- お役立ち記事
- A Detailed Explanation of Industrial Sensor Assembly and Inspection Processes
A Detailed Explanation of Industrial Sensor Assembly and Inspection Processes
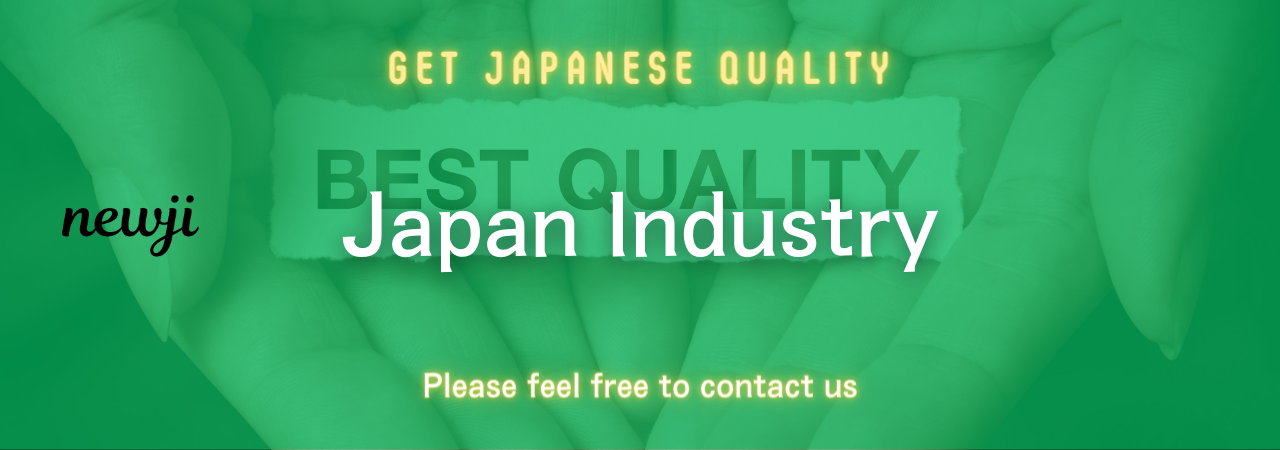
目次
Understanding Industrial Sensor Assembly
Industrial sensors play a crucial role in modern manufacturing and industrial processes.
They help monitor and control various parameters like temperature, pressure, and motion, ensuring smooth operations.
The assembly process of industrial sensors is detailed and meticulous.
Let’s take a closer look at how these sensors are put together.
Component Selection and Preparation
The first step in the assembly process is selecting the components.
These components include the sensor element, circuitry, and casing.
Each part must meet specific quality standards to ensure the sensor performs accurately.
Once the components are selected, they undergo a preparation phase.
This includes cleaning and inspecting each part to remove any contaminants or defects.
Proper preparation ensures the components fit together seamlessly during assembly.
Assembling the Sensor
The actual assembly process involves several steps.
First, the sensor element is mounted onto a substrate or circuit board.
Precision is key at this stage, as any misalignment can affect the sensor’s accuracy.
Next, the circuitry is attached.
This often involves soldering tiny electronic parts onto the circuit board.
Advanced techniques like Surface Mount Technology (SMT) are used to place components with high accuracy and efficiency.
The assembled sensor element and circuitry are then encased in a protective housing.
This casing shields the sensor from environmental factors that could degrade its performance over time.
Materials like stainless steel, plastic, or ceramic are commonly used, depending on the sensor’s application.
Finally, connectors are added to facilitate integration with other systems.
These connectors enable the sensor to communicate with control units, providing vital data for monitoring and control.
Quality Control During Assembly
Quality control is paramount throughout the assembly process.
Various tests are conducted at different stages to ensure the sensor meets the required standards.
For instance, visual inspections check for physical defects, while electrical tests verify the functionality of the circuitry.
Software-based inspections are also employed.
They simulate real-world conditions to ensure the sensor operates correctly under various scenarios.
By rigorously testing each sensor, manufacturers ensure reliability and performance.
