- お役立ち記事
- Drilling Techniques and Precision Improvement in Production Machinery
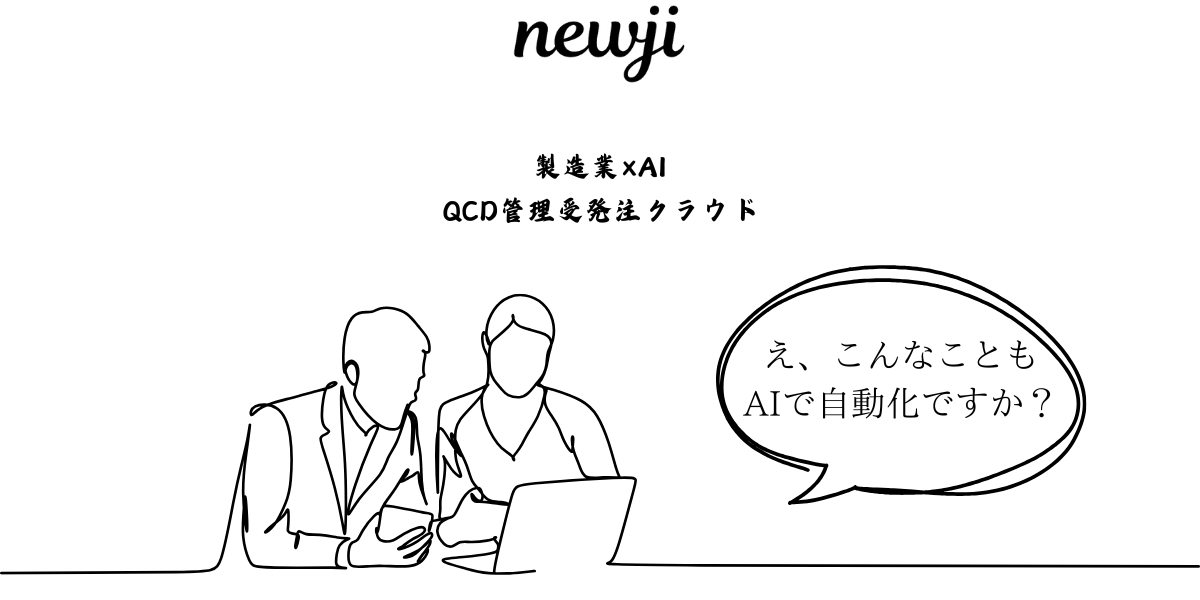
Drilling Techniques and Precision Improvement in Production Machinery
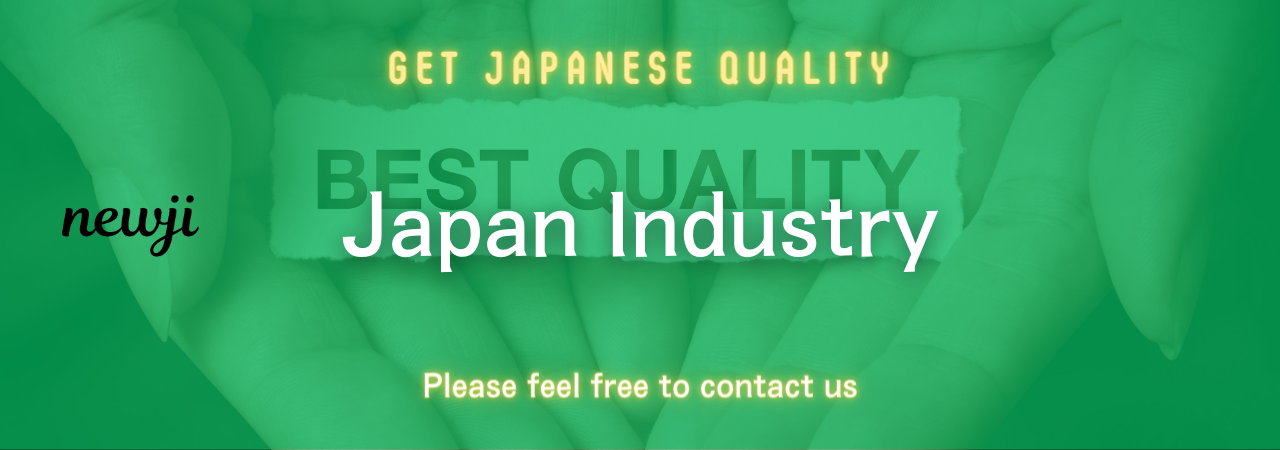
目次
Understanding Drilling Techniques
Drilling is an essential operation in the manufacturing process, providing a means to create holes and cavities in a material.
This technique plays a pivotal role in industries ranging from automotive to aerospace, and even in small-scale crafting projects.
Understanding the different types of drilling techniques and how to optimize them is crucial for enhancing the performance and precision of production machinery.
A fundamental aspect of efficient drilling is selecting the right technique for a specific material and application.
Common drilling methods include rotary drilling, which is frequently used for its straightforward and effective action, and percussion drilling, employed for harder materials like stone or concrete.
Each method utilizes different tools and approaches to cut through materials with minimal errors and maximum efficiency.
Rotary Drilling
Rotary drilling is the most widely used method due to its versatility.
It employs a rotating drill bit that gradually cuts into the material.
