- お役立ち記事
- Operation and Applications of Press Brakes in Metal Factories
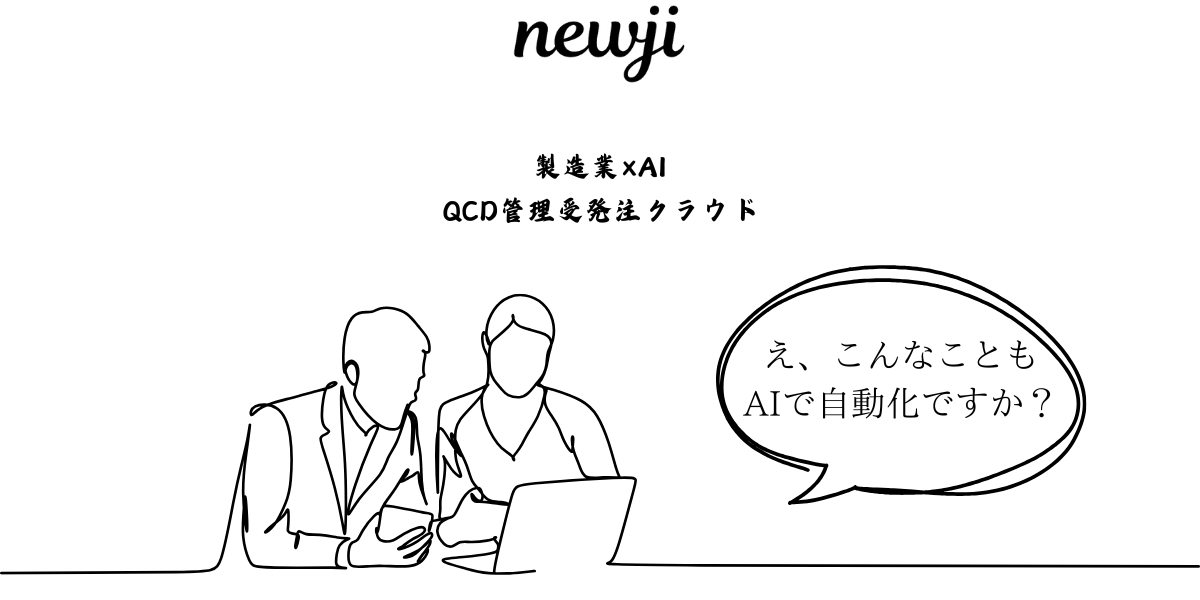
Operation and Applications of Press Brakes in Metal Factories
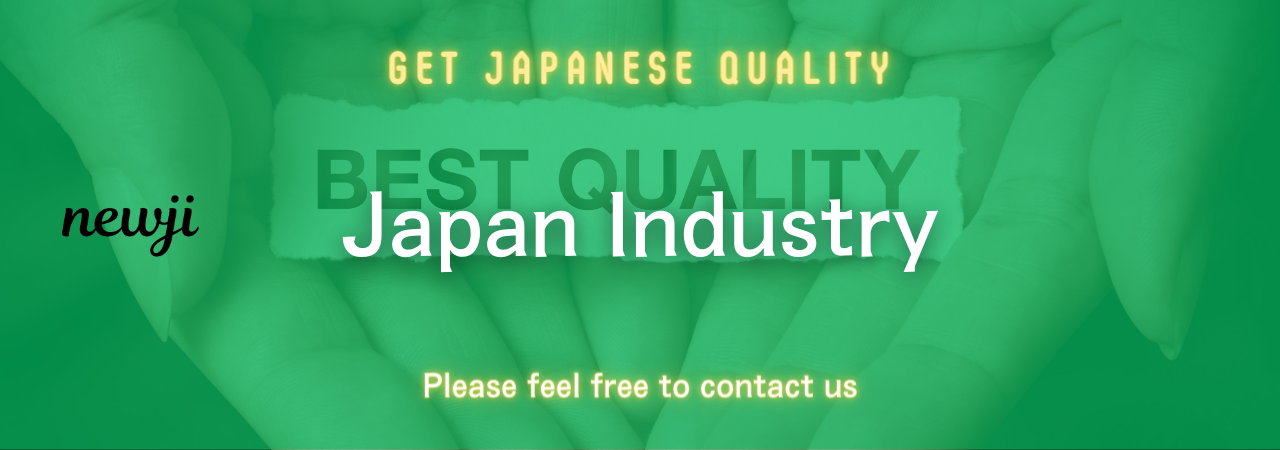
目次
Understanding Press Brakes
Press brakes are essential machines used in metal fabrication to bend and shape metal sheets.
In metal factories, these powerful tools allow for precision bending, making them invaluable for a variety of production tasks.
A press brake applies force to a metal sheet, typically along a straight line, to create a specific angle and form.
The operation involves positioning the metal sheet between a matching punch and die.
When the punch pushes the metal into the die, it bends to form the desired shape.
Press brakes are versatile and capable of creating intricate shapes and complex angles.
This versatility makes them crucial in manufacturing processes across industries including automotive, aerospace, and construction.
Types of Press Brakes
Several types of press brakes are used in metal fabrication, each offering distinct advantages.
Mechanical Press Brakes
Mechanical press brakes use a flywheel powered by an electric motor.
