- お役立ち記事
- A Practical Guide to Mold Design for Complex-Shaped Products
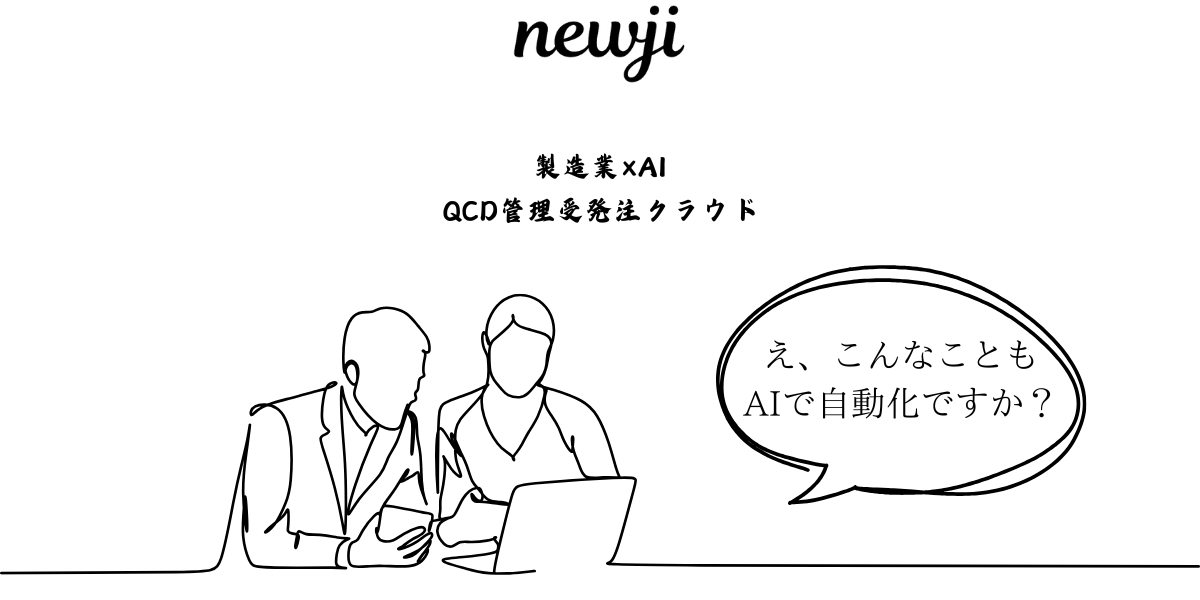
A Practical Guide to Mold Design for Complex-Shaped Products
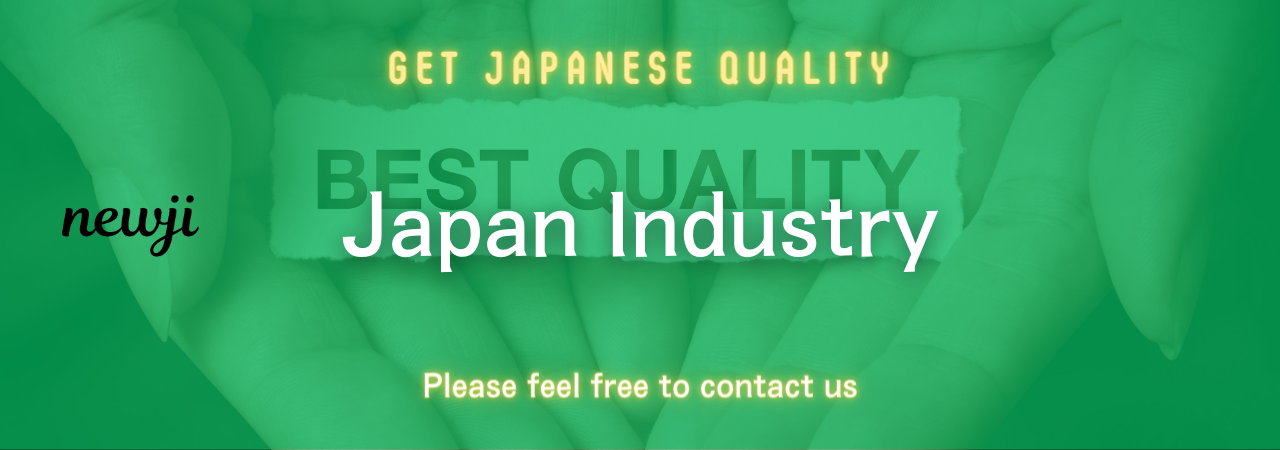
目次
Understanding the Basics of Mold Design
Mold design is an essential process in manufacturing, particularly when creating complex-shaped products.
Molds are templates or forms used to shape materials into the desired shape and size.
The creation of a good mold is crucial for the production of high-quality products.
When designing molds, it’s important to consider factors like material type, product complexity, and production volume.
Importance of Mold Design
The importance of mold design cannot be overstated.
A well-designed mold ensures efficiency, reduces waste, and increases product quality.
