- お役立ち記事
- Essential Joining Technologies for Metal Products: Basics of Friction Stir Welding
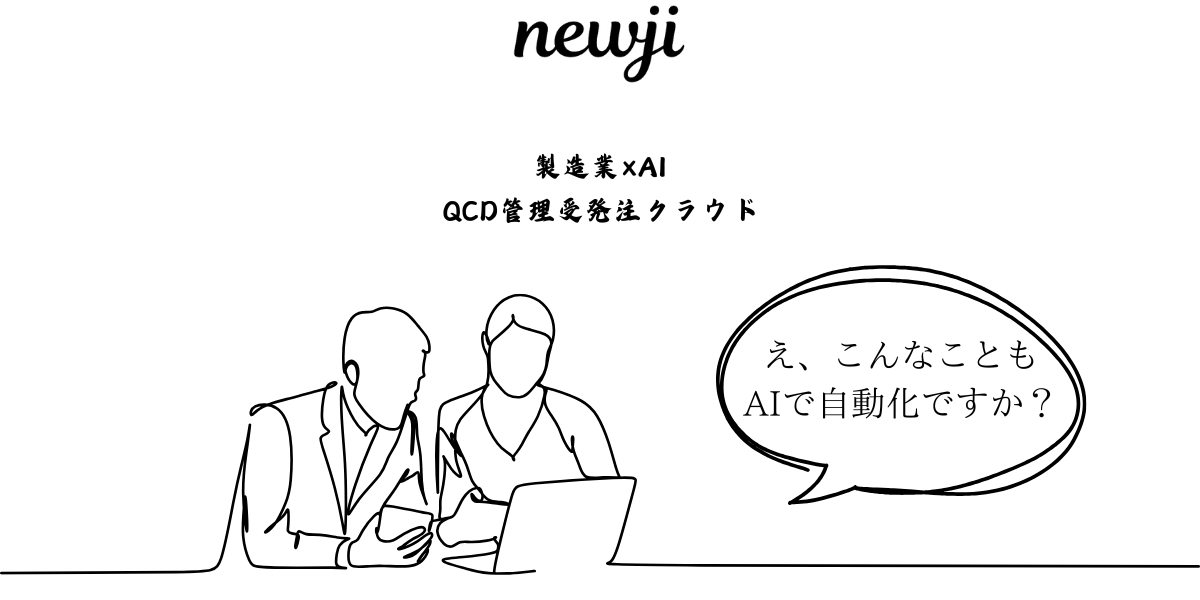
Essential Joining Technologies for Metal Products: Basics of Friction Stir Welding
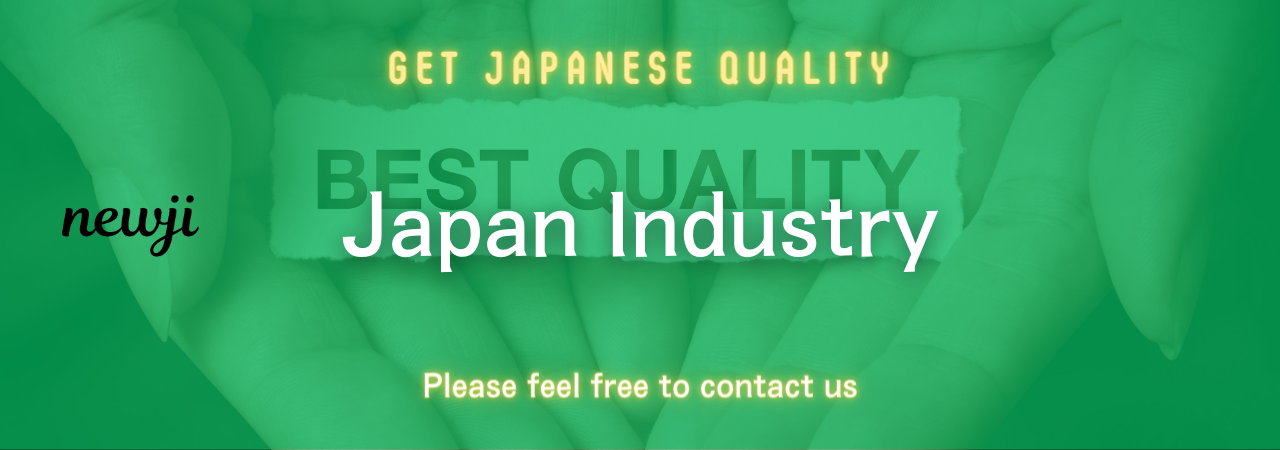
目次
What is Friction Stir Welding?
Friction Stir Welding (FSW) is an innovative and widely used solid-state joining process that was invented in 1991 by The Welding Institute (TWI) in the United Kingdom.
This process is primarily used for welding metal materials, offering a unique advantage by avoiding the melting of the base materials.
FSW utilizes a non-consumable rotating tool that plunges into the joint area between two workpieces, generating frictional heat that softens the material and allows them to be forged together.
