- お役立ち記事
- Case Studies of Non-Contact Sensor Technology in Production Lines
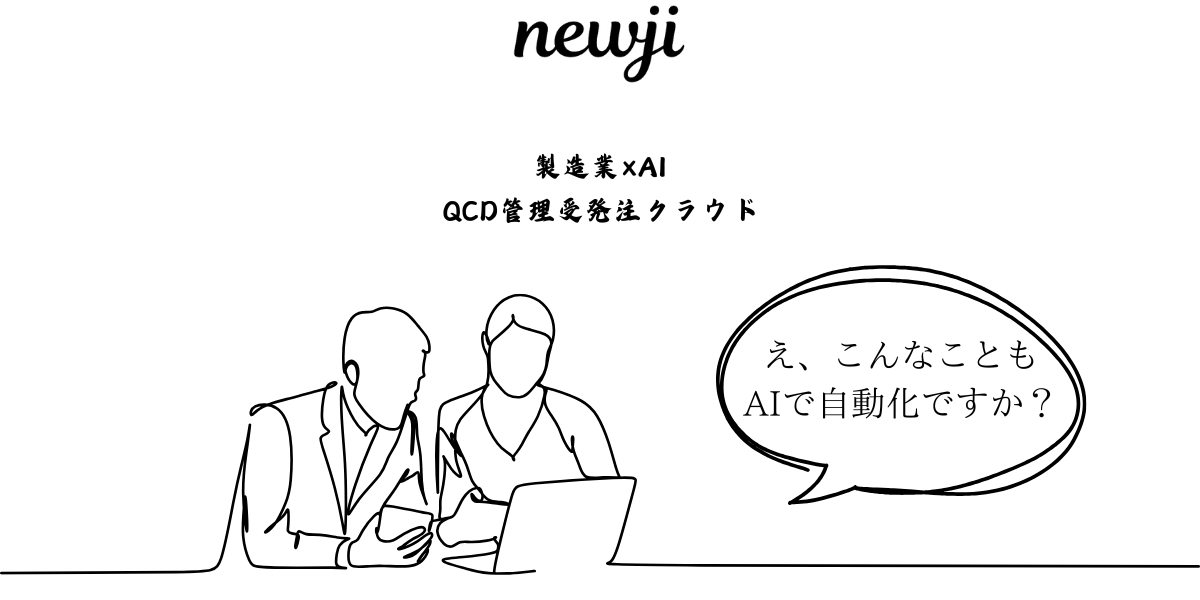
Case Studies of Non-Contact Sensor Technology in Production Lines
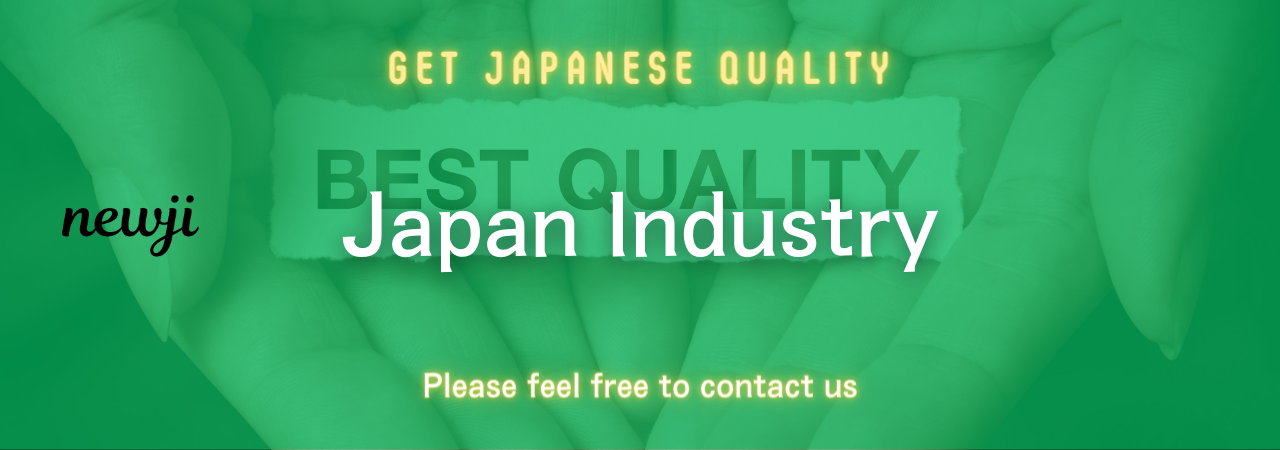
目次
Introduction to Non-Contact Sensor Technology
Non-contact sensor technology has revolutionized how production lines operate across industries.
By eliminating the need for physical contact, these sensors offer increased efficiency and reliability in monitoring and control tasks.
The technology uses various principles, such as optical, electromagnetic, and ultrasonic, to detect changes in the environment or properties of the materials being processed.
