- お役立ち記事
- Manufacturing Process of Clutch Pedals and Durability Reinforcement
Manufacturing Process of Clutch Pedals and Durability Reinforcement
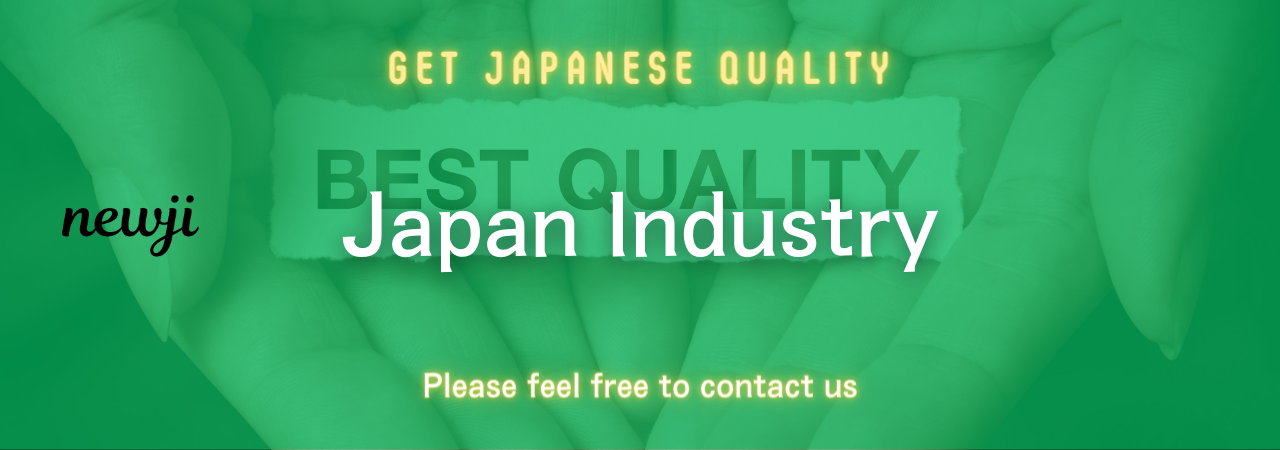
The manufacturing process of clutch pedals is a complex yet fascinating journey that combines precision, engineering, and innovation.
In this article, we’ll explore the steps involved in making clutch pedals and how they are reinforced for durability.
目次
Materials Selection
The first step in manufacturing clutch pedals is choosing the right materials.
Typically, clutch pedals are made from high-strength steel or aluminum alloys because of their durability and resistance to wear and tear.
Steel is favored for its tensile strength, while aluminum is selected for its lightweight properties.
Design and Prototyping
Once the materials are chosen, the next stage is design and prototyping.
Engineers use computer-aided design (CAD) software to create a detailed blueprint of the clutch pedal.
This design includes dimensions, shapes, and any specific features required.
After the design is finalized, a prototype is created.
Prototyping allows for testing and modifications before full-scale production begins.
Simulation and Testing
The prototype goes through various simulations and testing processes.
Engineers use stress analysis tools to ensure the design can withstand the forces it will encounter during operation.
This phase is crucial for identifying any potential weaknesses in the design.
Manufacturing Process
After successful testing and prototyping, the manufacturing phase begins.
This involves multiple steps, each critical to the finished product’s quality.
Cutting and Shaping
The first step is cutting the raw materials.
Advanced cutting machines, such as laser cutters, are used to achieve precise shapes.
These cut pieces are then shaped as per the design specifications using forging or stamping machines.
Forging involves heating the metal and then shaping it using high pressure, while stamping uses a die to cut and shape the metal.
Machining
Next, the shaped pieces undergo machining.
This involves removing any excess material and refining the pedal’s shape.
Machining ensures that each part is within the required dimensional tolerances.
Computer numerical control (CNC) machines are often used for this task to guarantee high precision.
Welding and Assembly
Once the individual parts are machined, they are assembled.
This assembly often involves welding different components together.
Welding must be done carefully to ensure strong joints that can withstand operational stresses.
Surface Treatment
After assembly, the clutch pedals undergo surface treatment processes to enhance their durability and appearance.
Some common treatments include:
Heat Treatment
Heat treatment is used to improve the metal’s strength and hardness.
The pedals are heated to a specific temperature and then cooled rapidly.
This process changes the metal’s microstructure, making it stronger.
Coating
To prevent corrosion and improve appearance, the pedals are often coated.
This can include painting, powder coating, or electroplating.
Coatings also add an extra layer of protection against wear.
Quality Control
Quality control is an essential step in the manufacturing process.
Each clutch pedal undergoes rigorous inspection to ensure it meets the required standards.
This can include dimensional checks, strength tests, and visual inspections.
Any pedal that does not meet the criteria is either reworked or scrapped.
Functional Testing
Functional testing involves simulating real-world operating conditions to ensure the clutch pedal performs as expected.
This can include load testing and endurance testing.
Pedals are subjected to forces they will encounter during actual use to ensure they can handle the stress without failure.
Durability Reinforcement
Reinforcing clutch pedals for durability involves several techniques aimed at increasing their lifespan and performance.
Material Enhancements
Selecting materials with high wear resistance is the first step in reinforcement.
Engineers may also use composite materials that combine different metals to enhance the pedal’s strength and durability.
Design Improvements
Additional reinforcement can be achieved through design improvements.
This includes adding support ribs or gussets to areas prone to stress.
Optimizing the pedal’s geometry distributes the forces more evenly, reducing the likelihood of failure.
Surface Coatings
Applying advanced surface coatings can significantly improve durability.
Coatings such as diamond-like carbon (DLC) or ceramic coatings provide excellent wear resistance.
They also reduce friction, leading to smoother operation and less wear over time.
Testing and Feedback
Continuous testing and feedback are crucial for durability reinforcement.
By analyzing failure points and gathering data from real-world use, engineers can make ongoing improvements to the design and materials.
This iterative process helps create clutch pedals that last longer and perform better.
Conclusion
The manufacturing process of clutch pedals and their durability reinforcement is a comprehensive journey that involves selecting the right materials, detailed design, precise machining, and rigorous testing.
By following these steps and continually improving through feedback and testing, manufacturers can produce clutch pedals that meet the high demands of modern vehicles.
Understanding this process highlights the intricate work involved in creating a component that often goes unnoticed but is crucial for vehicle performance and safety.
資料ダウンロード
QCD調達購買管理クラウド「newji」は、調達購買部門で必要なQCD管理全てを備えた、現場特化型兼クラウド型の今世紀最高の購買管理システムとなります。
ユーザー登録
調達購買業務の効率化だけでなく、システムを導入することで、コスト削減や製品・資材のステータス可視化のほか、属人化していた購買情報の共有化による内部不正防止や統制にも役立ちます。
NEWJI DX
製造業に特化したデジタルトランスフォーメーション(DX)の実現を目指す請負開発型のコンサルティングサービスです。AI、iPaaS、および先端の技術を駆使して、製造プロセスの効率化、業務効率化、チームワーク強化、コスト削減、品質向上を実現します。このサービスは、製造業の課題を深く理解し、それに対する最適なデジタルソリューションを提供することで、企業が持続的な成長とイノベーションを達成できるようサポートします。
オンライン講座
製造業、主に購買・調達部門にお勤めの方々に向けた情報を配信しております。
新任の方やベテランの方、管理職を対象とした幅広いコンテンツをご用意しております。
お問い合わせ
コストダウンが利益に直結する術だと理解していても、なかなか前に進めることができない状況。そんな時は、newjiのコストダウン自動化機能で大きく利益貢献しよう!
(Β版非公開)