- お役立ち記事
- Basics of Injection Pressure and Its Impact on Molding Quality
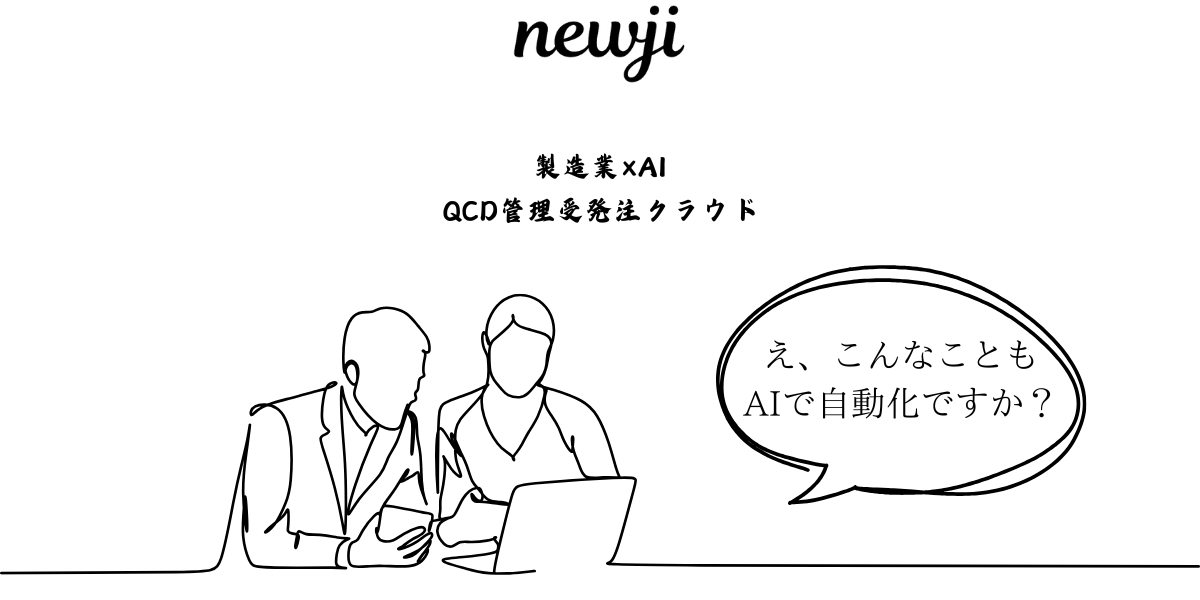
Basics of Injection Pressure and Its Impact on Molding Quality
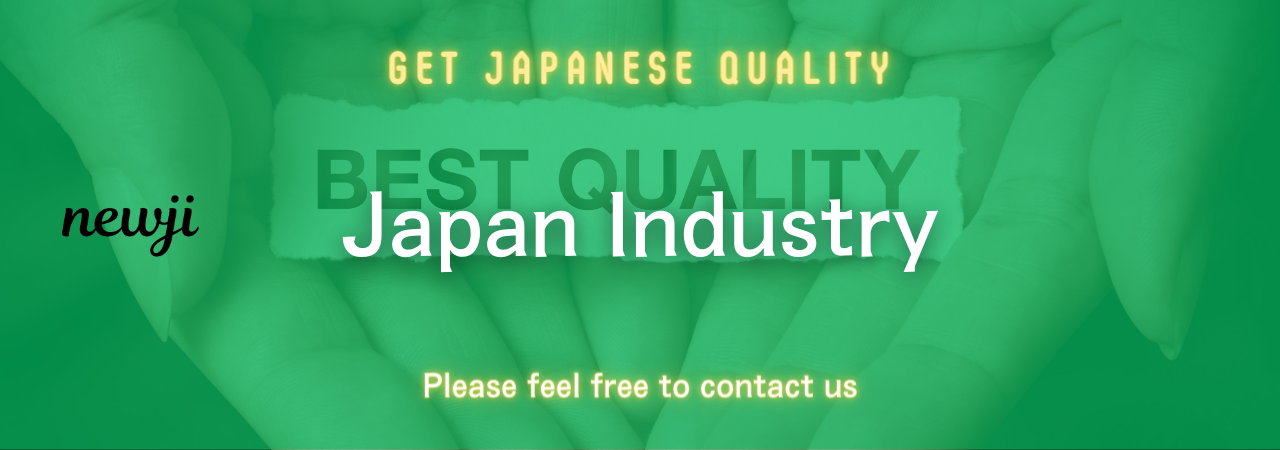
目次
Understanding Injection Pressure
Injection pressure is a critical aspect of the injection molding process.
It refers to the amount of pressure applied to force molten plastic into a mold cavity.
This pressure ensures that the material fills the mold completely, achieving the desired shape and dimensions.
