- お役立ち記事
- Troubleshooting Molding Cycle Times and Tips for Improving Quality
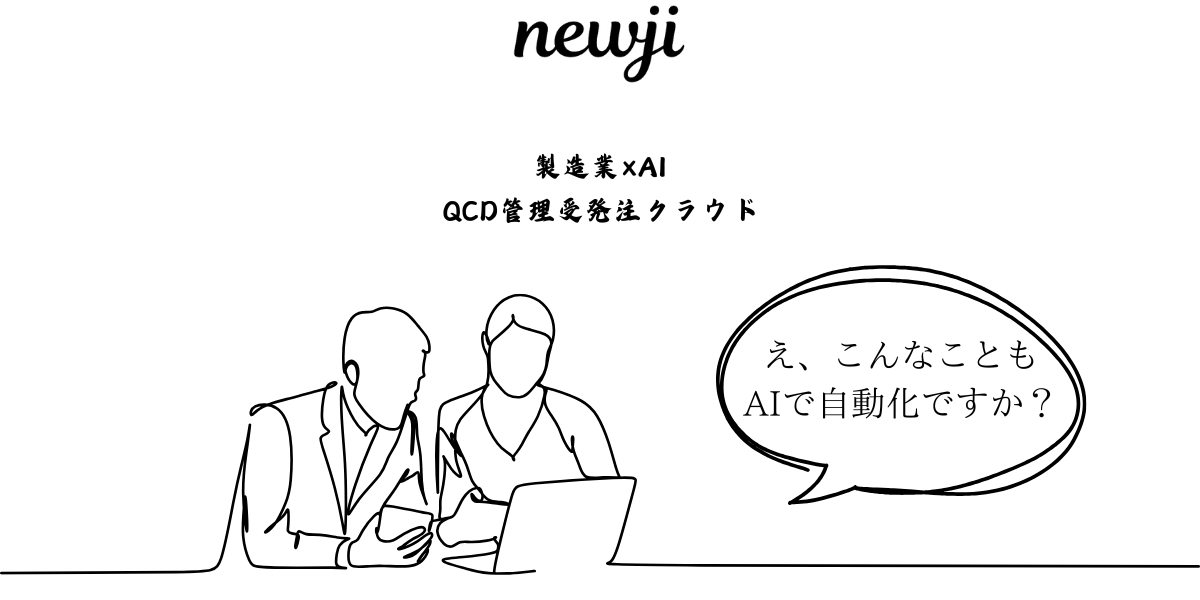
Troubleshooting Molding Cycle Times and Tips for Improving Quality
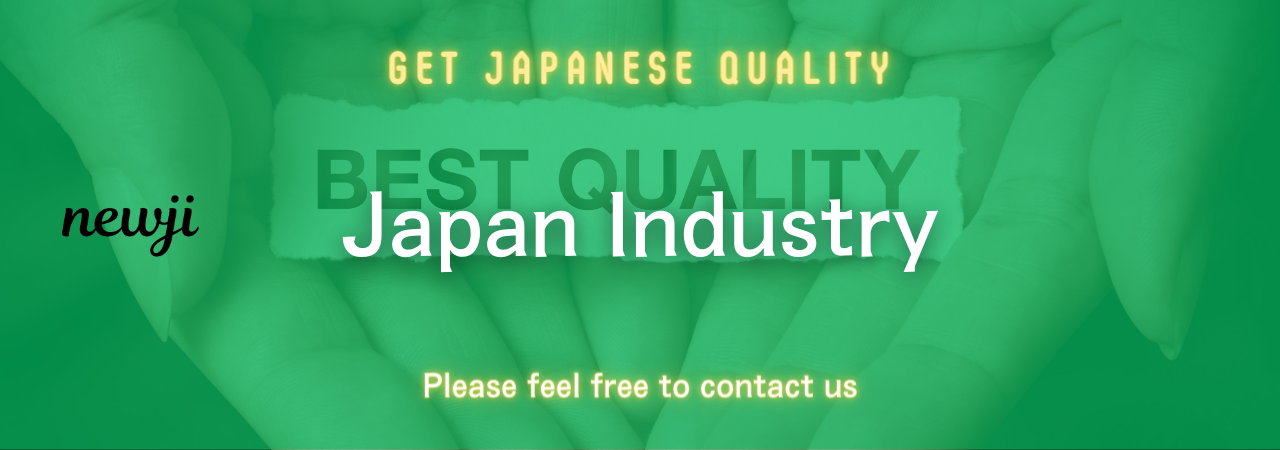
目次
Understanding Molding Cycle Times
Molding cycle time is a critical factor in the manufacturing process, especially in industries involving plastic production, injection molding, and similar processes.
Cycle time refers to the total time taken for a single molding operation to be completed, including the various stages such as melting, injecting, cooling, and ejecting.
Understanding and optimizing these cycle times can significantly enhance production efficiency and product quality, leading to improved profitability and customer satisfaction.
