- お役立ち記事
- Importance and Procedure of Fracture Toughness Testing in Aluminum Products
Importance and Procedure of Fracture Toughness Testing in Aluminum Products
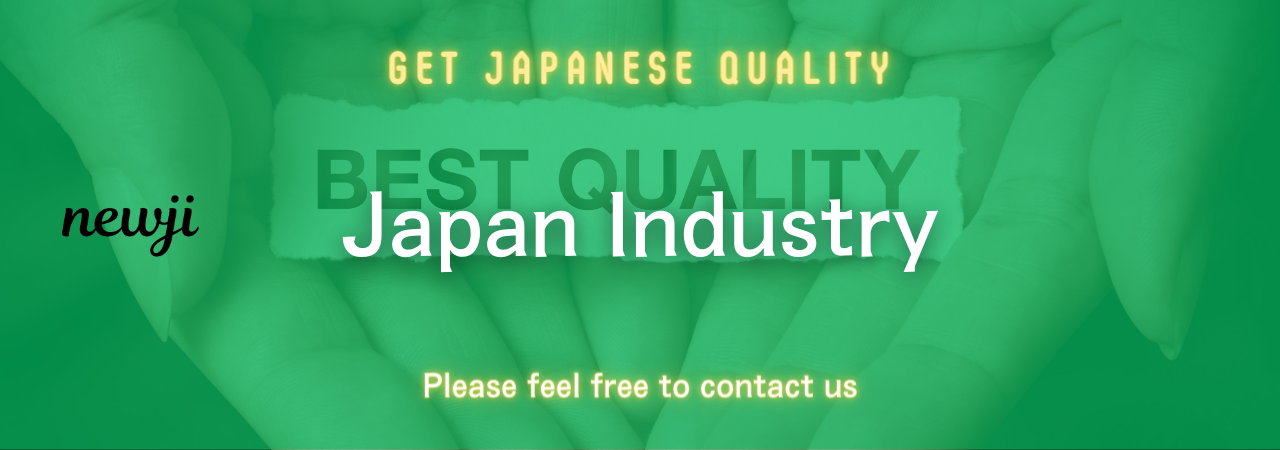
目次
Understanding Fracture Toughness
Fracture toughness is a crucial property in materials engineering, particularly for aluminum products that are extensively used in various industries.
Understanding fracture toughness helps engineers and manufacturers predict how a material will behave under stress and prevent catastrophic failures.
Aluminum, known for its lightweight and good strength-to-weight ratio, is commonly used in aerospace, automotive, and construction.
Assessing its fracture toughness is essential to ensure reliability and safety in these applications.
What is Fracture Toughness?
Fracture toughness is the ability of a material to resist fracture when a crack is present.
Unlike traditional strength tests, which measure how much force a material can withstand before breaking, fracture toughness focuses on a material’s ability to absorb energy and resist propagation of cracks.
This property is tested using specific methods and conditions to simulate real-world stresses and strains.
Why is Fracture Toughness Important for Aluminum Products?
Aluminum is subject to various stresses in many of its applications.
In the aerospace industry, for instance, aircraft components must withstand changes in pressure, temperature, and mechanical stress without cracking.
Automobiles use aluminum for body panels and structural components, where durability and crash resistance are critical.
In construction, aluminum products need to maintain structural integrity under load and environmental conditions.
Understanding and measuring fracture toughness in these contexts helps ensure aluminum components won’t fail unexpectedly.
This is vital for maintaining safety standards and enhancing product performance.
Procedure of Fracture Toughness Testing
Testing fracture toughness requires a specific procedure that follows standard methodologies.
These tests offer precise data engineers can use to analyze aluminum’s performance under stress.
Preparation of Test Specimens
The first step in fracture toughness testing is the preparation of test specimens.
These specimens are usually shaped into a specific form, often a rectangular bar or plate, with a notch.
The notch serves as a controlled defect from which a crack will grow during testing.
Aluminum specimens need to be precisely crafted and machined to ensure consistent results.
