- お役立ち記事
- Items to be considered by procurement and purchasing departments when upgrading processing facilities
Items to be considered by procurement and purchasing departments when upgrading processing facilities
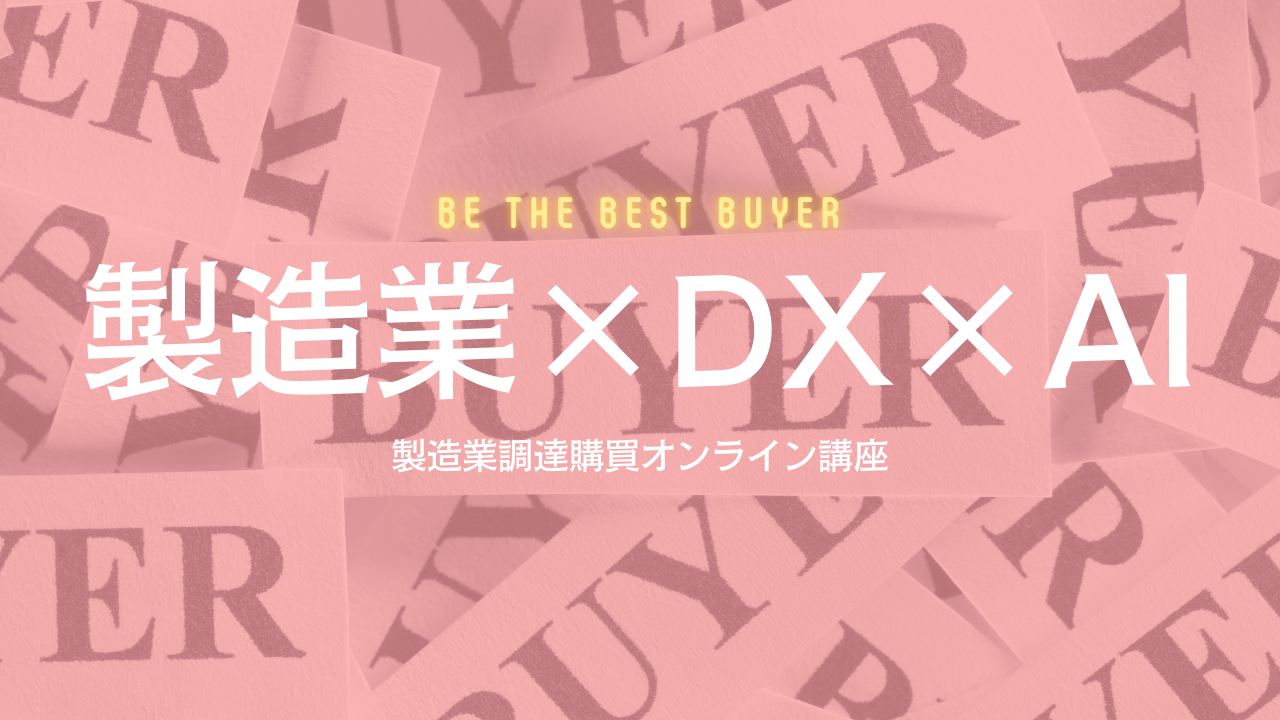
When facilities require modernization or expansion to keep up with changes in production needs, procurement and purchasing departments play a key role in the upgrade process. There are many factors that must be carefully evaluated to ensure a smooth transition.
Safety should always be the top priority. New equipment and machinery introduced must meet all applicable safety regulations. Thorough research is needed to confirm compliance standards are met. It may also be necessary to upgrade other safety features like lighting, guardrails, ventilation systems, alarms, etc. to protect workers. Proper training will also need to be provided to employees on the new equipment and any changes to workflow.
Capacity is another important consideration. Will the upgraded facilities allow for increased output? Analysis of current and projected production volumes will help determine the right scale for the upgrade. Flexibility for future growth should also be accounted for in initial plans and designs if possible. Too small an upgrade may soon prove insufficient as the business expands.
