- お役立ち記事
- How to Achieve Cost Reduction and Productivity Improvement by Shortening Cooling Time
How to Achieve Cost Reduction and Productivity Improvement by Shortening Cooling Time
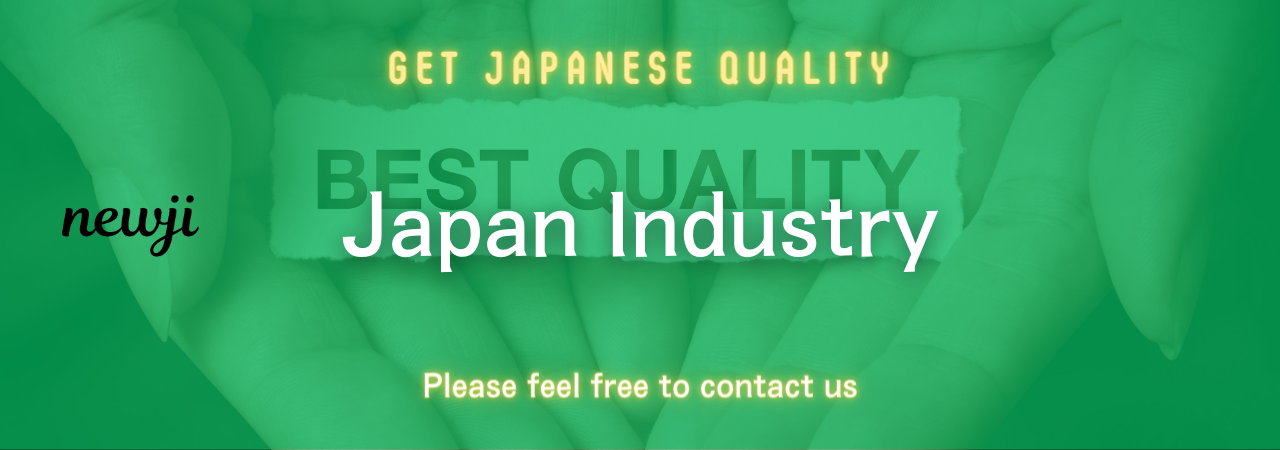
目次
Understanding Cooling Time in Manufacturing
In manufacturing processes, cooling time plays a significant role in determining both the efficiency and the cost-effectiveness of production.
Cooling time refers to the period during which a heated item solidifies to reach the desired physical state for further processing or final application.
This phase can significantly impact the schedule and quality of operations.
Reducing cooling time without compromising quality is a challenge faced by many manufacturers.
Efforts to shorten this time can lead to increased productivity and significant cost savings.
The relationship between cooling time, cost reduction, and productivity improvement is a dynamic one that needs careful management and optimization.
Strategies to Shorten Cooling Time
There are several strategies manufacturers can employ to minimize cooling time effectively.
Implementing these strategies not only enhances the speed of production but also ensures energy-efficient operations.
1. Material Selection
The choice of materials can greatly influence cooling times.
Materials with high thermal conductivity can help in dissipating heat more rapidly, thus reducing cooling time.
For example, using aluminum molds instead of steel ones can facilitate quicker heat transfer.
Additionally, selecting materials with a lower specific heat capacity can further aid in achieving faster cooling.
2. Optimizing Mold Design
Design tweaks in molds used during production can significantly influence cooling efficiency.
Incorporating cooling channels strategically within the mold can help to maintain uniform temperature distribution.
This method reduces hotspots that can prolong cooling times.
Computer-aided design (CAD) tools can be instrumental in simulating and optimizing mold designs for better cooling performance.
3. Enhancing Cooling Techniques
Advanced cooling techniques such as the use of conformal cooling channels, which conform to the shape of the mold, can greatly enhance the cooling process.
Other innovative methods like pulsed cooling, where cooling fluids are cycled in pulses, can also improve cooling efficiency without necessitating a constant flow of coolants.
4. Process Adjustments
Fine-tuning the processing parameters such as cycle time, pressure, and temperature can yield better cooling outcomes.
Automatic adjustments through process controls can optimize these parameters in real-time as operations progress.
This ensures that cooling is consistent with the demands of production.
The Importance of Technology in Shortening Cooling Time
Leveraging technology plays a crucial role in reducing cooling times.
Integrating Internet of Things (IoT) devices can facilitate real-time monitoring and control of cooling phases.
These devices can provide crucial data analytics that can be used to fine-tune cooling processes over time.
Digital twins, which are virtual replicas of physical manufacturing processes, can also be utilized to simulate the cooling period and predict the outcomes of different adjustments.
By using simulation software, manufacturers can preemptively evaluate the effectiveness of various cooling strategies without physically altering production lines.
Impact on Cost Reduction
Shortening cooling time can have a profound impact on cost reduction in various ways:
1. Energy Efficiency
Reduced cooling time can result in significant energy savings, as equipment does not need to run as long to cool down materials.
This lower energy consumption can directly translate to reduced utility bills and an overall decrease in operational costs.
2. Increased Throughput
By minimizing the time dedicated to cooling, manufacturers can increase their production throughput.
Machines and molds can be used more frequently, resulting in higher productivity without additional investment in new machinery.
3. Lower Maintenance Costs
Shortening cooling periods can lead to reduced wear and tear on equipment caused by prolonged exposure to heat.
This can extend the lifespan of machinery and reduce the frequency and cost of maintenance and repairs.
4. Minimized Inventory Costs
Quick cooling enables faster turnaround, reducing the need for large inventory stocks.
Lower levels of inventory decrease holding costs and increase cash flow.
The Role of Training and Education
Educating and training employees on the importance and techniques of efficient cooling can foster a culture of continuous improvement.
Teams that understand the process can contribute to identifying inefficiencies and brainstorming innovative solutions.
Workshops, seminars, and regular training sessions can help keep the workforce updated on the latest techniques and technologies.
Conclusion
Optimizing cooling time stands as a strategic approach that manufacturers can take to boost productivity and reduce costs.
Through a combination of material innovations, technology integration, process optimization, and employee training, businesses can achieve significant enhancements in their manufacturing cycle.
Although each strategy may offer isolated benefits, together they offer a robust solution for increasing competitiveness and achieving greater economic efficiency.
Investing in these areas will yield long-term benefits and position manufacturers to respond effectively to market demands.
資料ダウンロード
QCD調達購買管理クラウド「newji」は、調達購買部門で必要なQCD管理全てを備えた、現場特化型兼クラウド型の今世紀最高の購買管理システムとなります。
ユーザー登録
調達購買業務の効率化だけでなく、システムを導入することで、コスト削減や製品・資材のステータス可視化のほか、属人化していた購買情報の共有化による内部不正防止や統制にも役立ちます。
NEWJI DX
製造業に特化したデジタルトランスフォーメーション(DX)の実現を目指す請負開発型のコンサルティングサービスです。AI、iPaaS、および先端の技術を駆使して、製造プロセスの効率化、業務効率化、チームワーク強化、コスト削減、品質向上を実現します。このサービスは、製造業の課題を深く理解し、それに対する最適なデジタルソリューションを提供することで、企業が持続的な成長とイノベーションを達成できるようサポートします。
オンライン講座
製造業、主に購買・調達部門にお勤めの方々に向けた情報を配信しております。
新任の方やベテランの方、管理職を対象とした幅広いコンテンツをご用意しております。
お問い合わせ
コストダウンが利益に直結する術だと理解していても、なかなか前に進めることができない状況。そんな時は、newjiのコストダウン自動化機能で大きく利益貢献しよう!
(Β版非公開)