- お役立ち記事
- Unlocking Japan’s Manufacturing Potential: The Role of Industrial Robots in Revolutionizing Production
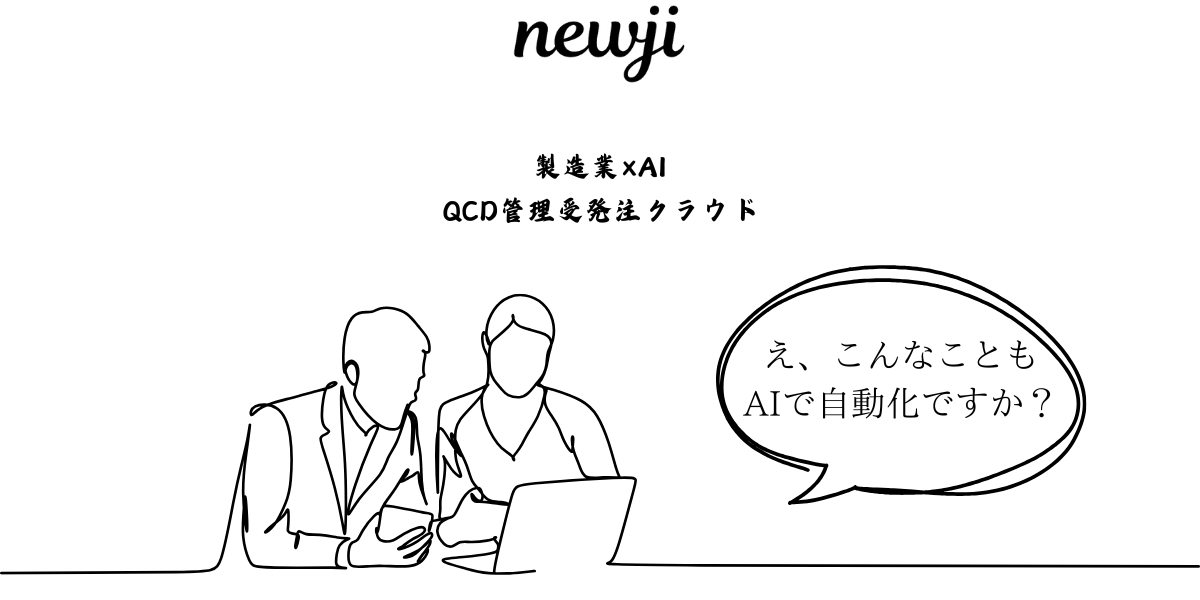
Unlocking Japan’s Manufacturing Potential: The Role of Industrial Robots in Revolutionizing Production
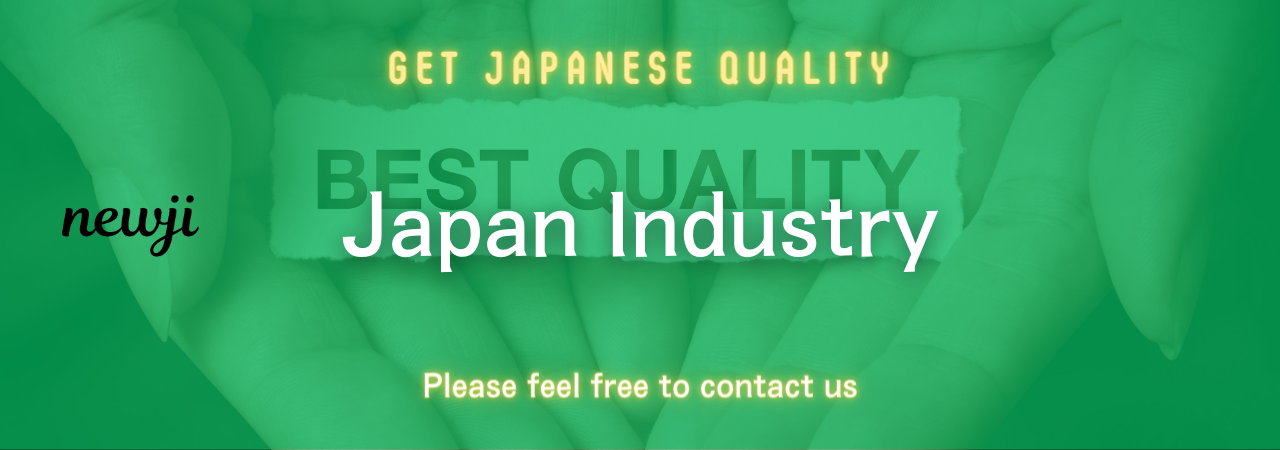
目次
Introduction to Japan’s Manufacturing Excellence
Japan has long been recognized as a global leader in manufacturing.
