- お役立ち記事
- Thermal Displacement Countermeasures in High-Precision Machining and Practical Implementation
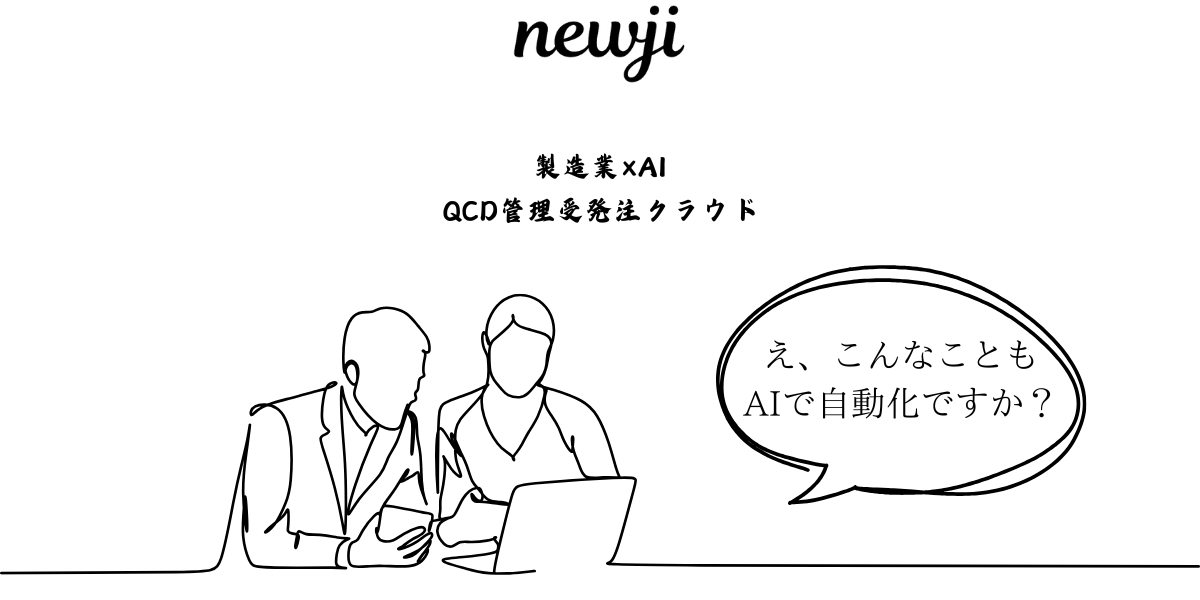
Thermal Displacement Countermeasures in High-Precision Machining and Practical Implementation
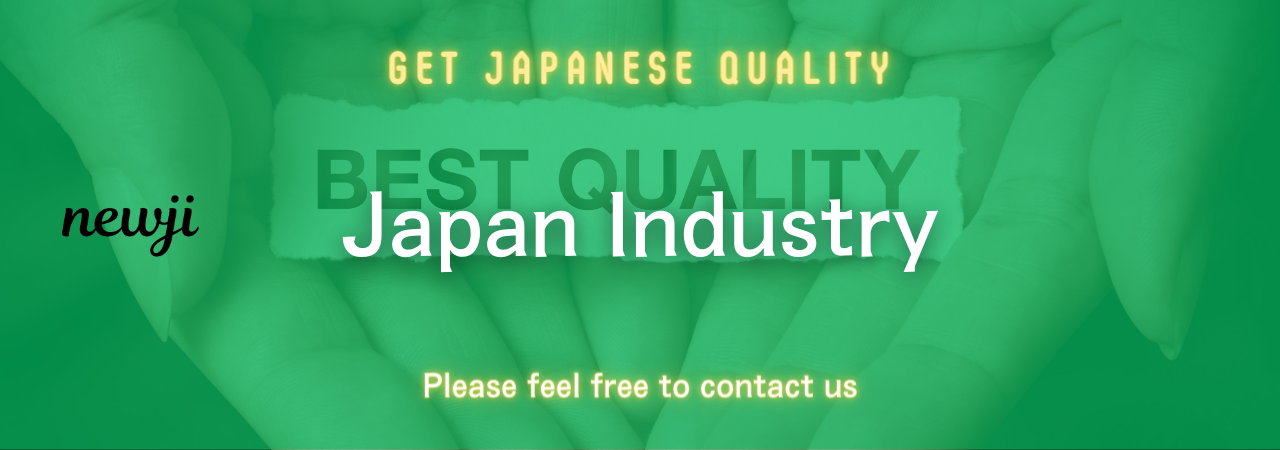
目次
Understanding Thermal Displacement in High-Precision Machining
Thermal displacement is a significant challenge in the realm of high-precision machining.
It occurs when temperature fluctuations cause materials and machinery to expand or contract.
This can lead to deviations in the intended measurements and part dimensions.
When precision is paramount, even minor temperature-induced changes can result in defects or failures in the finished products.
In machining processes, thermal displacement is mainly driven by the heat generated during machining operations.
