- お役立ち記事
- Revolutionizing Efficiency: How the Japanese Master the Molding Cycle in Modern Manufacturing
Revolutionizing Efficiency: How the Japanese Master the Molding Cycle in Modern Manufacturing
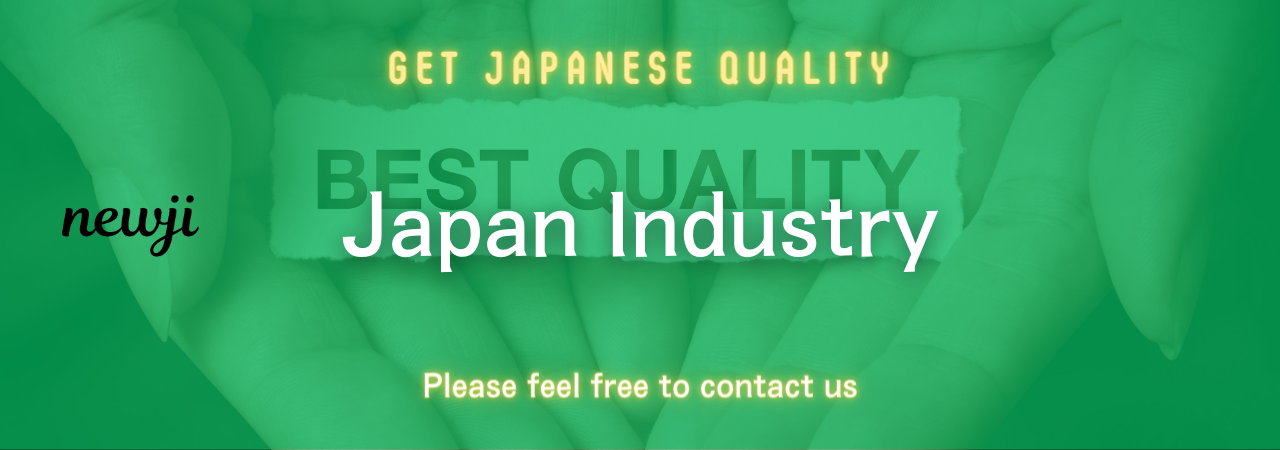
目次
Introduction to Modern Manufacturing Efficiency
In today’s highly competitive global market, efficiency in manufacturing is paramount.
Companies strive to optimize every aspect of their production processes to reduce costs and increase output.
One of the key players in this domain is Japan, renowned for its mastery in manufacturing efficiency.
This article explores how Japanese manufacturers excel in the molding cycle, revolutionizing modern manufacturing practices.
Understanding the Molding Cycle
The molding cycle is a critical process in manufacturing, involving the shaping of raw materials into desired products.
It encompasses several stages, including material preparation, molding, cooling, ejection, and finishing.
Efficiency in the molding cycle directly impacts production speed, product quality, and cost-effectiveness.
Mastering this cycle is essential for manufacturers aiming to maintain competitiveness in the market.
Japanese Expertise in the Molding Cycle
Japanese manufacturers have long been leaders in optimizing the molding cycle.
Their approach combines advanced technology, meticulous planning, and continuous improvement.
Historical Context: Lean Manufacturing and Kaizen
Japan’s manufacturing excellence is rooted in principles like Lean Manufacturing and Kaizen.
Lean focuses on minimizing waste without compromising productivity.
Kaizen emphasizes continuous, incremental improvements in all areas of production.
These philosophies have been instrumental in refining the molding cycle.
Modern Practices in Japanese Manufacturing
Today, Japanese manufacturers integrate cutting-edge technologies such as automation, robotics, and data analytics.
These tools enhance precision, reduce cycle times, and ensure consistent product quality.
Moreover, Japanese firms prioritize worker training and involvement, fostering a culture of accountability and excellence.
Advantages of Japanese Mastery in the Molding Cycle
Japan’s proficiency in the molding cycle offers numerous benefits to manufacturers and their partners.
High Efficiency and Precision
Japanese molding processes are characterized by their high efficiency and precision.
Advanced machinery and well-optimized workflows minimize cycle times and maximize output.
This leads to increased productivity and the ability to meet tight deadlines.
Superior Quality Control
Quality is a cornerstone of Japanese manufacturing.
Stringent quality control measures are implemented at every stage of the molding cycle.
This ensures that products meet exacting standards and reduces the likelihood of defects and recalls.
Strong Supplier Relationships
Japanese companies cultivate robust relationships with their suppliers.
This collaboration fosters mutual trust and ensures reliable supply chains.