The flywheel transfers energy to move the ram, which in turn bends the metal.
These systems are known for their rapid operating speeds and consistent force.
Mechanical press brakes are suitable for high-volume production runs as they can repeat the same operation quickly and efficiently.
Hydraulic Press Brakes
Hydraulic press brakes use hydraulic cylinders to generate force, providing precise control over the bending process.
They are known for their reliability and are often preferred in situations where accuracy and repeatability are essential.
Hydraulic press brakes are also energy efficient as they only consume power while in operation.
These brakes are ideal for handling larger and thicker metal sheets and can be used for various applications, from simple bends to complex production tasks.
CNC Press Brakes
Computer Numerical Control (CNC) press brakes integrate computer technology with traditional press brake operations.
The computer interface allows operators to input precise bending measurements and angles.
This automation reduces human error and increases productivity.
CNC press brakes are highly flexible and are often used for jobs requiring multiple intricate bends.
Their ability to facilitate fast tool changes makes them ideal for custom jobs with variable bending requirements.
Applications of Press Brakes in Metal Factories
Press brakes serve numerous applications in metal factories, making them indispensable in the fabrication process.
Automotive Industry
In the automotive industry, press brakes produce various parts like brackets, body panels, and support beams.
The precise bending offered by press brakes ensures that each part fits perfectly, maintaining the structural integrity of the vehicle.
With the ability to handle both thin sheets for body panels and thicker materials for chassis components, press brakes are vital in automotive manufacturing.
Aerospace Industry
The aerospace industry relies heavily on the accuracy of press brakes for producing components that must meet stringent safety requirements.
Parts crafted for aircraft, such as wing components and engine mounts, must adhere to exact specifications, something that press brakes can consistently achieve.
The precision and reliability provided by CNC press brakes are especially beneficial in aerospace applications where each part must perform under extreme conditions.
Construction Industry
In construction, press brakes are used to fabricate structural components like beams, braces, and sheet metal roofing materials.
The ability to quickly produce large quantities of consistently shaped metal parts aids in the efficient building of structures.
Press brakes enhance the speed of construction projects while maintaining high standards of quality.
Custom Metal Fabrication
For custom metal fabrication shops, press brakes are versatile tools that can handle single pieces or small batch production.
They are invaluable when creating custom prototypes, signage, metal art, and specialized equipment.
The adaptability of press brakes allows fabricators to meet unique customer specifications, offering a wide range of design possibilities and fostering creativity in metalwork projects.
Operating a Press Brake
Operating a press brake requires a skilled operator to ensure safety and accuracy.
It begins with selecting the appropriate tools, such as the punch and die, which determine the bend angle and radius.
The operator must set the back gauge and ram stroke distance to ensure the metal is positioned correctly for each bend.
Prior to operation, it is crucial to conduct safety checks to make sure the machine is functioning properly and that the work area is clear of hazards.
Operators must wear appropriate protective gear, such as gloves and eye protection, to reduce the risk of injury.
Additionally, precision in programming is essential with CNC press brakes to ensure the bending sequence is executed as planned.
It’s important for operators to have a thorough understanding of the machine’s capabilities and limitations, ensuring that each job is completed efficiently and safely.
The Future of Press Brake Technology
The future of press brake technology is poised for innovation, with advancements aimed at increasing efficiency, precision, and automation in metal fabrication.
The integration of artificial intelligence and machine learning could further automate press brake systems, enabling self-adjustments in real-time to accommodate variances in material properties or external conditions.
Developments in tooling are also expected, offering longer-lasting and more adaptable tools capable of handling new materials and complex geometries.
Moreover, enhancements in software will likely improve user interfaces, allowing operators to easily manipulate machine settings through intuitive controls.
In conclusion, press brakes are fundamental in metal factories, serving a wide range of industries through their versatility and precision.
As technology advances, these machines will continue to evolve, offering even greater efficiency and expanding the possibilities in metal manufacturing.
資料ダウンロード
QCD調達購買管理クラウド「newji」は、調達購買部門で必要なQCD管理全てを備えた、現場特化型兼クラウド型の今世紀最高の購買管理システムとなります。
ユーザー登録
調達購買業務の効率化だけでなく、システムを導入することで、コスト削減や製品・資材のステータス可視化のほか、属人化していた購買情報の共有化による内部不正防止や統制にも役立ちます。
NEWJI DX
製造業に特化したデジタルトランスフォーメーション(DX)の実現を目指す請負開発型のコンサルティングサービスです。AI、iPaaS、および先端の技術を駆使して、製造プロセスの効率化、業務効率化、チームワーク強化、コスト削減、品質向上を実現します。このサービスは、製造業の課題を深く理解し、それに対する最適なデジタルソリューションを提供することで、企業が持続的な成長とイノベーションを達成できるようサポートします。
オンライン講座
製造業、主に購買・調達部門にお勤めの方々に向けた情報を配信しております。
新任の方やベテランの方、管理職を対象とした幅広いコンテンツをご用意しております。
お問い合わせ
コストダウンが利益に直結する術だと理解していても、なかなか前に進めることができない状況。そんな時は、newjiのコストダウン自動化機能で大きく利益貢献しよう!
(Β版非公開)