- お役立ち記事
- Wear Resistance Testing and Evaluation Standards for Aluminum Alloys
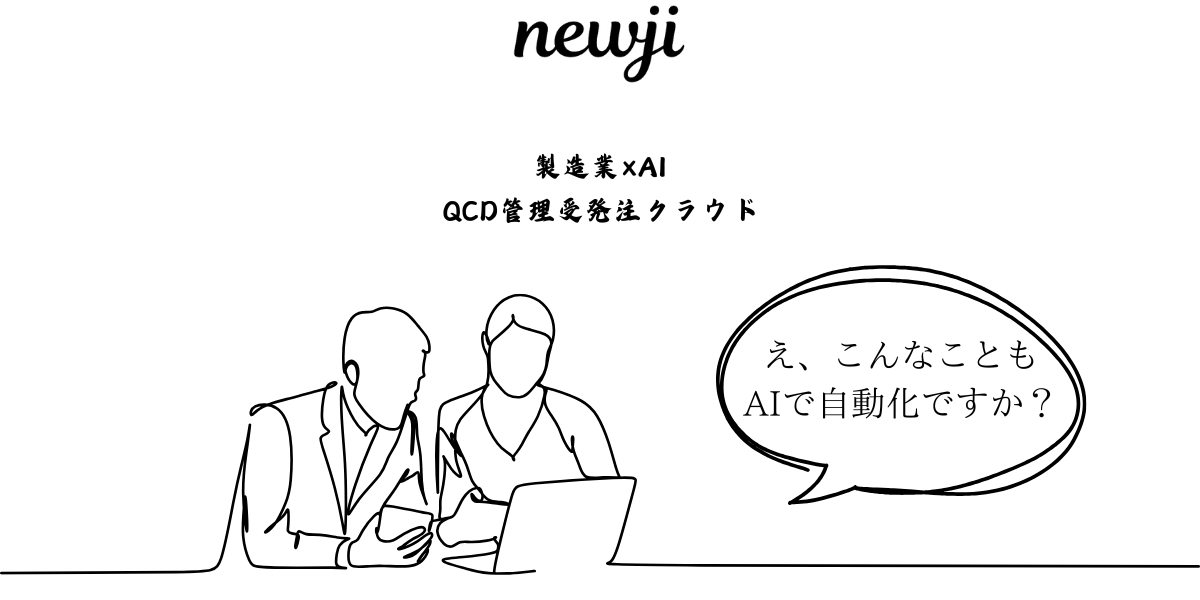
Wear Resistance Testing and Evaluation Standards for Aluminum Alloys
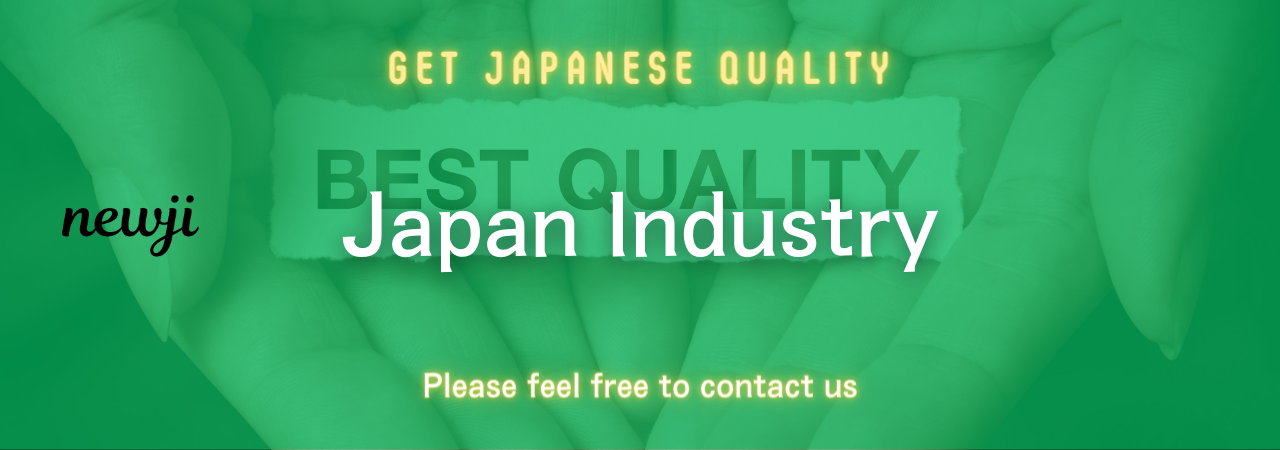
目次
Introduction to Wear Resistance in Aluminum Alloys
Aluminum alloys are widely used in various industries due to their lightweight, corrosion resistance, and excellent mechanical properties.
However, like any material, aluminum alloys are subjected to wear during operation.
Understanding wear resistance is essential for ensuring the longevity and reliability of aluminum components.
Wear resistance testing and evaluation help in determining how aluminum alloys perform under different conditions.
Understanding Wear Resistance
Wear resistance refers to a material’s ability to withstand damage due to frictional contact with other materials.
It is a crucial property for components that experience repetitive contact and movement, such as automotive parts, aircraft structures, and machinery components.
In aluminum alloys, wear resistance is influenced by various factors, including alloy composition, heat treatment, and surface coatings.
