- お役立ち記事
- Air Pump Manufacturing Process and Durability Improvement
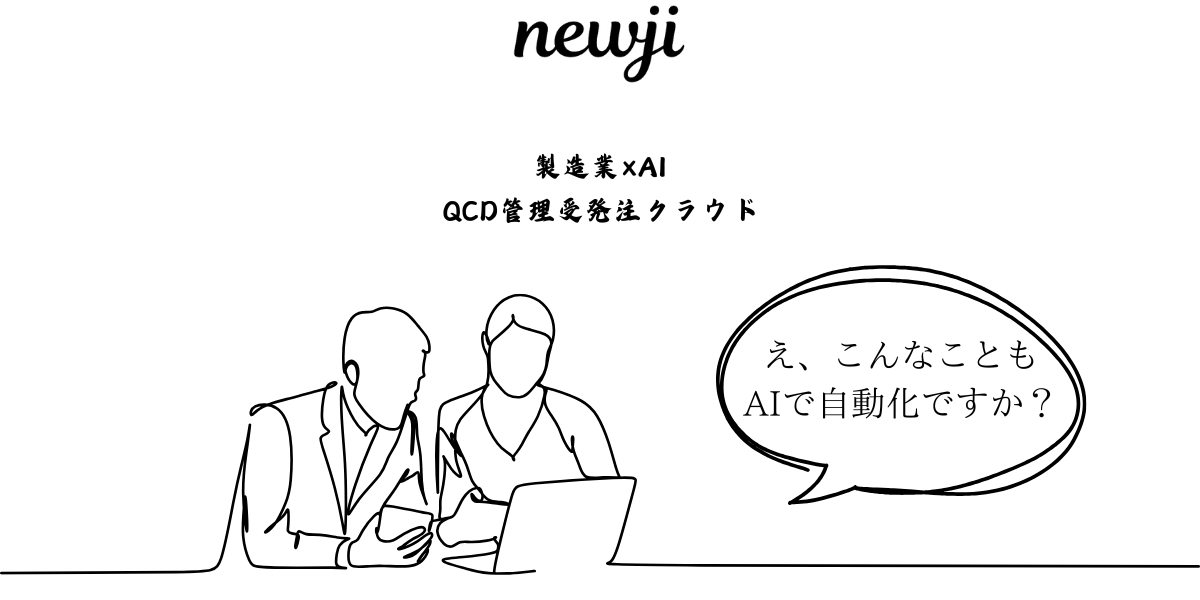
Air Pump Manufacturing Process and Durability Improvement
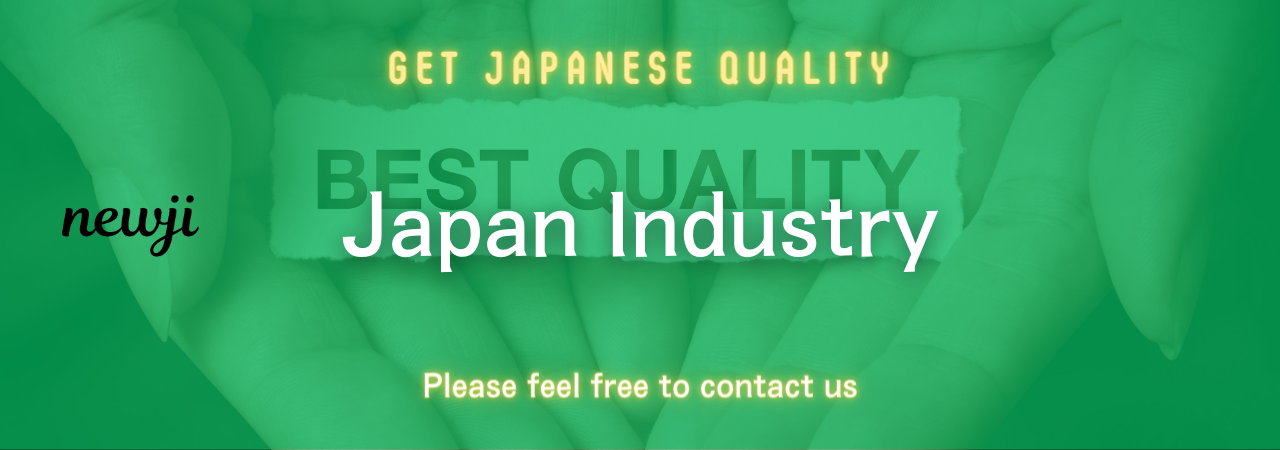
目次
Introduction to Air Pump Manufacturing
Air pumps are essential tools used in various applications, from inflating vehicle tires to industrial uses.
They are widely used due to their efficiency and reliability.
The manufacturing of air pumps involves several processes, each crucial to ensuring the final product’s quality and performance.
The process begins with the design phase, moves through material selection, and ends with assembly and quality testing.
