- お役立ち記事
- Tachometer Manufacturing Process and Accuracy Improvement
Tachometer Manufacturing Process and Accuracy Improvement
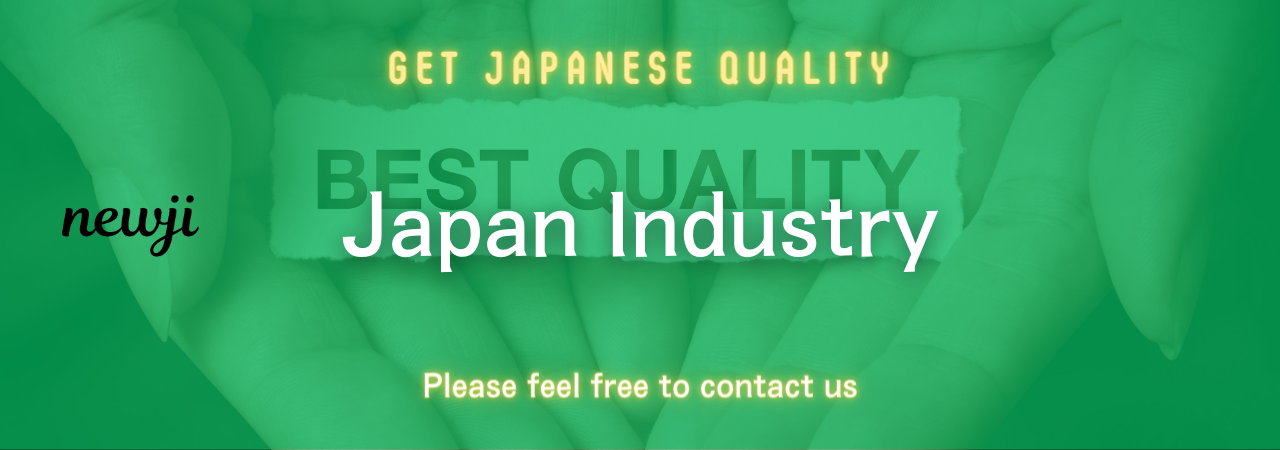
目次
Introduction to Tachometers
A tachometer is an essential instrument used to measure the rotational speed of an object, typically a shaft or disk, as in an engine or other machine.
The rotational speed is presented in revolutions per minute (RPM).
Tachometers are widely used in automotive applications to monitor engine speed, but they also find applications in other sectors such as aviation, manufacturing, and machinery.
Understanding the manufacturing process of tachometers is crucial for improving their accuracy and effectiveness.
This article sheds light on the intricate processes involved in their manufacturing and explores ways to enhance their accuracy.
The Manufacturing Process of Tachometers
Design and Material Selection
The first step in manufacturing a tachometer involves designing the device tailored to its intended application.
Engineers take into account factors like the range of speeds to be measured, the environment in which the tachometer will operate, and the power supply required.
Choosing the right materials is also crucial.
Components such as the housing, dial, and pointer are often made from durable materials like aluminum or plastic, while internal components may use more sensitive materials for accurate readings.
Component Manufacturing
Once the design is finalized, individual components of the tachometer are manufactured.
This includes mechanical, electrical, and electronic components such as sensors, display units, and casing.
Typically, the manufacturing process makes use of precision machining for mechanical parts and microfabrication techniques for electronic components.
Assembly
After manufacturing the individual components, the assembly process begins.
Precision is crucial at this stage to ensure that the components fit together perfectly.
Skilled technicians or automated assembly lines combine these components into a functional tachometer.
Each part is carefully installed to ensure minimal mechanical friction and optimal electrical connections.
Calibration
Calibration is a vital part of the manufacturing process, ensuring the tachometer’s readings are accurate.
During calibration, the device is set to measure known rotational speeds and adjusted until it provides accurate readings.
This involves both software tuning for digital tachometers and mechanical adjustments for analog models.
Calibration ensures that the tachometer consistently delivers precise measurements.
Quality Control
Quality control is a pivotal part of the tachometer manufacturing process.
Rigorous tests are conducted to ensure each unit meets performance standards.
This may involve subjecting the tachometer to various rotational speeds, environmental conditions, and wear tests.
Only those units that pass these quality checks without exception proceed to the market.
Accuracy Improvements in Tachometers
Advanced Sensors
Improving the accuracy of tachometers can be achieved by utilizing advanced sensors.
Sensors based on optical, magnetic, or laser technology can provide more precise measurements and higher resolution.
These sensors, when integrated into a tachometer, help to improve its reliability and accuracy significantly.
Digital Processing
The digital processing of the tachometer signal is another way to enhance accuracy.
Converting the analog signal to digital can greatly reduce noise and improve measurement precision.
With digital signal processing algorithms, tachometers can filter out unwanted noise and ensure that readings are stable and accurate even under challenging conditions.
Environment Adaptation
For greater accuracy, design improvements can be made to help tachometers adapt to their environment.
Ensuring that the instrument is protected from temperature fluctuations, vibrations, and moisture can result in more reliable readings.
Using sealed enclosures, vibration dampeners, and temperature-resistant materials significantly contributes to the accuracy of tachometers.
Regular Calibration
Even after manufacturing, ongoing calibration is essential to maintain the accuracy of a tachometer.
Regular calibration checks and adjustments are necessary to ensure the instrument compensates for wear or environmental effects over time.
Many modern tachometers include features that alert users when recalibration is needed, helping maintain accuracy throughout its service life.
Conclusion
The manufacturing process of tachometers is intricate and requires careful attention to detail to ensure high accuracy.
From the selection of materials to advanced calibration techniques, each step influences the overall performance of the instrument.
Adopting innovative technologies such as advanced sensors and digital processing can further improve the accuracy of tachometers.
Regular maintenance and calibration are essential for sustained accuracy.
Understanding and improving these processes benefit industries relying on precise measurements, leading to more efficient and effective operations.
資料ダウンロード
QCD調達購買管理クラウド「newji」は、調達購買部門で必要なQCD管理全てを備えた、現場特化型兼クラウド型の今世紀最高の購買管理システムとなります。
ユーザー登録
調達購買業務の効率化だけでなく、システムを導入することで、コスト削減や製品・資材のステータス可視化のほか、属人化していた購買情報の共有化による内部不正防止や統制にも役立ちます。
NEWJI DX
製造業に特化したデジタルトランスフォーメーション(DX)の実現を目指す請負開発型のコンサルティングサービスです。AI、iPaaS、および先端の技術を駆使して、製造プロセスの効率化、業務効率化、チームワーク強化、コスト削減、品質向上を実現します。このサービスは、製造業の課題を深く理解し、それに対する最適なデジタルソリューションを提供することで、企業が持続的な成長とイノベーションを達成できるようサポートします。
オンライン講座
製造業、主に購買・調達部門にお勤めの方々に向けた情報を配信しております。
新任の方やベテランの方、管理職を対象とした幅広いコンテンツをご用意しております。
お問い合わせ
コストダウンが利益に直結する術だと理解していても、なかなか前に進めることができない状況。そんな時は、newjiのコストダウン自動化機能で大きく利益貢献しよう!
(Β版非公開)