- お役立ち記事
- Impact of Automation on Employees in Semiconductor Manufacturing
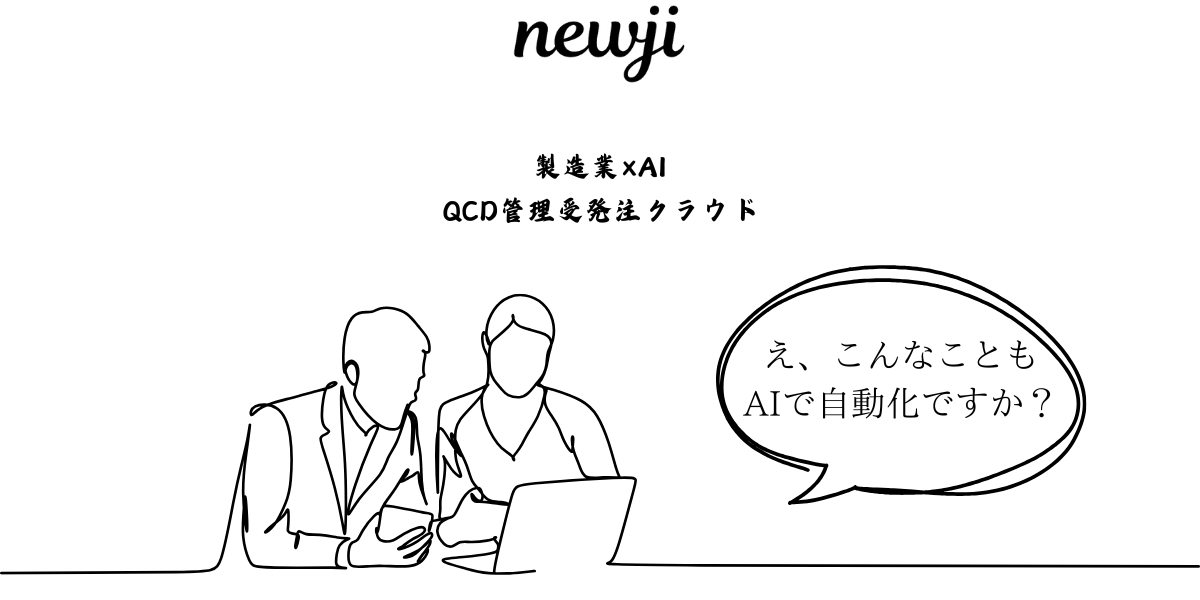
Impact of Automation on Employees in Semiconductor Manufacturing
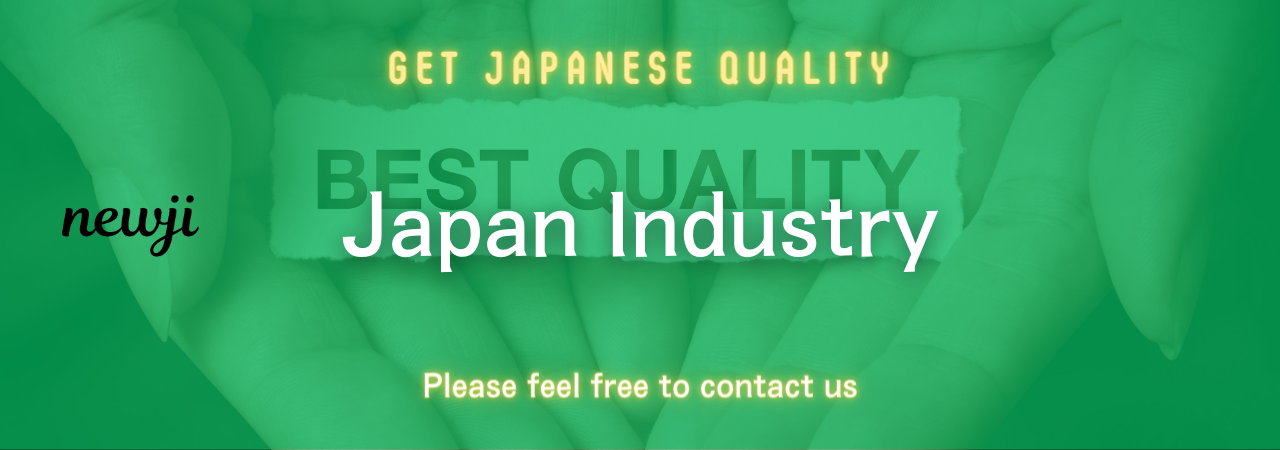
目次
Understanding Automation in Semiconductor Manufacturing
Automation in semiconductor manufacturing refers to the use of advanced technologies, like robotics and intelligent systems, to perform tasks traditionally carried out by human workers.
These tasks range from material handling and quality control to intricate assembly processes.
The goal of automation is to boost productivity, enhance precision, and reduce production costs.
By embracing automation, semiconductor manufacturers can produce more chips with higher consistency and efficiency.
While this technological advancement brings significant benefits, it also presents challenges and implications for the workforce involved.
Positive Impacts of Automation on Employees
Skill Enhancement and Upskilling
Automation can provide employees with opportunities for skill enhancement and upskilling.
As machines take over repetitive and mundane tasks, workers can focus on developing new skills that require human intervention, like problem-solving and decision-making.
