- お役立ち記事
- Differences Between Slotting and Broaching
Differences Between Slotting and Broaching
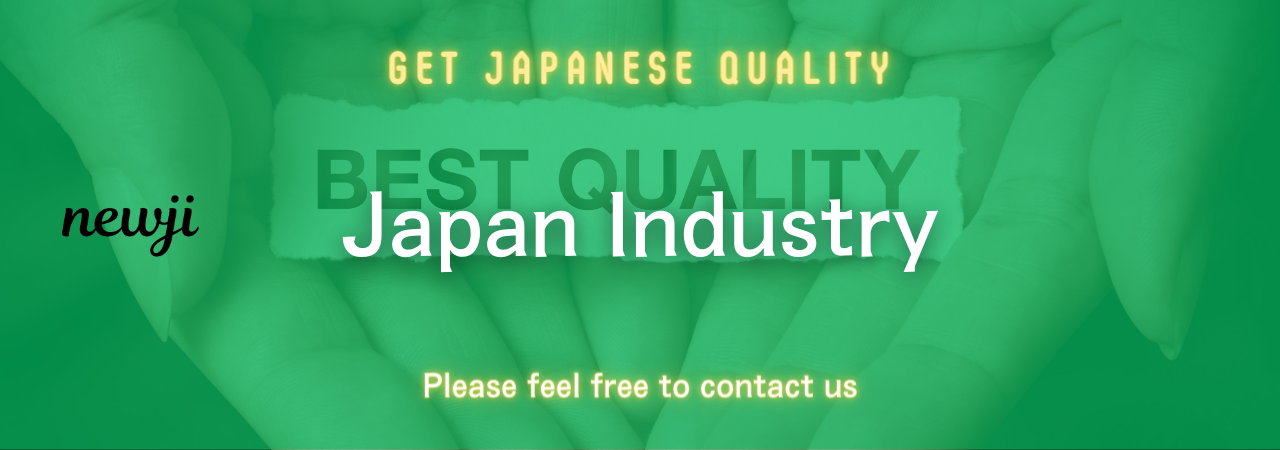
目次
Introduction to Slotting and Broaching
When it comes to machining processes, slotting and broaching are two methods that often come up in discussions for their efficiency in shaping and cutting metal parts.
Though they may seem similar, both have distinct roles and applications in the world of manufacturing.
This piece will help clarify the differences between these two machining techniques, highlighting their unique characteristics, benefits, and ideal uses.
Understanding Slotting
What is Slotting?
Slotting is a method used to create slots, grooves, or keyways on a part.
This technique is typically performed on a machine called a slotting machine or a vertical shaper.
It involves the reciprocating vertical movement of the tool, which gradually cuts into the metal workpiece.
Applications of Slotting
Slotting is particularly favored for creating keyways in gears and pulleys.
It’s also used in scenarios where vertical machining is necessary, such as in automotive and aerospace components.
Slotting is valued for its precision, making it suitable for intricate designs and detailed work.
Advantages of Slotting
One significant advantage of slotting is its ability to handle large, irregular-shaped parts.
Since the tool moves vertically, it allows for greater control over the depth and precision of the cut.
Additionally, slotting doesn’t require many tool replacements, which results in lower maintenance costs and increased efficiency in production.
Understanding Broaching
What is Broaching?
Broaching is another machining process used to remove material in a precise and efficient manner.
It employs a tool known as a broach, which is essentially a multi-tooth tool with each tooth progressing in size to slice through the material.
Broaching can be performed on both internal and external surfaces.
Applications of Broaching
Broaching is ideal for creating complex profiles and features that other machining processes might struggle with.
It is commonly used for making splines, keyways, and detailed flat surfaces.
Industries such as automotive, aerospace, and manufacturing heavily rely on broaching for parts like gears, shafts, and fasteners.
Advantages of Broaching
Broaching stands out for its speed and versatility.
Once set up, broaching can produce multiple parts quickly, making it a highly efficient process for mass production.
It also offers superior accuracy and consistency, which is crucial in achieving high-quality finishes on parts.
Key Differences Between Slotting and Broaching
Movement and Process
The main difference between slotting and broaching lies in the movement and tool design.
Slotting uses a single tool that moves in a reciprocating vertical motion, while broaching uses a tool with successive teeth that progressively cut through the material.
Tool Design
In slotting, the tool usually remains static in design, but in broaching, the broach tool is designed with a progression of teeth, each one larger than the last, enabling it to cut deeper with a single pass.
Applications and Suitability
Slotting is preferred for vertical cuts such as keyways, while broaching is better suited for complex, precise shapes, especially where mass production is required.
Slotting is often used on larger or heavier pieces due to the mechanical setup of its machines, whereas broaching can handle small to medium-sized parts more efficiently.
Choosing the Right Method
Selecting between slotting and broaching depends largely on the specific needs of the project.
If the task requires vertical slot cutting and high precision on a larger workpiece, slotting might be the best option.
On the other hand, if the job involves producing a large number of complex parts quickly, broaching offers the ideal solution.
Cost Considerations
Cost also plays an essential role in deciding between the two techniques.
Broaching tools and their setup can be more expensive initially due to the complexity of the tools.
However, they can offer cost efficiency in large production runs due to their speed and reduced cycle times.
Slotting might present lower initial costs but can accumulate operating expenses if the project demands frequent adjustments or tool changes.
Conclusion
Understanding the differences between slotting and broaching can significantly impact the efficiency and quality of machining projects.
Both have their unique strengths and applications, and the choice between them should be guided by the specifics of the task, including the material requirements, desired precision, budget, and production volume.
By weighing these factors carefully, manufacturers can optimize their processes and achieve the best results for their production lines.
資料ダウンロード
QCD調達購買管理クラウド「newji」は、調達購買部門で必要なQCD管理全てを備えた、現場特化型兼クラウド型の今世紀最高の購買管理システムとなります。
ユーザー登録
調達購買業務の効率化だけでなく、システムを導入することで、コスト削減や製品・資材のステータス可視化のほか、属人化していた購買情報の共有化による内部不正防止や統制にも役立ちます。
NEWJI DX
製造業に特化したデジタルトランスフォーメーション(DX)の実現を目指す請負開発型のコンサルティングサービスです。AI、iPaaS、および先端の技術を駆使して、製造プロセスの効率化、業務効率化、チームワーク強化、コスト削減、品質向上を実現します。このサービスは、製造業の課題を深く理解し、それに対する最適なデジタルソリューションを提供することで、企業が持続的な成長とイノベーションを達成できるようサポートします。
オンライン講座
製造業、主に購買・調達部門にお勤めの方々に向けた情報を配信しております。
新任の方やベテランの方、管理職を対象とした幅広いコンテンツをご用意しております。
お問い合わせ
コストダウンが利益に直結する術だと理解していても、なかなか前に進めることができない状況。そんな時は、newjiのコストダウン自動化機能で大きく利益貢献しよう!
(Β版非公開)