The nation’s commitment to quality, innovation, and efficiency has set benchmarks across various industries.
One of the pivotal factors contributing to Japan’s manufacturing prowess is the integration of industrial robots in production processes.
This article delves into the role of industrial robots in revolutionizing production within Japan’s manufacturing landscape.
We will explore the advantages and disadvantages, procurement and purchasing strategies, supplier negotiation techniques, market conditions, and best practices that underpin this transformation.
The Rise of Industrial Robots in Japanese Manufacturing
The adoption of industrial robots in Japan has surged over the past few decades.
This trend is driven by the need for increased productivity, precision, and the ability to maintain high-quality standards.
Japanese manufacturers are leveraging robotics to enhance various aspects of production, from assembly lines to complex manufacturing tasks.
Historical Context
Japan’s journey with industrial robots began in the 1970s.
Initially, robots were primarily used for simple, repetitive tasks.
However, advancements in technology have expanded their capabilities significantly.
Today, robots handle sophisticated operations, collaborate with human workers, and adapt to changing production needs.
Technological Advancements
Recent advancements in robotics technology have been instrumental in this transformation.
Improved sensors, artificial intelligence, and machine learning have enabled robots to perform more complex and adaptive tasks.
Collaborative robots, or cobots, work alongside humans, providing assistance and increasing overall efficiency.
These technological strides have solidified Japan’s position at the forefront of robotic manufacturing.
Advantages of Industrial Robots in Production
The integration of industrial robots into production processes offers numerous benefits.
These advantages span operational efficiency, quality control, workforce dynamics, and financial performance.
Enhanced Productivity and Efficiency
Industrial robots operate with high precision and can perform tasks faster than human workers.
They work tirelessly without the need for breaks, resulting in significantly increased production rates.
This heightened productivity allows manufacturers to meet growing demand and maintain competitive advantage.
Improved Quality and Consistency
Robots ensure uniformity and accuracy in manufacturing processes.
They minimize human errors, leading to consistent product quality.
This reliability is crucial for maintaining brand reputation and meeting stringent industry standards.
Cost Savings
While the initial investment in robotics can be substantial, the long-term cost savings are considerable.
Robots reduce labor costs, minimize waste, and enhance energy efficiency.
Additionally, they can operate in harsh environments, reducing the need for specialized safety measures.
Workforce Augmentation
Instead of replacing human workers, industrial robots often complement them.
They handle repetitive and physically demanding tasks, allowing employees to focus on more strategic and creative aspects of production.
This synergy fosters a more engaging and productive work environment.
Disadvantages and Challenges
Despite their advantages, the implementation of industrial robots presents certain challenges.
Understanding these drawbacks is essential for making informed procurement and purchasing decisions.
High Initial Investment
The cost of acquiring and integrating industrial robots can be prohibitive, especially for small and medium-sized enterprises (SMEs).
Purchasing robots involves not only the cost of the machines but also expenses related to installation, training, and maintenance.
Technical Complexity
Operating and maintaining industrial robots requires specialized knowledge and skills.
