- お役立ち記事
- Differences Between PLC and DCS
Differences Between PLC and DCS
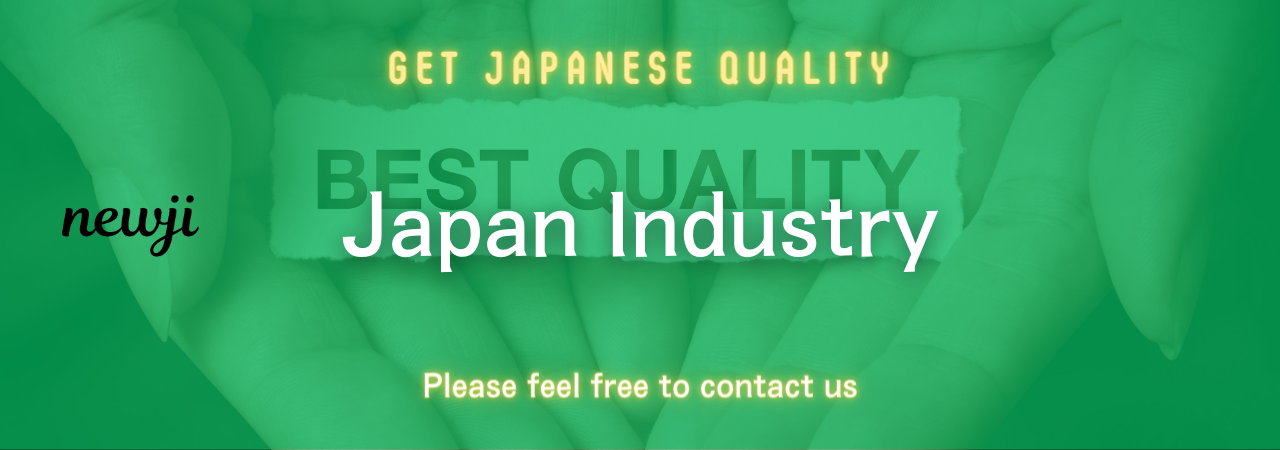
目次
Understanding PLC and DCS
When delving into the world of industrial automation, two common terms arise: PLC and DCS.
Both serve critical roles in controlling processes, yet they do so in different ways.
To understand these differences, it’s important first to grasp what PLC and DCS are.
What is a PLC?
A Programmable Logic Controller, or PLC, is a type of computer specifically designed to manage and control manufacturing processes.
PLCs are highly reliable and capable of operating in industrial environments.
They are frequently used for controlling machinery on factory assembly lines, amusement rides, or lighting fixtures.
Typically, a PLC is tasked with a particular operation or process.
It is known for its high-speed operation and the ability to handle numerous I/O (input/output) operations efficiently.
Due to their robust nature, PLCs are suited for environments where conditions might be less than ideal, such as extreme temperatures or dusty settings.
What is a DCS?
A Distributed Control System, or DCS, manages processes that are distributed throughout large plants.
DCSs are often used in industries like oil and gas, chemical plants, and paper manufacturing.
The focus of a DCS is on controlling processes rather than specific pieces of machinery.
DCS systems monitor and control through a distributed setup, which means they manage numerous integrated subsystems whereas PLCs tend to handle more isolated tasks.
In essence, a DCS provides broader control over entire plant processes, enabling efficient management over sprawling industrial operations.
Key Differences Between PLC and DCS
The primary differences between PLC and DCS arise from their core functionalities and applications in industrial settings.
Design and Structure
PLCs are designed to handle specific tasks and are typically modular in nature.
They are built with flexibility in mind, allowing users to add or remove modules as needed.
This design makes PLCs adaptable to varying control applications.
In contrast, a DCS is usually supplied as a complete system that integrates with the plant’s entire control infrastructure.
DCSs are built to handle complex large-scale processes, offering a centralized solution that includes hardware, configuration tools, and operator interfaces.