It allows manufacturers to produce identical and precise parts quickly.
Moreover, correct mold design reduces the risk of defects and returns.
For complex-shaped products, mold design becomes even more important, as these products often require precision and accuracy.
Key Considerations in Mold Design
When approaching mold design, several critical factors must be taken into account.
Understanding these factors ensures that the final product meets both design specifications and quality standards.
Material Selection
Selecting the right material is crucial for effective mold design.
The material must withstand the molding process and the conditions under which it will be used.
For instance, materials must be selected for durability, heat resistance, and reactivity.
Common molding materials include plastic, rubber, metal, and ceramics, each having unique properties.
Product Complexity
The complexity of the product plays a significant role in mold design.
Complex-shaped products often require intricate mold designs to capture every detail of the product.
This includes considering factors like undercuts, draft angles, and surface finishes.
Designing for complex shapes frequently involves using advanced technologies like 3D modeling and computer-aided design (CAD).
Production Volume
The number of units to be produced affects the mold design process.
For high-volume production, more durable materials and designs that allow for quick cycling and minimal downtime are necessary.
Conversely, low-volume production can opt for slightly less durable materials, optimizing for cost rather than speed.
Steps in Designing Molds for Complex-Shaped Products
When creating molds for complex-shaped products, following a structured process is essential to achieve the best results.
Here’s a practical guide to the key steps in designing these molds.
1. Conceptualization and Design
Begin with thorough planning and design.
Understanding the product’s geometry, function, and application is crucial.
Use CAD software to create detailed design models of the mold and the product.
Collaboration with engineers and product designers during this phase is beneficial.
Their input helps ensure the mold design meets functional and aesthetic product requirements.
2. Prototype Development
Before finalizing the mold design, creating a prototype is a critical step.
Rapid prototyping techniques, such as 3D printing, can be used to test the mold’s functionality and fit.
This process helps identify design flaws and allows for adjustments before creating the final mold.
3. Mold Manufacturing
Once the prototype is approved, the actual mold manufacturing begins.
This involves selecting suitable materials and using precise machining techniques.
For complex-shaped molds, CNC machining or electrical discharge machining (EDM) are commonly employed.
These methods provide the precision required to achieve the desired level of detail.
4. Testing and Refinement
After manufacturing the mold, testing is necessary.
The testing phase identifies defects or discrepancies in the final product.
Conduct thorough tests to ensure the product meets quality standards and design specifications.
If issues are identified, refinements must be made to the mold design.
Challenges in Mold Design for Complex Shapes
Mold designing for complex-shaped products comes with its own set of challenges.
Understanding and addressing these challenges is necessary for successful mold fabrication.
Precision and Accuracy
Achieving precision in mold design is often challenging but essential, especially for products with intricate details.
Ensuring high accuracy involves using advanced technologies and skilled craftsmanship.
Cost Management
Designing molds for complex shapes can be costly, given the materials, technology, and expertise involved.
Managing these costs while maintaining quality is a significant challenge.
To mitigate costs, efficient design techniques and alternative materials should be explored.
Time Constraints
The development timeline for complex molds can be extensive, sometimes causing delays in production.
Implementing efficient project management practices and choosing the right manufacturing techniques can help minimize these delays.
Conclusion
Mold design for complex-shaped products requires careful planning and execution.
By understanding the basics, considering key factors, and following a structured design process, manufacturers can create effective molds that lead to high-quality products.
Despite the challenges, advancements in technology and material science continue to improve the efficiency and precision of mold design.
Molding experts, engineers, and designers who collaborate effectively are more likely to produce successful outcomes, ensuring that the molds they create serve their intended purpose with excellence.
資料ダウンロード
QCD調達購買管理クラウド「newji」は、調達購買部門で必要なQCD管理全てを備えた、現場特化型兼クラウド型の今世紀最高の購買管理システムとなります。
ユーザー登録
調達購買業務の効率化だけでなく、システムを導入することで、コスト削減や製品・資材のステータス可視化のほか、属人化していた購買情報の共有化による内部不正防止や統制にも役立ちます。
NEWJI DX
製造業に特化したデジタルトランスフォーメーション(DX)の実現を目指す請負開発型のコンサルティングサービスです。AI、iPaaS、および先端の技術を駆使して、製造プロセスの効率化、業務効率化、チームワーク強化、コスト削減、品質向上を実現します。このサービスは、製造業の課題を深く理解し、それに対する最適なデジタルソリューションを提供することで、企業が持続的な成長とイノベーションを達成できるようサポートします。
オンライン講座
製造業、主に購買・調達部門にお勤めの方々に向けた情報を配信しております。
新任の方やベテランの方、管理職を対象とした幅広いコンテンツをご用意しております。
お問い合わせ
コストダウンが利益に直結する術だと理解していても、なかなか前に進めることができない状況。そんな時は、newjiのコストダウン自動化機能で大きく利益貢献しよう!
(Β版非公開)