Types of Wear
There are several types of wear that aluminum alloys may experience.
These include abrasive wear, adhesive wear, erosive wear, and corrosive wear.
Abrasive wear occurs when hard particles or rough surfaces move across a material, causing it to gradually wear away.
Adhesive wear happens due to the transfer of material between surfaces in contact.
Erosive wear is caused by high-speed particles hitting the material’s surface.
Corrosive wear involves chemical reactions between the material and its environment, leading to deterioration.
Each type of wear requires specific testing methods to evaluate an alloy’s resistance accurately.
Wear Resistance Testing Methods
Several standardized methods exist to assess the wear resistance of aluminum alloys.
These methods simulate real-world wear conditions and help manufacturers understand how an alloy will perform during its service life.
Pinned Disc Test
The pinned disc test is commonly used to evaluate abrasive wear resistance.
In this test, a hard pin is pressed against a rotating aluminum disc under controlled pressure and speed.
The wear track formed on the disc is measured to determine the amount of material loss.
This method provides reliable data on how an aluminum alloy will perform in applications involving sliding contacts.
Ball-on-Disk Test
The ball-on-disk test is similar to the pinned disc test but uses a ball instead of a pin.
This test is ideal for studying adhesive wear resistance.
A ball made of a hard material slides against the aluminum alloy under controlled conditions.
The wear track on the disk and the amount of material transferred to the ball are analyzed.
This test offers insights into how well an alloy can withstand adhesive wear conditions.
Jet Erosion Test
The jet erosion test evaluates the erosive wear resistance of aluminum alloys.
A high-speed jet of abrasive particles is directed onto the material’s surface at a specific angle.
The material loss is measured to determine the erosion rate.
This test is particularly useful for applications where aluminum components are exposed to fluid flow with suspended particles, such as turbines and pumps.
Evaluation Standards for Aluminum Alloys
To ensure consistency and reliability in wear resistance testing, several standards have been developed by organizations like ASTM International and ISO.
ASTM Standards
ASTM International provides several standards related to wear testing of metal materials, including aluminum alloys.
One important standard is ASTM G99, which covers the ball-on-disk test method for evaluating sliding wear.
It outlines the procedures for carrying out the test and reporting the results.
Another relevant standard is ASTM G65, which focuses on the dry sand/rubber wheel abrasion test.
This standard is used to determine the resistance of materials to abrasive wear.
ISO Standards
ISO has developed standards that complement ASTM’s protocols.
For example, ISO 20808 provides guidelines for the ball-on-disk test method used worldwide.
This ensures that results are comparable across international borders.
These standards aim to establish consistent testing conditions, ensuring that results are repeatable and actionable.
Adhering to these standards is crucial for manufacturers who need reliable data to improve wear-resistant properties in aluminum alloys.
Factors Affecting Wear Resistance in Aluminum Alloys
Several factors influence the wear resistance of aluminum alloys:
Alloy Composition
The composition of an aluminum alloy can significantly impact its wear resistance.
Alloys with high hardness tend to perform better against abrasive wear.
The presence of certain elements, such as silicon and copper, can enhance wear resistance by strengthening the alloy’s microstructure.
Heat Treatment
Heat treatment processes, such as quenching and aging, can improve the wear resistance of aluminum alloys by altering their mechanical properties.
Aging, for instance, can increase the hardness and strength of an alloy, thereby enhancing its resistance to different types of wear.
Surface Coatings
Applying surface coatings is an effective way to improve the wear resistance of aluminum alloys.
Techniques like anodizing, hard coatings, and thermal spraying create a protective layer on the surface that reduces wear during operation.
These coatings prolong the lifespan of components and maintain their integrity in demanding conditions.
Conclusion
Understanding and evaluating the wear resistance of aluminum alloys are vital for industries that rely heavily on these versatile materials.
Through effective testing using standardized methods, manufacturers can gain valuable insights and make informed decisions about material selection and treatments.
By implementing accurate wear resistance testing and evaluation, industries can ensure that aluminum alloy components meet performance expectations and deliver long-lasting results in various applications.
資料ダウンロード
QCD調達購買管理クラウド「newji」は、調達購買部門で必要なQCD管理全てを備えた、現場特化型兼クラウド型の今世紀最高の購買管理システムとなります。
ユーザー登録
調達購買業務の効率化だけでなく、システムを導入することで、コスト削減や製品・資材のステータス可視化のほか、属人化していた購買情報の共有化による内部不正防止や統制にも役立ちます。
NEWJI DX
製造業に特化したデジタルトランスフォーメーション(DX)の実現を目指す請負開発型のコンサルティングサービスです。AI、iPaaS、および先端の技術を駆使して、製造プロセスの効率化、業務効率化、チームワーク強化、コスト削減、品質向上を実現します。このサービスは、製造業の課題を深く理解し、それに対する最適なデジタルソリューションを提供することで、企業が持続的な成長とイノベーションを達成できるようサポートします。
オンライン講座
製造業、主に購買・調達部門にお勤めの方々に向けた情報を配信しております。
新任の方やベテランの方、管理職を対象とした幅広いコンテンツをご用意しております。
お問い合わせ
コストダウンが利益に直結する術だと理解していても、なかなか前に進めることができない状況。そんな時は、newjiのコストダウン自動化機能で大きく利益貢献しよう!
(Β版非公開)