- お役立ち記事
- Unveiling the Role of AE Sensors in Revolutionizing Japanese Manufacturing Techniques
Unveiling the Role of AE Sensors in Revolutionizing Japanese Manufacturing Techniques
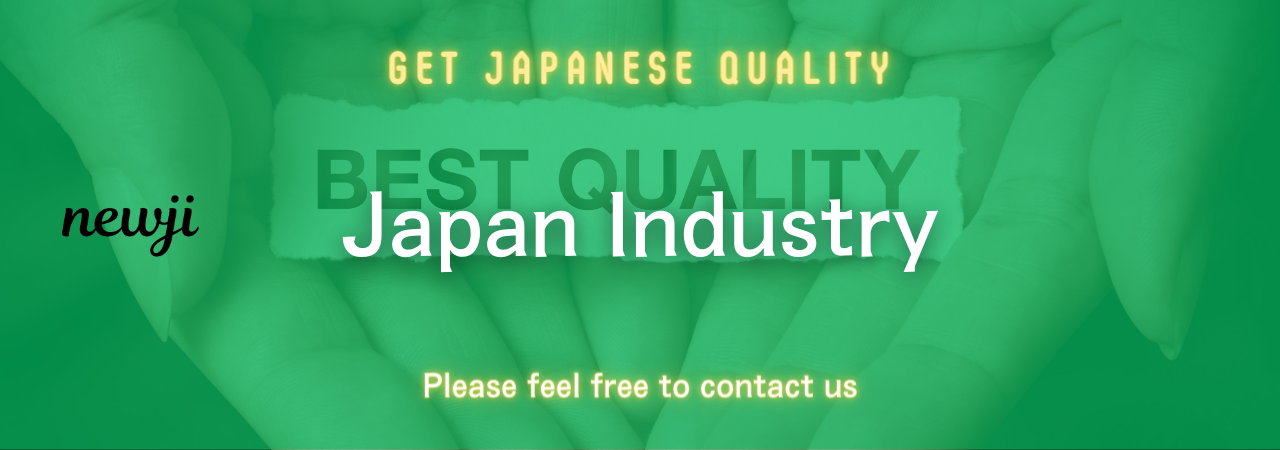
目次
Introduction to AE Sensors in Japanese Manufacturing
Japanese manufacturing has long been recognized for its precision, efficiency, and innovation. A critical component of this success is the integration of advanced technologies that optimize production processes and ensure high-quality outcomes. Among these technologies, Acoustic Emission (AE) sensors have emerged as pivotal tools in revolutionizing manufacturing techniques. This article explores the role of AE sensors in Japanese manufacturing, delving into their functionalities, benefits, challenges, and best practices for procurement and integration.
Understanding Acoustic Emission (AE) Sensors
How AE Sensors Work
Acoustic Emission sensors are devices that detect transient elastic waves produced by the rapid release of energy from localized sources within a material. These sensors monitor the stress and strain within machinery and structures by capturing high-frequency sound waves generated during production processes. By analyzing these acoustic signals, AE sensors can identify defects, monitor structural health, and predict equipment failures, thereby enabling proactive maintenance and quality control.
Key Features of AE Sensors
AE sensors are characterized by their sensitivity to high-frequency acoustic waves, typically ranging from 20 kHz to 1 MHz. They are designed to operate in various environments, offering robust performance in industrial settings. Key features include:
– **High Sensitivity:** Capable of detecting minute acoustic emissions.
– **Wide Frequency Range:** Suitable for diverse applications across manufacturing processes.
– **Durability:** Engineered to withstand harsh industrial conditions.
– **Real-Time Monitoring:** Provides immediate feedback for prompt decision-making.
– **Compatibility:** Easily integrates with existing monitoring systems and data analysis software.
Impact of AE Sensors on Manufacturing Techniques
Enhancing Quality Control
Quality control is paramount in Japanese manufacturing, where precision is non-negotiable. AE sensors play a vital role in maintaining high standards by continuously monitoring production processes. They detect anomalies and defects at early stages, allowing for timely interventions that prevent defective products from reaching the market. This real-time quality assurance minimizes waste, reduces rework, and ensures consistency in product quality.
Improving Production Efficiency
By providing detailed insights into machinery performance, AE sensors help optimize production efficiency. They identify bottlenecks, monitor equipment health, and ensure that machines operate within optimal parameters. This data-driven approach enables manufacturers to streamline operations, reduce downtime, and enhance overall productivity. Consequently, companies can achieve higher output levels without compromising on quality.
