- お役立ち記事
- Revolutionizing Japanese Manufacturing: How Simcenter FLOEFD Enhances Efficiency and Innovation
Revolutionizing Japanese Manufacturing: How Simcenter FLOEFD Enhances Efficiency and Innovation
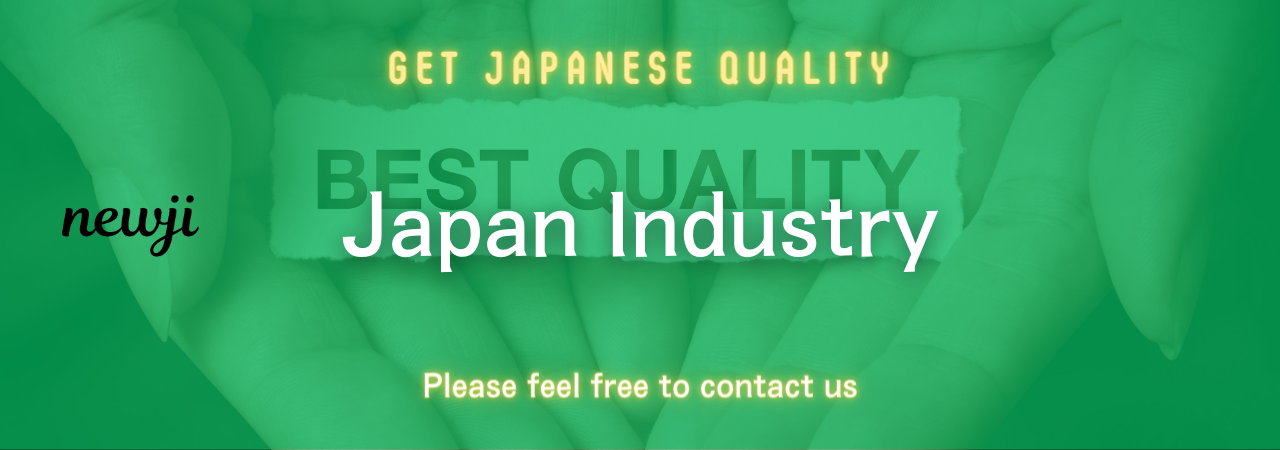
目次
Introduction to Simcenter FLOEFD in Japanese Manufacturing
Simcenter FLOEFD is a powerful computational fluid dynamics (CFD) software that has significantly transformed the landscape of Japanese manufacturing.
Developed by Siemens, this tool integrates deeply with popular CAD systems, making it easier for engineers to simulate fluid flow, heat transfer, and other complex phenomena directly within their design environment.
This article explores how Simcenter FLOEFD can enhance efficiency and drive innovation in Japanese manufacturing, drawing upon real-world experiences and case studies.
Understanding Japanese Manufacturing Excellence
Japanese manufacturing has long been revered for its focus on quality, precision, and continuous improvement.
Lean manufacturing principles, kaizen practices, and the meticulous attention to detail have become synonymous with the Japanese approach.
Kaizen: Continuous Improvement
Kaizen, the practice of continuous improvement, is a cornerstone of Japanese manufacturing excellence.
Companies focus on making small, incremental changes that collectively lead to significant improvements in efficiency, quality, and productivity.
Simcenter FLOEFD aligns perfectly with kaizen by enabling engineers to test and refine their designs more iteratively and efficiently.
Lean Manufacturing and Efficiency
Another fundamental aspect of Japanese manufacturing is lean production.
This methodology aims to minimize waste and maximize efficiency, focusing on delivering value to the customer.
Simcenter FLOEFD supports this approach by allowing engineers to simulate various scenarios, identify inefficiencies, and optimize processes in the design phase, effectively reducing time-to-market and resource consumption.
Advantages of Using Simcenter FLOEFD in Japanese Manufacturing
Simcenter FLOEFD offers numerous benefits that can revolutionize Japanese manufacturing practices.
Here are some key advantages:
Streamlined Workflow Integration
One of the distinguishing features of Simcenter FLOEFD is its deep integration with popular CAD systems like NX, Solid Edge, and PTC Creo.
This seamless integration allows engineers to perform CFD analysis directly within their CAD environment, eliminating the need to transfer data between different software tools.
It accelerates the design process and reduces the risk of errors.
Reduced Prototyping Costs
Simcenter FLOEFD enables virtual prototyping, which significantly cuts down the costs associated with physical prototyping.
By simulating real-world conditions, engineers can test multiple design iterations virtually and identify the optimal solution before moving to physical production.
This approach minimizes material wastage and reduces development costs.
Improved Design Accuracy
Accuracy is crucial in Japanese manufacturing, where even the smallest flaws can have significant repercussions.
Simcenter FLOEFD’s advanced solver technology ensures highly accurate simulations, allowing engineers to predict performance accurately and make informed decisions.
This precision is particularly beneficial in industries like automotive, electronics, and aerospace, where tolerances are tight, and reliability is paramount.
Enhanced Innovation
With Simcenter FLOEFD, engineers have the freedom to explore innovative designs without the constraints of traditional prototyping.
They can experiment with new materials, test unconventional geometries, and optimize complex systems, fostering a culture of innovation and pushing the boundaries of what’s possible.
Challenges and Considerations
While Simcenter FLOEFD offers many advantages, its implementation requires careful consideration.
Initial Investment and Training
Adopting new software involves an initial investment in licensing and training.
Companies must ensure that their teams are adequately trained to utilize the full potential of Simcenter FLOEFD.
