- お役立ち記事
- Specific Strategies to Improve Cost Efficiency in Insert Molding
Specific Strategies to Improve Cost Efficiency in Insert Molding
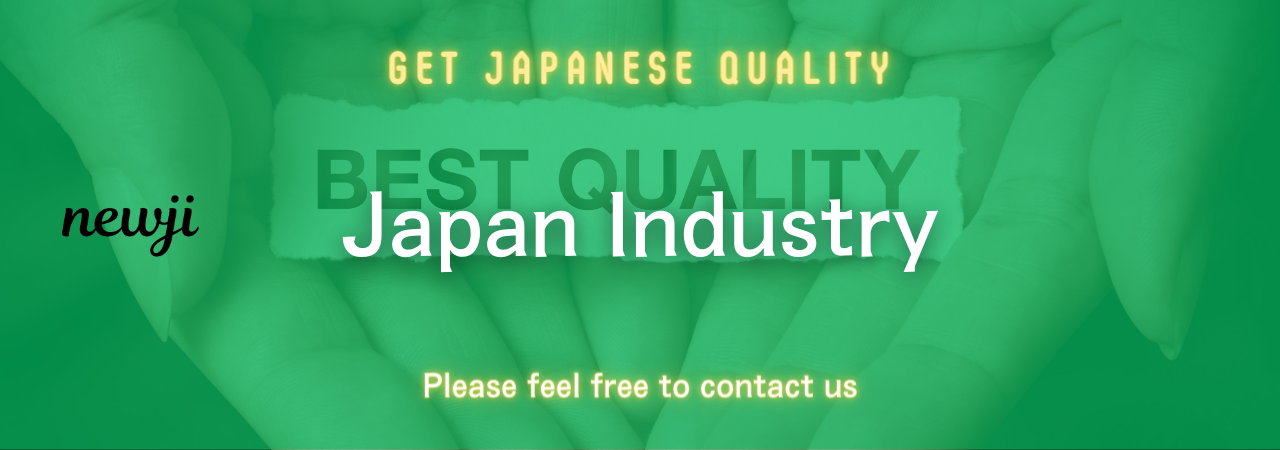
目次
Understanding Insert Molding
Insert molding is a manufacturing process that involves encapsulating metal or plastic parts with injected plastic to produce a single unit.
It combines multiple components into a single piece, often enhancing the functionality and durability of the final product.
This method is commonly used in industries like automotive, electronics, medical devices, and consumer products.
To achieve cost efficiency in insert molding, manufacturers need to focus on optimizing various stages of the production process.
By implementing specific strategies, companies can minimize waste, reduce expenses, and boost overall productivity.
Strategies for Cost Efficiency
1. Design Optimization
A well-thought-out design is crucial for ensuring cost efficiency in insert molding.
During the designing phase, engineers should focus on creating a mold that requires minimal material use and reduces the overall complexity.
Simplifying the mold design can help in reducing the cycle time and material consumption.
Using simulation software can assist in identifying potential issues in the design phase, allowing for necessary adjustments before manufacturing begins.
This proactive approach helps prevent costly errors and rework.
2. Material Selection
Choosing the right materials can have a significant impact on the cost efficiency of insert molding.
Opt for high-performance materials that offer the best balance between cost and functionality.
Consider using engineering-grade plastics or thermoplastics, which provide durability without compromising on quality.
Additionally, recycling plastic scrap can reduce material costs.
Implementing a recycling process not only helps in decreasing material waste but also supports sustainable manufacturing practices.
3. Efficient Machine Utilization
Investing in modern insert molding machines with advanced features can contribute to cost efficiency.
Newer machines are designed to optimize energy consumption, resulting in reduced operating costs.
Regular maintenance and calibration of machines ensure that they run at peak efficiency.
Upgrading older equipment and automating repetitive tasks can further improve machine utilization and reduce labor costs.
4. Process Automation
Automation is a key strategy for enhancing cost efficiency in the manufacturing process.
