- お役立ち記事
- Differences Between Impact Extrusion and Cold Extrusion
Differences Between Impact Extrusion and Cold Extrusion
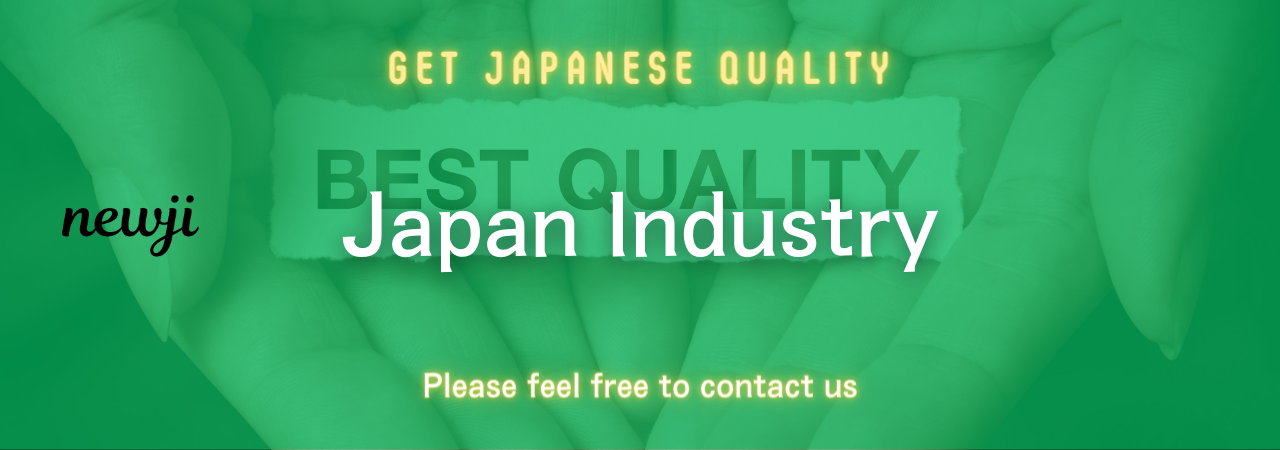
目次
Understanding Impact Extrusion
Impact extrusion is a metal forming process that uses high-speed force to shape metals.
This method is primarily used for shaping softer metals such as aluminum, tin, and lead.
In an impact extrusion process, a metal slug is placed in a die, and a powerful press rapidly forces a punch into the slug.
The great impact causes the metal to flow around the punch and take the shape of the die cavity.
This process is often used to manufacture cans, tubes, and other hollow objects.
One of the main benefits of impact extrusion is its ability to produce components with complex shapes and high precision.
Additionally, because the process can be done at room temperature, it preserves the material’s properties and can be more environmentally friendly than other manufacturing processes that require heating.
Exploring Cold Extrusion
Cold extrusion, on the other hand, works at room or slightly elevated temperatures.
It is commonly applied to metals like steel, aluminum, copper, and their alloys.
In cold extrusion, a round billet is placed in a closed cavity and pushed through a die opening by a punch.
Unlike impact extrusion, which relies on high-speed force, cold extrusion generally uses slower, consistent pressure.
Cold extrusion is widely used for producing high-strength parts such as automotive components, fasteners, and machinery parts.
One of its advantages is the improved mechanical properties of the extruded parts, often resulting in stronger and more durable products due to the work hardening of the metal.
Additionally, it offers high precision and produces minimal waste, making it a cost-effective option for large-scale production.
Key Differences Between the Processes
While both impact and cold extrusion techniques are valuable for shaping metals, they have significant differences that affect their applications and outcomes.
1. Speed and Force
One of the primary differences is the speed and force used in the processes.
Impact extrusion relies on high-speed force, making it suitable for quick fabrication of softer metals.
Cold extrusion, however, utilizes slower, steady pressure, which is ideal for metals requiring more shaping control and strength enhancement.
2. Temperature Considerations
Temperature is a crucial distinguishing factor between the two.
Impact extrusion often occurs at room temperature, but the metal may be softer, so heat isn’t typically needed.
Cold extrusion can also take place at room temperature but may sometimes require slight heating to aid the metal’s ductility and flow.
3. Material Suitability
Both processes can handle different materials, but their efficiency varies with metal types.
Impact extrusion works best with metals like aluminum and lead, while cold extrusion is favorable for tougher materials like steel.
4. Product Complexity and Precision
Impact extrusion is excellent for producing complex and intricate shapes quickly due to its high-speed impact.
Cold extrusion, though sometimes slower, can achieve tighter tolerances and superior precision, especially for parts that require high strength and durability.
Applications and Uses
Each method of extrusion serves specific industries based on the nature of the components needed.
Impact Extrusion Applications
Impact extrusion is predominantly used in the manufacturing of:
– Beverage cans, due to the ability to produce thin walls quickly and efficiently.
– Cosmetic containers, where precision and a high-quality finish are required.
– Tubes and other hollow shapes for industries needing lightweight and shaped components.
Cold Extrusion Applications
Cold extrusion is favored in industries focusing on strength and reliability, including:
– Automotive parts, such as gears, axles, and structural components, necessitating high durability and precision.
– Medical devices, where stringent tolerances and material integrity are critical.
– Aerospace components that benefit from the enhanced strength and structural integrity.
Choosing the Right Process
When deciding between impact and cold extrusion, manufacturers need to consider several factors, including:
– The type of metal being used: Softer metals may be better suited to impact extrusion, while harder metals find more applicability in cold extrusion methods.
– Desired product characteristics: If the end product requires high strength and durability, cold extrusion might be the better choice.
– Production scale and efficiency: Impact extrusion could be more cost-effective for large-scale production due to its speed, whereas cold extrusion might suit small to medium batches where precision is paramount.
Understanding the differences between impact and cold extrusion can help industries make informed decisions about which method is best suited for their specific manufacturing needs.
資料ダウンロード
QCD調達購買管理クラウド「newji」は、調達購買部門で必要なQCD管理全てを備えた、現場特化型兼クラウド型の今世紀最高の購買管理システムとなります。
ユーザー登録
調達購買業務の効率化だけでなく、システムを導入することで、コスト削減や製品・資材のステータス可視化のほか、属人化していた購買情報の共有化による内部不正防止や統制にも役立ちます。
NEWJI DX
製造業に特化したデジタルトランスフォーメーション(DX)の実現を目指す請負開発型のコンサルティングサービスです。AI、iPaaS、および先端の技術を駆使して、製造プロセスの効率化、業務効率化、チームワーク強化、コスト削減、品質向上を実現します。このサービスは、製造業の課題を深く理解し、それに対する最適なデジタルソリューションを提供することで、企業が持続的な成長とイノベーションを達成できるようサポートします。
オンライン講座
製造業、主に購買・調達部門にお勤めの方々に向けた情報を配信しております。
新任の方やベテランの方、管理職を対象とした幅広いコンテンツをご用意しております。
お問い合わせ
コストダウンが利益に直結する術だと理解していても、なかなか前に進めることができない状況。そんな時は、newjiのコストダウン自動化機能で大きく利益貢献しよう!
(Β版非公開)