- お役立ち記事
- Manufacturing Process of Submersible Pumps and Durability Improvement
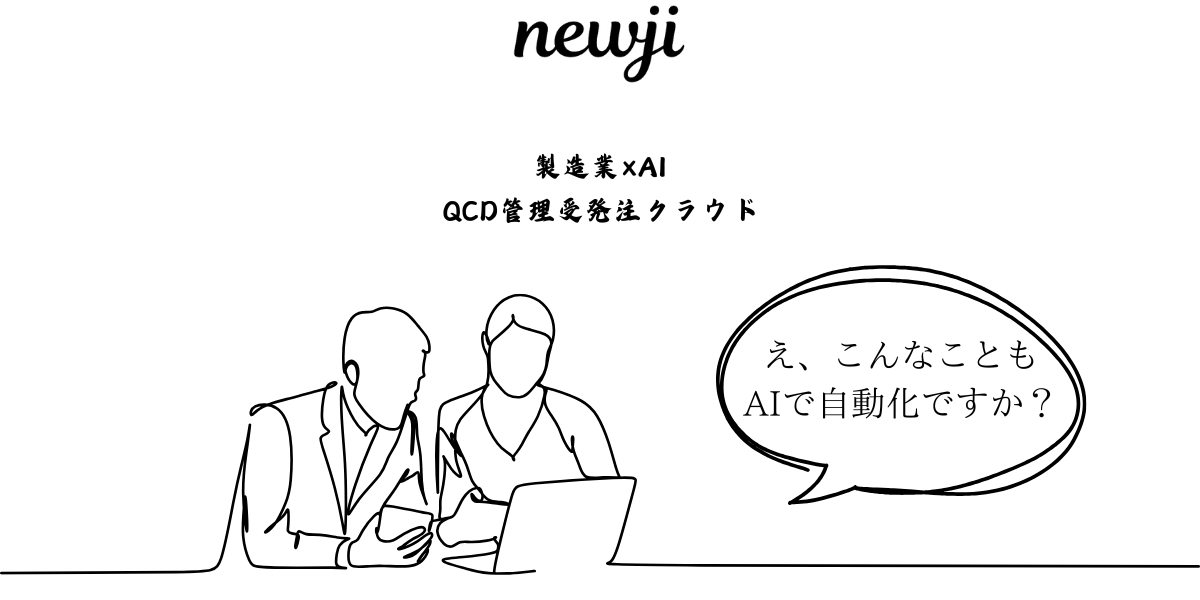
Manufacturing Process of Submersible Pumps and Durability Improvement
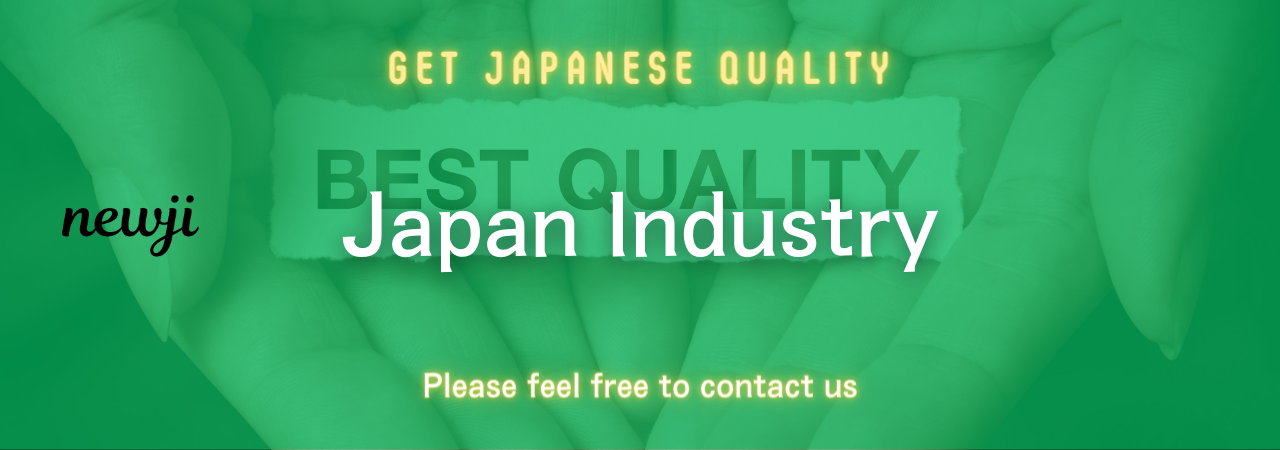
目次
Introduction to Submersible Pumps
Submersible pumps are key pieces of equipment used in various industries, including agriculture, mining, and waste management.
They are designed to operate underwater, making them ideal for draining water from basements, pools, and wells.
Understanding the manufacturing process and how to improve the durability of these pumps ensures they remain efficient and reliable for longer periods.
The Manufacturing Process
Design and Prototyping
The initial step in manufacturing submersible pumps is the design and prototyping phase.
