- お役立ち記事
- Bowling Ball Manufacturing Process and Balance Improvement
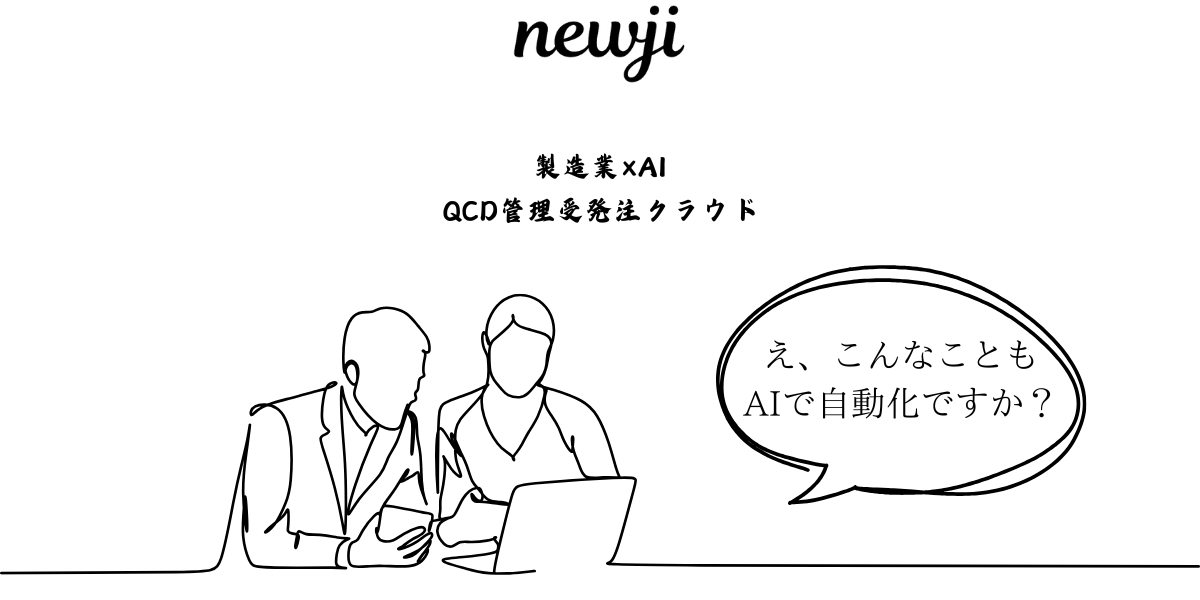
Bowling Ball Manufacturing Process and Balance Improvement
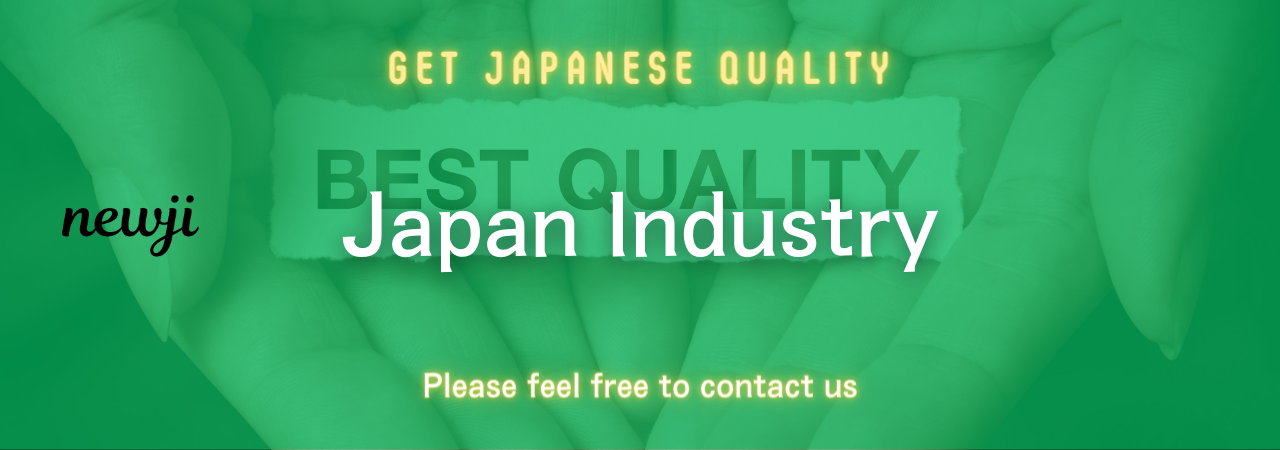
目次
Introduction to Bowling Ball Manufacturing
Bowling is a sport loved by people of all ages and abilities worldwide.
At the heart of this game lies the bowling ball, a precisely engineered piece of equipment.
Understanding how a bowling ball is manufactured can give insight into its performance and quality.
In this article, we’ll explore the intriguing process of bowling ball manufacturing and how improvements in balance contribute to its overall use.
