- お役立ち記事
- Applications and Selection Criteria for Refractory Ceramics in Ceramic Products
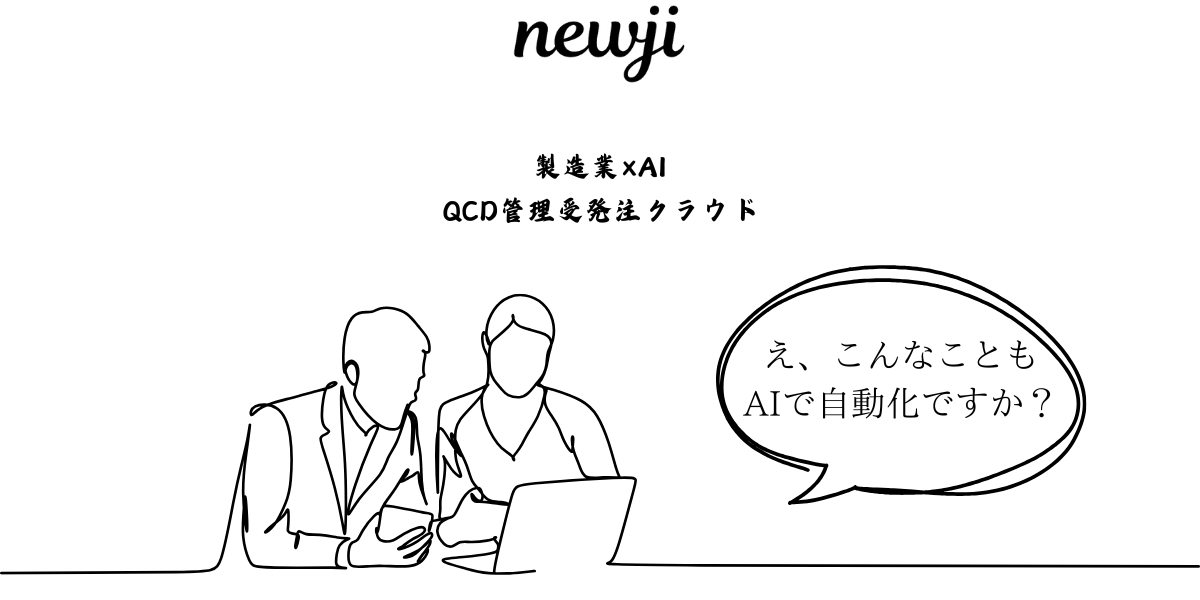
Applications and Selection Criteria for Refractory Ceramics in Ceramic Products
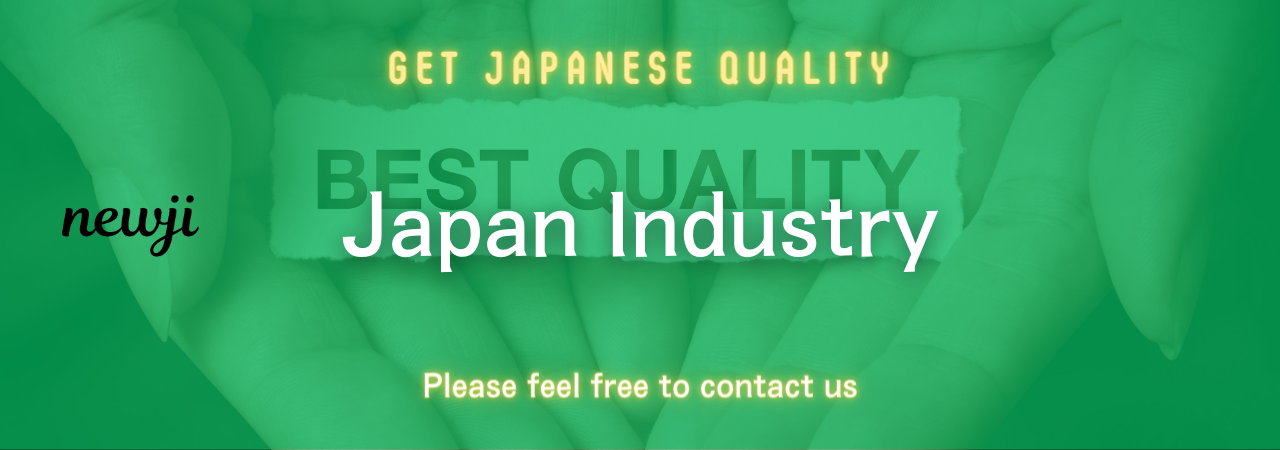
目次
Introduction to Refractory Ceramics
Refractory ceramics are essential components in various industries, especially those involving high-temperature processes.
These materials are engineered to withstand extreme thermal conditions, which is crucial in manufacturing sectors like steel, glass, cement, and energy production.
Refractory ceramics are defined by their ability to maintain structural integrity and function at temperatures exceeding 1000°C.
The unique properties of these ceramics make them indispensable in creating durable, efficient, and high-quality ceramic products that meet industry demands.
