- お役立ち記事
- Differences Between Surface Grinding and End Grinding
Differences Between Surface Grinding and End Grinding
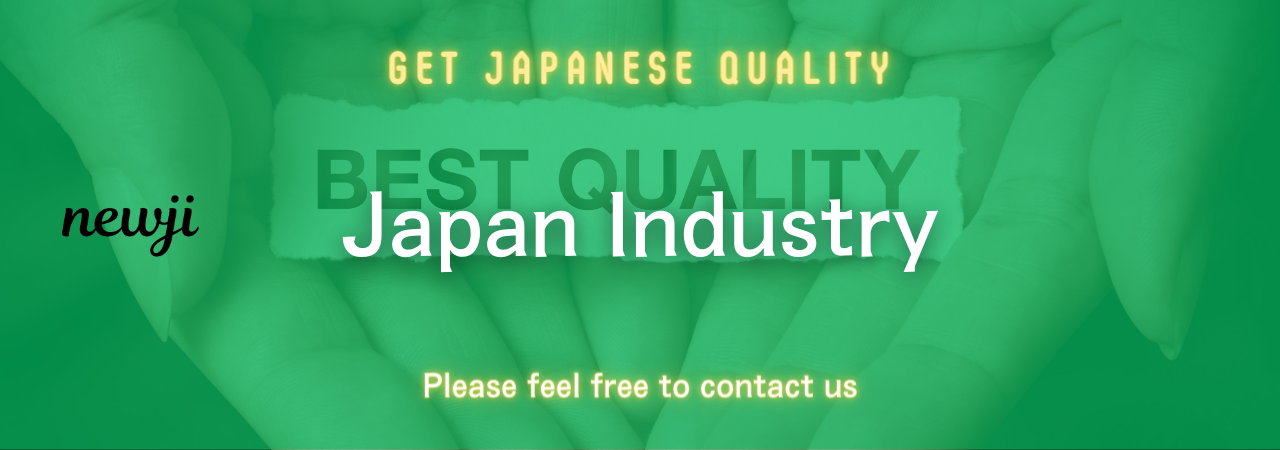
目次
Understanding Surface Grinding
Surface grinding is a machining process that involves removing material from the surface of a workpiece to create a smooth, flat surface.
This technique is commonly used in manufacturing to provide precision and accuracy in the finishing of components.
A surface grinder utilizes a rotating abrasive wheel to remove material layer by layer.
The grinding wheel’s movement is typically back-and-forth, helping to achieve the desired surface finish.
Operators often use surface grinding for creating precise flat surfaces on metal parts, molds, and dies.
One of the most significant advantages of surface grinding is its ability to produce surfaces with very tight tolerances and a high level of precision.
This is crucial in industries such as automotive, aerospace, and engineering, where precision components are essential.
Different types of grinding wheels can be employed during surface grinding, each with specific characteristics suited for particular tasks.
Key Features of Surface Grinding
– **Precision:** Surface grinding offers excellent accuracy and the ability to produce very smooth surfaces.
– **Versatility:** It can handle a wide range of materials, including metals, plastics, and ceramics.
– **Ideal for Large Workpieces:** Surface grinding works well with large, flat surfaces.
– **Different Grinding Wheels:** Various types of wheels for specific grinding applications.
Exploring End Grinding
End grinding, on the other hand, is a different machining process that focuses on grinding the ends of workpieces.
This process is primarily used for creating flat or contoured surfaces at the end of a part.
End grinding is often achieved using an end grinder, which typically features a spindle-driven grinding wheel.
This wheel grinds the end of the workpiece either by rotating it or by rotating the workpiece itself against a stationary wheel.
End grinding is particularly useful in situations where you need to refine the ends of rods, bolts, or similar components.
This method helps achieve accurate measurements and finishes on the ends of these products.
It is frequently used in applications where the ends of parts must meet strict specifications in terms of shape, smoothness, and angle.
Key Features of End Grinding
– **Focus on Ends:** Specifically targets the ends of components for precise finishing.
– **Angular Grinding Capability:** Can create angled surfaces on the ends of parts.
– **Useful for Precision Parts:** Ideal for machining ends that require high tolerance levels.
– **Variety of Grinders Available:** End grinders can vary based on the specific task at hand, with options for manual, automated, or CNC machines.
Comparing Surface Grinding and End Grinding
Both surface and end grinding serve essential roles in manufacturing and engineering, but they are used in different scenarios based on the task requirements.
Here are some distinct differences between the two:
– **Purpose:** Surface grinding is about refining the entire surface of a component; end grinding is specifically for finishing component ends.
– **Equipment Used:** Surface grinders tend to have larger, flat grinding surfaces, while end grinders can be smaller and designed for specific end shapes.
– **Applications:** Surface grinding is typically used for flat surfaces, whereas end grinding is applied to cylindrical items, rods, or other shaped parts that need end finishing.
– **Precision Requirements:** Both processes offer high levels of precision; however, surface grinding is often chosen for applications demanding exceptional flatness across the whole surface.
In sum, the right choice between surface grinding and end grinding largely depends on the specific requirements of the project at hand.
Manufacturers must assess the shape, size, and desired precision level of their components to choose the appropriate grinding method.
Conclusion
Understanding the differences between surface grinding and end grinding is crucial for manufacturers seeking the best results in their machining operations.
Surface grinding is your go-to for flat surfaces requiring perfection and precision, making it a staple in various industries.
Meanwhile, end grinding serves a specific purpose, focusing on refining the ends of components to meet tight specifications.
These techniques, though distinct, are integral to achieving the necessary quality and accuracy in manufacturing, ensuring that every component performs its function seamlessly.
資料ダウンロード
QCD調達購買管理クラウド「newji」は、調達購買部門で必要なQCD管理全てを備えた、現場特化型兼クラウド型の今世紀最高の購買管理システムとなります。
ユーザー登録
調達購買業務の効率化だけでなく、システムを導入することで、コスト削減や製品・資材のステータス可視化のほか、属人化していた購買情報の共有化による内部不正防止や統制にも役立ちます。
NEWJI DX
製造業に特化したデジタルトランスフォーメーション(DX)の実現を目指す請負開発型のコンサルティングサービスです。AI、iPaaS、および先端の技術を駆使して、製造プロセスの効率化、業務効率化、チームワーク強化、コスト削減、品質向上を実現します。このサービスは、製造業の課題を深く理解し、それに対する最適なデジタルソリューションを提供することで、企業が持続的な成長とイノベーションを達成できるようサポートします。
オンライン講座
製造業、主に購買・調達部門にお勤めの方々に向けた情報を配信しております。
新任の方やベテランの方、管理職を対象とした幅広いコンテンツをご用意しております。
お問い合わせ
コストダウンが利益に直結する術だと理解していても、なかなか前に進めることができない状況。そんな時は、newjiのコストダウン自動化機能で大きく利益貢献しよう!
(Β版非公開)