Raw Materials and Composition
Bowling balls are made from various materials, including polyester, urethane, and reactive resin.
The selection of material largely affects the ball’s performance characteristics.
Polyester, often used in beginners’ balls, offers a harder surface that glides smoothly on the lane.
Urethane provides better traction, causing the ball to hook more.
Reactive resin balls deliver even higher friction, offering maximum control for skilled players.
Manufacturers procure high-quality raw materials and then start the production process.
This involves crafting the core, coverstock, and assembling these parts with precision.
Blueprinting the Core
The core is the heart of any bowling ball.
It’s crucial in determining how a ball behaves on a lane.
Depending on the design, cores could be symmetric or asymmetric.
Symmetric cores are evenly balanced, typically offering a more predictable reaction.
Asymmetric cores, on the other hand, provide increased dynamics, which influence the ball’s motion in complex ways.
Core design is key to the balance and overall performance of a bowling ball.
Engineers use computer-aided design (CAD) software to create blueprints, ensuring that every aspect aligns perfectly to desired performance specifications.
Moulding the Core
Once designed, the core is molded using dense materials like ceramic, bismuth graphite, and other substances.
These materials offer the utmost precision due to their weight and density.
The core is formed in a mold where these materials are injected under high pressure.
After the material solidifies, the core is removed and examined to ensure it matches the intended design specifications.
Applying the Coverstock
Next comes the application of the coverstock, which is usually made of polyester, urethane, or reactive resin, as previously mentioned.
This step involves encasing the core with the selected coverstock material.
The chosen material is heated until it becomes pliable, then poured over the core in a mold.
Once it cools and hardens, the ball undergoes a process called lathe turning, where any excess material is trimmed, resulting in a smooth, rounded surface.
Sculpting the Perfect Surface
The ball’s surface texture significantly influences its friction with the lane.
Different textures are achieved through sanding and polishing processes.
Sanding can create a matte finish that helps the ball grip the lane, while polishing can give a glossy surface for less friction.
Manufacturers use a grit scale to determine the sanding level, tailoring it to the desired performance.
The balance between sanding and polishing is essential to achieve an optimal balance for each bowling ball type.
Enhancing Balance
Balance in a bowling ball is not just about symmetry in weight but ensuring that it travels in a straight, predictable path or hooks in a consistent curve, as desired.
To improve balance, manufacturers focus on the weight distribution within the ball.
Weights, known as balance blocks, are added into the core during manufacturing.
These adjustments allow the ball manufacturer to control how weight is distributed across the ball, affecting the roll and hook potential.
Finally, quality control checks ensure that each ball meets strict tolerances for imbalances.
This ensures every ball rolls true to design specifications, providing bowlers with consistent performance across the board.
Testing and Quality Control
Before reaching consumers, each bowling ball undergoes rigorous testing.
This includes checks for quality, balance, and performance compliance with the manufacturer’s specifications.
State-of-the-art equipment measures balls for perfect roundness and appropriate weight.
Experts test durability by simulating repeated use.
Only after passing these evaluations are balls approved for shipment to local sports shops and consumers.
Conclusion
The intricate process of manufacturing a bowling ball involves a scientific blend of materials, precise engineering, and fine-tuned balance adjustments.
A well-manufactured ball contributes significantly to a player’s performance, offering control, predictability, and power.
Understanding this process enhances appreciation for the craftsmanship and technology behind every shot, making the experience more enjoyable for both amateur and professional bowlers alike.
Next time you hit the lanes, you can roll with greater confidence, knowing the technology hard at work within your bowling ball.
資料ダウンロード
QCD調達購買管理クラウド「newji」は、調達購買部門で必要なQCD管理全てを備えた、現場特化型兼クラウド型の今世紀最高の購買管理システムとなります。
ユーザー登録
調達購買業務の効率化だけでなく、システムを導入することで、コスト削減や製品・資材のステータス可視化のほか、属人化していた購買情報の共有化による内部不正防止や統制にも役立ちます。
NEWJI DX
製造業に特化したデジタルトランスフォーメーション(DX)の実現を目指す請負開発型のコンサルティングサービスです。AI、iPaaS、および先端の技術を駆使して、製造プロセスの効率化、業務効率化、チームワーク強化、コスト削減、品質向上を実現します。このサービスは、製造業の課題を深く理解し、それに対する最適なデジタルソリューションを提供することで、企業が持続的な成長とイノベーションを達成できるようサポートします。
オンライン講座
製造業、主に購買・調達部門にお勤めの方々に向けた情報を配信しております。
新任の方やベテランの方、管理職を対象とした幅広いコンテンツをご用意しております。
お問い合わせ
コストダウンが利益に直結する術だと理解していても、なかなか前に進めることができない状況。そんな時は、newjiのコストダウン自動化機能で大きく利益貢献しよう!
(Β版非公開)