- お役立ち記事
- Revolutionizing Precision: How Japan’s Multi-Measurement Devices are Transforming Manufacturing
Revolutionizing Precision: How Japan’s Multi-Measurement Devices are Transforming Manufacturing
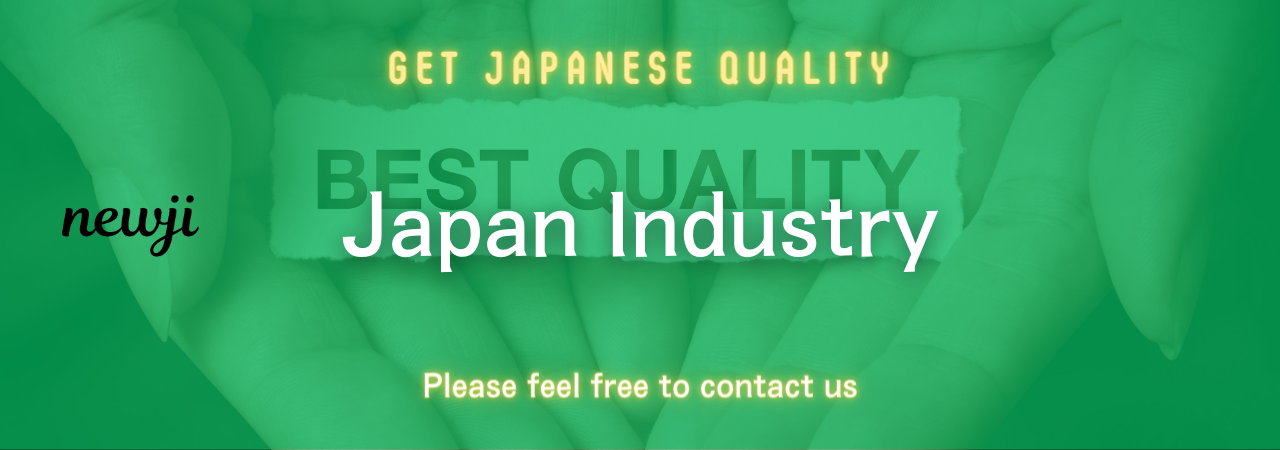
目次
Introduction
Japan has long been acclaimed for its cutting-edge technology and precision engineering, with its manufacturing industry leading the way in innovation and quality.
One of the key developments driving this reputation is the introduction of multi-measurement devices.
These devices, characterized by their high accuracy and versatility, are revolutionizing precision measurement in various manufacturing sectors.
As someone deeply immersed in the world of procurement and purchasing, it’s essential to understand how Japan’s multi-measurement devices are transforming manufacturing processes, the advantages and disadvantages they present, as well as the best practices for sourcing these innovative tools.
The Basics of Multi-Measurement Devices
Multi-measurement devices, also known as multi-sensors, integrate multiple measurement technologies into a single system.
This capability enables manufacturers to conduct a variety of measurements—such as dimensional, optical, and tactile—in one seamless operation.
Such precision is particularly valuable in industries where tight tolerances and consistent quality assurance are crucial.
Advantages of Multi-Measurement Devices
The primary advantage of multi-measurement devices is their ability to streamline measurement processes while maintaining exceptional accuracy and reliability.
By consolidating different measurement functions into one apparatus, these devices eliminate the need for multiple, separate tools.
This integration results in significant time savings, reduced risk of human error, and lower costs associated with equipment maintenance and calibration.
Furthermore, these devices often come equipped with advanced software that enhances data collection and analysis, allowing manufacturers to gather more detailed insights into their production processes.
Such insights are crucial for improving quality control, enhancing production efficiency, and ultimately boosting competitiveness in the global market.
Disadvantages and Challenges
Despite their many benefits, multi-measurement devices are not without challenges.
The high initial cost of investment can be a barrier for small and medium-sized enterprises, which may struggle to justify the expense.
Additionally, the complexity of these devices requires skilled operators who are trained to utilize sophisticated software and interpret complex data outputs accurately.
Another consideration is the compatibility of new devices with existing systems.
Integrating a sophisticated multi-measurement device into a legacy manufacturing setup can be challenging, requiring significant time and resources to ensure seamless operation.
Market Conditions and Trends
The market for multi-measurement devices is robust and growing, primarily driven by the increasing demand for precision in manufacturing coupled with the advancement of Industry 4.0 technologies.
Japan, as a leader in this field, is at the forefront of research and development, setting trends in the integration of artificial intelligence and machine learning with measurement technologies.
Manufacturers worldwide are placing a higher emphasis on automation, data accuracy, and process efficiency.
This trend is pushing the multi-measurement device market toward more intelligent systems that not only measure with unprecedented precision but also predict potential issues and self-correct in real time.
Innovations in Japanese Multi-Measurement Devices
Japanese manufacturers are renowned for their commitment to quality, and this ethos is evident in the innovation of multi-measurement devices.