Such partnerships contribute to smoother operations and the ability to swiftly address any issues that arise.
Challenges and Disadvantages
While Japanese mastery in the molding cycle offers significant advantages, there are also challenges to consider.
High Initial Investment
Implementing advanced manufacturing technologies and training requires substantial investment.
Not all companies may have the financial resources to adopt these practices immediately.
This can be a barrier for smaller firms looking to enhance their manufacturing processes.
Cultural and Language Barriers
Working with Japanese suppliers can present cultural and language challenges.
Understanding and adapting to Japanese business etiquette and communication styles is essential.
Misunderstandings can lead to delays and strained relationships if not properly managed.
Supplier Negotiation Techniques
Effective negotiation with Japanese suppliers is crucial for successful procurement and purchasing.
Building Long-Term Relationships
Japanese business culture values long-term partnerships over short-term gains.
Investing time in building trust and understanding with suppliers can lead to more favorable terms and better cooperation.
This approach fosters loyalty and encourages suppliers to prioritize your needs.
Understanding Japanese Negotiation Styles
Japanese negotiations tend to be thorough and incremental.
Decisive outcomes are rare; instead, discussions progress through consensus-building.
Patience and persistence are key, as decisions often require approval from multiple stakeholders.
Market Conditions Affecting the Molding Cycle
The global manufacturing landscape is continuously evolving, influencing the molding cycle’s efficiency.
Technological Advancements
Emerging technologies such as 3D printing and artificial intelligence are transforming manufacturing processes.
Japanese manufacturers are at the forefront of integrating these innovations into the molding cycle.
Staying abreast of technological trends is essential for maintaining efficiency and competitiveness.
Supply Chain Dynamics
Global supply chain disruptions, such as those caused by the COVID-19 pandemic, have highlighted the importance of resilient supply chains.
Japanese companies prioritize supply chain stability through diversified sourcing and strategic partnerships.
This resilience ensures continuity in the molding cycle despite external challenges.
Best Practices from Japanese Manufacturing
Adopting best practices from Japanese manufacturers can significantly enhance the molding cycle’s efficiency.
Implementing Kaizen for Continuous Improvement
Adopting the Kaizen philosophy encourages ongoing improvements in all aspects of the molding cycle.
Regularly assessing and refining processes leads to sustained efficiency gains and adaptability to changing conditions.
Leveraging Automation and Robotics
Integrating automation and robotics into the molding process increases precision and reduces manual errors.
These technologies can handle repetitive tasks efficiently, freeing up human resources for more complex activities.
Investing in Workforce Training
A well-trained workforce is critical to maintaining high efficiency in the molding cycle.
Continuous training ensures that employees are skilled in the latest technologies and best practices, contributing to overall productivity.
Implementing Japanese Techniques in Your Manufacturing Process
To achieve similar efficiency gains, manufacturers can incorporate Japanese techniques into their operations.
Assessing Current Processes
Begin by evaluating existing molding cycle processes to identify areas for improvement.
Determine where waste occurs and which stages are potential bottlenecks.
Adopting Lean Principles
Implementing Lean principles can streamline operations by eliminating unnecessary steps and optimizing workflow.
This leads to reduced cycle times and lower production costs.
Fostering a Culture of Continuous Improvement
Encourage all employees to contribute ideas for improving the molding cycle.
A collaborative environment promotes innovation and ensures that inefficiencies are promptly addressed.
Advantages for Procurement and Purchasing Departments
Effective management of the molding cycle translates to significant benefits for procurement and purchasing.
Cost Reduction
Enhancing the molding cycle’s efficiency can lead to lower production costs.
These savings can be passed on to buyers or reinvested into other areas of the business.
Improved Supplier Performance
Efficient processes require reliable suppliers.
By working closely with Japanese suppliers and implementing best practices, procurement departments can ensure timely and quality deliveries.
Enhanced Flexibility and Responsiveness
A streamlined molding cycle allows for greater flexibility in responding to market demands.
This agility is crucial in maintaining a competitive edge in a rapidly changing market environment.
Case Studies: Success Stories in Japanese Manufacturing
Examining real-world examples provides insights into the practical application of Japanese manufacturing techniques.
Toyota’s Just-In-Time Production
Toyota pioneered the Just-In-Time (JIT) production system, which minimizes inventory levels and reduces waste.
By aligning production schedules closely with demand, Toyota ensures efficient use of resources and rapid response to market changes.
Canon’s Precision Engineering
Canon’s expertise in precision engineering enhances the molding cycle’s accuracy and consistency.
