- お役立ち記事
- Basics of Gate Design and Its Importance in Injection Molding
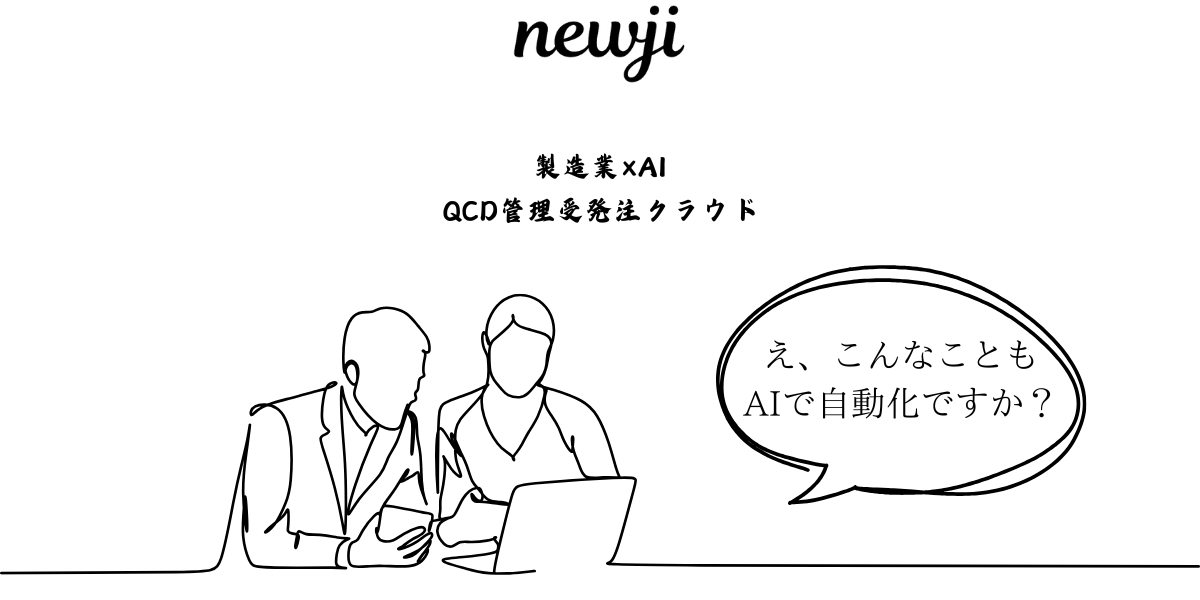
Basics of Gate Design and Its Importance in Injection Molding
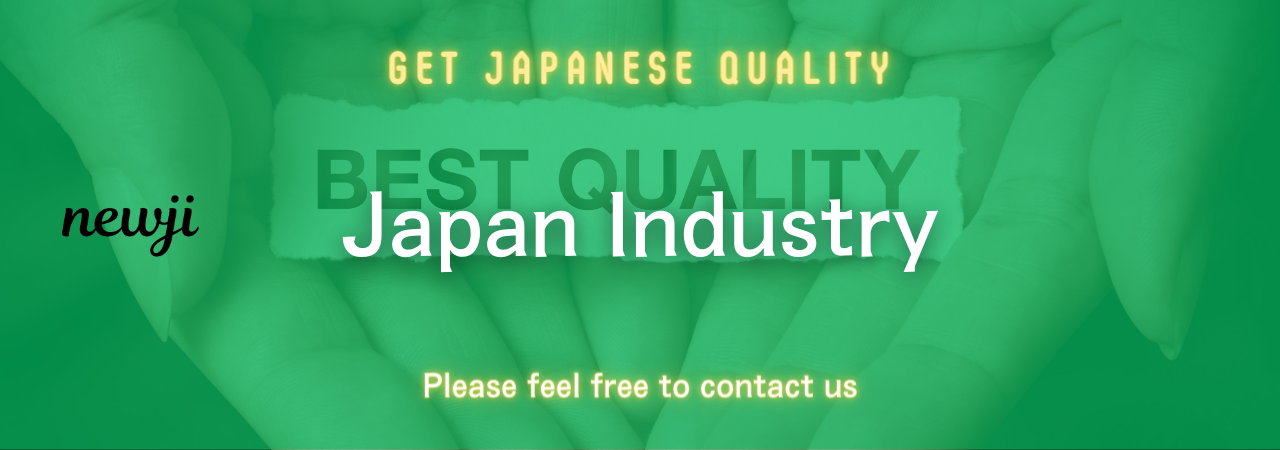
目次
Understanding the Role of Gates in Injection Molding
Injection molding is a manufacturing process used for producing parts by injecting molten material into a mold.
This versatile method is used for creating parts of various sizes and complexities, applicable in industries such as automotive, consumer goods, and medical devices.
Within this process, gates play a crucial role.
Gates are the pathways through which molten plastic flows into the mold cavity, and their design and placement significantly affect the quality and efficiency of the molding process.
