- お役立ち記事
- Basics of Preventing Alkali-Silica Reactions in Concrete
Basics of Preventing Alkali-Silica Reactions in Concrete
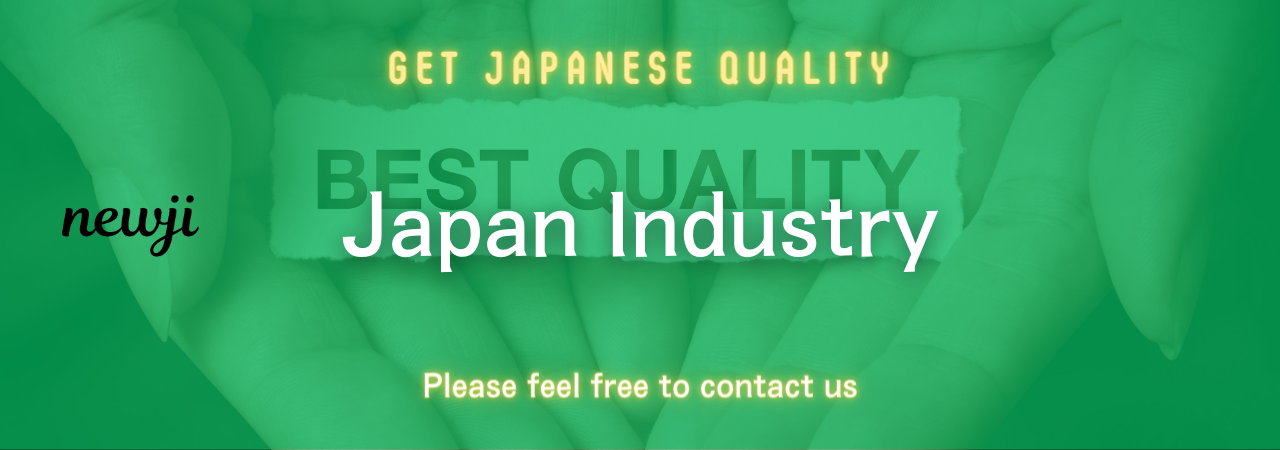
目次
Understanding Alkali-Silica Reactions
Alkali-silica reactions (ASR) are chemical reactions that occur within concrete.
This reaction takes place between the alkaline cement paste and reactive silica found in some aggregates.
When they react, they form a gel that can absorb water and expand, causing internal pressure within the concrete.
This expansion can lead to significant cracking and structural damage over time if not properly managed.
Why Are Alkali-Silica Reactions a Concern?
Understanding the implications of ASR is vital for ensuring the longevity and durability of concrete structures.
These reactions can lead to unsightly cracks and a loss of structural integrity.
In severe cases, it might even result in premature failure of the concrete, which can be costly to repair or replace.
Identifying and managing these reactions can save time and money in maintenance and increase the lifespan of the infrastructure.
Methods to Prevent Alkali-Silica Reactions
There are several strategies to mitigate the risks associated with ASR in concrete structures.
These involve adjusting the components and methods used in the concrete mix.
Choosing the Right Aggregates
One effective way to prevent ASR is to use aggregates that are not reactive.
When selecting aggregates, conducting petrographic analysis or laboratory testing can help identify their reactivity.
Using aggregates known to be less reactive significantly reduces the chance of ASR.
Using Supplementary Cementitious Materials
Supplementary cementitious materials (SCMs), such as fly ash, slag cement, or silica fume, can play a critical role in minimizing ASR.
These materials help reduce the alkalinity in the cement paste, lowering the potential for reaction with any reactive silica present.
Moreover, SCMs can help improve the overall properties of concrete, making it more durable and resistant to other forms of degradation.
Ensuring Low Alkali Content
Limiting the alkali content of the concrete mix is another important factor.
This can be achieved by selecting low-alkali cements or using non-reactive aggregates that do not contribute to the alkalinity.
Regular testing and monitoring during the mixing stage can ensure that alkali levels remain within the desired parameters.
Moisture Control
Since water is a crucial component that facilitates the ASR process, controlling moisture exposure is fundamental.
Concrete should be designed and maintained to minimize water ingress and prevent saturated conditions.
Proper drainage and sealing methods can be employed to ensure moisture control, reducing the likelihood of ASR development.
Monitoring and Maintenance
Preventing ASR doesn’t end with the initial construction; continuous monitoring and maintenance are crucial to ensure long-term performance.
Regular Inspections
Periodic inspection of concrete structures can help detect any early signs of ASR, such as cracking or discoloration.
These inspections allow for early intervention, applying preventative measures before significant damage occurs.
Employing knowledgeable professionals to conduct these inspections can be beneficial in identifying subtle signs that might be overlooked.
Implementing Repair Strategies
In cases where ASR has already begun, repair strategies should be implemented to mitigate further damage.
These may include sealing cracks, applying surface treatments, or using chemical inhibitors designed to slow the reaction process.
Early repair can extend the life of the concrete structure and minimize the extent of the damage.
Innovative Approaches to ASR Prevention
Research and technological advancements continue to provide new methods for preventing and managing ASR.
Advanced Testing Technologies
Recent developments in testing technologies allow for more precise identification of reactive aggregates and potential ASR.
These technologies can provide detailed insights, enabling more informed decision-making when designing concrete mixes.
Development of New Materials
Innovative materials and additives are being developed to further reduce the potential for ASR.
These include advanced SCMs that offer better performance than traditional options.
Such innovations contribute significantly to enhancing concrete durability and mitigating ASR risks.
Conclusion
Preventing alkali-silica reactions in concrete is essential for maintaining the durability and integrity of concrete structures.
By understanding the mechanisms behind ASR and implementing effective preventative strategies, structures can remain safe and functional for their intended lifespan.
From the selection of materials to regular maintenance and innovative solutions, every step plays a vital role in managing ASR.
With careful planning and execution, it’s possible to significantly reduce the occurrence and impact of these reactions, ensuring robust and long-lasting concrete infrastructure.
資料ダウンロード
QCD調達購買管理クラウド「newji」は、調達購買部門で必要なQCD管理全てを備えた、現場特化型兼クラウド型の今世紀最高の購買管理システムとなります。
ユーザー登録
調達購買業務の効率化だけでなく、システムを導入することで、コスト削減や製品・資材のステータス可視化のほか、属人化していた購買情報の共有化による内部不正防止や統制にも役立ちます。
NEWJI DX
製造業に特化したデジタルトランスフォーメーション(DX)の実現を目指す請負開発型のコンサルティングサービスです。AI、iPaaS、および先端の技術を駆使して、製造プロセスの効率化、業務効率化、チームワーク強化、コスト削減、品質向上を実現します。このサービスは、製造業の課題を深く理解し、それに対する最適なデジタルソリューションを提供することで、企業が持続的な成長とイノベーションを達成できるようサポートします。
オンライン講座
製造業、主に購買・調達部門にお勤めの方々に向けた情報を配信しております。
新任の方やベテランの方、管理職を対象とした幅広いコンテンツをご用意しております。
お問い合わせ
コストダウンが利益に直結する術だと理解していても、なかなか前に進めることができない状況。そんな時は、newjiのコストダウン自動化機能で大きく利益貢献しよう!
(Β版非公開)