Injection pressure is a vital parameter that affects the quality and consistency of molded parts.
It plays a significant role in determining the cycle time, material properties, and the overall efficiency of the molding process.
Many factors influence the injection pressure, such as the type of plastic material, mold design, and injection speed.
Understanding these factors helps manufacturers optimize the injection molding process to produce high-quality parts efficiently.
The Role of Injection Pressure in Molding Quality
Injection pressure directly impacts the quality of molded parts.
If the pressure is too low, the molten plastic may not fill the mold completely, leading to defects such as short shots or incomplete parts.
On the other hand, excessive pressure can cause flash, where material leaks out of the mold cavity, resulting in excess material on the part’s edges.
Maintaining the appropriate injection pressure ensures that the plastic flows smoothly into all areas of the mold, creating parts with accurate dimensions and intricate details.
It also helps reduce internal stresses and warping, contributing to the structural integrity and appearance of the final product.
Factors Influencing Injection Pressure
Several factors should be considered when determining the appropriate injection pressure for a particular molding process.
Material Properties
Different types of plastics require different injection pressures due to variations in their viscosity and flow characteristics.
For example, materials with higher viscosity may require higher pressures to fill the mold.
Understanding the specific material properties is crucial for setting the correct injection pressure.
Mold Design
The design of the mold also plays a significant role in determining the injection pressure.
Complex molds with thin wall sections or intricate details may require higher pressures to ensure the material fills the entire cavity.
Additionally, the number and arrangement of gates, which are the entry points for the molten plastic, can affect pressure distribution within the mold.
Injection Speed
Injection speed, or the rate at which the material is injected into the mold, influences the pressure required for filling the cavity.
Faster injection speeds typically require higher pressures to ensure the plastic flows quickly through the mold.
However, finding a balance is crucial, as excessive speed and pressure can result in defects or damage to the mold.
Temperature Settings
The temperature of the molten plastic and the mold itself can affect the injection pressure.
Higher temperatures typically reduce the viscosity of the material, allowing it to flow more easily and requiring less pressure.
Conversely, cooler temperatures may necessitate higher pressures to achieve complete mold filling.
Optimizing Injection Pressure for Quality Molding
Ensuring optimal injection pressure is essential for producing high-quality molded parts.
Manufacturers can take several steps to achieve this:
Conducting Thorough Material Analysis
Understanding the properties of the plastic material being used is crucial for setting the appropriate injection pressure.
Conducting material analysis helps in selecting the right parameters for the molding process.
Designing Efficient Molds
Working closely with mold designers to create efficient mold designs can help minimize the pressure required for complete filling.
Simplicity in mold design, proper gating arrangements, and attention to wall thickness are vital considerations.
Process Monitoring and Control
Regularly monitoring and adjusting the injection molding parameters, including pressure, can help maintain consistent part quality.
Using advanced control systems and sensors allows for real-time adjustments to optimize the process.
Regular Maintenance and Calibration
Regular maintenance and calibration of injection molding machines ensure that they operate at peak efficiency.
Accurate pressure settings depend on well-maintained equipment that performs reliably.
Conclusion
Injection pressure is a fundamental aspect of the injection molding process that significantly impacts the quality of molded parts.
By understanding the factors influencing injection pressure and taking steps to optimize it, manufacturers can produce high-quality and consistent products.
Considering material properties, mold design, injection speed, and temperature settings are essential for achieving the perfect balance.
With careful attention to these aspects, the injection molding process can be refined for efficiency and superior product quality.
資料ダウンロード
QCD調達購買管理クラウド「newji」は、調達購買部門で必要なQCD管理全てを備えた、現場特化型兼クラウド型の今世紀最高の購買管理システムとなります。
ユーザー登録
調達購買業務の効率化だけでなく、システムを導入することで、コスト削減や製品・資材のステータス可視化のほか、属人化していた購買情報の共有化による内部不正防止や統制にも役立ちます。
NEWJI DX
製造業に特化したデジタルトランスフォーメーション(DX)の実現を目指す請負開発型のコンサルティングサービスです。AI、iPaaS、および先端の技術を駆使して、製造プロセスの効率化、業務効率化、チームワーク強化、コスト削減、品質向上を実現します。このサービスは、製造業の課題を深く理解し、それに対する最適なデジタルソリューションを提供することで、企業が持続的な成長とイノベーションを達成できるようサポートします。
オンライン講座
製造業、主に購買・調達部門にお勤めの方々に向けた情報を配信しております。
新任の方やベテランの方、管理職を対象とした幅広いコンテンツをご用意しております。
お問い合わせ
コストダウンが利益に直結する術だと理解していても、なかなか前に進めることができない状況。そんな時は、newjiのコストダウン自動化機能で大きく利益貢献しよう!
(Β版非公開)