However, the long-term benefits of reduced prototyping costs and faster time-to-market often justify the upfront expenditures.
Integration with Existing Systems
Integrating Simcenter FLOEFD with existing systems and workflows requires thorough planning and execution.
Companies should evaluate their current processes and determine how best to incorporate the software to maximize its benefits.
Collaborating with experienced consultants or Siemens professionals can facilitate a smooth transition.
Data Management
Handling the vast amounts of data generated by simulations can be challenging.
Companies need robust data management systems to store, retrieve, and analyze simulation results efficiently.
Implementing a centralized data management strategy can streamline operations and ensure consistency across projects.
Supplier Negotiation Techniques and Market Conditions
Working with Japanese suppliers requires a nuanced understanding of Japanese business culture and market conditions.
Cultural Sensitivity
Building strong relationships with Japanese suppliers hinges on understanding their culture.
Respect, patience, and politeness are highly valued traits in Japanese business dealings.
Communicating openly, honestly, and humbly can go a long way in establishing and maintaining trust.
Emphasizing Long-Term Partnerships
Japanese businesses often prefer long-term, stable partnerships over short-term gains.
Demonstrating a commitment to mutual growth and success can be pivotal in securing favorable terms and fostering strong collaboration.
Understanding Market Dynamics
The Japanese manufacturing market is highly competitive and dynamic.
Staying abreast of market trends, advancements, and competitor activities is essential for making informed decisions.
Regularly attending industry expos, conferences, and networking events can provide valuable insights into the latest developments.
Best Practices for Implementing Simcenter FLOEFD
Adopting Simcenter FLOEFD effectively requires a strategic approach.
Start with Pilot Projects
Implementing Simcenter FLOEFD on a smaller scale initially can help identify potential challenges and fine-tune processes.
Selecting a pilot project with realistic goals and clear metrics can provide valuable insights and build confidence among team members.
Invest in Training and Support
Ensuring that engineers are well-trained is critical for maximizing the software’s potential.
Offering comprehensive training programs and ongoing support can empower teams to utilize Simcenter FLOEFD effectively and innovate continuously.
Collaborate Cross-Functionally
Fostering collaboration between different departments, such as procurement, R&D, and production, can enhance the implementation of Simcenter FLOEFD.
Cross-functional teams can provide diverse perspectives, identify integration opportunities, and address challenges more holistically.
Leverage Vendor Expertise
Siemens and their partners offer extensive resources and expertise in implementing and optimizing Simcenter FLOEFD.
Leveraging this knowledge can expedite the integration process, overcome obstacles, and maximize returns on investment.
Case Studies and Real-World Applications
Numerous Japanese companies have successfully integrated Simcenter FLOEFD into their operations, achieving remarkable results.
Case Study: Automotive Industry
A leading Japanese automotive manufacturer used Simcenter FLOEFD to optimize the design of their cooling systems.
By simulating various scenarios, they identified an innovative design that improved cooling efficiency by 20%.
This led to enhanced vehicle performance and customer satisfaction.
Case Study: Electronics Industry
An electronics giant implemented Simcenter FLOEFD to refine the thermal management of their latest smartphone model.
Accurate simulations allowed them to identify and mitigate potential overheating issues, resulting in a more reliable product and reduced warranty claims.
Case Study: Aerospace Industry
A prominent aerospace company used Simcenter FLOEFD to enhance the aerodynamic performance of their latest aircraft design.
By simulating airflow and optimizing wing designs, they achieved a 15% reduction in drag, leading to significant fuel savings and lower operational costs.
Conclusion: Embracing the Future of Japanese Manufacturing
Simcenter FLOEFD is a game-changer for Japanese manufacturing.
Its ability to streamline workflows, reduce costs, and foster innovation aligns perfectly with the principles of kaizen and lean manufacturing.
While challenges exist, a strategic implementation can unlock tremendous benefits and drive Japanese manufacturing toward a more efficient and innovative future.
By leveraging the power of Simcenter FLOEFD, Japanese manufacturers can reinforce their position as global leaders, delivering high-quality, cutting-edge products to the market with unprecedented efficiency.
Embracing this technology not only upholds the tradition of excellence but also prepares the industry for the future, where digitalization and innovation are paramount.
資料ダウンロード
QCD調達購買管理クラウド「newji」は、調達購買部門で必要なQCD管理全てを備えた、現場特化型兼クラウド型の今世紀最高の購買管理システムとなります。
ユーザー登録
調達購買業務の効率化だけでなく、システムを導入することで、コスト削減や製品・資材のステータス可視化のほか、属人化していた購買情報の共有化による内部不正防止や統制にも役立ちます。
NEWJI DX
製造業に特化したデジタルトランスフォーメーション(DX)の実現を目指す請負開発型のコンサルティングサービスです。AI、iPaaS、および先端の技術を駆使して、製造プロセスの効率化、業務効率化、チームワーク強化、コスト削減、品質向上を実現します。このサービスは、製造業の課題を深く理解し、それに対する最適なデジタルソリューションを提供することで、企業が持続的な成長とイノベーションを達成できるようサポートします。
オンライン講座
製造業、主に購買・調達部門にお勤めの方々に向けた情報を配信しております。
新任の方やベテランの方、管理職を対象とした幅広いコンテンツをご用意しております。
お問い合わせ
コストダウンが利益に直結する術だと理解していても、なかなか前に進めることができない状況。そんな時は、newjiのコストダウン自動化機能で大きく利益貢献しよう!
(Β版非公開)