Enabling Predictive Maintenance
Maintenance strategies have evolved from reactive to proactive, thanks to AE sensors. Predictive maintenance leverages the data captured by AE sensors to forecast potential equipment failures before they occur. This predictive capability allows for scheduled maintenance activities, minimizing unexpected downtime and extending the lifespan of machinery. In the highly competitive manufacturing landscape of Japan, such efficiencies are crucial for maintaining a competitive edge.
Advantages of Implementing AE Sensors in Japanese Manufacturing
Increased Precision and Reliability
AE sensors enhance the precision of manufacturing processes by providing accurate and timely data on equipment performance and product integrity. This increased reliability ensures that manufacturing operations are consistently aligned with stringent quality standards, a hallmark of Japanese manufacturing excellence.
Cost Savings through Early Defect Detection
Early detection of defects translates into significant cost savings. By identifying issues before they escalate, manufacturers can avoid costly rework, material wastage, and potential recalls. The proactive nature of AE sensors ensures that problems are addressed promptly, maintaining operational efficiency and financial health.
Enhanced Supplier Relationships
Integrating AE sensors fosters stronger relationships with suppliers, particularly Japanese ones known for their technological prowess. Reliable quality control and efficient production processes build trust and facilitate smoother collaborations. This synergy not only enhances product quality but also drives mutual growth and innovation.
Challenges and Disadvantages of AE Sensors
Initial Investment and Implementation Costs
The adoption of AE sensors involves substantial initial investment. Costs encompass the purchase of advanced sensor technology, installation, and integration with existing systems. For some manufacturers, especially small and medium-sized enterprises, these expenses can be prohibitive, necessitating careful financial planning and justification based on long-term benefits.
Technical Complexity and Training Requirements
AE sensors require specialized knowledge for effective operation and data interpretation. Implementing these systems demands comprehensive training for personnel, which can be time-consuming and resource-intensive. Moreover, the technical complexity may pose challenges in integrating AE sensors with established manufacturing processes, requiring ongoing support and expertise.
Integration with Existing Systems
Seamless integration of AE sensors with existing manufacturing systems is critical for maximizing their benefits. However, this integration can be challenging due to compatibility issues, data interoperability, and the need for customized solutions. Manufacturers must invest in appropriate infrastructure and possibly upgrade existing systems to fully leverage the capabilities of AE sensors.
Procurement and Purchasing of AE Sensors from Japanese Suppliers
Benefits of Sourcing from Japanese Manufacturers
Japanese suppliers are renowned for their high-quality manufacturing standards, technological innovation, and reliability. Procuring AE sensors from Japanese manufacturers ensures access to cutting-edge technology and robust performance. Additionally, Japanese suppliers often provide exceptional customer service, technical support, and customization options, enhancing the overall value proposition for purchasers.
Evaluating Supplier Capabilities
When sourcing AE sensors, evaluating supplier capabilities is essential. Key factors include:
– **Technical Expertise:** Assessing the supplier’s knowledge and experience with AE sensor technology.
– **Quality Assurance:** Ensuring adherence to international quality standards and certifications.
– **Production Capacity:** Confirming the supplier can meet demand without compromising quality.
– **Innovation:** Evaluating the supplier’s commitment to research and development for continuous improvement.
– **Customer Support:** Ensuring availability of comprehensive support services post-purchase.
Negotiation Techniques for Securing the Best Deals
Effective negotiation with Japanese suppliers involves understanding their business culture and establishing mutual trust. Key techniques include:
– **Building Relationships:** Establishing a strong rapport through regular communication and respectful interactions.
– **Understanding Value Propositions:** Recognizing the unique value offered by suppliers and aligning negotiations accordingly.
– **Long-Term Perspective:** Focusing on long-term partnerships rather than short-term gains.
– **Transparency:** Being clear about requirements, expectations, and constraints to foster trust.
– **Flexibility:** Being open to flexible terms that benefit both parties, such as volume discounts or customized solutions.
Market Conditions for AE Sensors in Japan
Current Trends and Innovations
The AE sensor market in Japan is characterized by continuous innovation and adoption of advanced technologies. Current trends include the integration of Internet of Things (IoT) capabilities, enhancing real-time data analytics, and leveraging artificial intelligence (AI) for predictive maintenance. Manufacturers are increasingly seeking smart AE sensors that offer greater connectivity, automation, and data-driven insights to stay competitive.
