- お役立ち記事
- Safety Management in Weaving Factories and Employee Initiatives
Safety Management in Weaving Factories and Employee Initiatives
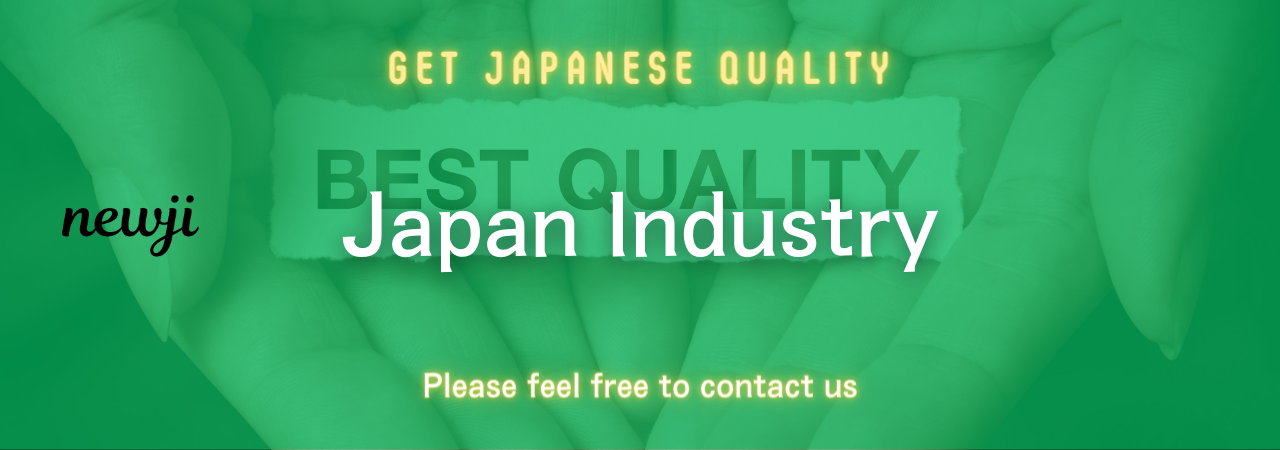
目次
Understanding Safety Management in Weaving Factories
Safety management is an essential aspect of any manufacturing industry, especially in weaving factories where workers often handle large machinery and complex materials.
The primary goal is to protect the health and wellness of employees while optimizing operational efficiency.
Creating a safe environment not only enhances productivity but also helps in complying with legal standards and building a trustworthy brand image.
Before exploring employee initiatives, it’s crucial to understand the key components of safety management in these settings.
These include hazard identification, risk assessment, control measures, and continuous monitoring.
Hazard Identification
Identifying potential hazards is the first step in establishing a safety framework.
In a weaving factory, these could range from mechanical hazards like moving parts and equipment failure to ergonomic issues such as repetitive strain from machinery operation.
Chemical hazards could also arise from the dyes and solvents used in fabric production.
Awareness of these risks enables management to develop appropriate safety measures.
Risk Assessment
Once hazards are identified, assessing the risk involved with each plays a crucial role in safety management.
This process involves evaluating the likelihood of hazardous events occurring and determining the potential impact on employees and operations.
By prioritizing risks, factories can allocate resources more effectively to address the most critical safety concerns.
Control Measures
Control measures are the strategies implemented to mitigate identified risks.
These include engineering controls such as machine guards and safety interlocks, administrative controls like safety protocols and procedures, and personal protective equipment (PPE) for workers.
Training staff on proper safety practices and emergency response procedures is equally important.
Regular maintenance of equipment and safety audits ensure that control measures remain effective over time.
Continuous Monitoring
Safety management is not a one-time event but an ongoing process.
Continuous monitoring involves regularly reviewing and updating safety protocols based on new developments and feedback from employees.
Accident and incident reporting systems should be in place to capture data for further analysis and improvement.
Management should encourage a culture of transparency where workers feel comfortable reporting safety issues without fear of reprisal.
Employee Initiatives for Safety Management
Employees are at the forefront of safety management in weaving factories.
Their active participation is essential to prevent accidents and promote a safe work environment.
Here are some initiatives that employees can undertake to enhance safety in their workplaces:
Engaging in Safety Training
Education is a critical tool for empowering employees to take charge of their safety.
Workers should regularly participate in safety training sessions to stay updated on best practices and protocols.
Training should cover the correct use of equipment, emergency response, and first-aid procedures.
By being well-informed, employees are better equipped to handle potentially hazardous situations.
Promoting a Safety Culture
A positive safety culture encourages workers to prioritize safety in every task they undertake.
Employees should be encouraged to speak up about unsafe conditions or suggest improvements to current safety measures.
Peer support and recognitions, such as “safety employee of the month” awards, can motivate workers to adhere to and promote safety protocols.
Management should lead by example, demonstrating their commitment to building a safety-first environment.
Participating in Safety Committees
Safety committees play a significant role in improving workplace safety.
Employees can volunteer to be part of these committees to work collaboratively with management in identifying safety issues and developing practical solutions.
Members of the committee act as representatives for their peers, voicing concerns and providing feedback on safety policies.
Active participation ensures that the interests and wellbeing of all employees are considered in decision-making.
Reporting Incidents and Near Misses
Promptly reporting accidents, incidents, and near misses helps identify trends and potential areas for improvement.
Employees should be encouraged to report any safety concerns without the fear of blame or repercussions.
Knowing that their input is valued and will lead to action promotes openness and transparency.
By analyzing these reports, management can implement changes that prevent future occurrences.
Maintaining Personal Responsibility
While collective efforts are crucial, individual responsibility is equally important.
Employees should always adhere to safety procedures and wear the required PPE for each task.
Staying vigilant, following instructions, and maintaining good housekeeping practices can significantly reduce the risk of accidents.
By taking personal responsibility for their actions, employees contribute to a safer workplace for everyone.
Conclusion
Safety management in weaving factories is vital in protecting workers and ensuring smooth operations.
The collaboration between management and employees is key to achieving an effective safety framework.
By implementing comprehensive safety measures and encouraging active employee participation, weaving factories can create a secure and productive working environment.
Ultimately, prioritizing safety fosters trust, reliability, and efficiency in the workplace, benefiting both employees and the organization as a whole.
資料ダウンロード
QCD調達購買管理クラウド「newji」は、調達購買部門で必要なQCD管理全てを備えた、現場特化型兼クラウド型の今世紀最高の購買管理システムとなります。
ユーザー登録
調達購買業務の効率化だけでなく、システムを導入することで、コスト削減や製品・資材のステータス可視化のほか、属人化していた購買情報の共有化による内部不正防止や統制にも役立ちます。
NEWJI DX
製造業に特化したデジタルトランスフォーメーション(DX)の実現を目指す請負開発型のコンサルティングサービスです。AI、iPaaS、および先端の技術を駆使して、製造プロセスの効率化、業務効率化、チームワーク強化、コスト削減、品質向上を実現します。このサービスは、製造業の課題を深く理解し、それに対する最適なデジタルソリューションを提供することで、企業が持続的な成長とイノベーションを達成できるようサポートします。
オンライン講座
製造業、主に購買・調達部門にお勤めの方々に向けた情報を配信しております。
新任の方やベテランの方、管理職を対象とした幅広いコンテンツをご用意しております。
お問い合わせ
コストダウンが利益に直結する術だと理解していても、なかなか前に進めることができない状況。そんな時は、newjiのコストダウン自動化機能で大きく利益貢献しよう!
(Β版非公開)