- お役立ち記事
- Design and Applications of Parallel Link Robots in General Machinery
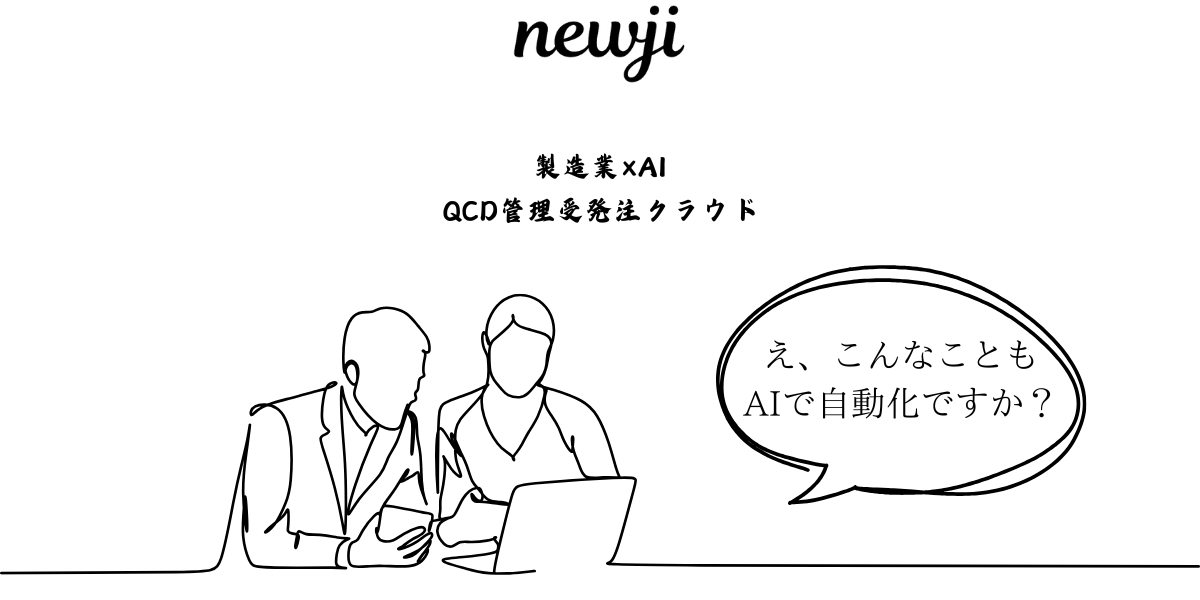
Design and Applications of Parallel Link Robots in General Machinery
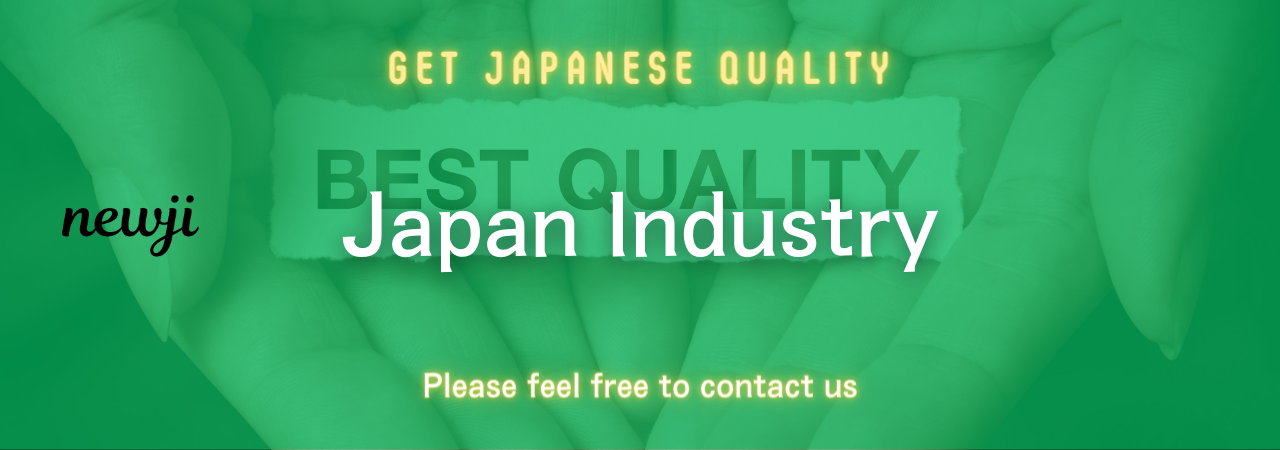
目次
Introduction to Parallel Link Robots
Parallel link robots, often referred to as parallel manipulators, are a type of robotic mechanism characterized by having multiple arms or links that work together in tandem to control a single platform or end effector.
Unlike serial manipulators where joints are connected in a series, parallel link robots have several arms connected to a common base and a mobile platform, allowing for high precision and the ability to handle heavy loads with minimal deformation.
This unique structure gives parallel link robots a distinct advantage over traditional robotic systems in various applications.
Design Principles of Parallel Link Robots
The design of parallel link robots involves critical parameters such as the type of joints, link lengths, and the configuration of the base and the platform.
Most parallel link robots employ prismatic or revolute joints that allow linear or rotational movements.
The geometry of the robot highly influences its speed, accuracy, and ability to carry loads.