Crack Initiation
Crack initiation starts by inducing a small crack, often through fatigue pre-cracking.
This involves applying a cyclic load to a notched specimen until a crack initiates, simulating real-world wear and tear.
This step is crucial; the crack must be small enough not to affect the material’s overall strength until testing but visible enough to propagate under test conditions.
Conducting the Test
The actual fracture toughness test involves applying a load to the specimen in a controlled manner.
This is done using testing equipment like a Universal Testing Machine capable of precise load application.
The load is increased slowly while monitoring the crack until it begins to grow further.
There are several standard testing methods used, such as:
– **Compact Tension Test (CT):** A common test where a compact, rectangular specimen with a notch is loaded in tension.
– **Bend Test:** Involves applying a force to bend the specimen, accounting for toughness under bending stresses.
– **Chevron Notch Test:** Useful for brittle materials, where the notch shape concentrates stress for a controlled crack initiation.
The choice of method depends on the type of aluminum product and its application.
Data and Analysis
During the test, data like force, displacement, and crack length are recorded.
These recordings help determine the fracture toughness value, usually expressed in terms of stress intensity factor K_IC or J-integral.
Engineers analyze this data to understand the material’s behavior and to implement design modifications or material processing adjustments if needed.
Applications of Fracture Toughness Testing
Fracture toughness testing is crucial not only for product safety but also for product development.
By understanding fracture toughness, manufacturers can choose the right aluminum grade for specific applications.
Product Development and Improvement
Testing leads to better product design and material selection.
With data from fracture toughness tests, designers can predict failure modes and improve product safety and longevity.
This proactive approach enhances innovation in industries relying on aluminum for lightweight, durable solutions.
Quality Assurance and Certification
Fracture toughness data is often required for complying with industry standards and certifications.
In sectors like aerospace, adherence to these standards assures that aluminum components meet safety and performance criteria, minimizing risks of failures in service.
Regular testing ensures that products continuously meet these rigorous standards.
Predictive Maintenance and Failure Analysis
Understanding fracture toughness helps in predictive maintenance.
By knowing the limits of aluminum components, engineers can plan maintenance schedules effectively and replace parts before failures occur.
Furthermore, in failure analysis, determining fracture toughness aids in uncovering the failure’s root cause, helping prevent similar events in the future.
Conclusion
Fracture toughness testing remains a backbone in assessing aluminum’s durability and reliability in practical applications.
From the initial preparation of test specimens to the final data analysis, every step ensures aluminum products can withstand substantial stress without catastrophic failure.
By emphasizing fracture toughness, industries can drive innovation, maintain safety, and push the boundaries of aluminum applications further.
Understanding and prioritizing fracture toughness testing is essential in developing better, safer, and more resilient aluminum products.
資料ダウンロード
QCD調達購買管理クラウド「newji」は、調達購買部門で必要なQCD管理全てを備えた、現場特化型兼クラウド型の今世紀最高の購買管理システムとなります。
ユーザー登録
調達購買業務の効率化だけでなく、システムを導入することで、コスト削減や製品・資材のステータス可視化のほか、属人化していた購買情報の共有化による内部不正防止や統制にも役立ちます。
NEWJI DX
製造業に特化したデジタルトランスフォーメーション(DX)の実現を目指す請負開発型のコンサルティングサービスです。AI、iPaaS、および先端の技術を駆使して、製造プロセスの効率化、業務効率化、チームワーク強化、コスト削減、品質向上を実現します。このサービスは、製造業の課題を深く理解し、それに対する最適なデジタルソリューションを提供することで、企業が持続的な成長とイノベーションを達成できるようサポートします。
オンライン講座
製造業、主に購買・調達部門にお勤めの方々に向けた情報を配信しております。
新任の方やベテランの方、管理職を対象とした幅広いコンテンツをご用意しております。
お問い合わせ
コストダウンが利益に直結する術だと理解していても、なかなか前に進めることができない状況。そんな時は、newjiのコストダウン自動化機能で大きく利益貢献しよう!
(Β版非公開)