- お役立ち記事
- How to Shorten Molding Cycles Using Shot Size Optimization Techniques
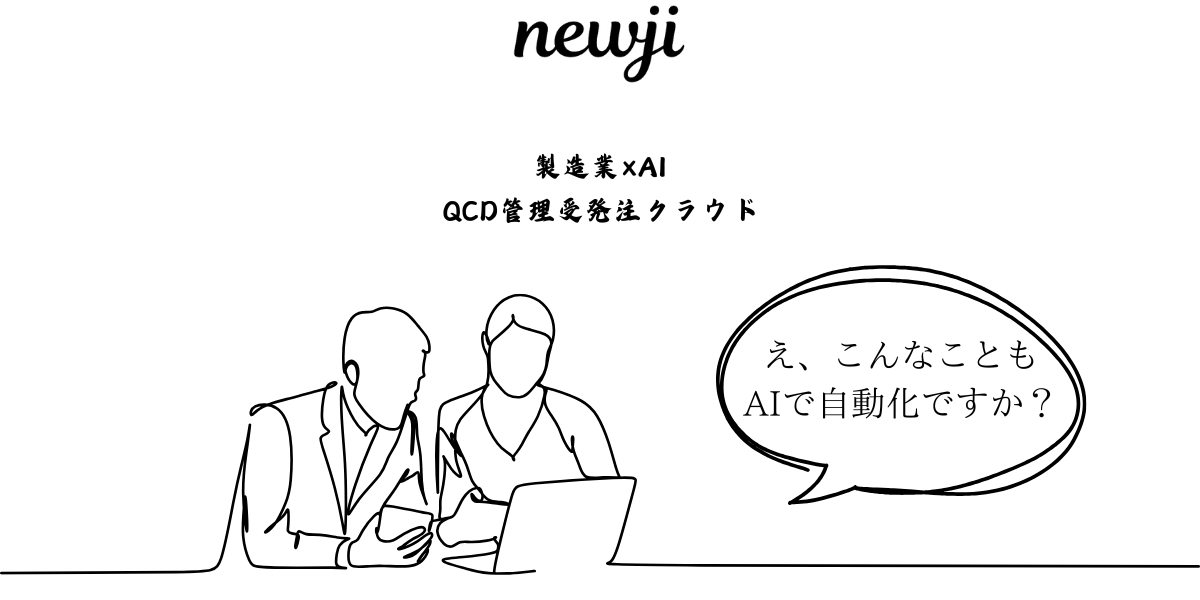
How to Shorten Molding Cycles Using Shot Size Optimization Techniques
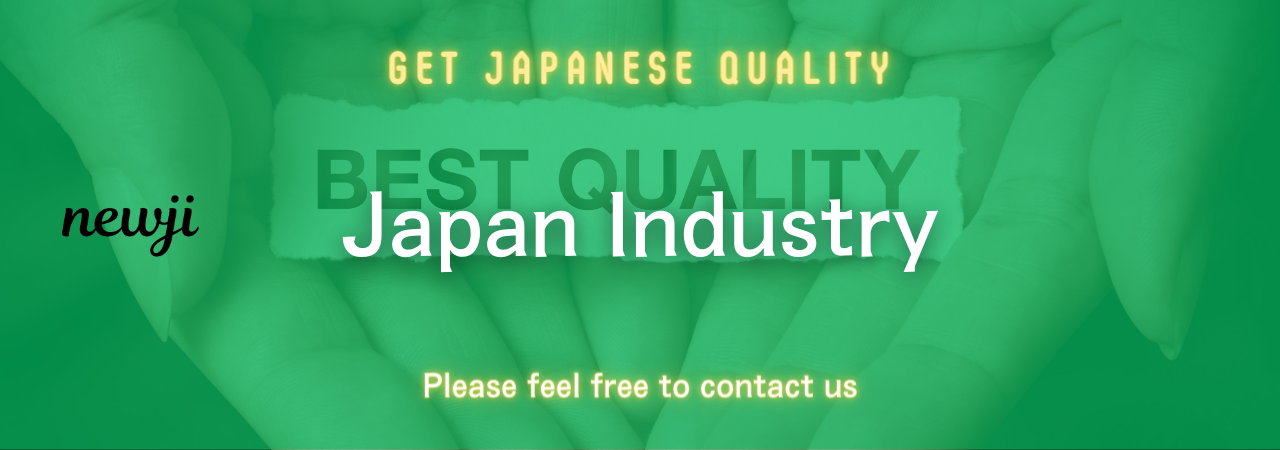
目次
Understanding Shot Size in Molding
Injection molding is a widely used manufacturing process for producing plastic parts.
One of the critical aspects of this process is optimizing the shot size, which refers to the amount of material injected into the mold to form a desired part.
Achieving the correct shot size is crucial as it impacts the quality of the finished product and the efficiency of the manufacturing process.
Shot size optimization helps to reduce waste, improve cycle times, and lower production costs.
