- お役立ち記事
- Differences Between Laser Cutting and Waterjet Cutting
Differences Between Laser Cutting and Waterjet Cutting
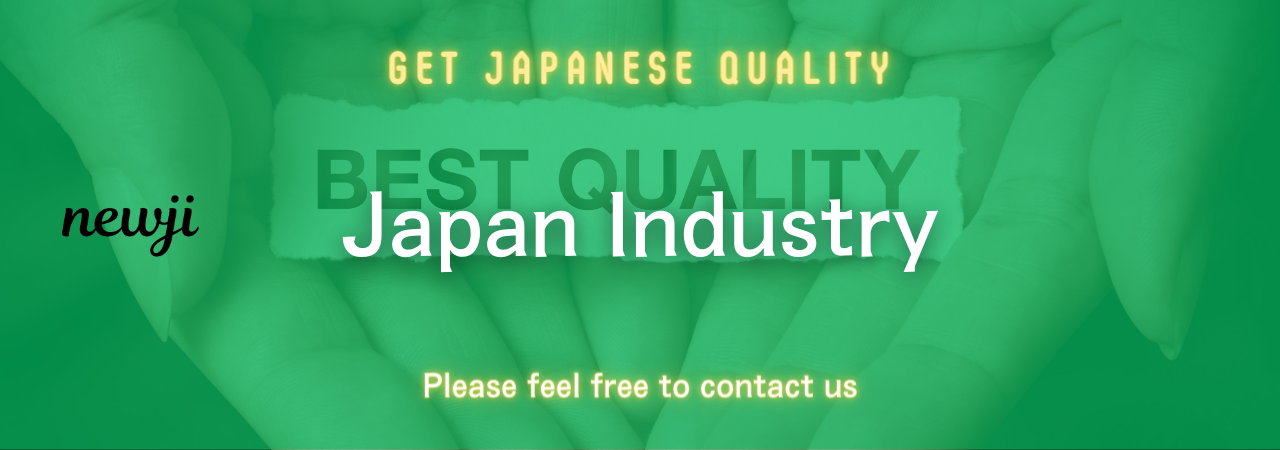
When it comes to precision cutting of materials like metal, wood, or plastic, two highly effective methods often come up: laser cutting and waterjet cutting.
Both techniques offer distinct advantages and are suitable for different applications.
Understanding the differences between laser cutting and waterjet cutting can help in choosing the right method for your specific needs.
目次
What is Laser Cutting?
Laser cutting is a technology that uses a concentrated beam of light to cut through materials.
The laser beam is directed onto the material, which heats up to the point of melting or vaporizing, allowing for precise cuts.
This method is highly accurate and can be used on a variety of materials, including metals, plastics, and woods.
How Does Laser Cutting Work?
Laser cutting machines use a combination of computer numerical control (CNC) and high-powered lasers.
A computer is programmed with the design to be cut, and the laser follows these instructions to produce the final product.
The laser beam is generally less than 0.32 mm in diameter, enabling it to make very precise cuts and intricate designs.
Laser cutters can cut through materials less than 20 mm thick, making them ideal for fine details.
Advantages of Laser Cutting
One major advantage of laser cutting is its precision.
The focused beam allows for intricate cuts and detailed designs that are difficult to achieve with other methods.
Laser cutting also produces very little waste material since the cuts are so fine.
Additionally, the process is faster than many traditional cutting methods, making it an efficient choice for high-volume production.
What is Waterjet Cutting?
Waterjet cutting involves using a high-pressure stream of water, often mixed with an abrasive material, to cut through materials.
This method is highly versatile and can cut through a wide range of materials, including metals, stone, glass, and composites.
Waterjets can penetrate materials up to 200 mm thick, making them suitable for heavy-duty cutting tasks.
How Does Waterjet Cutting Work?
Waterjet cutting machines operate by forcing a high-pressure stream of water through a small nozzle.
When cutting harder materials, abrasives like garnet are mixed with the water to enhance the cutting capability.
The pressurized stream travels at speeds up to 900 m/s, allowing it to erode material as it moves along its path.
The process is controlled by a computer, ensuring accuracy and repeatability.
Advantages of Waterjet Cutting
One key advantage of waterjet cutting is its capability to cut through a wider variety of materials.
