- お役立ち記事
- Methods for Adjusting Injection Pressure and Streamlining the Molding Process
Methods for Adjusting Injection Pressure and Streamlining the Molding Process
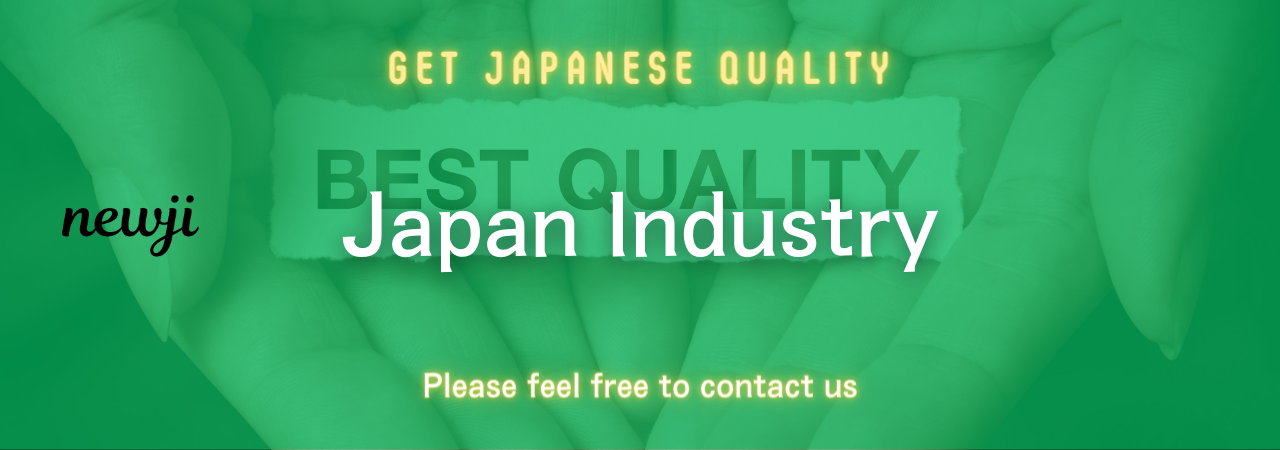
目次
Understanding Injection Molding
Injection molding is a manufacturing process used to produce parts by injecting molten material into a mold.
It is widely used for mass production, where the same part is created thousands or even millions of times in succession.
The process involves creating the mold, melting the material, injecting it into the mold, cooling, and then releasing the finished part.
One of the critical parameters in injection molding is the injection pressure.
Properly adjusting the injection pressure is crucial for producing high-quality parts and streamlining the overall molding process.
Importance of Injection Pressure
Injection pressure is a decisive factor in how well the molten material fills the mold cavity.
This pressure pushes the material into every nook and cranny, ensuring that the finished part has the correct dimensions and features.
Too low an injection pressure can result in incomplete filling, leading to defects and weaknesses in the molded parts.
Conversely, too high a pressure can cause issues such as flashing, where excess material escapes from the mold cavity.
Therefore, finding the right balance is essential for maintaining product quality and efficiency.
Adjusting the Injection Pressure
Analyzing Material Properties
The first step in adjusting injection pressure is understanding the material being used.
Different materials have different flow characteristics and, therefore, require varying levels of pressure.
For instance, materials with higher viscosity will need higher pressures to fill the mold effectively.
Thoroughly analyzing material data sheets can provide insights into the optimal pressure settings.
Understanding Mold Design
The design of the mold also plays a significant role in determining the appropriate injection pressure.
Factors such as mold complexity, part geometries, and the number of cavities will influence how pressure should be applied.
Complex molds with intricate details may require a more precise pressure setting to ensure each feature is accurately formed.
Using Scientific Molding Techniques
Scientific molding is an advanced method that involves analyzing the process through data and experimentation to optimize each parameter, including injection pressure.
This approach uses data from sensor-based technology to measure pressure, temperature, and material flow within the mold to make informed adjustments.
By adopting scientific molding techniques, manufacturers can fine-tune pressure settings to achieve consistent results.
Implementing Gradual Adjustments
When making changes to the injection pressure, it’s best to do so gradually.
Significant shifts can lead to unstable processes and may introduce more variables to be corrected.
Instead, incremental adjustments allow you to monitor changes in part quality and tweak the settings accordingly for optimal results.
Streamlining the Molding Process
Regular Mold Maintenance
Regular maintenance of the mold is indispensable for a streamlined molding process.
Over time, wear and tear can affect mold integrity, requiring more pressure to achieve the same results.
By keeping molds in good condition, manufacturers can maintain efficiency and part quality without needing excessive pressure adjustments.
Automation and Monitoring Systems
Incorporating automation and monitoring systems can significantly streamline the injection molding process.
These technologies provide real-time data on various parameters, including pressure, allowing for immediate adjustments.
Automation reduces human error, while monitoring systems keep track of the process’s consistency and efficiency.
Temperature Control
Temperature control is another key factor in the molding process.
The temperature of both the molten material and the mold itself can affect how easily the material flows, directly impacting the required pressure.
Ensuring that temperature settings remain consistent can help in maintaining optimal pressure.
Training and Skill Development
Finally, investing in the training and skill development of operators can streamline the molding process.
Skilled operators can better understand how pressure adjustments impact production and quality, enabling them to make more effective decisions.
Providing continuous education on the latest technologies and techniques can lead to more efficient production.
Conclusion
Adjusting injection pressure and streamlining the molding process are essential elements for achieving high-quality parts and efficient production.
By understanding material properties, mold design, and implementing advanced techniques, manufacturers can fine-tune their processes for better results.
Regular maintenance, along with automation and skilled personnel, can further enhance efficiency, leading to a more productive and prosperous operation.
資料ダウンロード
QCD調達購買管理クラウド「newji」は、調達購買部門で必要なQCD管理全てを備えた、現場特化型兼クラウド型の今世紀最高の購買管理システムとなります。
ユーザー登録
調達購買業務の効率化だけでなく、システムを導入することで、コスト削減や製品・資材のステータス可視化のほか、属人化していた購買情報の共有化による内部不正防止や統制にも役立ちます。
NEWJI DX
製造業に特化したデジタルトランスフォーメーション(DX)の実現を目指す請負開発型のコンサルティングサービスです。AI、iPaaS、および先端の技術を駆使して、製造プロセスの効率化、業務効率化、チームワーク強化、コスト削減、品質向上を実現します。このサービスは、製造業の課題を深く理解し、それに対する最適なデジタルソリューションを提供することで、企業が持続的な成長とイノベーションを達成できるようサポートします。
オンライン講座
製造業、主に購買・調達部門にお勤めの方々に向けた情報を配信しております。
新任の方やベテランの方、管理職を対象とした幅広いコンテンツをご用意しております。
お問い合わせ
コストダウンが利益に直結する術だと理解していても、なかなか前に進めることができない状況。そんな時は、newjiのコストダウン自動化機能で大きく利益貢献しよう!
(Β版非公開)