The Importance of Non-Contact Sensors in Production
Production lines depend heavily on precise and real-time data to maintain consistency and quality.
Non-contact sensors play a crucial role in achieving these goals.
They provide accurate measurements without direct interaction with the products, which means reduced wear and tear and contamination possibilities.
Additionally, their ability to work at high speeds without slowing down the production process makes them invaluable.
Advantages of Non-Contact Sensors
The primary advantage of non-contact sensors is their ability to perform without interfering with the operation.
This contributes to enhanced longevity of equipment and fewer disruptions.
Non-contact sensors are also known for their high accuracy and precision.
They can detect minute changes that might be missed by traditional contact-based sensors.
Their versatility allows them to operate in harsh environments where physical contact would be impractical or impossible.
Lastly, they contribute significantly to the scalability of production lines as they can be easily integrated and upgraded to meet changing demands.
Case Study 1: Optical Sensors in Electronic Manufacturing
One of the most significant applications of non-contact sensor technology is in the electronic manufacturing sector.
In this case study, we consider a major electronics company that introduced optical sensors into their production line.
The primary role of these sensors was to inspect printed circuit boards (PCBs) for defects.
Implementation and Impact
Before implementing optical sensors, inspection processes were manually intensive and error-prone.
By integrating optical sensors, the company automated the inspection process, significantly reducing human error and increasing production rates.
High-resolution imaging allowed for detailed analysis without halting the production line, thus ensuring continuous operation.
Case Study 2: Ultrasonic Sensors in the Automotive Industry
The second case study examines the use of ultrasonic sensors in automotive manufacturing.
Here, the sensors were used to ensure precision in assembling components like fuel tanks and exhaust systems.
Enhancing Accuracy and Efficiency
Ultrasonic sensors emit high-frequency sound waves that reflect off surfaces to measure distances.
This capability was employed in determining the exact fit and alignment of automotive parts.
The sensors’ ability to work in dusty and oil-rich environments, without degradation in performance, was particularly beneficial.
The end result was a more efficient assembly process, with reduced adjustment times and improved quality control.
Case Study 3: Magnetic Sensors in Metal Processing
In metal processing, non-contact sensors prove their utility through the use of magnetic sensors.
This case study involves a steel manufacturing plant that used magnetic sensors to monitor and control the thickness of metal sheets being rolled.
Real-Time Monitoring for Quality Control
Magnetic sensors provided real-time data regarding the uniformity of metal sheets.
Before their introduction, quality checks were performed post-production, leading to significant waste if defects were found.
With magnetic sensors, any deviation from the required thickness was immediately corrected, reducing material waste and ensuring consistent quality output.
The Future of Non-Contact Sensor Technology
As industries continue to evolve, the demand for non-contact sensor technology is expected to grow.
Emerging technologies, such as the Internet of Things (IoT) and artificial intelligence (AI), are likely to integrate with these sensors, offering even more sophisticated monitoring and control solutions.
Such advancements promise to enhance predictive maintenance capabilities, further reducing downtime in production lines.
Challenges and Opportunities
Despite their benefits, non-contact sensors are not without challenges.
Interference from environmental factors such as temperature and humidity can affect sensor accuracy.
Overcoming these challenges provides an opportunity for innovation in sensor technology, driving research into more robust and adaptable sensors.
Conclusion
Non-contact sensor technology is a key driver of efficiency and quality in production lines across various industries.
Through specific case studies, we see its impact on improving accuracy, reducing waste, and enhancing product quality.
As the technology advances, it will continue to be a critical component in the digital transformation of manufacturing processes.
資料ダウンロード
QCD調達購買管理クラウド「newji」は、調達購買部門で必要なQCD管理全てを備えた、現場特化型兼クラウド型の今世紀最高の購買管理システムとなります。
ユーザー登録
調達購買業務の効率化だけでなく、システムを導入することで、コスト削減や製品・資材のステータス可視化のほか、属人化していた購買情報の共有化による内部不正防止や統制にも役立ちます。
NEWJI DX
製造業に特化したデジタルトランスフォーメーション(DX)の実現を目指す請負開発型のコンサルティングサービスです。AI、iPaaS、および先端の技術を駆使して、製造プロセスの効率化、業務効率化、チームワーク強化、コスト削減、品質向上を実現します。このサービスは、製造業の課題を深く理解し、それに対する最適なデジタルソリューションを提供することで、企業が持続的な成長とイノベーションを達成できるようサポートします。
オンライン講座
製造業、主に購買・調達部門にお勤めの方々に向けた情報を配信しております。
新任の方やベテランの方、管理職を対象とした幅広いコンテンツをご用意しております。
お問い合わせ
コストダウンが利益に直結する術だと理解していても、なかなか前に進めることができない状況。そんな時は、newjiのコストダウン自動化機能で大きく利益貢献しよう!
(Β版非公開)