Efficiency gains can lower long-term costs. New technologies may offer faster cycle times, reduced waste, or less labor hours per unit produced. Energy consumption of new systems should be evaluated to reduce environmental impact and energy bills. Maintenance requirements are also a factor- some newer equipment options have simplified designs that are less prone to breakdowns.
Cost is a primary factor but shouldn’t be the sole decision driver. Total installed cost, expected return on investment, and lifespan of the upgrade must all be weighed. Short-term impacts like temporary reduced productivity during installation should be considered. Operating costs over the expected lifespan should be projected and compared to current costs. Financing options may help spread payments over multiple years.
Sustainability has grown in importance. Processes and equipment that conserve resources and lower emissions will become increasingly important to customers and regulations. Some upgrades can incorporate renewable energy, material reuse systems, more efficient lighting, or other eco-friendly features that demonstrate corporate social responsibility while lowering long-run costs. Near-zero waste targets may require re-engineering some production steps in the upgrade design.
Supply chain impacts need assessment. Will the upgrade affect relationships with existing vendors and partners? Changes to specifications, lead times, or product/part dimensions could disrupt suppliers if not properly coordinated. New equipment may require sourcing different raw materials or components that need secure, cost-effective supply lined up beforehand. Key suppliers should be engaged early in the planning process.
Scheduling demands experience. The timeline for the upgrade project must balance productivity needs with installation realities. Will certain production lines need to be fully or partially shutdown during transition periods? Can installation occur in phases to minimize downtime? Expectations of contractors and involvement of in-house maintenance staff require detailed planning. Buffer periods for unexpected delays or additional unforeseen needs are wise to include.
Assessing worker and organizational readiness is important but often overlooked. Resistance to change should be expected and addressed through clear communication about benefits of the upgrade. Additional training requirements are a scheduling and budget consideration. Cultural shifts may be needed- some processes that worked acceptably with older systems may not mesh well with new automated or digital equipment without adjustment. Change management plans can smooth transitions.
Thorough pilot testing whenever possible can avoid costly mistakes. Small-scale trials of new processes, layouts, or workflows allow identification and correction of issues. Digital simulations and virtual reality previews may also help validate designs and plans before full installation and commissioning. Pilots also educate workers and build confidence that the changes will function as intended when live production begins.
To summarize, procurement and purchasing teams play a key oversight role when upgrading facilities to keep production cutting edge and competitive. Careful multi-dimensional assessment considering operational impact, regulatory compliance, cost, schedule and people factors leads to smoother transitions and long-term success meeting business objectives. With diligent planning and stakeholder involvement, facility makeovers can position companies well for the future.
資料ダウンロード
QCD調達購買管理クラウド「newji」は、調達購買部門で必要なQCD管理全てを備えた、現場特化型兼クラウド型の今世紀最高の購買管理システムとなります。
ユーザー登録
調達購買業務の効率化だけでなく、システムを導入することで、コスト削減や製品・資材のステータス可視化のほか、属人化していた購買情報の共有化による内部不正防止や統制にも役立ちます。
NEWJI DX
製造業に特化したデジタルトランスフォーメーション(DX)の実現を目指す請負開発型のコンサルティングサービスです。AI、iPaaS、および先端の技術を駆使して、製造プロセスの効率化、業務効率化、チームワーク強化、コスト削減、品質向上を実現します。このサービスは、製造業の課題を深く理解し、それに対する最適なデジタルソリューションを提供することで、企業が持続的な成長とイノベーションを達成できるようサポートします。
オンライン講座
製造業、主に購買・調達部門にお勤めの方々に向けた情報を配信しております。
新任の方やベテランの方、管理職を対象とした幅広いコンテンツをご用意しております。
お問い合わせ
コストダウンが利益に直結する術だと理解していても、なかなか前に進めることができない状況。そんな時は、newjiのコストダウン自動化機能で大きく利益貢献しよう!
(Β版非公開)