These devices reflect the country’s cutting-edge capabilities in miniaturization, optical technology, and sensor integration.
Recent innovations include the development of compact, portable devices that offer similar functionalities to larger, more cumbersome machines.
Additionally, Japan’s focus on sustainable manufacturing practices is leading to the creation of eco-friendly devices designed to minimize waste and energy consumption.
Best Practices for Sourcing from Japan
When considering sourcing multi-measurement devices from Japan, leveraging a strategic approach is essential.
This involves understanding the nuances of the Japanese business culture, effective negotiation techniques, and the critical evaluation of supplier capabilities.
Understanding Japanese Business Culture
Japanese business culture prioritizes relationship-building and trust.
Establishing long-term relationships with suppliers can offer significant strategic advantages, such as better communication, more favorable terms, and a deeper understanding of product offerings.
Decision-making processes can be deliberate and thorough, often requiring patience and persistence.
Understanding these cultural norms can facilitate smoother transactions and more effective relationships.
Supplier Negotiation Techniques
When negotiating with Japanese suppliers, it’s beneficial to prepare thoroughly, demonstrating a clear knowledge of your needs and an understanding of the supplier’s capabilities.
Approach negotiations with respect and attention to detail, presenting requests and queries clearly and concisely.
Emphasizing a mutual benefit approach, where both parties understand their roles in achieving a successful outcome, can be more rewarding than a purely transactional negotiation.
Flexibility and compromise can lead to favorable outcomes and a stronger business relationship.
Evaluating Supplier Capabilities
A critical aspect of sourcing is comprehensively assessing supplier capabilities.
This includes evaluating technical expertise, production capacity, and quality assurance processes.
Japanese suppliers are often willing to demonstrate their sophisticated processes through factory visits, providing deeper insights into their operations.
Consider also the supplier’s track record with innovation and their ability to adapt to changing technologies or market demands.
This adaptability is crucial for maintaining a competitive edge in an ever-evolving industry.
Implementing Multi-Measurement Devices in Production
Successfully implementing multi-measurement devices involves a careful alignment of these devices with current production processes.
This requires strategic planning, involving key stakeholders such as production engineers, quality assurance managers, and IT specialists.
Steps to Successful Implementation
Begin with a detailed needs assessment to identify how multi-measurement devices can best integrate into your existing operations.
This will help determine the specific types of measurement capabilities required and highlight areas for potential improvement.
Engage with consultants or technology partners who specialize in deploying these sophisticated systems.
Their expertise can be invaluable in ensuring proper installation, training, and ongoing support for your team.
Invest in comprehensive training programs to ensure that operators are skilled in using both the hardware and associated software efficiently.
This is crucial for optimizing the full potential of multi-measurement devices.
Continuous Improvement and Feedback
Integrate a system of continuous feedback to regularly evaluate the performance of the devices.
This feedback loop will help identify areas for further optimization and adaptation to changing production needs.
Encourage cross-departmental collaboration, enabling various teams to leverage the insights gained from these devices to drive overall process improvements and innovations.
Conclusion
The rise of Japan’s multi-measurement devices is transforming the landscape of precision manufacturing.
While they offer unparalleled accuracy and efficiency, proper consideration of the associated challenges and strategic sourcing practices is critical to maximizing their benefits.
For procurement and purchasing professionals, developing a deep understanding of these devices, building strong relationships with Japanese suppliers, and applying best practices in integration are key steps toward achieving manufacturing excellence.
As we continue to advance in this digitized age of manufacturing, Japan’s contributions in multi-measurement technologies will undoubtedly play a pivotal role in reshaping industry standards and practices.
資料ダウンロード
QCD調達購買管理クラウド「newji」は、調達購買部門で必要なQCD管理全てを備えた、現場特化型兼クラウド型の今世紀最高の購買管理システムとなります。
ユーザー登録
調達購買業務の効率化だけでなく、システムを導入することで、コスト削減や製品・資材のステータス可視化のほか、属人化していた購買情報の共有化による内部不正防止や統制にも役立ちます。
NEWJI DX
製造業に特化したデジタルトランスフォーメーション(DX)の実現を目指す請負開発型のコンサルティングサービスです。AI、iPaaS、および先端の技術を駆使して、製造プロセスの効率化、業務効率化、チームワーク強化、コスト削減、品質向上を実現します。このサービスは、製造業の課題を深く理解し、それに対する最適なデジタルソリューションを提供することで、企業が持続的な成長とイノベーションを達成できるようサポートします。
オンライン講座
製造業、主に購買・調達部門にお勤めの方々に向けた情報を配信しております。
新任の方やベテランの方、管理職を対象とした幅広いコンテンツをご用意しております。
お問い合わせ
コストダウンが利益に直結する術だと理解していても、なかなか前に進めることができない状況。そんな時は、newjiのコストダウン自動化機能で大きく利益貢献しよう!
(Β版非公開)