Companies often invest in training programs to equip employees with the knowledge needed to work alongside automated systems effectively.
This continuous learning approach not only benefits the employees by making them more valuable but also benefits the company by retaining a skilled workforce.
Increased Safety and Reduced Physical Work
In semiconductor manufacturing, certain tasks can be physically demanding and, at times, hazardous.
Automation helps in mitigating these risks by replacing human intervention in potentially dangerous processes.
For example, robots can handle hazardous materials or perform high-precision work without exposing employees to risks.
This shift not only enhances workplace safety but also reduces the physical strain on workers, leading to a healthier work environment.
Job Satisfaction and Creativity
With automation taking care of repetitive tasks, employees can engage in more meaningful and fulfilling work.
This change allows workers to focus on tasks that require creativity, critical thinking, and innovation.
Such engagement can lead to higher job satisfaction as employees feel their contributions have a tangible impact on the company’s success.
Involving employees in innovative projects can also foster a sense of ownership and pride in their work, further boosting morale.
Challenges and Concerns of Automation
Job Displacement and Unemployment
One of the most significant concerns about automation is the potential displacement of jobs.
As machines and intelligent systems become more capable, there’s a risk that certain roles may become redundant.
This scenario can lead to unemployment or force employees to shift careers, necessitating retraining and adaptation.
While some positions might become obsolete, new opportunities may emerge that require different skill sets.
Navigating this transition can be challenging for both employees and employers.
Skills Gap and Inequality
The rapid pace of technological advancement can create a skills gap where the demand for new skills outpaces the supply.
Employees who cannot quickly adapt or acquire these new skills may find themselves at a disadvantage in the job market.
This situation can lead to inequality, where only those who can access and afford continuous learning and training opportunities can thrive.
Employers must ensure that support measures are in place to help all workers transition smoothly into the new automated environment.
Resistance to Change
Whenever significant changes occur in a workplace, there is always the potential for resistance from employees.
Automation can create anxiety and fear among workers who are concerned about job security and changes to their roles.
Such resistance can hinder the successful implementation of automation.
For companies to overcome this challenge, it’s crucial to communicate effectively with employees, addressing concerns and highlighting the positive impacts automation can bring to their work lives.
The Future of Semiconductor Manufacturing Workforce
Collaborative Robots (Cobots)
The future might not see robots completely taking over human roles but rather collaborating with them.
Collaborative robots, or cobots, are designed to work alongside humans, enhancing productivity without completely replacing human labor.
Cobots can perform specialized tasks while humans focus on strategic and complex aspects of manufacturing.
Employees in semiconductor manufacturing may find that their roles evolve to become more supervisory and strategic, overseeing and programming these cobots.
Focus on Soft Skills
As automation handles technical and repetitive tasks, the importance of soft skills grows in the workforce.
Skills such as communication, empathy, teamwork, and critical thinking will be pivotal for success in the automated work environment.
Employees will need to harness these skills to work effectively with other team members and adapt to continuously changing technological advancements.
Employers will prioritize these attributes when looking for new hires, highlighting the dynamic nature of future job requirements.
Continued Need for Human Expertise
Despite the rise in automation, human expertise will remain indispensable in semiconductor manufacturing.
There will always be a need for employees to design, develop, and maintain automation systems.
Human insight is crucial in decision-making processes, particularly in areas where creativity and bespoke solutions are required.
Thus, while machines perform specific tasks, humans will continue to play a vital role in driving innovation and steering companies towards new objectives.
Conclusion
Automation in semiconductor manufacturing presents both opportunities and challenges for employees.
While it can enhance skill sets, increase safety, and improve overall job satisfaction, it also poses risks regarding job displacement and skill gaps.
By embracing the potential benefits and addressing concerns head-on, the industry can strike a balance where technology and human expertise coexist harmoniously.
As the sector evolves, continuous learning and adaptability will be key for employees to thrive in this rapidly changing landscape.
資料ダウンロード
QCD調達購買管理クラウド「newji」は、調達購買部門で必要なQCD管理全てを備えた、現場特化型兼クラウド型の今世紀最高の購買管理システムとなります。
ユーザー登録
調達購買業務の効率化だけでなく、システムを導入することで、コスト削減や製品・資材のステータス可視化のほか、属人化していた購買情報の共有化による内部不正防止や統制にも役立ちます。
NEWJI DX
製造業に特化したデジタルトランスフォーメーション(DX)の実現を目指す請負開発型のコンサルティングサービスです。AI、iPaaS、および先端の技術を駆使して、製造プロセスの効率化、業務効率化、チームワーク強化、コスト削減、品質向上を実現します。このサービスは、製造業の課題を深く理解し、それに対する最適なデジタルソリューションを提供することで、企業が持続的な成長とイノベーションを達成できるようサポートします。
オンライン講座
製造業、主に購買・調達部門にお勤めの方々に向けた情報を配信しております。
新任の方やベテランの方、管理職を対象とした幅広いコンテンツをご用意しております。
お問い合わせ
コストダウンが利益に直結する術だと理解していても、なかなか前に進めることができない状況。そんな時は、newjiのコストダウン自動化機能で大きく利益貢献しよう!
(Β版非公開)