Unlike serial robots, parallel robots tend to have a smaller workspace due to the nature of their short-arm configuration.
This limitation is often offset by the increased stiffness, accuracy, and dynamic performance.
Types of Parallel Link Robots
Parallel link robots come in various configurations, each suited for different applications.
The most common types include:
1. **Delta Robots:** Known for their high-speed pick-and-place capabilities, Delta robots have three arms connected to universal joints at the base.
2. **Stewart Platforms:** These are six-degree-of-freedom platforms commonly used for flight simulators and precision positioning.
3. **Gough Platforms:** Similar to Stewart platforms but differ in their structural design and applications.
Each type has its own specific applications based on its unique configurations and capabilities.
Applications of Parallel Link Robots in General Machinery
Parallel link robots are increasingly used in various industries due to their speed, precision, and versatility.
Manufacturing and Assembly
In the manufacturing sector, parallel link robots are used for tasks that require high precision and speed.
They excel in assembly operations, where precise movements are crucial to fit components together accurately.
Their ability to handle multiple degrees of freedom allows them to perform intricate tasks like assembling microchips and other delicate components.
Packaging and Material Handling
One of the most common applications of parallel link robots is in the packaging industry.
Delta robots, for example, are used extensively for high-speed pick-and-place tasks in packaging lines.
They rapidly sort, pack, and relocate items with incredible dexterity, enhancing overall productivity and reducing operational costs.
Medical and Surgical Applications
In the medical field, parallel link robots are gaining traction, particularly in surgery and rehabilitation.
Their precision movement allows them to assist in complex surgical procedures, providing surgeons with enhanced control and reduced fatigue during lengthy operations.
In rehabilitation, these robots provide precise and guided therapy movements, helping patients recover efficiently and safely.
Automotive Industry
In automotive manufacturing, parallel link robots help in tasks such as assembling vehicle components, painting, and quality inspection.
Their rigidity allows them to maintain high accuracy in repetitive tasks, ensuring the quality of assembly lines.
Automakers also use them in simulations to replicate the dynamic driving experience before mass production.
Advantages of Parallel Link Robots
Parallel link robots offer several advantages over traditional serial robots, making them highly desirable for specific industrial applications.
Increased Precision and Accuracy
Due to their closed-loop kinematic structure, parallel link robots can achieve higher precision and accuracy as the errors in one link or joint are compensated by the others.
This attribute makes them ideal for precision tasks such as machining and assembly.
Higher Load Capacity
The shared load among the multiple arms results in increased rigidity and higher load capacity.
Parallel link robots can handle heavier payloads with less deformation, an essential feature for heavy machinery tasks.
Enhanced Speed and Dynamics
The lightweight nature of the individual arms allows for quicker, more dynamic movements, significantly enhancing the speed of operations.
This characteristic is particularly beneficial in high-speed operations such as pick-and-place tasks in packaging and sorting.
Challenges in the Implementation of Parallel Link Robots
Despite their advantages, parallel link robots face several challenges that need addressing to maximize their potential.
Limited Workspace
The constrained workspace inherent to parallel robots limits their application to tasks requiring larger operational areas.
Design optimizations and advancements in robotic algorithms can help mitigate this issue.
Complex Control Systems
Due to the interlinked structure of multiple arms, parallel link robots require complex control systems and advanced algorithms for precise operation.
Developing these systems requires expertise in both programming and robotic mechanisms.
Higher Initial Costs
The sophisticated design and high precision positioning systems raise the initial cost of investment in parallel link robotics.
Though the long-term benefits in productivity and accuracy often outweigh these costs, initial budget constraints can be a barrier for some businesses.
Conclusion
The innovative design and versatile applications of parallel link robots make them a valuable asset in the general machinery industry.
Their ability to provide high precision, increased speed, and enhanced load capacity supports their deployment across various sectors, from medical to manufacturing.
As technology advances, overcoming current challenges will pave the way for even broader use of parallel link robots, solidifying their role in the future of robotic automation.
資料ダウンロード
QCD調達購買管理クラウド「newji」は、調達購買部門で必要なQCD管理全てを備えた、現場特化型兼クラウド型の今世紀最高の購買管理システムとなります。
ユーザー登録
調達購買業務の効率化だけでなく、システムを導入することで、コスト削減や製品・資材のステータス可視化のほか、属人化していた購買情報の共有化による内部不正防止や統制にも役立ちます。
NEWJI DX
製造業に特化したデジタルトランスフォーメーション(DX)の実現を目指す請負開発型のコンサルティングサービスです。AI、iPaaS、および先端の技術を駆使して、製造プロセスの効率化、業務効率化、チームワーク強化、コスト削減、品質向上を実現します。このサービスは、製造業の課題を深く理解し、それに対する最適なデジタルソリューションを提供することで、企業が持続的な成長とイノベーションを達成できるようサポートします。
オンライン講座
製造業、主に購買・調達部門にお勤めの方々に向けた情報を配信しております。
新任の方やベテランの方、管理職を対象とした幅広いコンテンツをご用意しております。
お問い合わせ
コストダウンが利益に直結する術だと理解していても、なかなか前に進めることができない状況。そんな時は、newjiのコストダウン自動化機能で大きく利益貢献しよう!
(Β版非公開)