- お役立ち記事
- Manufacturing Process of Automatic Garment Steamers and Adjustment of Steam Output
Manufacturing Process of Automatic Garment Steamers and Adjustment of Steam Output
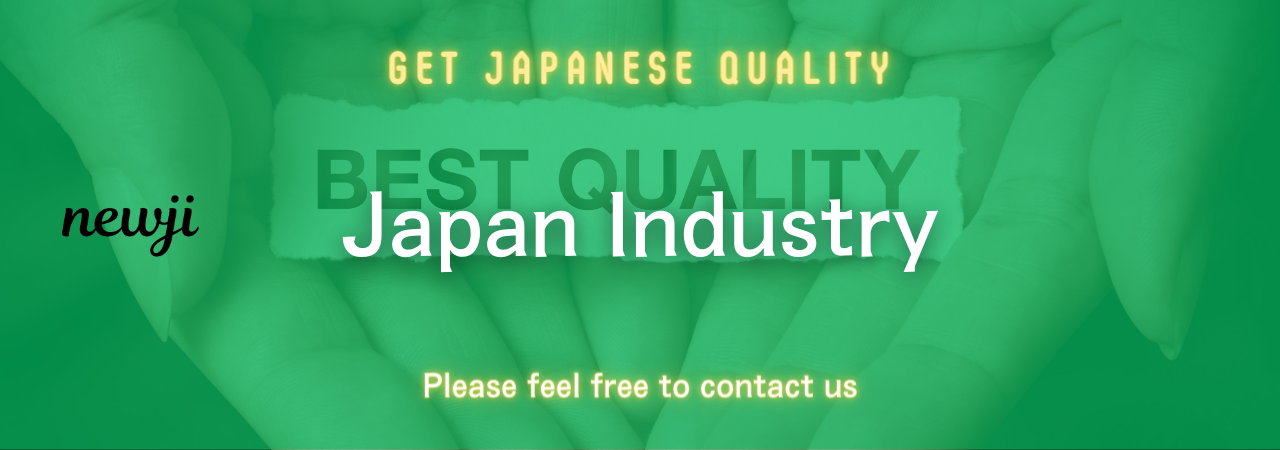
Automatic garment steamers have revolutionized the way we take care of our clothes, providing an efficient and quick way to remove wrinkles.
Understanding their manufacturing process and how to adjust their steam output can help you appreciate their functionality and ensure you use them correctly.
In this article, we’ll delve into these aspects in detail.
目次
Design and Conceptualization
The manufacturing process of an automatic garment steamer begins with the design and conceptualization phase.
Engineers and designers work together to create a blueprint that outlines the dimensions, features, and functionalities of the steamer.
This phase also includes deciding on the materials to be used, which are both durable and heat-resistant.
Initial Sketches and Prototypes
Initial sketches are drawn to provide a visual representation of the steamer.
These sketches are then converted into digital models using computer-aided design (CAD) software.
Prototypes are created from these digital models using 3D printing technology.
These prototypes are essential for testing the design’s practicality and functionality.
Material Selection
Material selection is crucial in the manufacturing process.
The materials chosen must withstand high temperatures and constant exposure to steam without degrading.
Types of Materials Used
Typically, the body of the steamer is made of high-grade plastic that can resist heat.
The internal components, such as the heating element and water reservoir, are often made of stainless steel or aluminum.
These materials are chosen for their durability and heat resistance.
Assembly Line Production
Once the design and materials are finalized, the assembly line production begins.
This phase involves the mass production of individual components, which are later assembled to form the complete steamer.
Component Manufacturing
Each component of the steamer is manufactured separately.
For instance, the heating element is crafted using high-resistance wire materials.
The water reservoir is molded using injection molding techniques, ensuring it is leak-proof and durable.
Quality Control
Quality control measures are implemented at every stage of component manufacturing.
Each piece is rigorously tested to ensure it meets the necessary standards.
Components that fail quality tests are discarded or sent back for rework.
Final Assembly
The final assembly process involves putting together all the individual components to form the complete steamer.
This is a meticulous process that requires precision and accuracy.
Step-by-Step Assembly
The heating element, water reservoir, and control unit are fixed into the steamer’s housing.
Electrical wiring is then connected to ensure the components work harmoniously.
The steamer is closed and sealed, and any external features, such as handles or buttons, are attached.
Testing the Steamer
Before the steamer is packaged and shipped, it undergoes extensive testing.
This includes checking the functionality of the heating element, ensuring there are no leaks, and verifying the steam output.
Only after passing these tests is the steamer approved for sale.
Adjusting the Steam Output
Understanding how to adjust the steam output of your automatic garment steamer is crucial for its efficient use.
The steam output can be adjusted based on the type of fabric you are steaming.
Here’s how you can do it.
Steam Settings
Most automatic garment steamers come with different steam settings.
These settings can usually be adjusted using a dial or button on the steamer.
Lower steam settings are ideal for delicate fabrics like silk, while higher settings are better suited for heavier fabrics such as cotton or linen.
Flow Control
Some steamers have a flow control feature that allows you to regulate the amount of steam produced.
This can be particularly useful when you are dealing with tough wrinkles.
To adjust the flow control, refer to the user manual for specific instructions as it may vary depending on the model.
Water Level
The water level in the reservoir can also affect the steam output.
Ensure that the reservoir is always filled to the recommended level.
An empty or low water reservoir can result in inadequate steam production.
Regular Maintenance
Regular maintenance of your steamer can help in maintaining optimal steam output.
Descaling the steamer periodically will prevent mineral build-up, which can block steam flow.
Cleaning the nozzles will also ensure that steam is distributed evenly.
Conclusion
Understanding the manufacturing process and steam output adjustment of automatic garment steamers can greatly enhance your user experience.
From initial design to final assembly, each step is meticulously carried out to ensure quality and functionality.
Adjusting the steam output according to the fabric type and maintaining the steamer regularly will ensure its longevity and efficiency.
By following these guidelines, you can keep your clothes wrinkle-free and in pristine condition effortlessly.
資料ダウンロード
QCD調達購買管理クラウド「newji」は、調達購買部門で必要なQCD管理全てを備えた、現場特化型兼クラウド型の今世紀最高の購買管理システムとなります。
ユーザー登録
調達購買業務の効率化だけでなく、システムを導入することで、コスト削減や製品・資材のステータス可視化のほか、属人化していた購買情報の共有化による内部不正防止や統制にも役立ちます。
NEWJI DX
製造業に特化したデジタルトランスフォーメーション(DX)の実現を目指す請負開発型のコンサルティングサービスです。AI、iPaaS、および先端の技術を駆使して、製造プロセスの効率化、業務効率化、チームワーク強化、コスト削減、品質向上を実現します。このサービスは、製造業の課題を深く理解し、それに対する最適なデジタルソリューションを提供することで、企業が持続的な成長とイノベーションを達成できるようサポートします。
オンライン講座
製造業、主に購買・調達部門にお勤めの方々に向けた情報を配信しております。
新任の方やベテランの方、管理職を対象とした幅広いコンテンツをご用意しております。
お問い合わせ
コストダウンが利益に直結する術だと理解していても、なかなか前に進めることができない状況。そんな時は、newjiのコストダウン自動化機能で大きく利益貢献しよう!
(Β版非公開)