- お役立ち記事
- Quality Control Points for Polyethylene Processing
Quality Control Points for Polyethylene Processing
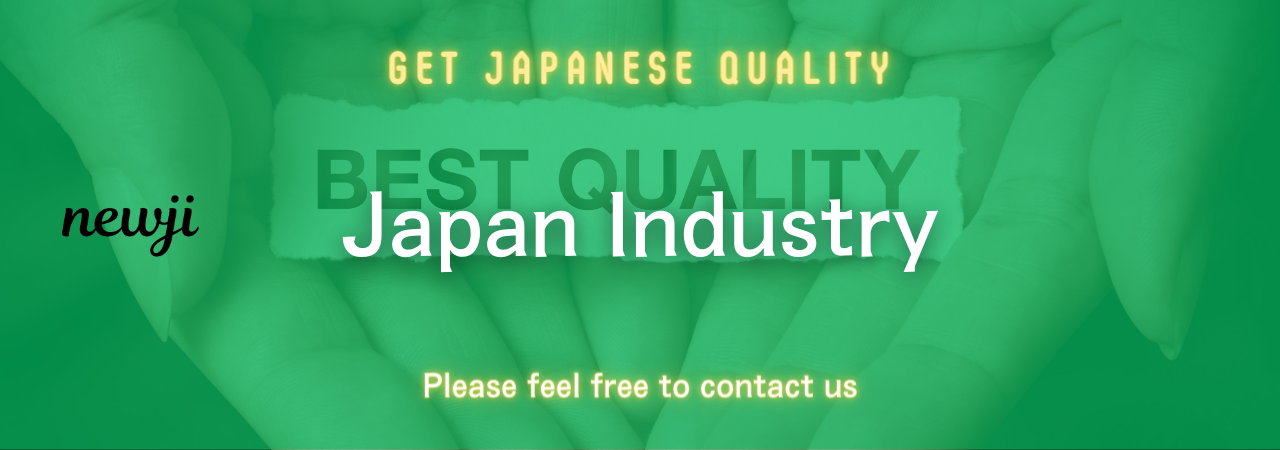
目次
Introduction to Polyethylene Processing
Polyethylene is a widely used plastic that is found in countless products around the world.
Its versatility and durability make it an ideal choice for everything from packaging to industrial applications.
However, ensuring the quality of polyethylene products is crucial, as defects can lead to significant problems such as product failure and increased costs.
Quality control in polyethylene processing is essential to ensure that finished products meet required standards and perform as expected.
Understanding Polyethylene
Polyethylene is a type of polymer that is made from the polymerization of ethylene.
It is one of the most common plastics used today and is characterized by its lightweight, high strength, and resistance to moisture and chemicals.
Polyethylene is available in various forms, including low-density polyethylene (LDPE), high-density polyethylene (HDPE), and linear low-density polyethylene (LLDPE), each offering distinct properties for different applications.
Properties and Applications
LDPE is known for its flexibility and is often used in film applications, such as shopping bags and food packaging.
HDPE, on the other hand, is more rigid and is used in containers, pipes, and automotive parts.
LLDPE provides a balance of flexibility and strength, making it suitable for stretch films and industrial liners.
Each type of polyethylene requires specific processing conditions to ensure optimal quality and performance.
Key Quality Control Points in Polyethylene Processing
To maintain high quality in polyethylene processing, manufacturers must adhere to several key quality control points.
These points focus on the material, the process itself, and the final product.
1. Raw Material Quality
The first step in quality control is ensuring that the raw materials used meet the required specifications.
Raw materials should be of high purity and consistent in composition to avoid defects in the final product.
Material suppliers should provide reliable certification of quality, and incoming materials should be tested to verify compliance with specifications.
2. Controlling Processing Parameters
Processing parameters such as temperature, pressure, and speed must be carefully controlled during polyethylene production.
Improper control of these parameters can lead to various issues, such as incomplete polymerization, poor surface finish, or structural weaknesses in the product.
Regular calibration and maintenance of equipment are essential to maintaining the correct processing conditions.
3. Monitoring Melt Flow Index (MFI)
The Melt Flow Index (MFI) is a critical parameter in polyethylene processing.
