- お役立ち記事
- Dimensional Tolerance Testing for Quality Control in General Machinery
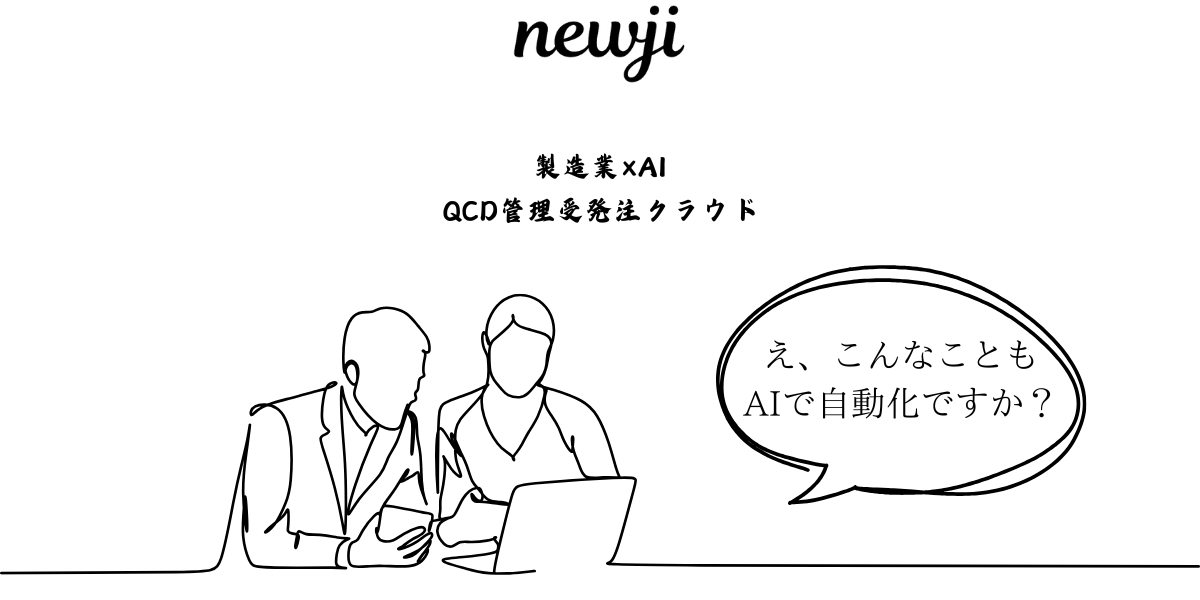
Dimensional Tolerance Testing for Quality Control in General Machinery
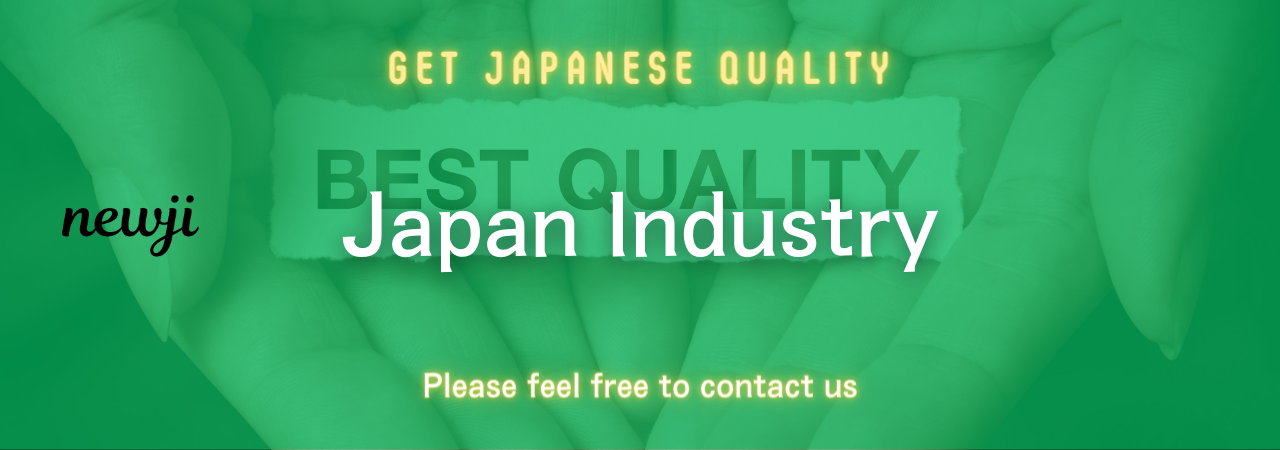
目次
Understanding Dimensional Tolerance in Machinery
In the world of general machinery, maintaining precise measurements is crucial for ensuring the proper functioning of parts and assemblies.
Dimensional tolerance refers to the allowable deviation from the exact measurements specified in engineering designs.
This concept plays a significant role in quality control processes, as it determines the accuracy and reliability of manufactured components.
By establishing acceptable ranges for dimensions, manufacturers can ensure their products meet quality standards while reducing the likelihood of malfunction and failure.
Understanding and implementing dimensional tolerance is essential for achieving consistency, minimizing waste, and maintaining customer satisfaction.
The Importance of Dimensional Tolerance Testing
Dimensional tolerance testing is a vital part of quality control in machinery production.
This practice helps determine how closely the manufactured components adhere to the specified design dimensions.
When variations in parts’ sizes fall within the established tolerance limits, the products are deemed acceptable.
