- お役立ち記事
- Case Studies of Developing Durable Products Using Compression Molding
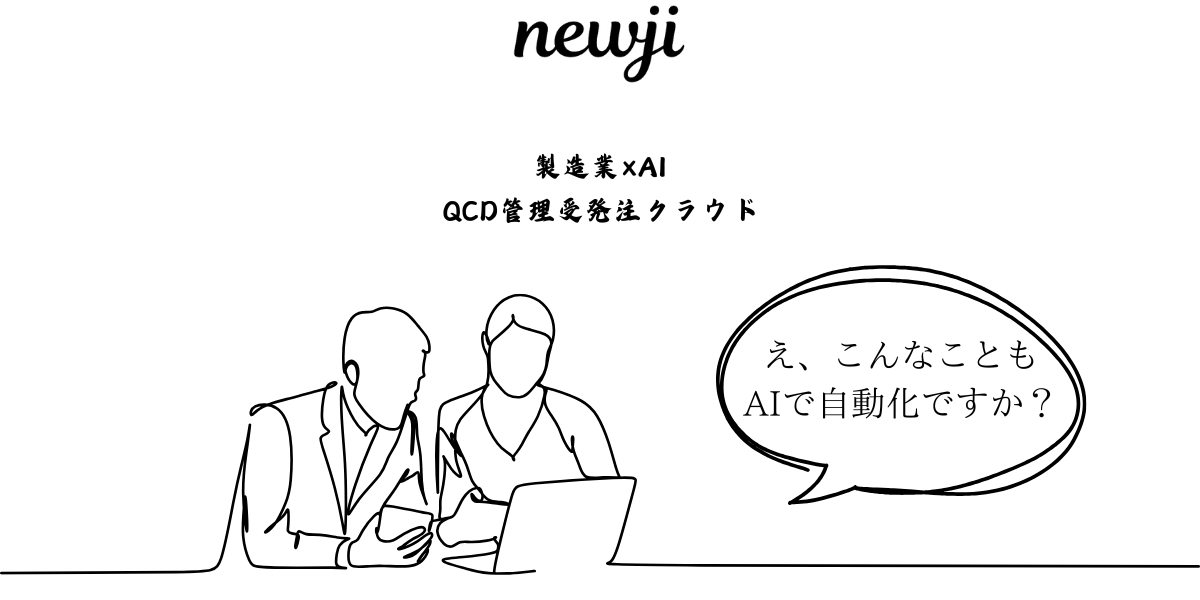
Case Studies of Developing Durable Products Using Compression Molding
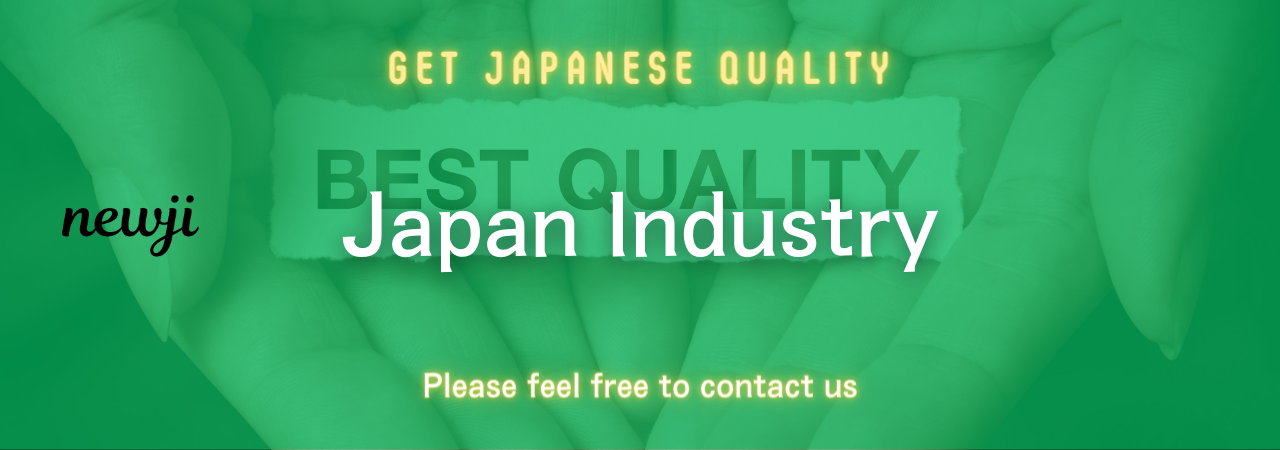
目次
Understanding Compression Molding
Compression molding is a widely used manufacturing process known for its efficiency in producing durable and versatile products.
It involves placing a material, typically a polymer, into a heated mold cavity.
Once in the mold, the material is subjected to heat and pressure, transforming it into a specific shape.
The mold is usually designed to create one product at a time, allowing for precise control over the final product’s dimensions and characteristics.
This technique is especially popular in industries requiring robust and high-quality components.
Advantages of Compression Molding
One of the primary benefits of compression molding is its ability to produce parts with exceptional strength and integrity.
The process applies consistent pressure and heat, ensuring the materials adhere and cure thoroughly.