Design and Material Selection
The first step in manufacturing air pumps is designing.
This involves determining the pump’s intended use, required pressure capacity, and other specifications.
Engineers create detailed blueprints and 3D models to guide the production process.
Material selection is equally critical in this stage.
Manufacturers choose materials based on durability, cost-effectiveness, and suitability for the pump’s intended application.
Common materials include metals like aluminum and steel, as well as plastics for lightweight designs.
The selected materials must withstand high pressure, wear, and other environmental conditions.
Component Manufacturing
Once the materials are selected, the manufacturing of individual components begins.
This process includes casting, machining, and molding parts like cylinders, pistons, and valves.
Precision is crucial in component manufacturing to ensure a tight fit and efficient operation.
Modern manufacturing techniques, such as CNC machining, are used to achieve high precision.
These machines operate automatically, guided by computer programs, to create complex shapes and designs.
Quality control measures are in place to check each component’s dimensions and integrity.
Assembly Line Process
After individual components are fabricated, the assembly process begins.
This is where all the parts come together to form a complete air pump.
Assembly usually happens on a production line, where each station adds specific components to the pump.
The assembly process involves attaching the pump motor, connecting the valves, and securing housing elements.
Moreover, it’s essential to ensure that seals and gaskets are perfectly placed to prevent air leaks.
Automation is often used in the assembly process to increase efficiency and consistency.
Testing for Durability and Performance
Testing is a critical phase in the manufacturing of air pumps.
It ensures that the pumps can withstand operational stresses and function efficiently over time.
During testing, engineers simulate real-world operating conditions, checking the pump’s pressure output, noise levels, and overall performance.
Long-term durability tests expose the pump to continuous operation for extensive periods.
This helps identify potential weaknesses in materials or design that could lead to premature failure.
Testing also involves checking for air leaks, which could compromise the pump’s effectiveness.
Improvements in Durability
Improving air pump durability is an ongoing focus for manufacturers.
One approach is using advanced materials that resist wear and corrosion.
By incorporating materials like stainless steel or advanced polymers, manufacturers can enhance the pump’s lifespan.
Another method is improving the pump’s design for better efficiency and longevity.
Incorporating features such as variable speed motors can reduce wear by allowing the pump to operate only as needed.
Regular maintenance recommendations are also provided to users to prolong pump life.
Innovations in Air Pump Technology
The air pump industry continually benefits from technological advancements.
Innovations such as smart pumps, which can adjust their operation based on usage data, are becoming common.
These smart pumps offer improvements in energy efficiency and performance monitoring.
Additionally, noise reduction technology is being integrated into new models.
By redesigning internal components to minimize vibration, manufacturers make quieter pumps without sacrificing performance.
Sustainability and Environmental Considerations
As with many manufacturing sectors, there is a growing emphasis on sustainability in air pump production.
Manufacturers are exploring eco-friendly materials and processes to reduce their environmental impact.
This includes recycling materials and improving production efficiency to minimize waste.
The adoption of energy-efficient designs and manufacturing processes also contributes to sustainability.
Manufacturers are focusing on reducing power consumption during both production and pump operation.
Conclusion
The manufacturing process of air pumps involves a series of detailed steps, from design and material selection to assembly and testing.
Each phase is crucial to ensure the pump’s effectiveness and durability.
By continually improving materials, designs, and technologies, manufacturers are creating air pumps that are more reliable and environmentally friendly.
Understanding these processes highlights the importance of precision and innovation in making air pumps that meet both current and future demands.
As technology advances, we can anticipate further improvements in air pump manufacturing and durability, contributing significantly to various industries and everyday applications worldwide.
資料ダウンロード
QCD調達購買管理クラウド「newji」は、調達購買部門で必要なQCD管理全てを備えた、現場特化型兼クラウド型の今世紀最高の購買管理システムとなります。
ユーザー登録
調達購買業務の効率化だけでなく、システムを導入することで、コスト削減や製品・資材のステータス可視化のほか、属人化していた購買情報の共有化による内部不正防止や統制にも役立ちます。
NEWJI DX
製造業に特化したデジタルトランスフォーメーション(DX)の実現を目指す請負開発型のコンサルティングサービスです。AI、iPaaS、および先端の技術を駆使して、製造プロセスの効率化、業務効率化、チームワーク強化、コスト削減、品質向上を実現します。このサービスは、製造業の課題を深く理解し、それに対する最適なデジタルソリューションを提供することで、企業が持続的な成長とイノベーションを達成できるようサポートします。
オンライン講座
製造業、主に購買・調達部門にお勤めの方々に向けた情報を配信しております。
新任の方やベテランの方、管理職を対象とした幅広いコンテンツをご用意しております。
お問い合わせ
コストダウンが利益に直結する術だと理解していても、なかなか前に進めることができない状況。そんな時は、newjiのコストダウン自動化機能で大きく利益貢献しよう!
(Β版非公開)