By automating various stages of insert molding, companies can reduce labor costs, improve consistency, and accelerate production times.
Utilizing robotic arms for material handling and assembly operations can significantly increase efficiency.
Automation reduces the chances of human error, allowing for a consistent and high-quality end product.
5. Quality Control
Implementing rigorous quality control measures throughout the insert molding process is essential for minimizing waste and rework.
Use advanced inspection technologies like 3D scanning and real-time data monitoring to detect defects early.
Maintaining strict quality standards ensures that products meet specifications, reducing the need for reprocessing.
Efficient quality control systems result in fewer rejected parts and, ultimately, cost savings.
Reducing Waste
Waste reduction is an important aspect of cost efficiency in insert molding.
A significant portion of waste in this process comes from excess plastic material and defective parts.
By focusing on the following areas, manufacturers can effectively minimize waste:
1. Material Usage
Optimize the amount of material used in each product by carefully designing molds and closely monitoring material flow during production.
Advanced software can simulate the injection process, providing insights into how material is distributed.
This allows for fine-tuning of the process to minimize waste.
2. Defect Reduction
Training employees on best practices and regular maintenance schedules for machinery can decrease the occurrence of defects.
Ensuring that quality standards are met at every stage of production will lead to less waste from defective products.
3. Recycling Initiatives
Implement a robust recycling initiative for scrap materials.
By reprocessing waste plastic, companies can recover material costs and contribute to environmental sustainability.
Improving Productivity
Enhancing productivity in insert molding leads to better cost efficiency.
Streamlining workflows and adopting lean manufacturing principles can significantly increase output.
1. Workflow Optimization
Analyze and review the entire production process to identify bottlenecks or inefficiencies.
Streamlining these processes reduces downtime and increases output.
Implementing lean manufacturing techniques such as the 5S methodology helps organize the workplace, leading to more efficient workflows.
2. Employee Training
Investing in comprehensive training programs for employees is critical for improving productivity.
Well-trained workers are more adept at handling machines, understanding processes, and identifying potential issues before they become costly problems.
3. Continuous Improvement
Adopt a culture of continuous improvement where feedback and innovation are encouraged.
Regularly review aspects of the production process, seeking areas for enhancement.
Encourage staff to suggest improvements, as they are often the ones most familiar with day-to-day operations.
Conclusion
Achieving cost efficiency in insert molding requires a strategic approach encompassing design optimization, smart material selection, automation, and a focus on reducing waste and improving productivity.
By implementing these strategies, manufacturers can significantly cut costs, enhance quality, and remain competitive in the industry.
The continuous assessment and adaptation of these strategies will ensure long-term success and profitability in the insert molding process.
資料ダウンロード
QCD調達購買管理クラウド「newji」は、調達購買部門で必要なQCD管理全てを備えた、現場特化型兼クラウド型の今世紀最高の購買管理システムとなります。
ユーザー登録
調達購買業務の効率化だけでなく、システムを導入することで、コスト削減や製品・資材のステータス可視化のほか、属人化していた購買情報の共有化による内部不正防止や統制にも役立ちます。
NEWJI DX
製造業に特化したデジタルトランスフォーメーション(DX)の実現を目指す請負開発型のコンサルティングサービスです。AI、iPaaS、および先端の技術を駆使して、製造プロセスの効率化、業務効率化、チームワーク強化、コスト削減、品質向上を実現します。このサービスは、製造業の課題を深く理解し、それに対する最適なデジタルソリューションを提供することで、企業が持続的な成長とイノベーションを達成できるようサポートします。
オンライン講座
製造業、主に購買・調達部門にお勤めの方々に向けた情報を配信しております。
新任の方やベテランの方、管理職を対象とした幅広いコンテンツをご用意しております。
お問い合わせ
コストダウンが利益に直結する術だと理解していても、なかなか前に進めることができない状況。そんな時は、newjiのコストダウン自動化機能で大きく利益貢献しよう!
(Β版非公開)