- お役立ち記事
- Revolutionizing Japanese Manufacturing: The Role of Geomagnetic Sensors
Revolutionizing Japanese Manufacturing: The Role of Geomagnetic Sensors
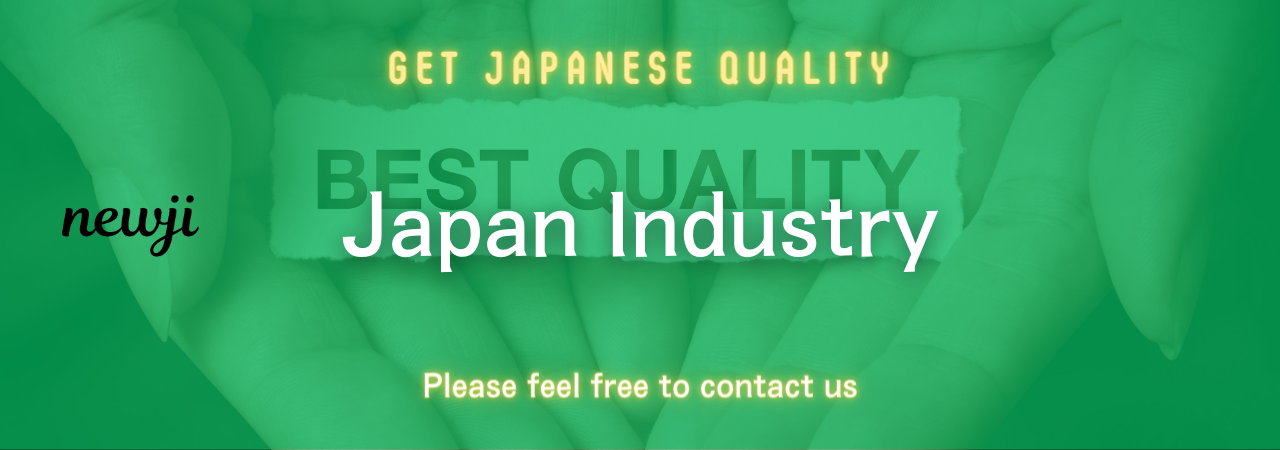
目次
The Significance of Geomagnetic Sensors in Japanese Manufacturing
In the ever-evolving landscape of manufacturing, continuous innovation is key to maintaining competitive advantage.
Japanese manufacturing companies, known globally for their precision and reliability, have embraced geomagnetic sensors as a transformative technology.
These sensors, critical components in modern production environments, have revolutionized various aspects of manufacturing, from automation to quality control.
Understanding Geomagnetic Sensors
Geomagnetic sensors are devices that measure the Earth’s magnetic field.
These sensors detect the direction, strength, and changes in the magnetic field, converting this data into electrical signals.
Commonly used in navigation systems, consumer electronics, and automotive applications, geomagnetic sensors have found a significant niche in manufacturing.
Advantages of Geomagnetic Sensors in Manufacturing
1. Enhanced Precision and Accuracy
Accuracy is a cornerstone of Japanese manufacturing.
Geomagnetic sensors offer high precision in detecting positions and movements, making them invaluable for robotic arms and automated guided vehicles (AGVs).
These sensors ensure tasks are performed consistently and accurately, reducing error margins significantly.
2. Improved Efficiency
Incorporating geomagnetic sensors in production lines enhances efficiency.
By providing real-time data on machinery and product movements, these sensors help streamline operations.
For instance, in automated warehouses, AGVs equipped with geomagnetic sensors can navigate seamlessly, reducing downtime and increasing productivity.
3. Increased Safety
Safety is paramount in any manufacturing setup.
Geomagnetic sensors contribute to safer work environments by preventing collisions and ensuring that machinery operates within designated parameters.
By providing accurate measurements and preventing equipment malfunctions, these sensors help mitigate workplace accidents.
4. Quality Control
Japanese manufacturers are renowned for their stringent quality control measures.
Geomagnetic sensors aid in maintaining high-quality standards by monitoring the consistency and integrity of products.
For instance, they can detect any deviation in a product’s assembly, ensuring that only goods that meet the desired specifications reach the market.
Disadvantages and Challenges
1. Cost
The integration of geomagnetic sensors can be expensive.
Initial costs for purchasing and installing these sensors, along with the necessary software and training, may be high.
Small and medium-sized enterprises (SMEs) may face financial constraints in adopting this technology.
2. Complexity in Integration
Incorporating geomagnetic sensors into existing manufacturing systems can be complex.
It requires a thorough understanding of current processes and potential adjustments.
Manufacturers need to ensure that their workforce is adequately trained to handle and maintain these advanced sensors.
3. Sensitivity to Environmental Factors
Geomagnetic sensors are sensitive to external magnetic interferences.
In manufacturing environments with heavy machinery or electronic equipment, these interferences can affect sensor readings.
Proper shielding and calibration are necessary to mitigate these challenges.
Practical Applications in Japanese Manufacturing
1. Automotive Manufacturing
The automotive industry is a major adopter of geomagnetic sensors.