There is a steep learning curve associated with robotics technology, necessitating ongoing training and development for the workforce.
Job Displacement Concerns
The automation of tasks previously handled by humans can lead to concerns about job displacement.
While robots enhance efficiency, they may reduce the demand for certain manual labor roles, impacting the workforce dynamics.
Integration Issues
Integrating robots into existing production systems can be complex.
Compatibility with current machinery, software, and workflows must be carefully managed to ensure seamless operation and avoid disruptions.
Procurement and Purchasing Strategies for Industrial Robots
Effectively procuring industrial robots is crucial for successful implementation.
This section outlines key strategies and considerations for procurement and purchasing within the Japanese manufacturing context.
Assessing Needs and Requirements
Before procuring robots, manufacturers must conduct a thorough assessment of their production needs.
Identifying specific tasks, desired outcomes, and performance metrics ensures that the selected robots align with operational goals.
Supplier Selection and Evaluation
Choosing the right supplier is paramount for procurement success.
Manufacturers should evaluate potential suppliers based on factors such as technological capabilities, reputation, reliability, and after-sales support.
Cost-Benefit Analysis
Conducting a comprehensive cost-benefit analysis helps in understanding the financial implications of robot procurement.
This analysis should consider initial costs, maintenance expenses, potential savings, and return on investment (ROI).
Customization and Scalability
Manufacturers should seek robots that can be customized to specific production needs and can scale with business growth.
Flexibility in robot functionality ensures that they remain relevant as production demands evolve.
Supplier Negotiation Techniques
Effective negotiation with suppliers can lead to favorable terms and successful robot procurement.
Here are some strategies to enhance negotiation outcomes.
Building Strong Relationships
Establishing a collaborative relationship with suppliers fosters trust and facilitates smoother negotiations.
Long-term partnerships can result in better pricing, priority support, and access to the latest technologies.
Understanding Market Conditions
Staying informed about market trends, demand fluctuations, and technological advancements empowers manufacturers during negotiations.
Knowledge of the supplier’s position and the broader market landscape enables informed decision-making.
Leveraging Competitive Bidding
Engaging multiple suppliers in a competitive bidding process can drive better pricing and terms.
This approach encourages suppliers to offer their best possible deals to secure the business.
Negotiating Value-Added Services
Beyond price, manufacturers can negotiate value-added services such as extended warranties, training programs, and maintenance packages.
These additional services enhance the overall value of the procurement deal.
Market Conditions in Japan’s Robotics Industry
Understanding the market conditions is essential for effective procurement and purchasing.
Japan’s robotics industry is characterized by innovation, competition, and a focus on quality.
Competitive Landscape
Japan boasts a highly competitive robotics market with numerous established players and emerging innovators.
This competition drives continuous improvement and fosters the development of cutting-edge technologies.
Technological Innovations
The Japanese robotics industry is at the forefront of technological advancements, including artificial intelligence, machine learning, and IoT integration.
Manufacturers can leverage these innovations to enhance production capabilities and stay ahead of the curve.
Regulatory Environment
Japan’s regulatory framework supports the growth of the robotics industry through favorable policies and standards.
Compliance with these regulations ensures that procured robots meet safety, quality, and performance criteria.
Economic Factors
Economic stability and government support play significant roles in the robotics market.
Government initiatives promoting automation and advanced manufacturing contribute to market growth and offer incentives for procurement.
Best Practices for Procuring Industrial Robots
Adopting best practices in robot procurement ensures successful implementation and maximizes benefits.
Here are key practices to consider.
Comprehensive Needs Assessment
A detailed evaluation of production requirements and goals is essential before initiating procurement.
This assessment helps in selecting robots that precisely meet operational needs and contribute to strategic objectives.
Vendor Due Diligence
Conducting thorough due diligence on potential suppliers safeguards against risks associated with procurement.
Evaluating supplier reliability, financial stability, and track record ensures that they can deliver quality products and support.