Inspection Processes for Industrial Sensors
After assembly, each sensor undergoes a thorough inspection process.
This phase is crucial for identifying and correcting any defects before the sensor is deployed.
Visual and Mechanical Inspections
The first line of inspection involves a visual check.
Technicians look for any physical anomalies like cracks, misalignments, or poor soldering.
These defects can compromise the sensor’s performance, so identifying them early is critical.
Mechanical inspections assess the physical properties of the sensor.
Various tools measure dimensions, weight, and alignment to ensure the sensor meets design specifications.
Mechanical stress tests may also be conducted to check durability.
Electrical Testing
After passing visual and mechanical checks, the sensor undergoes electrical testing.
This involves applying signals to the sensor and measuring its response.
Tests may include resistance, capacitance, and signal output checks.
Advanced testing equipment analyzes the sensor’s response to ensure it falls within acceptable parameters.
Any deviations can indicate potential issues that need addressing before the sensor can be deemed reliable.
Environmental and Functional Testing
Environmental testing simulates real-world conditions.
Sensors are exposed to various temperatures, humidity levels, and pressures to gauge their performance.
These tests ensure the sensor can withstand harsh industrial environments.
Functional testing assesses the sensor’s ability to perform its intended role.
This involves integrating the sensor into a test setup that mimics actual operating conditions.
The sensor’s outputs are monitored to ensure they align with expected values.
Final Verification and Documentation
Once all tests are completed, the sensor undergoes a final verification.
This involves a comprehensive review of all test results to confirm the sensor meets all criteria.
If any issue is found, it is addressed before the sensor is cleared for deployment.
Documentation is another critical aspect of the inspection process.
Each sensor’s test results, calibration data, and inspection records are meticulously recorded.
This documentation serves as a reference for future maintenance and ensures traceability.
The Importance of Thorough Inspection
The meticulous inspection process for industrial sensors is not just about meeting quality standards.
It is about ensuring the sensors reliably perform their critical roles in industrial environments.
Faulty sensors can lead to significant operational disruptions and increased costs.
By rigorously inspecting and testing each sensor, manufacturers can prevent these issues and deliver high-quality products.
Investing in thorough inspection processes ultimately benefits the end-users, providing them with reliable and efficient sensor solutions.
Conclusion
Understanding the industrial sensor assembly and inspection processes highlights the complexity and precision involved.
From component selection to final verification, every step is critical in ensuring the sensor’s reliability and performance.
Manufacturers employ advanced techniques and rigorous testing to meet high standards.
Through these detailed processes, they provide sensors that support vital industrial operations, ensuring safety and efficiency.
By appreciating these processes, one can better understand the importance of quality in industrial sensor manufacturing and the effort that goes into creating reliable monitoring solutions.
資料ダウンロード
QCD調達購買管理クラウド「newji」は、調達購買部門で必要なQCD管理全てを備えた、現場特化型兼クラウド型の今世紀最高の購買管理システムとなります。
ユーザー登録
調達購買業務の効率化だけでなく、システムを導入することで、コスト削減や製品・資材のステータス可視化のほか、属人化していた購買情報の共有化による内部不正防止や統制にも役立ちます。
NEWJI DX
製造業に特化したデジタルトランスフォーメーション(DX)の実現を目指す請負開発型のコンサルティングサービスです。AI、iPaaS、および先端の技術を駆使して、製造プロセスの効率化、業務効率化、チームワーク強化、コスト削減、品質向上を実現します。このサービスは、製造業の課題を深く理解し、それに対する最適なデジタルソリューションを提供することで、企業が持続的な成長とイノベーションを達成できるようサポートします。
オンライン講座
製造業、主に購買・調達部門にお勤めの方々に向けた情報を配信しております。
新任の方やベテランの方、管理職を対象とした幅広いコンテンツをご用意しております。
お問い合わせ
コストダウンが利益に直結する術だと理解していても、なかなか前に進めることができない状況。そんな時は、newjiのコストダウン自動化機能で大きく利益貢献しよう!
(Β版非公開)