In Japan, car manufacturers use these sensors for precise navigation of assembly robots and AGVs.
Geomagnetic sensors ensure that car parts are assembled with utmost precision, enhancing both efficiency and quality.
2. Consumer Electronics
Japan’s consumer electronics sector benefits immensely from geomagnetic sensors.
These sensors are embedded in devices to enhance user experience.
In manufacturing, they assist in the precise placement and alignment of small components, crucial for high-quality electronic products.
3. Robotics and Automation
Robotics is a field where geomagnetic sensors have made a significant impact.
Japanese manufacturers integrate these sensors into robotic systems for tasks requiring high precision.
From material handling to intricate assembly processes, geomagnetic sensors ensure robots operate accurately and efficiently.
Supplier Negotiation Techniques
Effective negotiation with suppliers is crucial to leveraging the benefits of geomagnetic sensors.
Here are some strategies:
1. Understanding Supplier Capabilities
Before entering negotiations, it’s essential to understand the supplier’s capabilities.
Know their strengths, limitations, and the specific geomagnetic sensor technologies they offer.
This information helps in setting realistic expectations and negotiating favorable terms.
2. Clear Communication of Requirements
Precisely communicate your technical and functional requirements.
Provide detailed specifications and use cases to ensure the supplier understands your needs.
Clear communication helps in getting a product that aligns with your manufacturing goals.
3. Building Long-Term Relationships
Focus on building long-term relationships with suppliers.
A collaborative approach fosters trust and can lead to better pricing, priority service, and access to the latest technological advancements.
4. Volume Discounts and Contract Terms
Negotiate for volume discounts and favorable contract terms.
Larger orders or long-term commitments can often secure better pricing.
Ensure the contract includes provisions for support, maintenance, and potential upgrades.
Market Conditions and Trends
The market for geomagnetic sensors is evolving rapidly.
Some key trends include:
1. Technological Advancements
Continuous advancements in sensor technology are leading to smaller, more efficient, and more accurate geomagnetic sensors.
These improvements are driving their adoption in various manufacturing sectors.
2. Rising Demand for Automation
The push towards Industry 4.0 is increasing the demand for automation and, consequently, for geomagnetic sensors.
Companies are increasingly seeking ways to streamline operations and improve efficiency through automation.
3. Integration with IoT
The integration of geomagnetic sensors with the Internet of Things (IoT) is another growing trend.
This combination allows for real-time monitoring and analysis, further enhancing manufacturing efficiency and decision-making processes.
Best Practices for Implementation
1. Comprehensive Planning
Effective implementation begins with comprehensive planning.
Conduct a thorough analysis of your manufacturing processes to identify areas where geomagnetic sensors can add value.
Develop a clear implementation plan with defined goals and timelines.
2. Employee Training
Invest in training your workforce.
Ensure employees understand how to use and maintain geomagnetic sensors.
Proper training minimizes errors and maximizes the benefits of these advanced sensors.
3. Regular Maintenance and Calibration
Regular maintenance and calibration are essential to ensure the accuracy and reliability of geomagnetic sensors.
Establish a maintenance schedule and adhere to it diligently.
4. Continuous Monitoring and Improvement
Continuously monitor the performance of geomagnetic sensors in your manufacturing setup.
Use the data collected to make informed decisions and drive continuous improvement.
Conclusion
Geomagnetic sensors are revolutionizing Japanese manufacturing, enhancing precision, efficiency, and quality.
Despite challenges such as cost and complexity, the benefits they offer far outweigh the disadvantages.
By effectively negotiating with suppliers, staying abreast of market trends, and adhering to best practices, manufacturers can successfully integrate geomagnetic sensors into their operations.
This integration not only improves the overall production process but also positions companies at the forefront of innovation and technology in the competitive manufacturing landscape.
資料ダウンロード
QCD調達購買管理クラウド「newji」は、調達購買部門で必要なQCD管理全てを備えた、現場特化型兼クラウド型の今世紀最高の購買管理システムとなります。
ユーザー登録
調達購買業務の効率化だけでなく、システムを導入することで、コスト削減や製品・資材のステータス可視化のほか、属人化していた購買情報の共有化による内部不正防止や統制にも役立ちます。
NEWJI DX
製造業に特化したデジタルトランスフォーメーション(DX)の実現を目指す請負開発型のコンサルティングサービスです。AI、iPaaS、および先端の技術を駆使して、製造プロセスの効率化、業務効率化、チームワーク強化、コスト削減、品質向上を実現します。このサービスは、製造業の課題を深く理解し、それに対する最適なデジタルソリューションを提供することで、企業が持続的な成長とイノベーションを達成できるようサポートします。
オンライン講座
製造業、主に購買・調達部門にお勤めの方々に向けた情報を配信しております。
新任の方やベテランの方、管理職を対象とした幅広いコンテンツをご用意しております。
お問い合わせ
コストダウンが利益に直結する術だと理解していても、なかなか前に進めることができない状況。そんな時は、newjiのコストダウン自動化機能で大きく利益貢献しよう!
(Β版非公開)