The materials are joined as the tool progresses along the seam, creating a high-integrity joint.
How Does Friction Stir Welding Work?
The FSW process is simple yet highly effective.
It begins with the preparation of the metal plates, which are firmly clamped to prevent movement during welding.
A specially designed cylindrical tool with a profiled pin is rotated and slowly inserted into the workpieces at the joint line.
The friction between the tool and the material generates heat, causing the material to soften without reaching the melting point.
As the tool traverses along the joint, it mechanically stirs the softened material together, creating a solid-state weld.
The Importance of Tool Design
The tool design in FSW is crucial as it directly impacts the quality of the weld.
The tool comprises two main parts: the shoulder and the pin.
The shoulder generates most of the heat through friction, while the pin stirs the softened material.
Different materials and joint designs require various tool configurations, making tool design a critical factor for achieving optimal results.
Advantages of Friction Stir Welding
Friction Stir Welding offers numerous advantages over traditional welding techniques.
Firstly, it is an environmentally friendly process, as it does not use external heat sources or filler materials that can produce harmful emissions.
FSW is a green technology that aligns with sustainable manufacturing practices.
Secondly, FSW produces high-quality welds with excellent mechanical properties, including high fatigue resistance and low distortion.
The absence of melting eliminates problems such as porosity and cracking, common in conventional welding processes.
FSW can join a variety of materials, including aluminum, copper, and their alloys, making it versatile for different industrial applications.
Cost-Effectiveness and Efficiency
FSW is known for its cost-effectiveness and efficiency.
The process is typically faster than conventional welding techniques, reducing production time and costs.
Moreover, the equipment and tooling used in FSW require less maintenance, minimizing downtime.
This welding method is particularly advantageous for joining long-length joints that would be time-consuming with traditional methods.
Applications of Friction Stir Welding
FSW is extensively used in various industries due to its ability to produce high-strength, high-quality joints.
In the aerospace industry, it is used for constructing lightweight, durable structures that must withstand the demanding conditions of flight.
Similarly, the automotive industry benefits from FSW by reducing the weight of vehicles while maintaining structural integrity.
FSW is also utilized in the shipbuilding industry, where it aids in creating large, welded sections without the need for fillers, improving the durability and lifespan of ships.
In electronics, it is employed to join copper components, ensuring high thermal and electrical conductivity.
Future Prospects of Friction Stir Welding
The scope for future advancements in Friction Stir Welding is vast.
With ongoing research and development, FSW is expected to expand its applicability to a broader range of materials, including harder metals and complex geometries.
Innovations in tool design and process monitoring are anticipated to further improve weld quality and process efficiency.
As manufacturers continue to seek sustainable and cost-effective solutions, FSW is poised to play a significant role in the future of metal joining technologies.
Challenges and Limitations
While FSW boasts many advantages, it also faces certain challenges and limitations.
One primary limitation is the initial setup cost, as the FSW machines and tools can be expensive.
Additionally, the process is currently limited to specific materials that can be softened by the generated frictional heat.
Joining certain high-temperature materials remains a significant challenge.
Moreover, the requirement for rigid clamping and tooling can be a hindrance in some applications.
Developing portable FSW systems could expand its use in more dynamic environments.
Conclusion
Friction Stir Welding is a groundbreaking technology that has transformed the way metal products are joined.
Its ability to produce strong, defect-free welds while being environmentally friendly makes it a desirable method for various manufacturing industries.
Despite its current limitations, continued advancements in FSW technology and process adaptability are likely to overcome these challenges.
As industries continue to prioritize sustainable and efficient manufacturing processes, Friction Stir Welding’s relevance and applicability will undoubtedly grow, cementing its place as a vital tool in metal joining technologies.
資料ダウンロード
QCD調達購買管理クラウド「newji」は、調達購買部門で必要なQCD管理全てを備えた、現場特化型兼クラウド型の今世紀最高の購買管理システムとなります。
ユーザー登録
調達購買業務の効率化だけでなく、システムを導入することで、コスト削減や製品・資材のステータス可視化のほか、属人化していた購買情報の共有化による内部不正防止や統制にも役立ちます。
NEWJI DX
製造業に特化したデジタルトランスフォーメーション(DX)の実現を目指す請負開発型のコンサルティングサービスです。AI、iPaaS、および先端の技術を駆使して、製造プロセスの効率化、業務効率化、チームワーク強化、コスト削減、品質向上を実現します。このサービスは、製造業の課題を深く理解し、それに対する最適なデジタルソリューションを提供することで、企業が持続的な成長とイノベーションを達成できるようサポートします。
オンライン講座
製造業、主に購買・調達部門にお勤めの方々に向けた情報を配信しております。
新任の方やベテランの方、管理職を対象とした幅広いコンテンツをご用意しております。
お問い合わせ
コストダウンが利益に直結する術だと理解していても、なかなか前に進めることができない状況。そんな時は、newjiのコストダウン自動化機能で大きく利益貢献しよう!
(Β版非公開)