Factors Affecting Molding Cycle Times
Several factors can influence the molding cycle times, and understanding these can help in troubleshooting delays and optimizing the process.
The first major factor is the material being used; different materials have varying melting points, viscosity, and cooldown times.
For instance, materials like nylon require different handling than polycarbonate, due to their intrinsic properties.
The second factor is mold design which plays a crucial role in defining the cycle time.
A well-designed mold ensures uniform cooling and quick release of the product, while poor design can lead to longer cycle times and defects in the product.
Thirdly, the machine settings themselves can greatly impact cycle times.
Parameters such as temperature, pressure, and injection speed need to be precisely controlled to maintain optimal cycle times.
Finally, environmental conditions also play a role.
Fluctuations in ambient temperature or humidity can affect the machine’s performance, thereby impacting cycle time consistency.
Common Problems with Molding Cycle Times
Despite careful planning, several common issues can arise that affect cycle times.
One of the most frequent problems is inconsistent cycle times, leading to discrepancies in production output.
Inconsistencies can arise from machine wear and tear, improper calibration, or variations in material quality.
Another issue is extended cycle time due to cooling inefficiencies.
Cooling is a critical phase in the molding process, often accounting for the longest part of the cycle.
Poor thermal management or ineffective cooling systems can prolong this phase, thereby extending the overall cycle time.
Cycle time may also be adversely affected by machine downtimes and maintenance issues.
Regular maintenance is crucial to ensure that all machine parts operate smoothly.
However, if machines frequently breakdown or require significant adjustments, cycle time can be severely impacted.
Tips for Improving Molding Cycle Times
When it comes to improving molding cycle times, several strategies can be employed.
Firstly, optimizing mold design is crucial.
This involves ensuring that molds are designed to facilitate quick cooling, easy ejection, and minimal defects.
Better mold design contributes significantly to reducing the cycle times.
Another important tip is to carefully select materials and understand their properties.
Using materials that are compatible with the machine’s capabilities and that can withstand specific temperatures and pressures will ensure efficient processing.
Maintenance of machines should never be overlooked.
Regular and preventive maintenance schedules can help detect early signs of wear and rectify issues before they affect production.
Ensuring machines are running at their peak efficiency will directly enhance cycle times.
Implementing automation and monitoring systems can also be very beneficial.
These systems allow real-time data collection and analysis, helping quickly identify and address issues impacting cycle times.
Automation also assists in maintaining consistency and precision across all stages of the molding cycle.
Improving Quality alongside Reducing Cycle Times
While the primary focus often is on reducing cycle times, it is equally important to maintain or improve product quality.
Rapid cycles should not compromise the quality, and careful calibration of all parameters is necessary for achieving both fast production and high-quality output.
Testing and quality checks should be integrated into the production line.
This helps in identifying defects early and avoids mass production of flawed products.
Investing in high-quality molds and keeping abreast of the latest technological advancements in materials and machinery will also help bring about improvements in both cycle time and quality.
Training employees to fully understand the operations of the machinery and the importance of each stage within the cycle can also make a difference.
Skilled operators can quickly troubleshoot issues and make informed adjustments that enhance both speed and quality.
Conclusion
Improving molding cycle times while maintaining quality is a balancing act that requires a thorough understanding of the entire molding process.
By focusing on key areas such as mold design, material selection, regular machinery maintenance, automation, and employee training, manufacturers can achieve optimized cycle times.
These improvements can lead to greater efficiencies, higher quality products, and ultimately, increased satisfaction for both manufacturers and consumers alike.
Understanding these aspects ensures a competitive edge in the market and lays a strong foundation for continuous improvement in production processes.
資料ダウンロード
QCD調達購買管理クラウド「newji」は、調達購買部門で必要なQCD管理全てを備えた、現場特化型兼クラウド型の今世紀最高の購買管理システムとなります。
ユーザー登録
調達購買業務の効率化だけでなく、システムを導入することで、コスト削減や製品・資材のステータス可視化のほか、属人化していた購買情報の共有化による内部不正防止や統制にも役立ちます。
NEWJI DX
製造業に特化したデジタルトランスフォーメーション(DX)の実現を目指す請負開発型のコンサルティングサービスです。AI、iPaaS、および先端の技術を駆使して、製造プロセスの効率化、業務効率化、チームワーク強化、コスト削減、品質向上を実現します。このサービスは、製造業の課題を深く理解し、それに対する最適なデジタルソリューションを提供することで、企業が持続的な成長とイノベーションを達成できるようサポートします。
オンライン講座
製造業、主に購買・調達部門にお勤めの方々に向けた情報を配信しております。
新任の方やベテランの方、管理職を対象とした幅広いコンテンツをご用意しております。
お問い合わせ
コストダウンが利益に直結する術だと理解していても、なかなか前に進めることができない状況。そんな時は、newjiのコストダウン自動化機能で大きく利益貢献しよう!
(Β版非公開)