Clear Contractual Agreements
Establishing clear and comprehensive contractual agreements prevents misunderstandings and disputes.
Contracts should outline specifications, pricing, delivery schedules, support services, and warranty terms.
Training and Support
Investing in training programs equips the workforce with the necessary skills to operate and maintain industrial robots.
Ongoing support from suppliers ensures that technical issues are promptly addressed, minimizing downtime.
Continuous Monitoring and Improvement
After procurement, continuous monitoring of robot performance and impact on production is crucial.
Regular assessments identify areas for improvement and inform future procurement decisions.
Future Trends in Industrial Robotics
The landscape of industrial robotics is continually evolving.
Anticipating future trends helps manufacturers stay ahead and leverage new opportunities.
Increased Adoption of AI and Machine Learning
Artificial intelligence and machine learning will further enhance robot capabilities, enabling more autonomous and intelligent operations.
This evolution will allow robots to adapt to complex and dynamic production environments.
Integration with IoT and Industry 4.0
The convergence of robotics with the Internet of Things (IoT) and Industry 4.0 technologies will enable seamless data exchange and real-time monitoring.
This integration facilitates smarter and more efficient manufacturing processes.
Advancements in Collaborative Robotics
Collaborative robots (cobots) will become more prevalent, working alongside humans to enhance productivity and flexibility.
Cobots will continue to evolve in safety features and adaptability, making them indispensable in various manufacturing settings.
Sustainability and Energy Efficiency
Future industrial robots will focus more on sustainability and energy efficiency, aligning with global environmental goals.
Energy-efficient robots reduce operational costs and contribute to a greener manufacturing footprint.
Conclusion
Industrial robots have been a cornerstone of Japan’s manufacturing success, driving productivity, quality, and innovation.
While challenges such as high initial investments and technical complexities exist, the benefits significantly outweigh the drawbacks.
Effective procurement and purchasing strategies, coupled with robust supplier negotiations and an understanding of market conditions, are essential for harnessing the full potential of industrial robots.
By adhering to best practices and staying abreast of future trends, manufacturers can continue to revolutionize their production processes and maintain their competitive edge in the global market.
Final Thoughts
As the manufacturing landscape evolves, the role of industrial robots will only become more critical.
Japan’s expertise in robotics provides a valuable framework for manufacturers worldwide to emulate and adapt.
Embracing industrial robots is not just about automation; it’s about fostering a culture of continuous improvement and innovation.
By unlocking Japan’s manufacturing potential through robotics, businesses can achieve new heights of efficiency, quality, and sustainability.
資料ダウンロード
QCD調達購買管理クラウド「newji」は、調達購買部門で必要なQCD管理全てを備えた、現場特化型兼クラウド型の今世紀最高の購買管理システムとなります。
ユーザー登録
調達購買業務の効率化だけでなく、システムを導入することで、コスト削減や製品・資材のステータス可視化のほか、属人化していた購買情報の共有化による内部不正防止や統制にも役立ちます。
NEWJI DX
製造業に特化したデジタルトランスフォーメーション(DX)の実現を目指す請負開発型のコンサルティングサービスです。AI、iPaaS、および先端の技術を駆使して、製造プロセスの効率化、業務効率化、チームワーク強化、コスト削減、品質向上を実現します。このサービスは、製造業の課題を深く理解し、それに対する最適なデジタルソリューションを提供することで、企業が持続的な成長とイノベーションを達成できるようサポートします。
オンライン講座
製造業、主に購買・調達部門にお勤めの方々に向けた情報を配信しております。
新任の方やベテランの方、管理職を対象とした幅広いコンテンツをご用意しております。
お問い合わせ
コストダウンが利益に直結する術だと理解していても、なかなか前に進めることができない状況。そんな時は、newjiのコストダウン自動化機能で大きく利益貢献しよう!
(Β版非公開)