbacks is the risk of overproduction.
If the anticipated demand does not materialize, companies can end up with large amounts of unsold inventory.
This can lead to increased storage costs and potential waste if products become obsolete or perishable.
Another challenge is reduced flexibility.
Since products are standardized and produced in bulk, there is less room for customization.
This can limit a company’s ability to meet specific customer needs, potentially affecting customer satisfaction.
Which Production Method is Right for Your Business?
Deciding between make-to-order and assembly production depends on several factors, including the nature of your products, market demand, and customer expectations.
Consider Your Product Type
If your business specializes in highly customized, complex products, make-to-order might be the better choice.
This allows you to cater to specific customer requirements, adding value to your offerings.
On the other hand, if your products are standardized and have a consistent demand, assembly production can help you achieve economies of scale and quicker delivery times.
Assess Market Demand
Understanding your market demand is crucial in choosing the right production method.
If your industry experiences seasonal fluctuations or unpredictable demand, assembly production can provide the flexibility needed to meet sudden increases.
Conversely, if your market is more stable and customers are willing to wait for customized products, make-to-order production could be a good fit.
Evaluate Customer Expectations
Customer expectations also play a significant role in your decision.
If your customers prioritize quick delivery, assembly production might be necessary to meet their needs.
However, if they value unique, tailored products, make-to-order production will allow you to exceed their expectations.
Conclusion
Understanding the differences between make-to-order production and assembly production is crucial for any manufacturing business.
While make-to-order offers customization and reduces inventory risks, it can result in longer lead times.
Assembly production, on the other hand, provides faster delivery and cost savings but at the risk of overproduction and less flexibility.
Carefully consider your product type, market demand, and customer expectations before choosing the production method that best aligns with your business goals.
By doing so, you can optimize your manufacturing processes, reduce costs, and ultimately, enhance customer satisfaction.
資料ダウンロード
QCD調達購買管理クラウド「newji」は、調達購買部門で必要なQCD管理全てを備えた、現場特化型兼クラウド型の今世紀最高の購買管理システムとなります。
ユーザー登録
調達購買業務の効率化だけでなく、システムを導入することで、コスト削減や製品・資材のステータス可視化のほか、属人化していた購買情報の共有化による内部不正防止や統制にも役立ちます。
NEWJI DX
製造業に特化したデジタルトランスフォーメーション(DX)の実現を目指す請負開発型のコンサルティングサービスです。AI、iPaaS、および先端の技術を駆使して、製造プロセスの効率化、業務効率化、チームワーク強化、コスト削減、品質向上を実現します。このサービスは、製造業の課題を深く理解し、それに対する最適なデジタルソリューションを提供することで、企業が持続的な成長とイノベーションを達成できるようサポートします。
オンライン講座
製造業、主に購買・調達部門にお勤めの方々に向けた情報を配信しております。
新任の方やベテランの方、管理職を対象とした幅広いコンテンツをご用意しております。
お問い合わせ
コストダウンが利益に直結する術だと理解していても、なかなか前に進めることができない状況。そんな時は、newjiのコストダウン自動化機能で大きく利益貢献しよう!
(Β版非公開)