- お役立ち記事
- Differences Between Procurement Costs and Manufacturing Costs
Differences Between Procurement Costs and Manufacturing Costs
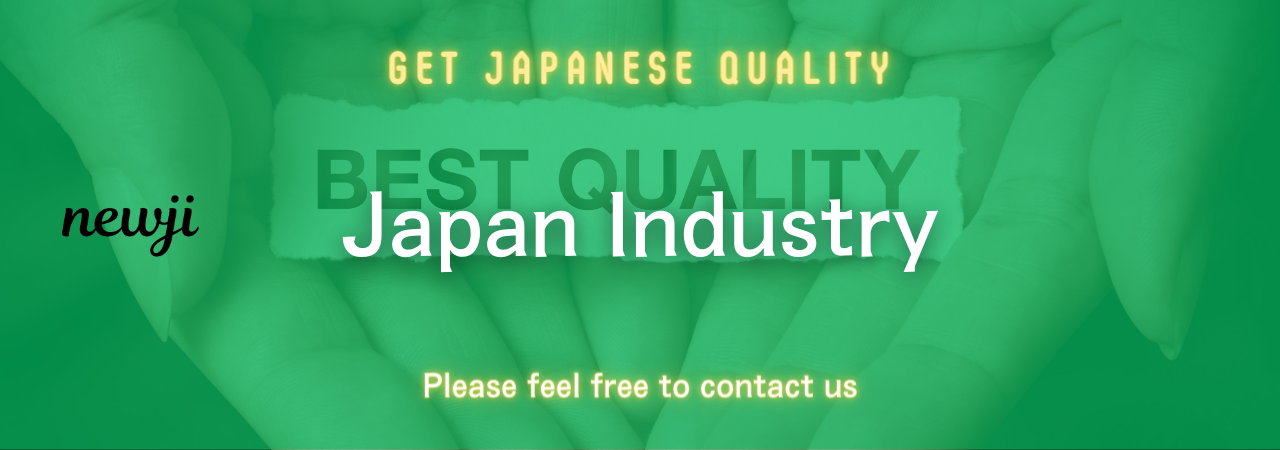
目次
Understanding Procurement Costs
Procurement costs are an essential part of any business operation, particularly for companies involved in the production and supply chain sectors.
These costs are associated with acquiring goods or services required for manufacturing products or for business operations.
The procurement process involves several components, including sourcing, purchasing, and receiving the required items.
Procurement costs comprise all expenses incurred during the acquisition of goods or services.
These costs can include direct expenses like the purchase price of raw materials, as well as indirect expenses such as shipping, handling, and taxes.
It is important for businesses to manage procurement costs efficiently to ensure profitability and maintain competitive pricing.
One critical aspect of procurement costs is that they often involve negotiations with suppliers.
Effective negotiation can help a company secure better pricing, leading to cost savings.
Moreover, building strong relationships with suppliers can result in more favorable terms and reduced procurement expenses over time.
Components of Procurement Costs
Understanding the different components of procurement costs is crucial for effective cost management.
Here are the main components:
1. **Purchase Price**: This is the amount paid to the supplier for the goods or services.
It is usually the largest component of procurement costs.
2. **Transportation Costs**: These are the expenses related to moving goods from the supplier to the company’s location.
Transportation costs can vary based on distance, method of transportation, and fuel prices.
3. **Handling and Packaging**: These costs cover the expenses of packaging, loading, and unloading the goods.
They are important for ensuring product safety during transit and storage.
4. **Taxes and Duties**: Depending on the location and nature of the goods, taxes or duties may be applicable.
These fees can significantly impact the total procurement cost.
5. **Storage Costs**: If goods need to be stored before use, there will be associated storage costs, which include warehouse rentals and maintenance expenses.
Understanding Manufacturing Costs
Manufacturing costs are the expenses incurred during the process of converting raw materials into finished goods.
These costs are a critical component of total production expenses and directly impact the profitability of a product.