Application and Use Case
PLCs are commonly used in discrete manufacturing industries where the production process can be broken down into smaller tasks.
For example, automotive assembly lines, packaging systems, and even roller coaster operations can each be individually managed by PLCs.
A DCS, however, is used in process-based industries where the focus is on managing continuous production flows or mixtures.
Refineries, water treatment plants, and chemical processing plants benefit from the complex, integrated control provided by a DCS.
Scalability and Flexibility
One of the standout features of PLCs is their scalability.
As industries grow and change, PLC systems can be easily expanded.
New modules or controllers can be added without substantial changes to the existing systems, offering a high degree of flexibility.
While scalable, a DCS is generally more suited to large, stable processes where changes occur less frequently.
Its system is designed to be robust and integrated, which can limit the ease of scalability compared to discrete and flexible PLC setups.
Response Time
PLCs are known for fast response times.
They react rapidly to input changes, making them ideal for time-sensitive applications.
On the other hand, DCS systems are not typically designed for high-speed operations but excel in monitoring and controlling large volumes of data over distributed systems.
Their response time is adequate for the continuous control and monitoring tasks required in process industries.
Advantages and Disadvantages
Advantages of PLC
1. **Reliability and Durability**: PLCs are designed to withstand harsh industrial environments.
2. **Cost-Effective**: Generally cheaper for smaller applications.
3. **Flexibility**: Easy to reprogram, allowing for flexible operations.
Disadvantages of PLC
1. **Limited Complex Control**: Not ideal for large-scale processes.
2. **Integration Challenges**: Can be harder to integrate into wider systems compared to a DCS.
Advantages of DCS
1. **Comprehensive Control**: Ideal for large and complex process systems.
2. **Centralized Monitoring**: Offers integrated and comprehensive monitoring and control.
3. **Higher Security**: Enhanced safety features and operation control.
Disadvantages of DCS
1. **Higher Cost**: Generally more expensive to implement and maintain than PLCs.
2. **Less flexible**: Not as adaptable to rapid changes compared to PLC systems.
Choosing Between PLC and DCS
When it comes to selecting between a PLC and a DCS, the decision largely depends on specific requirements and industry needs.
For small-scale or discrete tasks requiring high speed and flexibility, a PLC system may be more appropriate.
Conversely, if the goal is to manage an entire production process, especially one involving continuous data flow or distribution over wide areas, a DCS can offer significant advantages with its comprehensive control capabilities.
Both types of systems have proven their worth in industrial automation, and understanding their relative merits can guide industries in optimizing their operations and achieving their production goals efficiently.
資料ダウンロード
QCD調達購買管理クラウド「newji」は、調達購買部門で必要なQCD管理全てを備えた、現場特化型兼クラウド型の今世紀最高の購買管理システムとなります。
ユーザー登録
調達購買業務の効率化だけでなく、システムを導入することで、コスト削減や製品・資材のステータス可視化のほか、属人化していた購買情報の共有化による内部不正防止や統制にも役立ちます。
NEWJI DX
製造業に特化したデジタルトランスフォーメーション(DX)の実現を目指す請負開発型のコンサルティングサービスです。AI、iPaaS、および先端の技術を駆使して、製造プロセスの効率化、業務効率化、チームワーク強化、コスト削減、品質向上を実現します。このサービスは、製造業の課題を深く理解し、それに対する最適なデジタルソリューションを提供することで、企業が持続的な成長とイノベーションを達成できるようサポートします。
オンライン講座
製造業、主に購買・調達部門にお勤めの方々に向けた情報を配信しております。
新任の方やベテランの方、管理職を対象とした幅広いコンテンツをご用意しております。
お問い合わせ
コストダウンが利益に直結する術だと理解していても、なかなか前に進めることができない状況。そんな時は、newjiのコストダウン自動化機能で大きく利益貢献しよう!
(Β版非公開)