- お役立ち記事
- Methods for Adjusting Shot Size to Prevent Molding Defects
月間76,176名の
製造業ご担当者様が閲覧しています*
*2025年3月31日現在のGoogle Analyticsのデータより
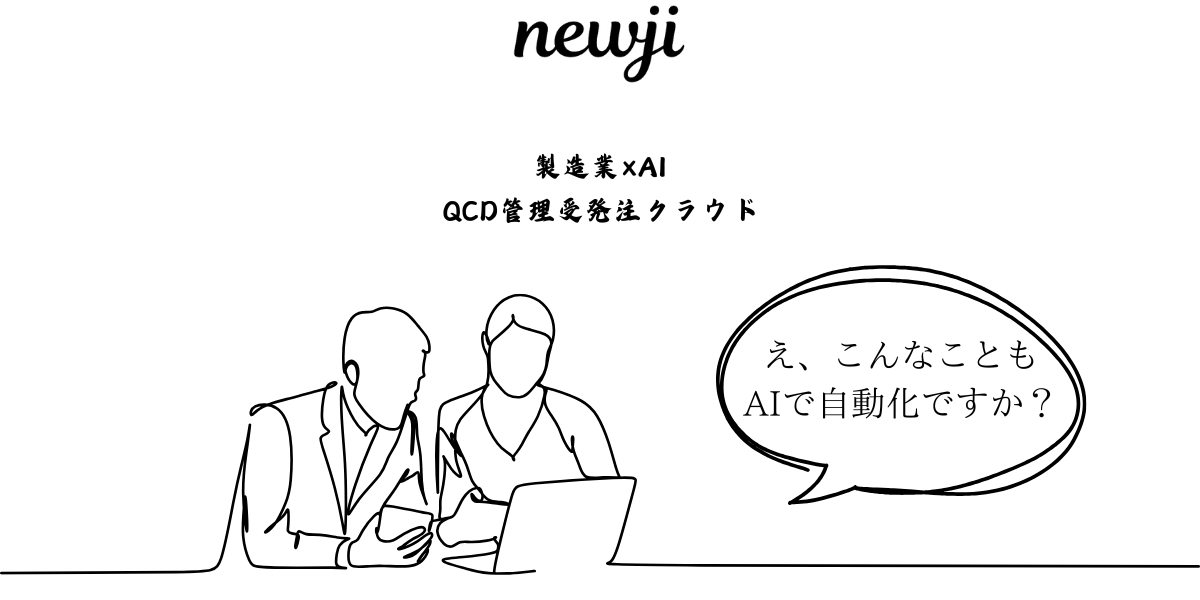
Methods for Adjusting Shot Size to Prevent Molding Defects
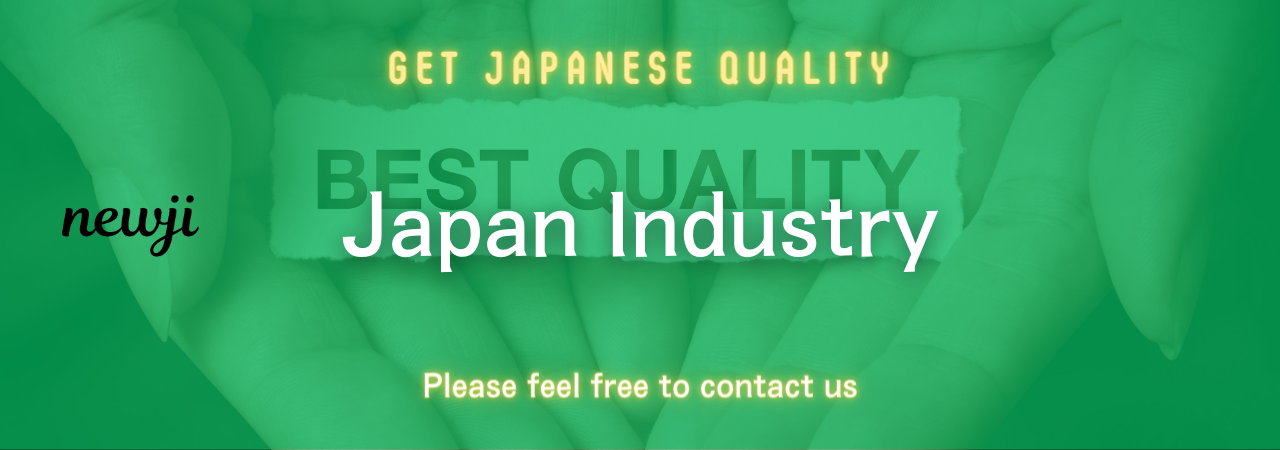
目次
Understanding Shot Size in Injection Molding
Injection molding is a process of manufacturing parts by injecting molten material into a mold.
It’s widely used for creating a variety of products, from small medical devices to large automotive components.
A critical aspect of achieving high-quality products in injection molding is the precise control of shot size.
Understanding and adjusting shot size correctly is essential to prevent defects and ensure the final product meets desired specifications.
What is Shot Size in Injection Molding?
