- お役立ち記事
- Differences Between Material Management and Parts Management
Differences Between Material Management and Parts Management
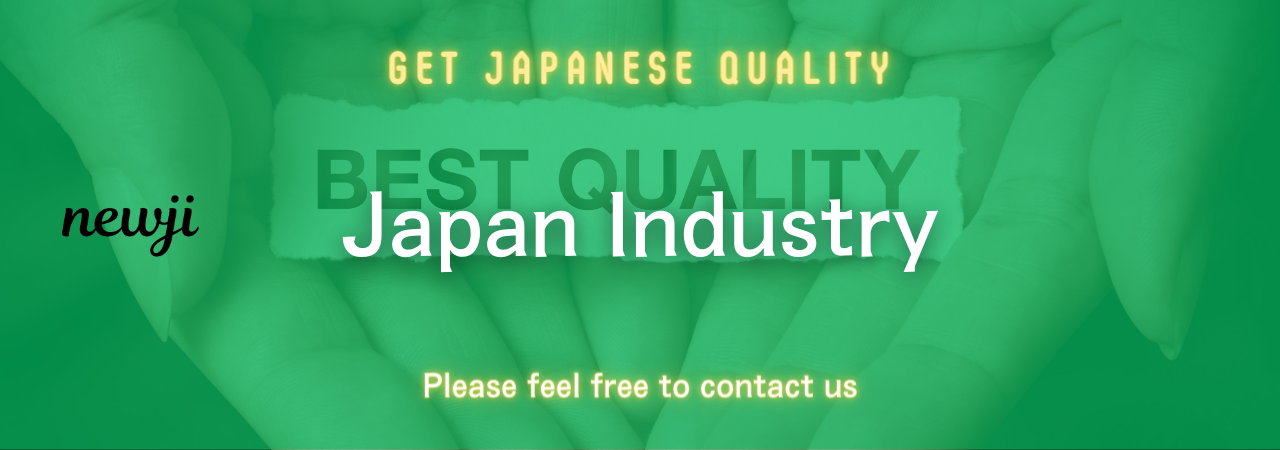
目次
Understanding Material Management
Material management plays a crucial role in any manufacturing or construction industry.
It involves planning, sourcing, and coordinating materials required for production processes.
The goal of material management is to ensure that the right quantity and quality of materials are available at the right time.
This not only helps in maintaining the production schedules but also minimizes costs associated with storage and waste.
Material management includes activities such as purchasing, inventory control, quality control, and logistics.
Each of these activities requires precise planning and strong coordination among different departments.
Purchasing involves finding reliable suppliers and negotiating contracts to acquire materials at competitive prices.
Inventory control, on the other hand, deals with maintaining an optimum level of stock, ensuring neither excess nor shortage of materials.
Quality control ensures that the materials procured meet the required standards and specifications.
Logistics involves the efficient movement of materials from the supplier to the storage areas or production floor.
Effective material management leads to smooth operations and increased profitability for a business.
Key Components of Material Management
There are several key components to consider in material management:
1. **Procurement**: This deals with the selection of suppliers and the purchase of raw materials. Efficient procurement strategies lead to cost savings and enhanced supplier relationships.
2. **Inventory Management**: It involves maintaining optimal inventory levels to meet production needs without incurring excessive carrying costs.
3. **Quality Assurance**: Ensuring the materials meet specific quality requirements to produce the best possible product.
4. **Logistics and Supply Chain**: Coordinates the transportation and storage of materials, ensuring timely delivery to avoid production delays.
Exploring Parts Management
Parts management, while similar to material management, focuses specifically on the various components and spare parts used in production industries.
This particular management discipline is vital in sectors like automotive, aerospace, and electronics, where numerous parts need to be managed efficiently.
The core objective of parts management is to ensure the availability of parts when needed, reducing downtime caused by a lack of essential components.
Parts management entails categorizing and keeping track of numerous parts, each with its unique identification numbers and specifications.
It involves tracking parts from procurement to usage, ensuring that they are stored correctly and easily accessible when needed.
Moreover, it includes the management of both new and reusable parts.
Maintaining a balance in parts inventory is crucial – having too many spare parts can lead to increased costs, while too few can cause production halts.
Key Elements of Parts Management
The effectiveness of parts management depends on several key elements:
1. **Classification and Cataloging**: Properly categorizing parts to facilitate easy identification and retrieval.
2. **Inventory Control**: Managing stock levels to ensure that inventory is neither excessive nor insufficient.
3. **Lifecycle Management**: Tracking the usage and wear of parts to determine when replacements or maintenance are necessary.
4. **Forecasting Demand**: Using historical data and predictive analytics to anticipate future needs for parts.
Key Differences Between Material Management and Parts Management
While material management and parts management share some similarities, there are several differences worth noting:
1. **Scope**: Material management deals with the entire range of materials used in production, including raw materials and consumables. Parts management focuses solely on components and spare parts.
2. **Functionality**: Material management emphasizes the procurement and flow of raw materials, while parts management focuses on the availability and management of specific parts for assembly or maintenance.
3. **Complexity**: Parts management often deals with a higher level of complexity as it involves managing numerous discrete parts, each with unique attributes and needs.
4. **Focus**: The primary focus of material management is to ensure timely availability and optimal use of materials, whereas parts management focuses more on minimizing downtime and maximizing equipment uptime by having the right parts available.
The Impact of Technology on Management Practices
Technology has significantly enhanced both material and parts management practices.
Automation and software tools assist in streamlining processes, reducing errors, and improving efficiency.
For instance, Enterprise Resource Planning (ERP) systems allow companies to integrate both material and parts management functions, providing real-time data and reporting capabilities.
With technology, businesses can automate inventory tracking, manage supplier relationships, and forecast material or parts needs more accurately.
Furthermore, digital twins and AI-driven predictive analytics help in anticipating demands and optimizing stock levels to avoid shortages or overstock situations.
These technological advancements enable businesses to respond more swiftly to changes in demand, improving overall operational effectiveness.
In conclusion, understanding the differences between material management and parts management is crucial for enhancing operational efficiency and achieving business success.
Each type of management has its unique focus and challenges, but when both are executed correctly and with the aid of modern technology, they can contribute significantly to a company’s efficiency and profitability.
資料ダウンロード
QCD調達購買管理クラウド「newji」は、調達購買部門で必要なQCD管理全てを備えた、現場特化型兼クラウド型の今世紀最高の購買管理システムとなります。
ユーザー登録
調達購買業務の効率化だけでなく、システムを導入することで、コスト削減や製品・資材のステータス可視化のほか、属人化していた購買情報の共有化による内部不正防止や統制にも役立ちます。
NEWJI DX
製造業に特化したデジタルトランスフォーメーション(DX)の実現を目指す請負開発型のコンサルティングサービスです。AI、iPaaS、および先端の技術を駆使して、製造プロセスの効率化、業務効率化、チームワーク強化、コスト削減、品質向上を実現します。このサービスは、製造業の課題を深く理解し、それに対する最適なデジタルソリューションを提供することで、企業が持続的な成長とイノベーションを達成できるようサポートします。
オンライン講座
製造業、主に購買・調達部門にお勤めの方々に向けた情報を配信しております。
新任の方やベテランの方、管理職を対象とした幅広いコンテンツをご用意しております。
お問い合わせ
コストダウンが利益に直結する術だと理解していても、なかなか前に進めることができない状況。そんな時は、newjiのコストダウン自動化機能で大きく利益貢献しよう!
(Β版非公開)