Key Applications of Refractory Ceramics
Steel and Metallurgical Industries
The steel industry heavily relies on refractory ceramics for the linings of furnaces, ladles, and crucibles.
These materials ensure that the structures can withstand the intense heat and thermal shock common in metallurgical processes.
Refractory ceramics extend the lifespan of these structures, improving productivity and reducing downtime due to maintenance or material failure.
Glass Manufacturing
In the glass industry, refractory ceramics are critical for maintaining quality and efficiency.
The production process involves high temperatures that can easily reach over 1500°C.
Refractory ceramics are used to line the kilns and ovens, ensuring that the temperature is controlled uniformly and that the final glass products are free of impurities introduced by deteriorating kiln materials.
Cement Production
Cement kilns operate at very high temperatures to break down raw materials into clinker, the key ingredient of cement.
Refractory ceramics provide the thermal resistance necessary to protect kiln linings from wear and erosion, ensuring consistent production quality and reducing operational costs.
Energy Production
In power generation, particularly in coal-fired power plants and gasification plants, refractory ceramics play a significant role.
They are used in boilers, burners, and gasifiers to handle combustion processes that involve high temperatures.
Their resistance to heat and corrosion helps maintain energy efficiency and reduce maintenance overhead.
Types of Refractory Ceramics
Acidic Refractories
These are primarily composed of silica, which makes them suitable for environments where acidic compounds are prevalent.
Common applications include the glass industry and acid regeneration plants.
However, acidic refractories are not ideal for environments that involve basic slags.
Basic Refractories
Made from magnesia or dolomite, basic refractories are used in settings with basic slags, such as steelmaking.
They offer exceptional resistance to chemical attacks from basic compounds, making them ideal for metallurgical applications.
Neutral Refractories
The composition of neutral refractories includes alumina and chromite, which can withstand acidic and basic environments.
This versatility makes them suitable for diverse industrial settings, where the exact nature of impurities is unpredictable.
Selection Criteria for Refractory Ceramics
Thermal Conductivity
The selection of refractory ceramics begins with assessing their thermal conductivity.
Materials with low thermal conductivity are preferred in environments requiring minimal heat loss, such as furnaces and kilns.
Conversely, high thermal conductivity materials are chosen for heat exchangers and other structures where efficient heat transfer is desired.
Chemical Compatibility
Ensuring chemical compatibility is crucial when selecting refractory ceramics for specific applications.
The chosen material must resist degradation from reactive chemicals in the environment, whether acidic or basic.
This is necessary to prevent contamination and maintain structural integrity.
Thermal Expansion
Thermal expansion properties determine how a material behaves under temperature fluctuations.
Refractory ceramics with low thermal expansion rates are favored because they are less likely to crack or spall under thermal shock conditions.
This property is especially important for applications with sudden temperature changes.
Mechanical Strength
The mechanical strength of refractory ceramics affects their ability to withstand physical wear and tear.
Applications involving heavy mechanical loads or abrasion require ceramics with high compressive strength.
This ensures long-lasting performance and reduces maintenance costs.
Challenges and Future Trends
Despite their robustness, refractory ceramics face challenges such as brittleness and difficulty in recycling.
Ongoing research aims to enhance their toughness and develop sustainable production processes.
Future trends focus on nanotechnology to improve the thermal and mechanical properties of refractory ceramics.
In addition, there is a growing interest in developing eco-friendly refractories that reduce environmental impact without compromising performance.
Conclusion
Refractory ceramics are pivotal in industries that operate under high-temperature conditions.
From steel production to energy generation, these materials enable efficient and sustainable manufacturing processes.
Understanding the specific applications and selection criteria is key to choosing the right refractory ceramics for your needs.
As technology progresses, the development and use of these materials will continue to evolve, opening new possibilities for industrial applications.
資料ダウンロード
QCD調達購買管理クラウド「newji」は、調達購買部門で必要なQCD管理全てを備えた、現場特化型兼クラウド型の今世紀最高の購買管理システムとなります。
ユーザー登録
調達購買業務の効率化だけでなく、システムを導入することで、コスト削減や製品・資材のステータス可視化のほか、属人化していた購買情報の共有化による内部不正防止や統制にも役立ちます。
NEWJI DX
製造業に特化したデジタルトランスフォーメーション(DX)の実現を目指す請負開発型のコンサルティングサービスです。AI、iPaaS、および先端の技術を駆使して、製造プロセスの効率化、業務効率化、チームワーク強化、コスト削減、品質向上を実現します。このサービスは、製造業の課題を深く理解し、それに対する最適なデジタルソリューションを提供することで、企業が持続的な成長とイノベーションを達成できるようサポートします。
オンライン講座
製造業、主に購買・調達部門にお勤めの方々に向けた情報を配信しております。
新任の方やベテランの方、管理職を対象とした幅広いコンテンツをご用意しております。
お問い合わせ
コストダウンが利益に直結する術だと理解していても、なかなか前に進めることができない状況。そんな時は、newjiのコストダウン自動化機能で大きく利益貢献しよう!
(Β版非公開)