However, if the parts deviate beyond these limits, they may require adjustments or rejection.
Such testing is crucial for several reasons.
Firstly, it ensures that all parts fit together seamlessly, preventing issues such as leaks, misalignment, or vibration that may arise from inaccurate manufacturing.
Secondly, maintaining strict dimensional tolerance reduces material waste and production costs, as fewer components need to be scrapped or reworked.
Finally, it helps uphold a company’s reputation by delivering reliable and high-quality products to customers.
Types of Dimensional Tolerances
Dimensional tolerances are divided into two main categories: geometric and size tolerances.
Understanding the differences between these two types helps manufacturers maintain the desired level of precision in their products.
Geometric Tolerances
Geometric tolerances define the allowable variations in a part’s shape, orientation, or position.
These tolerances control features such as straightness, flatness, cylindricity, and angularity.
By setting limits on these attributes, manufacturers can ensure that the parts function as intended and fit together properly.
For instance, if a shaft must remain straight within a specified limit, geometric tolerances help define how much deviation from perfect straightness is allowed.
Such specifications maintain the integrity and performance of machinery components.
Size Tolerances
Size tolerances, on the other hand, deal with the allowable variations in the actual dimensions of a part.
These include length, width, height, diameter, and thickness.
Size tolerances ensure that each part fits precisely with others, reducing the risk of gaps, overlaps, or misalignment.
For example, in a mechanical assembly requiring bolts and nuts, size tolerances dictate the range of acceptable diameters for threads on both components.
This ensures a proper fit, affecting the overall stability and performance of the assembly.
Methods for Dimensional Tolerance Testing
Manufacturers employ various methods to test and validate dimensional tolerances in machinery components.
Some of the widely used techniques include:
Precision Measurement Tools
Tools such as calipers, micrometers, and height gauges offer accurate readings of part dimensions.
These instruments help verify whether a component meets the size specifications set by the engineering designs.
While manual measurement can be time-consuming, it remains a reliable method for ensuring parts conform to dimensional tolerances.
Coordinate Measuring Machines (CMM)
CMMs are advanced devices that automate the measurement process, providing enhanced accuracy and efficiency.
Using contact or non-contact probes, CMMs assess geometric features and obtain precise data about a component’s dimensions.
This information helps verify that the part complies with both geometric and size tolerances.
Laser Scanning
Laser scanning technology provides a fast and non-invasive means of capturing detailed measurements of complex shapes and surfaces.
By creating a digital 3D model of the part, laser scanning offers comprehensive verification of dimensions, size, and geometric tolerances.
This method is particularly valuable for intricate components that require intricate measurements.
Challenges in Dimensional Tolerance Testing
While dimensional tolerance testing is essential for quality control, it can pose several challenges for manufacturers.
One such challenge is maintaining consistency when working with different materials that exhibit varying properties, such as thermal expansion or elasticity.
These factors can impact dimensional integrity during production, making accurate tolerance testing more complex.
Another challenge lies in balancing the need for precision with production costs and efficiency.
Excessively tight tolerances may lead to increased production expenses due to the need for more specialized tooling and equipment.
Finding the optimal balance allows manufacturers to produce components that are both cost-effective and precise.
Implementing Effective Quality Control Systems
To achieve reliable dimensional tolerance testing, manufacturers must establish comprehensive quality control systems.
This involves training personnel on proper measurement techniques, implementing routine calibration of measuring devices, and conducting regular audits to identify areas for improvement.
Additionally, adopting quality management systems such as ISO 9001 can help standardize processes and ensure continuous improvement.
By embracing these practices, manufacturers can maintain high levels of precision, reduce waste, and consistently deliver high-quality machinery components.
Conclusion
Dimensional tolerance testing serves as a backbone for quality control in the machinery industry.
By adhering to precise specifications and ensuring each component fits its intended purpose, manufacturers can produce reliable and high-performing products.
Understanding different types of tolerances, employing effective testing methods, and overcoming challenges are key steps toward successful implementation.
Investing in robust quality control systems and consistently improving processes allows manufacturers to meet customer expectations, reduce production costs, and maintain a competitive edge in the marketplace.
資料ダウンロード
QCD調達購買管理クラウド「newji」は、調達購買部門で必要なQCD管理全てを備えた、現場特化型兼クラウド型の今世紀最高の購買管理システムとなります。
ユーザー登録
調達購買業務の効率化だけでなく、システムを導入することで、コスト削減や製品・資材のステータス可視化のほか、属人化していた購買情報の共有化による内部不正防止や統制にも役立ちます。
NEWJI DX
製造業に特化したデジタルトランスフォーメーション(DX)の実現を目指す請負開発型のコンサルティングサービスです。AI、iPaaS、および先端の技術を駆使して、製造プロセスの効率化、業務効率化、チームワーク強化、コスト削減、品質向上を実現します。このサービスは、製造業の課題を深く理解し、それに対する最適なデジタルソリューションを提供することで、企業が持続的な成長とイノベーションを達成できるようサポートします。
オンライン講座
製造業、主に購買・調達部門にお勤めの方々に向けた情報を配信しております。
新任の方やベテランの方、管理職を対象とした幅広いコンテンツをご用意しております。
お問い合わせ
コストダウンが利益に直結する術だと理解していても、なかなか前に進めることができない状況。そんな時は、newjiのコストダウン自動化機能で大きく利益貢献しよう!
(Β版非公開)