Engineers use advanced software to create detailed models of the pump.
This phase includes deciding the specifications, such as the size, material, and power capacity of the pump.
Prototyping allows for the testing of these models in a controlled environment to ensure they meet required standards.
Selecting the Right Materials
Material selection is crucial for the durability and efficiency of the submersible pump.
Common materials include stainless steel, cast iron, and various polymers, chosen for their resistance to corrosion and wear.
Selecting high-quality materials ensures the pump can withstand harsh underwater environments, including high pressure and temperature fluctuations.
Manufacturing Parts
Once the design is approved, the next step is manufacturing the pump components.
This includes the impeller, motor, casing, and seals.
Each part is fabricated using specialized machinery.
For instance, impellers are often created through molding or casting, followed by precision machining to achieve the desired shape and size.
Assembly Process
The assembly of the submersible pump is a critical stage.
Technicians carefully assemble the components, ensuring all parts fit perfectly.
The motor is fitted into the casing, and the impeller is attached to the motor shaft.
Seals are then applied to prevent water from entering the motor housing.
Quality control checks are performed at each step to ensure the pump meets all specifications.
Testing and Quality Assurance
After assembly, the pump undergoes rigorous testing to ensure it operates efficiently.
Tests include checking for leaks, measuring the output flow rate, and verifying the electrical safety features.
Any defects found during testing are addressed immediately.
The pump is only allowed to proceed once it has passed all quality checks.
Packaging and Distribution
Once testing is complete, the pump is prepared for shipment.
This involves packaging it securely to prevent damage during transport.
Each pump is accompanied by a user manual and warranty information.
The pumps are then distributed to retailers or directly to customers.
Improving Durability
Regular Maintenance
Routine maintenance is essential to improving the durability of submersible pumps.
Regularly checking and replacing worn-out components can prevent larger issues.
Cleaning the pump to remove debris and buildup ensures smooth operation.
Scheduled maintenance can significantly extend the lifespan of the pump.
Using Quality Seals
The seals in a submersible pump are vital for preventing water ingress.
Using high-quality seals made from durable materials can prevent leaks and motor damage.
Regularly inspecting and replacing these seals as needed can improve the pump’s lifespan.
Optimizing Operating Conditions
Operating the pump within its specified conditions can prevent unnecessary wear and tear.
This includes adhering to the recommended flow rate, pressure, and temperature limits.
Avoiding extreme operating conditions can reduce the risk of damage to the pump components.
Upgrading Motor Technology
Using advanced motor technologies can enhance the performance and durability of submersible pumps.
Brushless motors, for instance, offer higher efficiency and longer lifespan compared to traditional brushed motors.
Upgrading to more efficient motor technology ensures the pump remains reliable over time.
Improving Corrosion Resistance
Submersible pumps are often exposed to corrosive environments.
Improving the corrosion resistance of the pump components can significantly enhance durability.
This can be achieved by using corrosion-resistant materials and applying protective coatings.
Regularly inspecting the pump for signs of corrosion and addressing them promptly can prevent significant damage.
Monitoring and Diagnostics
Implementing monitoring and diagnostic tools can help detect issues before they become severe.
Advanced sensors and software can provide real-time data on the pump’s performance.
This allows for timely maintenance and repairs, ensuring the pump remains in optimal condition.
Conclusion
Understanding the manufacturing process of submersible pumps and taking steps to improve their durability is crucial for ensuring their long-term efficiency and reliability.
From the design and material selection to regular maintenance and technological upgrades, each step plays a significant role in extending the life of these essential devices.
By focusing on quality and adhering to best practices, manufacturers and users can maximize the performance and lifespan of submersible pumps.
資料ダウンロード
QCD調達購買管理クラウド「newji」は、調達購買部門で必要なQCD管理全てを備えた、現場特化型兼クラウド型の今世紀最高の購買管理システムとなります。
ユーザー登録
調達購買業務の効率化だけでなく、システムを導入することで、コスト削減や製品・資材のステータス可視化のほか、属人化していた購買情報の共有化による内部不正防止や統制にも役立ちます。
NEWJI DX
製造業に特化したデジタルトランスフォーメーション(DX)の実現を目指す請負開発型のコンサルティングサービスです。AI、iPaaS、および先端の技術を駆使して、製造プロセスの効率化、業務効率化、チームワーク強化、コスト削減、品質向上を実現します。このサービスは、製造業の課題を深く理解し、それに対する最適なデジタルソリューションを提供することで、企業が持続的な成長とイノベーションを達成できるようサポートします。
オンライン講座
製造業、主に購買・調達部門にお勤めの方々に向けた情報を配信しております。
新任の方やベテランの方、管理職を対象とした幅広いコンテンツをご用意しております。
お問い合わせ
コストダウンが利益に直結する術だと理解していても、なかなか前に進めることができない状況。そんな時は、newjiのコストダウン自動化機能で大きく利益貢献しよう!
(Β版非公開)