- お役立ち記事
- Troubleshooting in Vacuum Molding: Tips to Avoid Failures
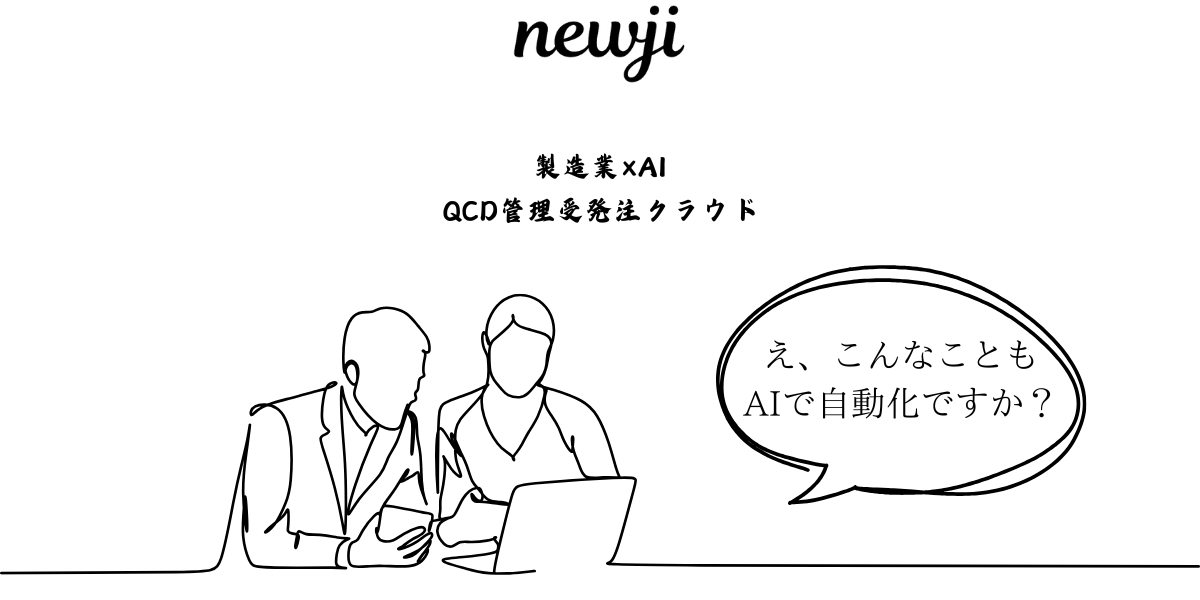
Troubleshooting in Vacuum Molding: Tips to Avoid Failures
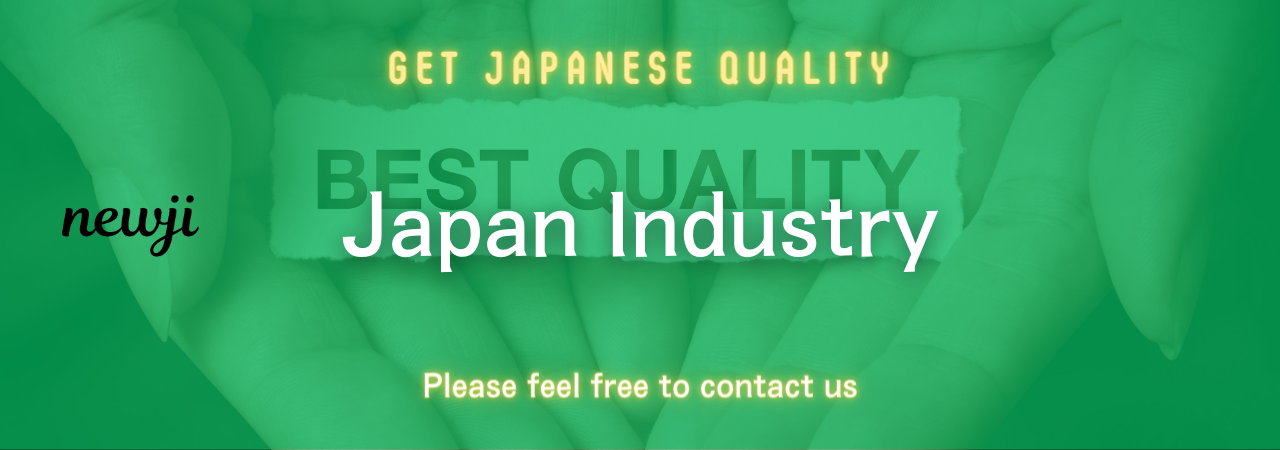
目次
Understanding Vacuum Molding
Vacuum molding is a pivotal process in the manufacturing industry that helps create precise and detailed plastic parts.
It utilizes a mold and vacuum to shape and form plastic sheets into complex components.
This method is not only efficient but also cost-effective, making it popular across various sectors.
The process begins with heating a plastic sheet until it becomes pliable.
Subsequently, the sheet is laid over a mold and vacuum is applied.
