- お役立ち記事
- Tolerance Control and Dimension Precision Improvement Methods in General Machinery
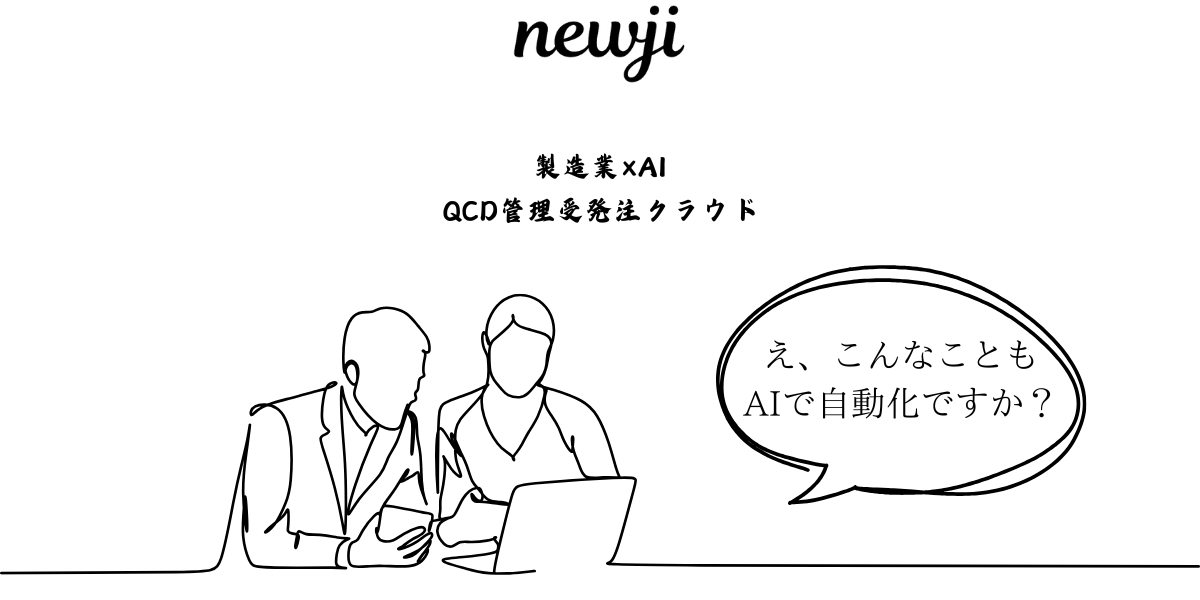
Tolerance Control and Dimension Precision Improvement Methods in General Machinery
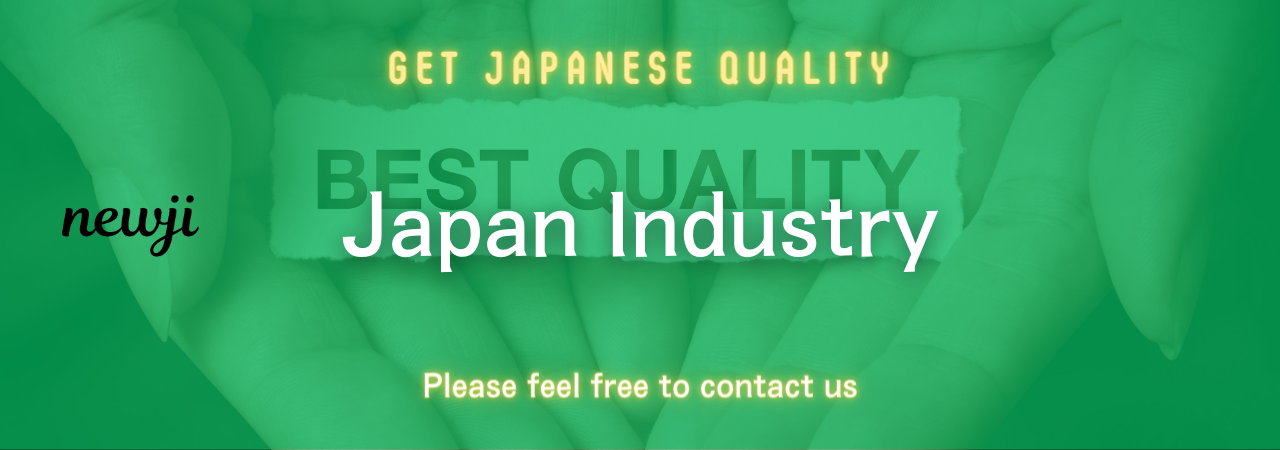
目次
Understanding Tolerance Control
Tolerance control is a vital aspect of manufacturing and plays a crucial role in ensuring that machinery functions as intended.
In the context of general machinery, it refers to the permissible limits of variation in a physical dimension or physical property of a manufactured part.
The ability to maintain these dimensions accurately affects the performance, reliability, and quality of machinery.
Manufacturers employ tolerance control to balance cost and precision.
Tighter tolerances often lead to higher manufacturing costs due to increased waste, slower production rates, and the need for more advanced machinery.
However, tighter tolerances can be necessary for parts requiring extreme precision, such as those found in the aerospace or medical industries.
The Importance of Tolerance Control
Tolerance control ensures that parts fit together correctly and function as a cohesive unit.
For example, in an engine, each part must be manufactured to precise specifications to ensure efficiency and performance.