Manufacturing costs are essential for determining the selling price of a product and for financial planning and analysis.
The primary goal in managing manufacturing costs is to produce products efficiently while minimizing expenses.
This involves careful planning of production processes, as well as the use of cost-effective materials and technologies.
Components of Manufacturing Costs
Manufacturing costs consist of several components, each contributing to the total cost of production:
1. **Direct Materials**: These are the raw materials that are directly used in the production of a product.
The cost of direct materials is usually a significant part of the total manufacturing cost.
2. **Direct Labor**: This includes the wages and benefits of employees who are directly involved in the production process.
Labor costs can vary depending on the skill level required and the complexity of the manufacturing process.
3. **Manufacturing Overhead**: These are the indirect costs related to production, such as utilities, depreciation on production equipment, and factory maintenance.
These expenses are necessary to keep the production process running smoothly.
4. **Quality Control**: Ensuring that products meet quality standards can incur additional costs.
This includes expenses for testing, inspection, and any necessary rework.
Key Differences Between Procurement Costs and Manufacturing Costs
While both procurement and manufacturing costs contribute to the overall cost of producing goods, they differ in several key areas:
1. **Nature of Costs**:
– Procurement costs are associated with acquiring the materials or services needed for production.
– Manufacturing costs arise from the actual process of creating the finished product.
2. **Timing**:
– Procurement costs are typically incurred before production begins, as they pertain to sourcing and acquiring necessary materials.
– Manufacturing costs occur during the production process, from the transformation of raw materials to the final product.
3. **Control and Management**:
– Procurement costs can often be managed through supplier negotiations and strategic sourcing.
– Manufacturing costs require efficient production management and process optimization to minimize expenses.
4. **Components**:
– Procurement costs largely revolve around external transactions and relationships.
– Manufacturing costs focus on internal processes and resource utilization.
The Importance of Managing Both Costs
Effective management of both procurement and manufacturing costs is crucial for a company’s profitability and competitiveness.
Businesses that excel in cost management are better equipped to offer competitive pricing, improve margins, and invest in growth opportunities.
To manage procurement costs, companies should focus on building strong supplier relationships and employing strategic sourcing techniques.
Leverage technology to streamline the procurement process and gain insights into supplier performance.
For manufacturing costs, companies should invest in efficient production processes and technologies.
Implement lean manufacturing principles to minimize waste and utilize resources effectively.
Continual improvement efforts and employee training can also help in reducing manufacturing costs.
In conclusion, understanding the differences between procurement and manufacturing costs is essential for any business aiming to optimize its production expenses.
By recognizing these differences and managing them effectively, businesses can achieve better financial performance and a stronger competitive position in the market.
資料ダウンロード
QCD調達購買管理クラウド「newji」は、調達購買部門で必要なQCD管理全てを備えた、現場特化型兼クラウド型の今世紀最高の購買管理システムとなります。
ユーザー登録
調達購買業務の効率化だけでなく、システムを導入することで、コスト削減や製品・資材のステータス可視化のほか、属人化していた購買情報の共有化による内部不正防止や統制にも役立ちます。
NEWJI DX
製造業に特化したデジタルトランスフォーメーション(DX)の実現を目指す請負開発型のコンサルティングサービスです。AI、iPaaS、および先端の技術を駆使して、製造プロセスの効率化、業務効率化、チームワーク強化、コスト削減、品質向上を実現します。このサービスは、製造業の課題を深く理解し、それに対する最適なデジタルソリューションを提供することで、企業が持続的な成長とイノベーションを達成できるようサポートします。
オンライン講座
製造業、主に購買・調達部門にお勤めの方々に向けた情報を配信しております。
新任の方やベテランの方、管理職を対象とした幅広いコンテンツをご用意しております。
お問い合わせ
コストダウンが利益に直結する術だと理解していても、なかなか前に進めることができない状況。そんな時は、newjiのコストダウン自動化機能で大きく利益貢献しよう!
(Β版非公開)