- お役立ち記事
- Unlocking Efficiency: How the Japanese “Supplier Master” Revolutionizes Manufacturing Supply Chains
Unlocking Efficiency: How the Japanese “Supplier Master” Revolutionizes Manufacturing Supply Chains
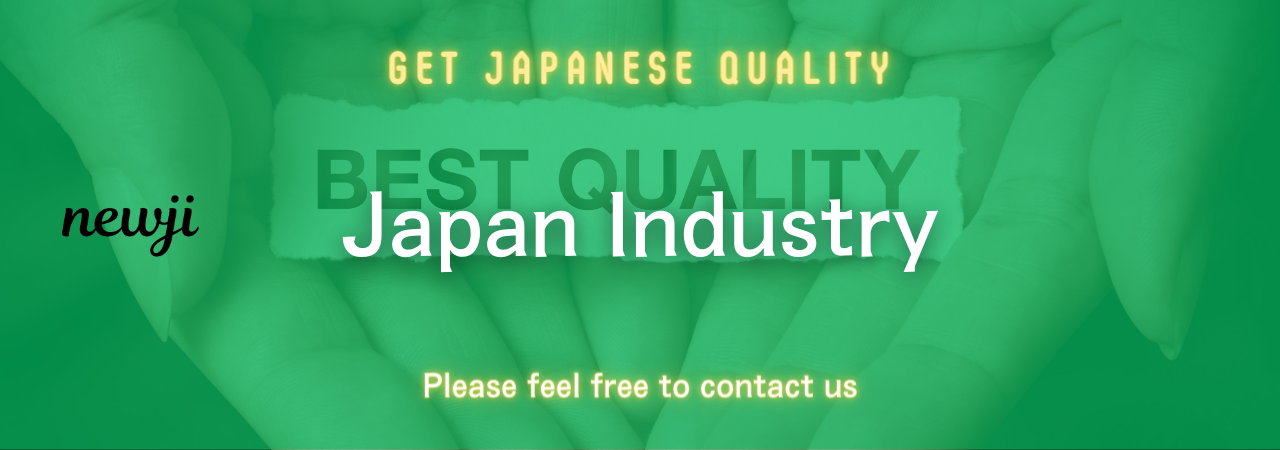
目次
Understanding the Japanese “Supplier Master”
The term “Supplier Master” refers to a unique model of supplier management that has been developed and perfected by Japanese manufacturing companies over decades.
This concept goes beyond the traditional supplier-buyer relationships, emphasizing mutual trust, innovation, and long-term partnership.
The Supplier Master approach integrates deeply into the core of manufacturing supply chains, significantly boosting efficiency and competitiveness.
Japanese companies are renowned for their commitment to quality, innovation, and continuous improvement – principles that are at the heart of the Supplier Master strategy.
Understanding this system requires exploring the cultural and operational nuances that underpin Japanese industrial practices.
Historical Context and Cultural Influences
Japanese business culture values long-term relationships and loyalty, which are crucial factors in the Supplier Master framework.
Rooted in the principle of “keiretsu,” a system where allied companies share resources and support each other, the Supplier Master approach fosters collaborative partnerships rather than transactional engagements.
These historical influences have resulted in a supply chain culture that prioritizes stability, innovation, and sustained growth.
Japanese manufacturers often work closely with suppliers from early development stages, ensuring alignment and shared goals.
Components of the Supplier Master Strategy
The Supplier Master model is characterized by several key components that distinguish it from traditional supplier management techniques:
Long-Term Relationship Building
Japanese manufacturers invest significant effort into cultivating long-term relationships with their suppliers.
This is not merely a business strategy but a cultural priority.
By developing deep bonds and trust, Japanese companies promote transparency, collaboration, and shared risk-taking.
Emphasis on Quality Control
A cornerstone of the Supplier Master approach is an unwavering commitment to quality.
Japanese companies and their suppliers collaborate closely to maintain and improve product standards.
This often involves mutual audits, shared quality control processes, and integrated systems that allow both parties to work toward common quality objectives.
Strategic Alignment and Joint Development
Japanese manufacturers often engage suppliers as strategic partners, involving them in product development and innovation processes.
This collaboration extends to shared R&D efforts, co-designing products, and collectively solving technical challenges.
Such integration not only enhances product quality but also accelerates innovation cycles.
Continuous Improvement (Kaizen)
The philosophy of Kaizen, or continuous improvement, is deeply ingrained in the Japanese Supplier Master approach.
Both manufacturers and suppliers are committed to constantly seeking ways to enhance processes, reduce waste, and improve efficiency.
This ongoing drive for improvement leads to cumulative gains, fostering a competitive edge.
Advantages of the Japanese Supplier Master Approach
Adopting the Supplier Master approach brings numerous benefits, particularly for global companies seeking to optimize their supply chains.
Enhanced Supply Chain Resilience
The strong relationships and mutual support systems fostered by the Supplier Master model enhance supply chain resilience.