What Are Gates in Injection Molding?
Gates are the final section of the runner system in an injection mold, acting as passageways for the molten plastic to enter the mold cavity.
They are essential components that significantly influence the flow and cooling of the material, consequently affecting the end product’s properties.
By controlling the flow of the material, gates help determine the final part’s strength, surface finish, and dimensional accuracy.
The Importance of Gate Design
Choosing the right gate design is crucial in achieving optimal results in injection molding.
An optimal gate design ensures uniform flow, minimizes stress, and reduces the risk of defects.
Influence on Material Flow
Proper gate design ensures even distribution of molten plastic inside the mold.
If the gate is poorly designed, it can cause unequal material flow, leading to defects such as warping, sink marks, or incomplete filling.
By optimizing the gate size and location, manufacturers can ensure a smooth and balanced flow of plastic, reducing the potential for defects.
Impact on Cooling Rates
The design and placement of gates also influence cooling rates.
As the material cools, it shrinks, and variations in cooling across different parts of the mold can lead to internal stresses and warping.
A well-designed gate helps to control the cooling process by enabling a consistent and uniform cooling rate throughout the molded part.
Effect on Product Quality
A well-thought-out gate design is crucial for achieving high-quality final products.
Optimal gate design minimizes defects, allowing for uniform surface finishes and reducing the need for post-processing.
This results in cost savings and improved production efficiency.
Common Gate Types in Injection Molding
Different gate designs offer specific advantages depending on the application’s requirements.
Edge Gates
Edge gates are among the most commonly used gate types, positioned along the edge of the mold cavity.
They are straightforward to design and implement, making them ideal for larger parts or components requiring post-mold machining.
However, they can lead to parting line flash if not carefully controlled.
Submarine Gates
Submarine gates, also known as tunnel gates, are positioned beneath the mold’s parting line and automatically trimmed when the part is ejected.
This gate type offers a blemish-free part appearance as there is no manual trimming required, making them ideal for smaller, delicate parts.
Fan Gates
Fan gates are used when a wide part needs uniform filling.
They distribute the molten plastic in a fan-like shape, ensuring even material flow across the entire width of the product.
This gate type is beneficial for parts with large surface areas, reducing the risk of warping and sink marks.
Pin Gates
Pin gates are small gates typically used in hot runner systems.
They deliver the molten plastic through a narrow orifice, resulting in minimal gate vestige.
Pin gates are well-suited for applications requiring aesthetic appeal and high precision, such as consumer products or medical devices.
Factors Affecting Gate Design
Several factors influence the choice and design of gates in injection molding.
Material Type
Different plastic materials have distinct flow characteristics that influence gate design.
Material properties such as viscosity and thermal conductivity determine the gate size and shape needed for optimal flow.
Understanding the material’s behavior helps designers select the appropriate gate type and parameters.
Part Geometry
The shape, size, and complexity of the molded part affect gate design.
Parts with intricate geometries may require precise gate placement to ensure complete and uniform filling.
Designers often use simulations to analyze how the molten plastic will fill the mold, informing gate design decisions.
Production Volume
Production volume also plays a role in gate design.
For high-volume production, gate designs that allow fast, efficient filling and rapid cooling are preferred.
Automated trimming, as seen with submarine gates, is often favored in such cases to reduce labor costs and improve consistency.
Conclusion
Gate design is a pivotal aspect of the injection molding process, with a direct influence on the final product’s quality, aesthetics, and structural integrity.
By considering factors such as material type, part geometry, and production volume, designers can optimize gate design to enhance product outcomes and manufacturing efficiency.
Understanding the basics of gate design allows manufacturers to make informed decisions, ultimately leading to better, more reliable products.
資料ダウンロード
QCD調達購買管理クラウド「newji」は、調達購買部門で必要なQCD管理全てを備えた、現場特化型兼クラウド型の今世紀最高の購買管理システムとなります。
ユーザー登録
調達購買業務の効率化だけでなく、システムを導入することで、コスト削減や製品・資材のステータス可視化のほか、属人化していた購買情報の共有化による内部不正防止や統制にも役立ちます。
NEWJI DX
製造業に特化したデジタルトランスフォーメーション(DX)の実現を目指す請負開発型のコンサルティングサービスです。AI、iPaaS、および先端の技術を駆使して、製造プロセスの効率化、業務効率化、チームワーク強化、コスト削減、品質向上を実現します。このサービスは、製造業の課題を深く理解し、それに対する最適なデジタルソリューションを提供することで、企業が持続的な成長とイノベーションを達成できるようサポートします。
オンライン講座
製造業、主に購買・調達部門にお勤めの方々に向けた情報を配信しております。
新任の方やベテランの方、管理職を対象とした幅広いコンテンツをご用意しております。
お問い合わせ
コストダウンが利益に直結する術だと理解していても、なかなか前に進めることができない状況。そんな時は、newjiのコストダウン自動化機能で大きく利益貢献しよう!
(Β版非公開)