Shot size refers to the amount of material injected into the mold during the molding process.
It is a crucial parameter because it strongly influences the quality and consistency of the molded parts.
Determining the correct shot size involves considering several factors such as material properties, mold design, and product dimensions.
If the shot size is too small, it might result in short shots, where the cavity isn’t completely filled, leading to incomplete parts.
On the other hand, if the shot size is too large, it can cause issues like flash or excessive material being squeezed out of the mold.
Common Molding Defects Due to Incorrect Shot Size
Various defects can occur if the shot size is not properly adjusted.
Being aware of these defects is the first step in effectively preventing them.
1. Short Shots
Short shots happen when the molten material doesn’t fill the mold cavity completely.
This usually results from insufficient material being injected.
As a result, parts may have incomplete sections, which compromises their functionality and aesthetics.
2. Flash
Flash is the occurrence of extra material that can leak out along the molds’ parting line.
This defect is often due to excessive shot size forcing material to escape from the mold cavity.
While it might seem minor, flash can require additional machining or manual removal, adding time and cost to the manufacturing process.
3. Sink Marks
Sink marks are depressions or craters on the surface of the molded part.
They usually result from insufficient packing or poor control of shot size during the cooling phase.
Properly adjusting and controlling the shot size is vital to prevent these visible and structural defects.
Methods for Adjusting Shot Size
Adjusting shot size effectively involves a combination of careful measurement, monitoring, and fine-tuning of the injection molding process.
Here are several methods to ensure the correct shot size:
1. Understanding Material Requirements
Different materials have unique properties and flow characteristics.
Using the correct material for your mold and understanding its requirements is crucial for determining the optimal shot size.
Review technical datasheets for information on recommended processing parameters, which can guide you on the right shot size.
2. Calculating Shot Volume
Calculating the correct shot volume involves determining the volume of the mold cavity.
This calculation should be based on the part’s size and geometry, while also considering the material’s density and any additional allowances for material shrinkage.
Using shot volume calculations can provide a baseline for setting machine parameters.
3. Adjusting Based on Feedback
Implementing real-time monitoring tools can assist in gathering feedback during production.
Machines equipped with sensors provide valuable data to analyze whether the mold is filled correctly or if any defects appear.
Regular adjustments based on this feedback help fine-tune the shot size for optimal results.
4. Trial and Error
Trial and error remain integral to perfecting shot size.
Conducting test runs with various shot sizes helps identify the most effective settings.
By observing the outcome of each test, you can gradually hone in on the right parameters needed to prevent defects.
5. Collaborating with Machine Operators
Machine operators offer practical insights into the intricacies of adjusting shot size.
Collaborating with them allows you to gain a deeper understanding of the machine’s performance and any anomalies that may require attention.
Their experience can be invaluable in resolving shot size-related issues.
Ensuring Quality in Injection Molding
The key to preventing molding defects lies not just in understanding shot size but in maintaining consistent quality throughout the molding process.
This requires a holistic approach where all aspects of injection molding—from design and materials to machine settings—are optimized for quality.
Comprehensive Mold Design
Ensuring the mold design is comprehensive and aligns with the product specifications is fundamental.
A correctly designed mold should account for all flow paths and patterns to minimize defects such as short shots and flash.
Working with skilled mold designers can result in effective solutions tailored to specific project needs.
Regular Maintenance and Calibration
Regular maintenance and calibration of injection molding machines are crucial in sustaining high performance and accurate shot size.
Regular checks on machine components like screws and barrels help avoid issues related to wear and tear that might influence shot precision.
By embracing these methods and focusing on precision in shot size control, manufacturers can significantly reduce molding defects, ensuring high-quality outcomes for injection molded products.
Well-adjusted shot size not only enhances the product’s aesthetic appeal but also its structural integrity, leading to better performance in the field.
資料ダウンロード
QCD管理受発注クラウド「newji」は、受発注部門で必要なQCD管理全てを備えた、現場特化型兼クラウド型の今世紀最高の受発注管理システムとなります。
ユーザー登録
受発注業務の効率化だけでなく、システムを導入することで、コスト削減や製品・資材のステータス可視化のほか、属人化していた受発注情報の共有化による内部不正防止や統制にも役立ちます。
NEWJI DX
製造業に特化したデジタルトランスフォーメーション(DX)の実現を目指す請負開発型のコンサルティングサービスです。AI、iPaaS、および先端の技術を駆使して、製造プロセスの効率化、業務効率化、チームワーク強化、コスト削減、品質向上を実現します。このサービスは、製造業の課題を深く理解し、それに対する最適なデジタルソリューションを提供することで、企業が持続的な成長とイノベーションを達成できるようサポートします。
製造業ニュース解説
製造業、主に購買・調達部門にお勤めの方々に向けた情報を配信しております。
新任の方やベテランの方、管理職を対象とした幅広いコンテンツをご用意しております。
お問い合わせ
コストダウンが利益に直結する術だと理解していても、なかなか前に進めることができない状況。そんな時は、newjiのコストダウン自動化機能で大きく利益貢献しよう!
(β版非公開)