Companies are better prepared to handle disruptions, thanks to the tightly-knit networks that facilitate resource sharing and problem-solving.
Improved Product Quality
By embedding quality control into every stage of the supply chain, the Supplier Master approach ensures consistently high product quality.
This emphasis on quality not only satisfies customer expectations but also reduces costs associated with defects and recalls.
Innovation and Competitive Advantage
The collaborative nature of the Supplier Master model accelerates innovation.
By involving suppliers in development processes and leveraging their expertise, companies can achieve technological advancements that set them apart in the market.
Cost Efficiency
While the initial investment in building long-term supplier relationships may be higher, the Supplier Master approach ultimately leads to cost efficiency.
Reduced defects, streamlined processes, and shared R&D efforts result in lower overall production costs.
Challenges and Disadvantages
While the Supplier Master model offers significant advantages, it is not without challenges and potential disadvantages.
Time and Resource Investment
Developing and maintaining long-term supplier relationships requires substantial time and resource investment.
This can be a barrier for companies seeking quick returns or operating in fast-paced industries where speed is paramount.
Cultural Misalignment
Companies not accustomed to Japanese business culture may struggle with the long-term focus and the importance placed on relationship-building.
Cultural differences can lead to misunderstandings and misalignment between international companies and Japanese suppliers.
Dependency and Risk
The interdependency fostered by the Supplier Master model can be a double-edged sword.
While it enhances collaboration, it also means that problems at one supplier can have a far-reaching impact on the entire supply chain.
Careful risk management and diversification are needed to mitigate these risks.
Supplier Negotiation Techniques
In the context of the Supplier Master approach, negotiation is not about winning; it’s about building viable, long-term partnerships.
Building Trust and Communication
Effective negotiation begins with establishing trust.
This involves transparency, consistency, and a mutual commitment to shared goals.
Open lines of communication and regular dialogue are essential to foster a trusting relationship.
Understanding Cultural Nuances
Cultural sensitivity is crucial when negotiating with Japanese suppliers.
American and European companies, for example, may prioritize assertiveness in negotiations, whereas Japanese companies often value patience and relationship-building.
Understanding these cultural differences can lead to more fruitful discussions and better outcomes.
Emphasizing Mutual Benefits
Negotiations should focus on creating value for both parties.
By identifying areas of mutual benefit, companies and suppliers can reach agreements that strengthen their partnership and produce better long-term results.
Market Conditions and Best Practices
The global market for manufacturing supplies is continuously evolving, influenced by technological advancements, regulatory changes, and economic fluctuations.
Adapting to Market Conditions
Companies engaged in the Supplier Master approach must remain agile and adaptable.
This involves staying informed about market trends, actively participating in industry discussions, and being ready to pivot strategies to align with changing conditions.
Leveraging Technology
Technology plays a critical role in optimizing supply chains.
From AI-driven analytics to IoT-enabled systems, embracing innovative technologies can enhance communication, streamline operations, and improve decision-making processes.
Continuous Training and Development
Investing in employee training ensures that both manufacturers and suppliers remain competitive and capable of adopting the latest industry best practices.
Encouraging continuous learning supports innovation and enhances the overall efficiency of the supply chain.
Conclusion
The Japanese Supplier Master model represents a transformative approach to supply chain management.
By prioritizing long-term relationships, emphasizing quality and innovation, and fostering a culture of continuous improvement, this approach unlocks new levels of efficiency and competitiveness.
While challenges exist, the benefits of adopting the Supplier Master strategy are substantial for companies willing to invest in these relationships.
As the global market continues to evolve, the principles embedded in the Supplier Master approach offer a timeless blueprint for enhancing supply chain effectiveness and driving sustainable growth.
資料ダウンロード
QCD調達購買管理クラウド「newji」は、調達購買部門で必要なQCD管理全てを備えた、現場特化型兼クラウド型の今世紀最高の購買管理システムとなります。
ユーザー登録
調達購買業務の効率化だけでなく、システムを導入することで、コスト削減や製品・資材のステータス可視化のほか、属人化していた購買情報の共有化による内部不正防止や統制にも役立ちます。
NEWJI DX
製造業に特化したデジタルトランスフォーメーション(DX)の実現を目指す請負開発型のコンサルティングサービスです。AI、iPaaS、および先端の技術を駆使して、製造プロセスの効率化、業務効率化、チームワーク強化、コスト削減、品質向上を実現します。このサービスは、製造業の課題を深く理解し、それに対する最適なデジタルソリューションを提供することで、企業が持続的な成長とイノベーションを達成できるようサポートします。
オンライン講座
製造業、主に購買・調達部門にお勤めの方々に向けた情報を配信しております。
新任の方やベテランの方、管理職を対象とした幅広いコンテンツをご用意しております。
お問い合わせ
コストダウンが利益に直結する術だと理解していても、なかなか前に進めることができない状況。そんな時は、newjiのコストダウン自動化機能で大きく利益貢献しよう!
(Β版非公開)