Competitive Landscape
The competitive landscape for AE sensors in Japan features a mix of established industry leaders and emerging innovators. Companies compete based on technological advancements, product reliability, customer service, and pricing strategies. Collaboration between manufacturers and technology providers is common, driving collective growth and fostering a dynamic market environment.
Future Outlook
The future of AE sensors in Japanese manufacturing looks promising, with anticipated growth driven by the rising demand for automation, quality control, and predictive maintenance. Continued advancements in sensor technology, coupled with increasing adoption across various manufacturing sectors, are expected to expand the market. Additionally, the emphasis on sustainability and efficiency will further propel the integration of AE sensors into manufacturing processes.
Best Practices for Integrating AE Sensors into Manufacturing Processes
Assessing Organizational Needs
Before integrating AE sensors, it is crucial to assess the specific needs and objectives of the organization. This involves identifying key areas where AE sensors can add value, such as quality control, predictive maintenance, or process optimization. A clear understanding of organizational requirements ensures that the integration of AE sensors aligns with overall business goals and delivers tangible benefits.
Ensuring Compatibility and Integration
Successful integration of AE sensors requires ensuring compatibility with existing systems and processes. This may involve upgrading infrastructure, adopting compatible data analysis tools, and customizing sensor configurations to fit specific applications. Collaboration with suppliers and technology partners is essential to address any integration challenges and achieve seamless implementation.
Training and Supporting Staff
Comprehensive training programs are essential to equip staff with the necessary skills to operate AE sensors effectively. Training should cover sensor installation, data interpretation, maintenance procedures, and troubleshooting. Ongoing support and professional development opportunities help maintain proficiency and adaptability as technology evolves.
Continuous Monitoring and Optimization
The benefits of AE sensors are maximized through continuous monitoring and optimization. Regularly analyzing sensor data enables manufacturers to identify trends, assess performance, and make informed decisions. Continuous improvement practices, supported by AE sensor insights, lead to sustained operational excellence and adaptability in a dynamic manufacturing landscape.
Case Studies: Successful Implementation of AE Sensors in Japanese Manufacturing
Several Japanese manufacturing companies have successfully implemented AE sensors, demonstrating significant improvements in quality control, efficiency, and maintenance. For instance, a leading automotive manufacturer integrated AE sensors into its assembly lines to monitor weld integrity. This implementation resulted in a noticeable reduction in defects, enhanced product quality, and decreased rework costs. Another example is a semiconductor manufacturer that utilized AE sensors for predictive maintenance, leading to minimized downtime and extended equipment lifespan. These case studies illustrate the transformative impact of AE sensors on manufacturing operations, highlighting their role in driving innovation and excellence.
Conclusion
Acoustic Emission sensors are revolutionizing Japanese manufacturing by enhancing quality control, improving production efficiency, and enabling predictive maintenance. Despite challenges such as initial investment costs and technical complexities, the advantages of implementing AE sensors—such as increased precision, cost savings, and strengthened supplier relationships—are substantial. By sourcing from reputable Japanese suppliers and adhering to best practices for integration, manufacturers can fully leverage the potential of AE sensors. As the market continues to evolve with advancements in technology, AE sensors will play an increasingly vital role in sustaining the competitive edge and excellence that characterize Japanese manufacturing.
資料ダウンロード
QCD調達購買管理クラウド「newji」は、調達購買部門で必要なQCD管理全てを備えた、現場特化型兼クラウド型の今世紀最高の購買管理システムとなります。
ユーザー登録
調達購買業務の効率化だけでなく、システムを導入することで、コスト削減や製品・資材のステータス可視化のほか、属人化していた購買情報の共有化による内部不正防止や統制にも役立ちます。
NEWJI DX
製造業に特化したデジタルトランスフォーメーション(DX)の実現を目指す請負開発型のコンサルティングサービスです。AI、iPaaS、および先端の技術を駆使して、製造プロセスの効率化、業務効率化、チームワーク強化、コスト削減、品質向上を実現します。このサービスは、製造業の課題を深く理解し、それに対する最適なデジタルソリューションを提供することで、企業が持続的な成長とイノベーションを達成できるようサポートします。
オンライン講座
製造業、主に購買・調達部門にお勤めの方々に向けた情報を配信しております。
新任の方やベテランの方、管理職を対象とした幅広いコンテンツをご用意しております。
お問い合わせ
コストダウンが利益に直結する術だと理解していても、なかなか前に進めることができない状況。そんな時は、newjiのコストダウン自動化機能で大きく利益貢献しよう!
(Β版非公開)