If the parts are out of tolerance, it may result in increased wear, reduced lifespan, or even complete failure.
Additionally, good tolerance control contributes to the standardization of parts.
When parts are produced with consistent quality, it allows for interchangeability and easier assembly, maintenance, and repair of machinery.
Methods to Achieve Dimension Precision
Achieving dimension precision in manufacturing processes involves various methods and techniques.
Here are some key approaches used in the industry:
Advanced Manufacturing Technologies
Implementing advanced manufacturing technologies is one method to improve dimension precision.
CNC (Computer Numerical Control) machines are often used as they offer exceptional precision and repeatability, essential for maintaining tight tolerances.
Moreover, 3D printing technology allows for the creation of complex geometries that might be difficult or impossible to achieve with traditional manufacturing techniques.
Precision Measurement Tools
The use of precision measurement tools is critical for verifying that components meet the required specifications.
Tools like micrometers, calipers, and coordinate measuring machines (CMMs) allow technicians to measure dimensions accurately.
These tools help identify parts that do not meet tolerance requirements before they are integrated into the final product.
Quality Control Systems
Establishing robust quality control systems ensures that all parts produced adhere to set tolerance levels.
Statistical process control (SPC) techniques monitor and control the process through statistical data.
SPC helps identify variations in the production process, allowing for immediate correction and minimizing errors.
Strategies to Improve Tolerance Control
Improving tolerance control and dimension precision involves the application of several strategic approaches:
Design for Manufacturability
Design for Manufacturability (DFM) is an approach where products are designed with manufacturing in mind.
This includes considering tolerance capabilities of different manufacturing processes and selecting the best approach that strikes a balance between cost and quality.
By integrating DFM principles early in the design phase, manufacturers can reduce production issues and ensure that parts stay within tolerance limits.
Training and Skill Development
Investment in training and skill development is crucial for improving tolerance control in manufacturing.
Operators and engineers need to be adept at using advanced machinery and understanding technical drawings and specifications.
Regular training sessions can help employees stay updated with the latest techniques and best practices in manufacturing precision.
Collaborative Supplier Relationships
Building collaborative relationships with suppliers can also enhance tolerance control.
Suppliers with a solid track record of precision can be instrumental in providing high-quality parts.
Collaborative efforts ensure that both manufacturers and suppliers are aligned in terms of quality standards and expectations.
The Impact of Technology on Tolerance Control
The advent of Industry 4.0 and digital transformation has significantly impacted tolerance control and dimension precision methods.
Technological innovations provide new opportunities for manufacturers to improve precision.
IoT and Data Analytics
The Internet of Things (IoT) enables machinery and devices to communicate and share data seamlessly.
This data can be analyzed to gain insights into the production process.
By utilizing IoT, manufacturers can predict and prevent deviations from tolerance, thus ensuring better precision.
Artificial Intelligence and Machine Learning
Artificial Intelligence (AI) and Machine Learning (ML) can help in optimizing manufacturing processes.
AI algorithms can analyze production data to detect patterns and anomalies that humans might miss.
This capability allows manufacturers to address potential tolerance issues before they become significant problems.
Challenges in Achieving Precision
While there are many advancements and methods to improve tolerance control and dimension precision, several challenges persist:
Material Variability
Different materials expand and contract differently under varying conditions.
Material variability can impact the final dimensions of a manufactured part, making it challenging to maintain consistent precision.
Machine Wear and Calibration
Over time, machines can wear out and become less accurate.
Regular calibration and maintenance are necessary to ensure machines function optimally and maintain their precision.
Balancing Cost and Precision
Achieving tight tolerances often comes at a higher cost.
Manufacturers must find an optimal balance between cost and the level of precision required for the application.
Conclusion
Improving tolerance control and dimension precision is essential for the success of general machinery manufacturing.
By leveraging advanced technologies, focusing on training, and adopting strategic approaches such as DFM, manufacturers can enhance their products’ precision and reliability.
While challenges remain, ongoing innovation and collaboration will continue to drive improvements in this critical area.
資料ダウンロード
QCD調達購買管理クラウド「newji」は、調達購買部門で必要なQCD管理全てを備えた、現場特化型兼クラウド型の今世紀最高の購買管理システムとなります。
ユーザー登録
調達購買業務の効率化だけでなく、システムを導入することで、コスト削減や製品・資材のステータス可視化のほか、属人化していた購買情報の共有化による内部不正防止や統制にも役立ちます。
NEWJI DX
製造業に特化したデジタルトランスフォーメーション(DX)の実現を目指す請負開発型のコンサルティングサービスです。AI、iPaaS、および先端の技術を駆使して、製造プロセスの効率化、業務効率化、チームワーク強化、コスト削減、品質向上を実現します。このサービスは、製造業の課題を深く理解し、それに対する最適なデジタルソリューションを提供することで、企業が持続的な成長とイノベーションを達成できるようサポートします。
オンライン講座
製造業、主に購買・調達部門にお勤めの方々に向けた情報を配信しております。
新任の方やベテランの方、管理職を対象とした幅広いコンテンツをご用意しております。
お問い合わせ
コストダウンが利益に直結する術だと理解していても、なかなか前に進めることができない状況。そんな時は、newjiのコストダウン自動化機能で大きく利益貢献しよう!
(Β版非公開)