It measures the flow characteristics of the polymer, which affects its processability and the properties of the final product.
Consistent MFI ensures that the product will have uniform dimensions and mechanical properties.
Regular testing of MFI during production helps identify any deviations that could compromise quality.
4. Ensuring Homogeneity
Homogeneity of the polymer melt is important to ensure products have uniform properties and appearance.
Inadequate mixing or blending can lead to issues such as streaking, problems with strength, or variations in product thickness.
Using the proper mixing equipment and methods helps maintain the integrity of the polyethylene blend.
5. Thickness Control
For products like films and sheets, maintaining consistent thickness is vital to performance and appeal.
Thickness variations can affect the strength, pliability, and barrier properties of the product.
Advanced measuring devices and feedback systems are used to monitor and adjust thickness in real-time during production.
Testing and Inspection
After processing, finished products must undergo a series of tests and inspections to ensure that they meet quality standards.
Visual Inspection
Visual inspection is a straightforward method to check for surface defects like bubbles, cracks, and inconsistencies.
Operators or automated systems can perform these checks to quickly identify and rectify any visible issues.
Mechanical Testing
Mechanical properties such as tensile strength, elongation, and impact resistance are tested to ensure the product can withstand intended usage conditions.
These tests often require specialized machinery and are conducted under standardized conditions to ensure accurate results.
Environmental Resistance Testing
Polyethylene products are often exposed to environmental factors such as moisture, temperature changes, and UV light.
Testing for environmental resistance ensures that the products maintain their integrity and performance over time.
Accelerated aging tests are commonly used to simulate long-term exposures in a shorter timeframe.
Continuous Improvement in Quality Control
Quality control in polyethylene processing is not a one-time effort.
It requires continuous monitoring and improvement to ensure sustained excellence in product quality.
Implementing Quality Management Systems
Many manufacturers adopt quality management systems (QMS), such as ISO 9001, to create a structured approach to quality control.
A QMS helps streamline processes, establish clear quality guidelines, and track improvements over time.
Training and Awareness
Trained personnel are crucial to effective quality control.
Continuous training ensures that employees are aware of the latest techniques, equipment, and industry standards.
Encouraging a culture of quality awareness leads to proactive identification and resolution of potential issues.
Utilizing Advanced Technology
Advances in technology, such as real-time data analytics and automation, play a significant role in quality control.
These tools allow for more precise monitoring and rapid adjustments during production, resulting in enhanced product quality and reduced waste.
Conclusion
Quality control in polyethylene processing is vital to ensure that products meet the required performance and safety standards.
By focusing on the quality of raw materials, processing parameters, and rigorous testing, manufacturers can produce high-quality polyethylene products with confidence.
Continuous improvement, supported by modern technology and a robust quality management system, helps maintain competitiveness and customer satisfaction in the dynamic plastics industry.
資料ダウンロード
QCD調達購買管理クラウド「newji」は、調達購買部門で必要なQCD管理全てを備えた、現場特化型兼クラウド型の今世紀最高の購買管理システムとなります。
ユーザー登録
調達購買業務の効率化だけでなく、システムを導入することで、コスト削減や製品・資材のステータス可視化のほか、属人化していた購買情報の共有化による内部不正防止や統制にも役立ちます。
NEWJI DX
製造業に特化したデジタルトランスフォーメーション(DX)の実現を目指す請負開発型のコンサルティングサービスです。AI、iPaaS、および先端の技術を駆使して、製造プロセスの効率化、業務効率化、チームワーク強化、コスト削減、品質向上を実現します。このサービスは、製造業の課題を深く理解し、それに対する最適なデジタルソリューションを提供することで、企業が持続的な成長とイノベーションを達成できるようサポートします。
オンライン講座
製造業、主に購買・調達部門にお勤めの方々に向けた情報を配信しております。
新任の方やベテランの方、管理職を対象とした幅広いコンテンツをご用意しております。
お問い合わせ
コストダウンが利益に直結する術だと理解していても、なかなか前に進めることができない状況。そんな時は、newjiのコストダウン自動化機能で大きく利益貢献しよう!
(Β版非公開)