Their focus on meticulous quality control results in high-quality products and minimal defects, reinforcing their reputation for excellence.
Challenges in Adopting Japanese Manufacturing Practices
While adopting Japanese techniques offers numerous benefits, it also presents certain challenges.
Resistance to Change
Implementing new practices can encounter resistance from employees accustomed to existing workflows.
Effective change management strategies are essential to facilitate smooth transitions and ensure employee buy-in.
Resource Allocation
Shifting to Japanese manufacturing practices may require significant resource allocation.
Investing in new technologies, training programs, and process redesigns necessitates careful planning and budgeting.
Strategies for Overcoming Implementation Challenges
Overcoming challenges requires strategic planning and a commitment to continuous improvement.
Leadership Commitment
Strong leadership is crucial in driving the adoption of new practices.
Leaders must exemplify the desired changes and provide clear direction and support to their teams.
Comprehensive Training Programs
Investing in comprehensive training ensures that employees understand and are capable of implementing new techniques.
Ongoing education helps maintain high standards and fosters a culture of excellence.
Incremental Implementation
Adopting changes incrementally allows for gradual adjustment and minimizes disruption.
Pilot programs can test new practices on a small scale before broader implementation.
The Global Impact of Japanese Manufacturing Efficiency
Japan’s mastery of the molding cycle has far-reaching effects on global manufacturing standards.
Setting Benchmark Standards
Japanese manufacturing practices set high benchmarks for efficiency and quality.
Other countries and companies often look to Japan as a model for best practices in manufacturing.
Influencing International Supply Chains
Japanese suppliers play a critical role in global supply chains.
Their reputation for reliability and quality influences international procurement and sourcing decisions.
Future Trends in Japanese Manufacturing
Looking ahead, several trends will shape the future of Japanese manufacturing efficiency.
Integration of Artificial Intelligence
AI is poised to further revolutionize the molding cycle by enabling predictive maintenance, optimizing workflows, and enhancing quality control.
Sustainability Initiatives
Japanese manufacturers are increasingly focusing on sustainable practices, reducing environmental impact through energy-efficient processes and eco-friendly materials.
Collaborative Robotics
The development of collaborative robots, or cobots, will enhance human-machine collaboration, improving both efficiency and workplace safety.
Implementing Continuous Improvement for Sustained Efficiency
Sustained efficiency requires a commitment to continuous improvement and adaptability.
Regular Process Audits
Conducting regular audits helps identify inefficiencies and areas for enhancement.
These evaluations ensure that the molding cycle remains optimized and responsive to changes.
Embracing Innovation
Staying open to innovation allows manufacturers to adopt new technologies and practices that can further enhance efficiency and quality.
Employee Engagement
Engaging employees in the improvement process fosters a sense of ownership and responsibility.
Motivated employees are more likely to contribute valuable ideas and support efficiency initiatives.
Conclusion: The Power of Japanese Mastery in Modern Manufacturing
Japanese expertise in the molding cycle exemplifies how meticulous planning, advanced technology, and a culture of continuous improvement can revolutionize manufacturing efficiency.
By adopting Japanese best practices, manufacturers worldwide can enhance their production processes, reduce costs, and deliver high-quality products.
The lessons learned from Japanese manufacturing offer a roadmap for achieving excellence in the ever-evolving landscape of modern manufacturing.
資料ダウンロード
QCD調達購買管理クラウド「newji」は、調達購買部門で必要なQCD管理全てを備えた、現場特化型兼クラウド型の今世紀最高の購買管理システムとなります。
ユーザー登録
調達購買業務の効率化だけでなく、システムを導入することで、コスト削減や製品・資材のステータス可視化のほか、属人化していた購買情報の共有化による内部不正防止や統制にも役立ちます。
NEWJI DX
製造業に特化したデジタルトランスフォーメーション(DX)の実現を目指す請負開発型のコンサルティングサービスです。AI、iPaaS、および先端の技術を駆使して、製造プロセスの効率化、業務効率化、チームワーク強化、コスト削減、品質向上を実現します。このサービスは、製造業の課題を深く理解し、それに対する最適なデジタルソリューションを提供することで、企業が持続的な成長とイノベーションを達成できるようサポートします。
オンライン講座
製造業、主に購買・調達部門にお勤めの方々に向けた情報を配信しております。
新任の方やベテランの方、管理職を対象とした幅広いコンテンツをご用意しております。
お問い合わせ
コストダウンが利益に直結する術だと理解していても、なかなか前に進めることができない状況。そんな時は、newjiのコストダウン自動化機能で大きく利益貢献しよう!
(Β版非公開)