This method is popular due to its adaptability across various materials, such as metals, plastics, and wood.
To optimize the precision of rotary drilling, it is essential to use the correct drill bit material, such as high-speed steel or carbide, suitable for the target material.
Furthermore, adjusting the speed and feed rate is crucial in achieving precise and efficient rotary drilling.
A slower speed allows for better heat dissipation and can prevent material deformation or excessive wear on the drill bit.
Operators should also apply the correct amount of pressure to avoid damaging the workpiece or reducing tool life.
Percussion Drilling
Percussion drilling is notably effective for penetrating hard materials.
This method involves delivering rapid, consecutive blows to the drill bit, which transmits the force into the material, thus breaking it apart and allowing penetration.
Commonly used in construction and mineral extraction, percussion drilling requires less rotational power but more energy to deliver the percussive action.
Precision in percussion drilling can be improved by maintaining the alignment and stability of the drilling equipment.
Furthermore, using specialized drill bits, such as tungsten carbide-tipped bits, enhances the efficiency and lifespan of the tools used in this method.
Operators should ensure the drilling machinery is properly calibrated and regularly maintained to reduce the risk of misalignment or mechanical failure.
Improving Precision in Drilling Operations
Precision in drilling operations is crucial for maintaining high-quality standards in production machinery.
Several factors influence the accuracy and quality of drilled holes, including the type of equipment, the sharpness of drill bits, and the stability of the workpiece.
Equipment Calibration
Regular calibration and maintenance of drilling equipment are vital for ensuring consistent precision.
This process involves checking alignment, tightening loose components, and ensuring that the machinery is well-lubricated and free from debris.
Operators should follow a strict maintenance schedule to keep the machinery in peak condition, preventing misalignments and inaccuracies.
Drill Bit Selection and Maintenance
Selecting the correct drill bit for the material is crucial for maintaining precision in drilling operations.
Using worn or damaged drill bits can result in uneven holes and increased risk of tool breakage.
Operators should assess the wear and tear regularly and replace drill bits when necessary.
Additionally, keeping the bits sharp by using proper grinding techniques can extend their lifespan and ensure clean cuts.
Workpiece Stabilization
Ensuring the stability of the workpiece during drilling operations is another critical factor for precision.
Using clamps or vises to secure the workpiece prevents movement that could lead to inaccuracies in drilling.
Additionally, operators should check for proper alignment of the drilled section and use marking tools to guide the drilling process accurately.
Advanced Drilling Technologies
Technological advancements have led to the development of advanced drilling technologies that further enhance precision and efficiency.
These innovations are especially beneficial in high-stakes industries where even minor errors can have significant consequences.
Computer Numerical Control (CNC) Drilling
CNC drilling has revolutionized precision in drilling operations by allowing automated control over the drilling process.
This technology utilizes computer programming to manage the movement of the drill bit with extreme accuracy.
CNC machines are capable of producing complex hole patterns with minimal human intervention, reducing the margin for error.
The precision offered by CNC drilling makes it ideal for industries such as aerospace and automotive, where stringent accuracy is paramount.
Operators must ensure that the CNC programs are correctly configured and regularly updated to maintain the highest level of precision.
Laser Drilling
Laser drilling is another cutting-edge technology that has made significant strides in enhancing precision.
It employs concentrated laser beams to vaporize material and create holes without physical contact.
This technique is remarkably precise and suitable for delicate or heat-sensitive materials that traditional drilling might damage.
While laser drilling offers unparalleled precision, it requires significant investment in equipment and operator training.
However, its application in industries like electronics and medical devices highlights its potential for incredible accuracy and clean cuts.
Conclusion
Drilling techniques and the precision of production machinery are interconnected aspects that require careful consideration.
By understanding the properties of different drilling methods, maintaining equipment, and employing advanced technologies, operators can maximize efficiency and accuracy in drilling operations.
As industries continue to evolve, adopting these practices is crucial for staying competitive and ensuring the highest quality standards.
Continual advancements in technology will likely yield new techniques and improvements, further enhancing the precision and capability of drilling operations in the future.
資料ダウンロード
QCD調達購買管理クラウド「newji」は、調達購買部門で必要なQCD管理全てを備えた、現場特化型兼クラウド型の今世紀最高の購買管理システムとなります。
ユーザー登録
調達購買業務の効率化だけでなく、システムを導入することで、コスト削減や製品・資材のステータス可視化のほか、属人化していた購買情報の共有化による内部不正防止や統制にも役立ちます。
NEWJI DX
製造業に特化したデジタルトランスフォーメーション(DX)の実現を目指す請負開発型のコンサルティングサービスです。AI、iPaaS、および先端の技術を駆使して、製造プロセスの効率化、業務効率化、チームワーク強化、コスト削減、品質向上を実現します。このサービスは、製造業の課題を深く理解し、それに対する最適なデジタルソリューションを提供することで、企業が持続的な成長とイノベーションを達成できるようサポートします。
オンライン講座
製造業、主に購買・調達部門にお勤めの方々に向けた情報を配信しております。
新任の方やベテランの方、管理職を対象とした幅広いコンテンツをご用意しております。
お問い合わせ
コストダウンが利益に直結する術だと理解していても、なかなか前に進めることができない状況。そんな時は、newjiのコストダウン自動化機能で大きく利益貢献しよう!
(Β版非公開)