Unlike laser cutting, waterjets can handle thicker and more durable materials without causing thermal distortion.
This makes waterjet cutting a preferred method for industries that deal with very thick or heat-sensitive materials.
Additionally, waterjet cutting is a “cold cutting” process, meaning it does not generate heat that could affect the structural integrity of the material being cut.
This is particularly important for materials like metal alloys and composites that are sensitive to temperature changes.
Comparison of Precision and Accuracy
When it comes to precision, laser cutting generally has an edge over waterjet cutting.
The focused laser beam allows for highly intricate cuts, which makes it ideal for fine detail work.
On the other hand, waterjet cutting is better suited for thick and multi-material cutting.
While waterjet cutters are precise, the addition of abrasives can sometimes lead to slight deviations in the cutting path, making it less ideal for extremely detailed projects.
Material Versatility
While both laser cutting and waterjet cutting are versatile, they each have their limitations.
Laser cutting is highly effective for thin to moderately thick materials like metals, plastics, and woods, but less effective for thicker or heat-sensitive materials.
Waterjet cutting is more versatile in terms of the types of materials it can cut, from metals and stone to glass and foam.
If you deal with a wide range of materials, waterjet cutting may offer the flexibility you need.
Operating Costs
The operating costs for laser cutting and waterjet cutting can vary significantly.
Laser cutting equipment can be more expensive to maintain due to the cost of the laser source and the need for precise calibration.
However, it is generally more efficient with quick setup times and higher cutting speeds, making it cost-effective for high-volume production.
Waterjet cutting equipment, on the other hand, has lower initial setup costs but higher operating costs due to the consumption of water and abrasives.
The cost of disposing of used abrasives and managing water waste should also be considered.
Environmental Considerations
In terms of environmental impact, both cutting methods have their pros and cons.
Laser cutting produces less waste material and is generally more energy-efficient.
However, it can produce harmful fumes depending on the material being cut, necessitating good ventilation systems.
Waterjet cutting, while producing no harmful fumes, consumes a significant amount of water and creates slurry waste that must be managed.
Recycling and water filtration systems can mitigate some of these impacts but add to the overall operating costs.
Choosing the Right Cutting Method
The best cutting method for your project will depend on several factors, including the type of material, thickness, desired precision, and budget.
For high-precision, intricate designs on thinner materials, laser cutting is often the preferred choice.
It’s particularly useful in the electronics, automotive, and medical industries where precision is crucial.
If you’re dealing with thick, hard-to-cut materials or a variety of different materials, waterjet cutting may be the better option.
Industries like aerospace, construction, and metal fabrication often turn to waterjet cutting for its versatility and ability to handle tough materials.
Understanding the differences between laser cutting and waterjet cutting can help you make an informed decision that meets your specific needs.
Both methods have their strengths and can be extremely effective when used appropriately.
Whether you prioritize precision, material versatility, or cost, knowing what each cutting technique entails will ensure you choose the right tool for the job.
資料ダウンロード
QCD調達購買管理クラウド「newji」は、調達購買部門で必要なQCD管理全てを備えた、現場特化型兼クラウド型の今世紀最高の購買管理システムとなります。
ユーザー登録
調達購買業務の効率化だけでなく、システムを導入することで、コスト削減や製品・資材のステータス可視化のほか、属人化していた購買情報の共有化による内部不正防止や統制にも役立ちます。
NEWJI DX
製造業に特化したデジタルトランスフォーメーション(DX)の実現を目指す請負開発型のコンサルティングサービスです。AI、iPaaS、および先端の技術を駆使して、製造プロセスの効率化、業務効率化、チームワーク強化、コスト削減、品質向上を実現します。このサービスは、製造業の課題を深く理解し、それに対する最適なデジタルソリューションを提供することで、企業が持続的な成長とイノベーションを達成できるようサポートします。
オンライン講座
製造業、主に購買・調達部門にお勤めの方々に向けた情報を配信しております。
新任の方やベテランの方、管理職を対象とした幅広いコンテンツをご用意しております。
お問い合わせ
コストダウンが利益に直結する術だと理解していても、なかなか前に進めることができない状況。そんな時は、newjiのコストダウン自動化機能で大きく利益貢献しよう!
(Β版非公開)