It ensures that just the right amount of material fills the mold cavity, minimizing excess material and defects.
By understanding and implementing shot size optimization techniques, manufacturers can significantly enhance their production performance.
Importance of Shot Size Optimization
Optimizing the shot size in injection molding offers several benefits.
One of the primary advantages is the reduction in cycle time.
When the correct amount of material is used, the cooling and solidification process is faster, leading to shorter cycle times.
This means more parts can be produced in less time.
Moreover, proper shot size optimization minimizes material wastage.
Using too much material can result in overflow, flash, and unnecessary trimming work.
Conversely, using too little can lead to incomplete filling and poor surface finish.
Both scenarios result in wastage and additional processing, which increases costs.
Finally, shot size optimization leads to improved part quality.
Properly filled molds with uniform material distribution ensure that parts have the intended mechanical properties and dimensions.
This reduces the likelihood of defects, saving time and resources in quality control and rework.
Techniques for Optimizing Shot Size
Several techniques can be employed to optimize shot size in injection molding.
By fine-tuning the process, manufacturers can achieve better efficiency and quality in their production.
1. Calibration of the Injection Molding Machine
Calibration is the foundation of any optimization process.
Regularly calibrating the injection molding machine ensures that it delivers the precise amount of material each time.
This includes checking the calibration of the machine’s screw, barrel, and nozzle.
This calibration process involves verifying the machine’s settings against the desired shot size and adjusting it accordingly.
An accurately calibrated machine will consistently deliver the correct shot size, improving productivity and reducing the chances of defects.
2. Material Selection and Evaluation
Selecting the right material can significantly impact shot size optimization.
Each type of plastic material has unique properties, such as viscosity, flow rate, and cooling time.
Understanding these properties when selecting materials helps in making appropriate adjustments, ensuring the mold is filled appropriately without defects.
Additionally, it’s advised to evaluate material performance regularly.
Changes in material batch or supplier could alter the flow and behavior, necessitating adjustments to optimize the shot size.
3. Adjusting Process Parameters
Process parameters such as temperature, pressure, and injection speed play a vital role in determining the shot size.
Each parameter needs careful adjustment and monitoring to achieve optimal shot size.
For instance, proper temperature control ensures that the material flows uniformly, while appropriate pressure ensures that the mold is filled completely without overflow.
Fine-tuning these parameters with trial and error can indicate the best settings for shot size optimization.
4. Utilizing Simulation Software
In recent years, simulation software has become an integral part of the injection molding process.
These advanced tools allow manufacturers to simulate the molding process and visualize how different shot sizes affect the final product.
Simulation software can predict potential problems like flow imbalances, air traps, or short shots before they occur in actual production.
By leveraging these insights, manufacturers can make informed decisions and adjust settings to optimize the shot size effectively.
5. Conducting Regular Quality Checks
Implementing regular quality checks is essential for maintaining optimized shot size.
Quality checks involve inspecting finished parts for defects or irregularities that might indicate suboptimal shot size.
By continually monitoring and analyzing production output, manufacturers can identify trends or issues in the process.
This ongoing assessment can lead to timely corrections and sustained optimization over long production runs.
Conclusion
Shot size optimization is a crucial element in injection molding that affects production efficiency, material usage, and product quality.
By thoroughly understanding the principles of shot size and employing techniques such as machine calibration, material evaluation, parameter adjustment, simulation software, and quality checks, manufacturers can significantly shorten molding cycles and enhance their operations.
The commitment to continual improvement and process optimization ensures that manufacturers not only meet their output goals but also deliver high-quality products consistently.
The advantages realized from shot size optimization, such as reduced cycle times and lower production costs, can provide a significant competitive edge in the market.
資料ダウンロード
QCD調達購買管理クラウド「newji」は、調達購買部門で必要なQCD管理全てを備えた、現場特化型兼クラウド型の今世紀最高の購買管理システムとなります。
ユーザー登録
調達購買業務の効率化だけでなく、システムを導入することで、コスト削減や製品・資材のステータス可視化のほか、属人化していた購買情報の共有化による内部不正防止や統制にも役立ちます。
NEWJI DX
製造業に特化したデジタルトランスフォーメーション(DX)の実現を目指す請負開発型のコンサルティングサービスです。AI、iPaaS、および先端の技術を駆使して、製造プロセスの効率化、業務効率化、チームワーク強化、コスト削減、品質向上を実現します。このサービスは、製造業の課題を深く理解し、それに対する最適なデジタルソリューションを提供することで、企業が持続的な成長とイノベーションを達成できるようサポートします。
オンライン講座
製造業、主に購買・調達部門にお勤めの方々に向けた情報を配信しております。
新任の方やベテランの方、管理職を対象とした幅広いコンテンツをご用意しております。
お問い合わせ
コストダウンが利益に直結する術だと理解していても、なかなか前に進めることができない状況。そんな時は、newjiのコストダウン自動化機能で大きく利益貢献しよう!
(Β版非公開)