As a result, the final product is often free of defects and ready to withstand various stressors.
Another advantage is its cost-effectiveness, especially for medium to large production runs.
The ability to reuse molds and the minimal waste generated contribute significantly to reducing costs.
Case Study 1: Automotive Industry Application
In the automotive industry, durability is a critical factor for components such as bumpers and chassis parts.
A case study involving a major car manufacturer illustrates the effectiveness of compression molding.
The manufacturer aimed to develop bumpers capable of withstanding impacts and harsh weather conditions.
By using reinforced polymers and precisely engineered molds, the company was able to produce bumpers that exceeded safety standards.
The durability tests showed that the products maintained their shape and structural integrity even after repeated collisions.
The success of this approach not only enhanced safety but also reduced maintenance costs over the vehicle’s lifetime.
Materials Used
The use of fiber-reinforced plastics in this case was pivotal.
These materials combine the high tensile strength of fibers with the flexible nature of plastics, resulting in a product that is both lightweight and strong.
The choice of material played a significant role in achieving the desired durability standards for the bumpers.
Case Study 2: Consumer Electronics
Another impressive application of compression molding is found in the consumer electronics sector, particularly in the production of durable phone cases.
A leading electronics firm sought to design a phone case that could protect devices from drops and scratches.
Through compression molding, the company was able to create a product with superior shock absorption properties.
The process allowed the engineers to incorporate ribs and other strengthening features into the mold design, which in turn enhanced the case’s protective capabilities.
Efficiency and Design Flexibility
The efficiency of compression molding in this case was notable.
Mass production of the phone cases was streamlined, resulting in a rapid manufacturing process.
Moreover, the ability to experiment with different mold designs provided flexibility in aesthetics and functionality.
As such, customers were able to choose from a variety of styles without compromising on protection.
Case Study 3: Medical Devices
Compression molding also plays a crucial role in the medical industry, particularly in the manufacture of medical equipment and components.
A medical device company focused on producing durable and sterile components for surgical devices used this method to great effect.
By employing compression molding, the company improved the reliability and longevity of its devices.
Ensuring Safety and Precision
Safety and precision are paramount in medical device manufacturing.
The firm utilized high-grade medical polymers that could withstand sterilization processes without degrading.
Additionally, compression molding allowed for the creation of complex shapes and fine details essential for surgical precision.
The resulting components were not only durable but also compatible with stringent healthcare regulations, ensuring patient safety.
Challenges in Compression Molding
While the benefits of compression molding are significant, the process does come with its own set of challenges.
One major concern is the initial cost of mold creation, which can be high.
This cost is often offset in larger production runs, but it remains a barrier for smaller manufacturers.
Additionally, the process requires precise control of variables such as heat and pressure to ensure product quality.
Innovations in technology continue to address these challenges, making compression molding an increasingly viable option for a wide range of industries.
Technical advancements such as automated control systems are improving the accuracy and efficiency of the process.
These innovations contribute to reducing costs and improving the quality of the final products.
Future Trends and Considerations
Looking ahead, the future of compression molding in developing durable products appears promising.
With ongoing research into materials and process improvements, manufacturers can expect even more durable and cost-effective solutions.
Sustainability is also becoming a key consideration, with eco-friendly materials being integrated into compression molding practices.
As companies focus on reducing their carbon footprint, the demand for recyclable and biodegradable materials in compression molding is expected to rise.
By leveraging these trends, businesses can not only enhance their product offerings but also contribute positively to environmental conservation.
In conclusion, the case studies detailed here illustrate the effectiveness of compression molding in producing durable products across various industries.
Its advantages in terms of product strength, cost, and design flexibility make it an attractive option for manufacturers.
Despite existing challenges, ongoing innovations and material advancements continue to push the boundaries of what is possible with this versatile manufacturing process.
資料ダウンロード
QCD調達購買管理クラウド「newji」は、調達購買部門で必要なQCD管理全てを備えた、現場特化型兼クラウド型の今世紀最高の購買管理システムとなります。
ユーザー登録
調達購買業務の効率化だけでなく、システムを導入することで、コスト削減や製品・資材のステータス可視化のほか、属人化していた購買情報の共有化による内部不正防止や統制にも役立ちます。
NEWJI DX
製造業に特化したデジタルトランスフォーメーション(DX)の実現を目指す請負開発型のコンサルティングサービスです。AI、iPaaS、および先端の技術を駆使して、製造プロセスの効率化、業務効率化、チームワーク強化、コスト削減、品質向上を実現します。このサービスは、製造業の課題を深く理解し、それに対する最適なデジタルソリューションを提供することで、企業が持続的な成長とイノベーションを達成できるようサポートします。
オンライン講座
製造業、主に購買・調達部門にお勤めの方々に向けた情報を配信しております。
新任の方やベテランの方、管理職を対象とした幅広いコンテンツをご用意しております。
お問い合わせ
コストダウンが利益に直結する術だと理解していても、なかなか前に進めることができない状況。そんな時は、newjiのコストダウン自動化機能で大きく利益貢献しよう!
(Β版非公開)