This can be due to friction between the cutting tools and the workpiece, as well as from the machine’s internal components such as motors and bearings.
The temperature can rise rapidly, necessitating effective thermal management strategies to ensure consistent machining accuracy.
Why Thermal Management Matters
Managing thermal displacement is crucial to maintaining the reliability and accuracy of precision manufacturing processes.
Unaddressed thermal expansion can force costly redesigns and cause quality control issues, impacting an operation’s overall productivity and financial outcomes.
Manufacturers must ensure that their products meet strict quality standards, which means controlling thermal effects is vital.
Effective thermal displacement countermeasures help maintain the dimensional integrity of machined parts.
This is especially important in industries like aerospace, automotive, and electronics, where minute discrepancies can have far-reaching effects.
By preventing thermal-induced inaccuracies, manufacturers can better guarantee customer satisfaction and uphold their reputation for quality.
Strategies for Combating Thermal Displacement
There are several strategies that manufacturers can implement to manage and mitigate thermal displacement in the machining process.
Let’s explore some of the most effective methods:
1. Material Selection
Choosing materials with low thermal expansion coefficients is a fundamental step in minimizing thermal displacement.
Materials like Invar and Zerodur can be used in certain applications due to their stability under temperature changes.
Selecting appropriate materials for both the workpiece and the machinery can significantly reduce thermal deformation risks.
2. Temperature Control Systems
Implementing advanced temperature control systems ensures that the machinery operates within a stable thermal environment.
This includes the use of cooling systems such as lubricants, cutting fluids, and air conditioners.
Maintaining a constant temperature in the machining area can prevent heat-related issues before they start.
3. Preheating Components
Preheating both the workpiece and machine components to their operational temperature can align their expansion properties before machining begins.
This approach minimizes the effects of rapid thermal changes during actual machining.
4. Real-Time Monitoring
Using sensors and monitoring systems can provide real-time data about temperature changes and thermal displacement within the machine.
Advanced analytics can then be used to adjust cutting parameters dynamically, ensuring that precision remains consistent throughout the process.
5. Design Optimization
Designing machine components with thermal considerations in mind can help counteract potential displacement issues.
For example, symmetrical designs can minimize uneven thermal expansion, while dedicated paths for coolant can efficiently remove excess heat from critical areas.
Practical Implementation in Manufacturing
Implementing these countermeasures requires a blend of planning, investment, and continuous improvement.
Let’s examine how practical implementation might look in a modern manufacturing setup:
Collaborative Design Process
Design engineers and machinists need to work closely when selecting materials and designing parts.
Early identification of potential thermal challenges allows for innovative solutions that can be integrated into the design stage, minimizing issues once production begins.
Integration of Smart Technologies
Incorporating smart technologies such as artificial intelligence and machine learning can further enhance thermal management.
These technologies can analyze patterns in thermal data and provide predictive insights, enabling proactive adjustments to machining processes.
Employee Training
Training machine operators and maintenance staff on thermal displacement’s impacts and countermeasures is crucial.
Educated staff can react swiftly to potential thermal issues and implement protocol changes without costly downtime.
Regular Maintenance
Ensuring equipment is well-maintained is fundamental to minimizing thermal anomalies.
Regular inspection, cleaning, and servicing can prevent malfunctions that might lead to unwanted heat generation in machinery.
Conclusion
Thermal displacement poses a challenging barrier to precision in machining, but it is a challenge that manufacturers can overcome with diligence and strategic planning.
Utilizing effective countermeasures, from material selection to advanced monitoring technologies, ensures that manufacturers maintain the high precision necessary for today’s demanding industries.
By investing in solutions that combat thermal displacement, businesses not only safeguard their production quality but also protect their reputation and bottom line.
資料ダウンロード
QCD調達購買管理クラウド「newji」は、調達購買部門で必要なQCD管理全てを備えた、現場特化型兼クラウド型の今世紀最高の購買管理システムとなります。
ユーザー登録
調達購買業務の効率化だけでなく、システムを導入することで、コスト削減や製品・資材のステータス可視化のほか、属人化していた購買情報の共有化による内部不正防止や統制にも役立ちます。
NEWJI DX
製造業に特化したデジタルトランスフォーメーション(DX)の実現を目指す請負開発型のコンサルティングサービスです。AI、iPaaS、および先端の技術を駆使して、製造プロセスの効率化、業務効率化、チームワーク強化、コスト削減、品質向上を実現します。このサービスは、製造業の課題を深く理解し、それに対する最適なデジタルソリューションを提供することで、企業が持続的な成長とイノベーションを達成できるようサポートします。
オンライン講座
製造業、主に購買・調達部門にお勤めの方々に向けた情報を配信しております。
新任の方やベテランの方、管理職を対象とした幅広いコンテンツをご用意しております。
お問い合わせ
コストダウンが利益に直結する術だと理解していても、なかなか前に進めることができない状況。そんな時は、newjiのコストダウン自動化機能で大きく利益貢献しよう!
(Β版非公開)