This vacuum sucks the air out, pulling the plastic tightly against the mold, thus giving it its detailed shape.
Upon cooling, the plastic retains this shape, creating a finished product ready for use.
Common Issues in Vacuum Molding
Like any other manufacturing process, vacuum molding may present challenges that can lead to product failures.
Understanding these issues allows manufacturers to troubleshoot effectively and minimize wastage.
One frequent problem is incomplete molding, where the plastic fails to fully conform to the mold.
This often results from inadequate vacuum pressure or improper heating of the plastic sheet.
Additionally, having a damaged or poorly designed mold can lead to defects in the final product.
Another common issue is excessive thinning.
This occurs when the material stretches too thin over certain areas, leading to weak spots in the final product.
Typically, this is caused by uneven heating or an inappropriate mold design that doesn’t account for material behavior.
Lastly, air bubbles can become trapped within the molded product.
These flaws are usually a sign of improper vacuum pressure or contaminated materials.
Preventing Common Failures
To ensure successful vacuum molding, several preventive measures can be implemented to avoid these common pitfalls.
Maintain Proper Equipment Calibration
Ensuring that all equipment is properly calibrated is crucial.
Regularly check and maintain the vacuum pumps, molds, and heating elements.
Calibrated machinery provides consistent results and reduces the risk of failure due to mechanical shortcomings.
Choose the Right Materials
Selecting the appropriate type of plastic for the specific application is vital.
Different plastics have unique properties, such as melting points and elasticity.
Understanding these properties helps in choosing a material that will perform well under the conditions of vacuum molding.
Optimize Mold Design
Invest in high-quality, well-designed molds that accommodate for the material’s behavior during the molding process.
Consider using computer simulations during the design phase to predict how the material will flow and how pressure will be distributed.
This foresight helps in minimizing issues like thinning and air bubbles.
Improved Control Over Heating
Equal distribution of heat across the plastic sheet is critical for achieving high-quality results.
Uneven heating can lead to thinning or incomplete molding.
Ensure that the heating elements are functioning uniformly and adjust the temperature settings according to the thickness and type of plastic being used.
Ensuring Consistent Vacuum Pressure
Maintaining a reliable and consistent vacuum pressure is essential for optimal molding.
Monitor vacuum levels closely during the process and address any fluctuations immediately.
Having backup systems can be beneficial to ensure that pressure is maintained even in the event of equipment failure.
Managing Material Handling and Storage
Proper storage and handling of plastic sheets are also important factors.
Protect materials from contamination, such as dust and moisture, which can lead to defects during molding.
Store them in a controlled environment to maintain their integrity and quality until they are ready for use.
Monitoring and Adjusting Process Parameters
Routine monitoring of process parameters, such as temperature, pressure, and timing, allows for quick adjustments to be made as needed.
This proactive approach can prevent issues from escalating into failures.
Document any changes made to the process and analyze them to understand their impact on the final product.
Training and Skill Development
Ensuring that all personnel involved in the vacuum molding process are adequately trained is crucial.
Regular training sessions should be conducted to keep staff up-to-date with best practices and new technologies.
A skilled workforce can make informed decisions and quickly troubleshoot issues, reducing the likelihood of failures.
Quality Control and Testing
Implementing a robust quality control system will help identify defects early in the production process.
Conduct regular testing of samples to ensure they meet the required specifications before proceeding to full-scale production.
This proactive approach can save time and resources by catching issues before they affect large batches of product.
By adhering to these guidelines and continuously analyzing and refining vacuum molding processes, manufacturers can significantly reduce the occurrence of failures and improve product quality.
Understanding and addressing the common issues associated with vacuum molding lead to enhanced efficiency and customer satisfaction.
資料ダウンロード
QCD調達購買管理クラウド「newji」は、調達購買部門で必要なQCD管理全てを備えた、現場特化型兼クラウド型の今世紀最高の購買管理システムとなります。
ユーザー登録
調達購買業務の効率化だけでなく、システムを導入することで、コスト削減や製品・資材のステータス可視化のほか、属人化していた購買情報の共有化による内部不正防止や統制にも役立ちます。
NEWJI DX
製造業に特化したデジタルトランスフォーメーション(DX)の実現を目指す請負開発型のコンサルティングサービスです。AI、iPaaS、および先端の技術を駆使して、製造プロセスの効率化、業務効率化、チームワーク強化、コスト削減、品質向上を実現します。このサービスは、製造業の課題を深く理解し、それに対する最適なデジタルソリューションを提供することで、企業が持続的な成長とイノベーションを達成できるようサポートします。
オンライン講座
製造業、主に購買・調達部門にお勤めの方々に向けた情報を配信しております。
新任の方やベテランの方、管理職を対象とした幅広いコンテンツをご用意しております。
お問い合わせ
コストダウンが利益に直結する術だと理解していても、なかなか前に進めることができない状況。そんな時は、newjiのコストダウン自動化機能で大きく利益貢献しよう!
(Β版非公開)