- お役立ち記事
- Case Studies of Injection Molding Machine Implementation and Success Factors
Case Studies of Injection Molding Machine Implementation and Success Factors
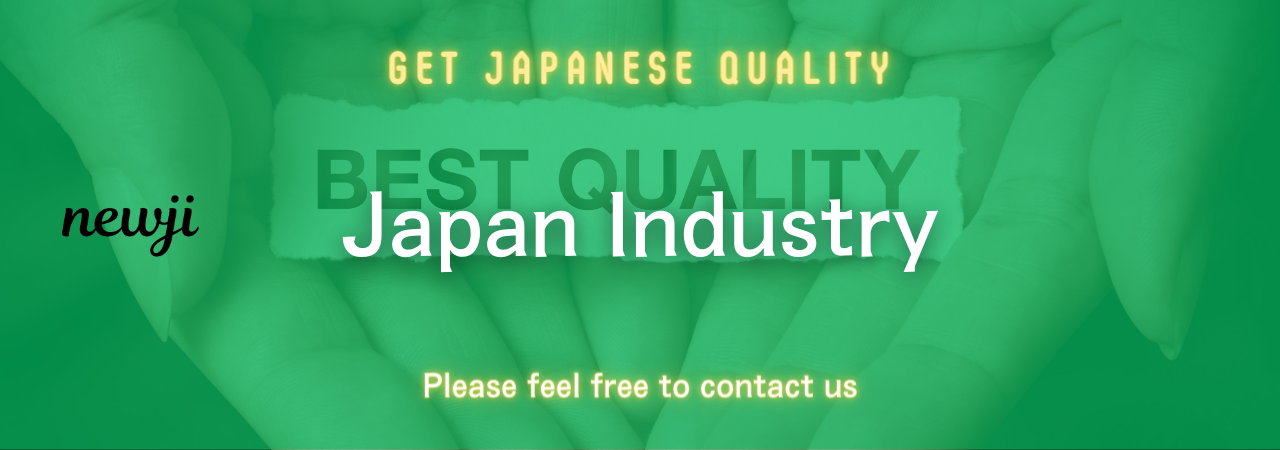
目次
Introduction to Injection Molding Machines
Injection molding machines are an essential component of the manufacturing process for creating complex plastic parts with precision and efficiency.
By using a mold, these machines inject molten plastic material into a hollow cavity, producing parts for industries ranging from automotive to consumer goods.
Successful implementation of injection molding machines can drive productivity, reduce costs, and deliver consistent quality.
Understanding the factors that contribute to successful implementation is crucial for businesses looking to integrate this technology into their production processes.
Understanding the Implementation Process
Implementing an injection molding machine involves several key steps that ensure a smooth transition and maximize benefits.
Proper planning is essential, starting with a thorough assessment of the manufacturing needs and the specific requirements of the production line.
This involves determining the type of machine needed, the capacity, and the technical specifications that align with the desired output.
Selection of the Right Machine
Choosing the appropriate injection molding machine is a critical decision that can significantly impact the success of the implementation.
Factors such as the size of the parts, the type of plastic used, and the production volume must be considered.
Manufacturers need to evaluate different machines based on their clamping force, injection capacity, and energy efficiency.
Opting for machines that align with the production goals and are capable of handling the specific material and design requirements ensures optimal performance.
Successful Case Studies of Implementation
Case Study 1: Automotive Industry Application
An automotive parts manufacturer decided to implement injection molding machines to enhance its production line for creating high-precision dashboard components.
The company conducted a comprehensive analysis of their requirements, focusing on machines that offered high tolerance and reliability.
By investing in advanced multi-cavity injection molding machines, the manufacturer achieved significant cost savings due to reduced material wastage and faster production cycles.
The implementation also improved the consistency of the parts, leading to higher customer satisfaction and improved market competitiveness.
Case Study 2: Consumer Goods Manufacturing
A major player in the consumer electronics sector faced the challenge of producing complex cases for its latest line of gadgets.
The company leveraged state-of-the-art injection molding machines with advanced monitoring systems and robotic automation.
The implementation process included training the workforce to operate these machines efficiently and integrating IoT systems for real-time performance tracking.
As a result, the company reduced its cycle time by 30%, leading to a notable increase in production capacity.
This not only met the growing demand but also enhanced the product’s design capabilities with finer detail and custom options.
Case Study 3: Medical Equipment Production
A leading manufacturer of medical devices implemented injection molding to produce disposable components used in healthcare applications.
Precision and quality were critical factors due to the stringent regulations in the medical field.
The company opted for machines with features like cleanroom compliance and advanced filtration systems to maintain the required hygiene standards.
Furthermore, the integration of quality control software enabled instant defect detection, minimizing waste and ensuring high-quality output.
The successful implementation allowed the company to offer reliable medical parts, thus expanding its market reach.
Key Success Factors in Implementation
Thorough Planning and Assessment
A successful implementation hinges on detailed planning.
Understanding the full scope of the project, from budget constraints to technical requirements, lays the foundation for informed decision-making.
Accurate demand forecasting and aligning production capabilities with market needs help avoid costly adjustments later.
Technology and Innovation
Integrating modern technology is pivotal for optimizing the operations of injection molding machines.
Automation, data analytics, and machine learning can enhance the efficiency and adaptability of the production process.
Staying abreast of technological advancements provides a competitive edge and reduces time to market.
Skilled Workforce
Human expertise must complement technological investments.
Training programs designed to enhance the skill set of operators ensure smooth machine operation and quick resolution of potential issues.
A knowledgeable team can also contribute innovative ideas for process improvements and problem-solving.
Maintaining Quality Standards
Quality assurance is paramount in industries utilizing injection molding.
Implementing robust quality control measures and routine maintenance schedules ensures machines continue to operate at peak performance and deliver high-quality products.
Early identification of defects through automated systems can prevent costly recalls and reputational damage.
Conclusion
The successful implementation of injection molding machines requires a multifaceted approach involving careful planning, technology integration, skilled personnel, and rigorous quality control.
Case studies across various industries show how these factors contribute to enhanced productivity, cost-effectiveness, and quality assurance.
As manufacturers continue to face new challenges and demands, adopting best practices in injection molding technology remains a crucial part of their strategy for success.
By learning from successful case implementations, businesses can better navigate their integration process and achieve desired outcomes.
資料ダウンロード
QCD調達購買管理クラウド「newji」は、調達購買部門で必要なQCD管理全てを備えた、現場特化型兼クラウド型の今世紀最高の購買管理システムとなります。
ユーザー登録
調達購買業務の効率化だけでなく、システムを導入することで、コスト削減や製品・資材のステータス可視化のほか、属人化していた購買情報の共有化による内部不正防止や統制にも役立ちます。
NEWJI DX
製造業に特化したデジタルトランスフォーメーション(DX)の実現を目指す請負開発型のコンサルティングサービスです。AI、iPaaS、および先端の技術を駆使して、製造プロセスの効率化、業務効率化、チームワーク強化、コスト削減、品質向上を実現します。このサービスは、製造業の課題を深く理解し、それに対する最適なデジタルソリューションを提供することで、企業が持続的な成長とイノベーションを達成できるようサポートします。
オンライン講座
製造業、主に購買・調達部門にお勤めの方々に向けた情報を配信しております。
新任の方やベテランの方、管理職を対象とした幅広いコンテンツをご用意しております。
お問い合わせ
コストダウンが利益に直結する術だと理解していても、なかなか前に進めることができない状況。そんな時は、newjiのコストダウン自動化機能で大きく利益貢献しよう!
(Β版非公開)